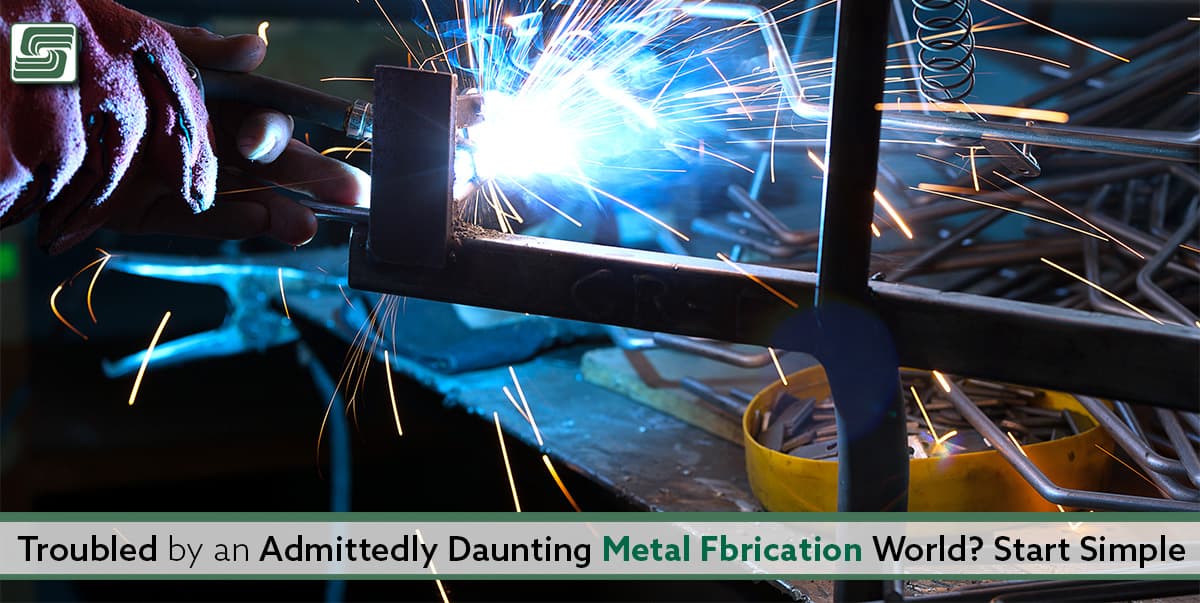
One thing identifying us as sentient beings is how we can accomplish the same task using different methods. Simple things like adding air to a bike tire. You manually pump or use an air compressor.
That same concept applies to metal fabrication.
Custom Metal Fabrication
Any changes made to metal, such as cutting, folding, welding, etc., are part of the metal fabrication process. Each type of fabrication process means meeting a specific purpose.
For instance, cutting, one of the most common metal fabrication processes, divides large sections of metal sheets and plates. In most cases, the cut metal is fresh.
Some of the most common metal fabrication processes are:
- Cutting
- Folding
- Machining
- Punching
- Welding
Other methods include:
- Annealing
- Bending
- Cold Forming and Rolling
- Drawing
- Electro-Discharge
- Extrusion
- Forge Hammering
- Laser Cutting
- Rolling
- Spinning
- Water Jet Cutting
- Wire Cut EDM
Here are some other custom metal fabrication techniques and their applications.
Sheet Metal Shearing
Shearing is a metal fabrication method used to cut long metal sheets horizontally. In some applications, the cutting tool vertically cuts against the length of the sheet. Another shearing method moves the metal towards an open cutting blade, like a guillotine paper cutter.
The most common use of shearing is to trim the edges of the metal sheet. The resulting products from metal shearing are used in the manufacture of refrigerators, oven side panels, other household appliances, and the automotive industry.
Stamping—The Use of a Die
It is essential to clarify that stamping isn’t the only metal fabrication process to use a die. In some applications, the purpose is making a hole, while in others to raise a part of the sheet metal without punching through it.
Stamping creates impressions for letters, images, logos, etc., on a metal panel or sheet. Coins provide an excellent example of the stamping process.
The automotive industry stamps part and vehicle identification numbers of components. The electronic industry stamps patent and part numbers, as well.
Casting: Oldest Fabrication Form
Humans have been casting metal for hundreds of years. The process involves pouring molten metal into a mold, which then solidifies. Casting may be the oldest method, but it’s also the most flexible. When fabricating complex shapes, casting becomes the easiest option.
Casting overcomes the issues associated with other methods of fabrication—making assembly parts needing folding, stamping, and shearing.
Metals like copper, silver, iron, magnesium, and steel are often cast because they are used across various industries.
Common Fabrication Examples
The most typical items produced are metallic cabinets, enclosures, ventilation shafts, hoods, exhaust systems, tanks, and prototypes.
Fabricating Exotic Metals
We've only discussed normal metal, but what happens when you need to work with something different? As we explain in our article, Fabricating Exotic Metals, you need non-standard tooling:
Most exotic metals have very different thermal properties than metals such as steels, titanium, or Inconel®, which impacts the type of tooling needed to machine these materials. For example, tools may need to be larger than standard materials.
Exotic metals also have different thermal expansion properties than common steels. Therefore, a standard machine tool may not work well for these. Some metals can have thermal gradients 50-100 times greater than steel.
Exotic metals generally need a higher spindle speed, higher horsepower, and more horsepower per tooth than steels, which is particularly true when machining hard materials.
Geometric Dimensions and Tolerances
Before turning on a brake press or lighting a welder, make sure you know what you're doing! Work off properly designed and marked drawing from an engineer following geometric dimensions and tolerances (GD&T) guidelines. We explain why this is important in our article, GD&T Part 1.
When producing goods, the manufacturing industry must adhere to several regulatory standards, such as ISO quality management. To do so, manufacturers typically apply the principles of geometric dimensioning and tolerancing to their design and production processes.
GD&T allows engineers to communicate the critical aspects of their designs while accommodating variability because of manufacturing processes. This means designers and engineers can effectively communicate with manufacturers uniformly.
This standardization in communication is necessary because many manufacturers produce and ship goods globally. Differences in design requirements, engineering conventions, and regulatory standards can cause confusion and delays in the supply chain. GD&T eliminates these issues.
In Sum
When designing any product, it’s important to consider the fabrication process. For example, how it will be manufactured matters.
The resulting product may be stronger and more durable depending on the process used. Other factors are also important, like using, cutting, and finishing the type of metal, which makes the choice of the manufacturing process for your next product important.
Besides these considerations, each process has its strengths and weaknesses. Learning about each type of fabrication method is important so you can make the best possible decision when fabricating your product.
For example, welding is very strong in a welded joint but can’t be bent. It’s strong, but not flexible. Punching, on the other hand, is strong but flexible.
As you research the different fabrication options, keep in mind that the most effective one depends on the needs of your project. It’s also important to remember that each process has its upsides and downsides, and it’s up to you to choose the right method.