Punching & Forming
Punching and forming departments are crucial to any metal fabrication company's operations. In the punching department, a CNC-controlled punch press cuts and shapes metal sheets fed with raw material sheets. The CNC controls the cutting, punching, and shaping operations to produce highly precise and consistent parts.
In the forming department, CNC-controlled brake presses bend and shape metal sheets. The brake presses feature offline programming, so the operators program the machine's movements and settings using computer software, allowing for higher accuracy and flexibility.
The CNC-controlled brake presses handle various types of metal sheets, including aluminum, stainless steel, and carbon steel, and create complex shapes and forms with high accuracy. Sensors and safety features prevent accidents and ensure the safety of operators.
Using CNC-controlled equipment in punching and forming departments increases efficiency and productivity, reducing production time and costs while ensuring consistent quality. This technology produces more complex designs and shapes, expanding the range of products.
The punching and forming departments are integral to the metal fabrication process. Using CNC-controlled equipment and offline programming is essential to meeting the demands of modern manufacturing.
Material Dimensions
- Thicknesses up to 1-inch
- Lengths up to 16 feet
Punching & Forming FAQs
If you're looking for answers to common questions about punching and forming, you'll find them on our FAQ page. You can access the page by following the link provided on this website. It's a valuable resource for anyone who wants to learn more about punching and forming, and it's easy to find with just a few clicks.
So whether you're a beginner or an experienced professional, please take a moment to explore our FAQ page and discover the information you need to succeed in your projects.
The Fab Times
If you would like to learn more about forming steel or other related topics, visit our blog, The Fab Times. Subscribe to receive articles when they're published. We promise, no spam!
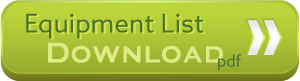
Simplifying Complex Projects is What We Do. How Can We Help You?