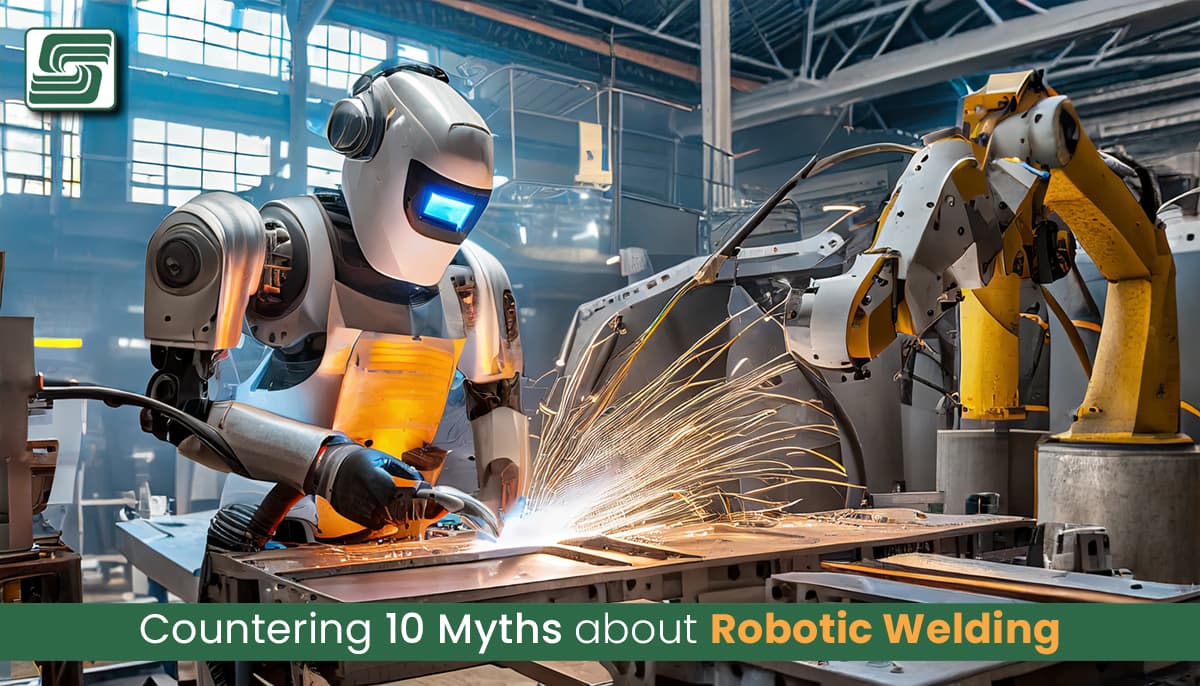
Welding with robots is kind of like riding a bike for the first time. At first, you may be a little wobbly and unsure, but once you get the hang of it, you zoom around with the wind in your hair before you know it!
Similarly, robotic welding has faced some initial hesitance and misconceptions, but it offers immense benefits and possibilities upon closer look.
Read on as we pedal through and debunk the most common myths about robotic welding.
Myth #1: Robots Steal Jobs
Robotic welding has been controversial and concerned, with one prevailing myth being that robots steal jobs. However, this assumption cannot recognize the many benefits that robotic welding brings to the industry.
In reality, robots are revolutionizing the welding process rather than eliminating jobs and creating new opportunities for skilled workers.
One important point is that robots excel at performing repetitive and physically demanding tasks with high precision and consistency. While some manual welding jobs may be automated, it also frees human welders to focus on more complex tasks requiring critical thinking and problem-solving skills.
Instead of replacing workers, robotic welding technology complements their abilities by increasing overall productivity. The demand for skilled welders continues to grow as industries expand and evolve.
Robotic automation in welding has fueled this demand even further by increasing production capacity. As manufacturers adopt robotic systems for higher volume projects, they also take on more work and expand their operations.
More skilled welders are needed to operate and maintain these automated systems. Another crucial point is that robots require human oversight and programming expertise to function effectively.
Skilled technicians are necessary during the initial setup and ongoing monitoring and maintenance of robotic welding cells. Human operators ensure quality control by setting parameters such as arc length, wire speed, voltage settings, etc., directly impacting the final weld quality.
Acknowledging the collaborative nature of human-robot interaction in modern manufacturing environments is essential. Rather than replacing humans entirely, robotic systems work alongside them in a complementary manner known as cobots. This collaboration allows humans to bring their expertise while robots handle labor-intensive or hazardous tasks.
In this way, job roles evolve rather than disappear entirely as industries adopt technological advancements like robotic welding. The myth that robots steal jobs overlooks the nuanced reality of how automation technologies like robotic welding benefit workers and industries.
Rather than replacing skilled welders, robotic systems empower them by automating repetitive tasks and increasing overall productivity. The demand for skilled workers in welding continues to grow as industries expand their operations and adopt automation technologies.
By working alongside humans, robots enhance manufacturing and create new job opportunities requiring programming expertise and maintenance skills. It is crucial to dispel this myth and recognize the collaborative potential that robotic welding brings to the industry.
Myth #2: Robotic Welding is Only for High-Volume, Repetitive Welding
Robotic welding is often mistakenly perceived as a technology only suited for high-volume, repetitive tasks. However, this is a common misconception that cannot recognize the versatility and adaptability of modern robotic welding systems.
These intelligent machines handle various welding applications with precision and efficiency. One crucial aspect is that robotic welders are programmed to execute complex welding operations accurately. They possess advanced sensor technology and sophisticated algorithms that allow them to adjust their movements, monitor weld quality in real-time, and make necessary corrections.
This means they are not limited to repetitive tasks but tackle intricate welds requiring various angles, orientations, or joint designs. Robotic welders also offer tremendous flexibility regarding the materials they work with. Contrary to popular belief, they are not solely designed for specific metal alloys or thicknesses.
With the programming and tooling modifications, these machines weld various materials such as steel, aluminum, stainless steel, and even exotic alloys like titanium. Their ability to accommodate different material specifications makes them suitable for high-volume production runs and custom fabrication projects.
Another advantage worth highlighting is the speed at which robotic welders operate. They possess exceptional repeatability and accuracy levels that enable them to consistently produce high-quality welds at a rapid pace. This allows manufacturers to achieve increased productivity without compromising on precision or consistency. Advancements in robotics have led to enhanced software capabilities that enable easy reprogramming for varying product specifications.
Robotic welding systems now offer intuitive user interfaces and offline programming tools that simplify programming processes even for those without extensive coding experience. This means that small batch productions or one-off jobs benefit from robotic welding technology without incurring significant setup costs or sacrificing quality.
It is wrong to assume that robotic welding systems are only designed for high-volume repetitive tasks. These machines have the versatility to handle various welding applications, from simple to complex, with different materials and specifications.
Their accuracy, speed, and adaptability suit them well for mass-production environments and smaller-scale projects. By dispelling the myth that robotic welding is limited to repetitive tasks, manufacturers harness the full potential of this technology and reap its many benefits across various industries.
Myth #3: Robotic Welding Produces Inferior Weld Quality Compared to Manual Welding
Robotic welding produces inferior weld quality compared to manual welding. This common myth has led many to believe that robotic welding technology cannot match the finesse and precision of human welders.
However, advancements in robotic welding systems have proven this notion unfounded. One of the key advantages of robotic welding is its unparalleled consistency.
Unlike humans, robots do not suffer from fatigue or inconsistency in their work. They are programmed to maintain a constant speed, angle, and pressure throughout welding, resulting in highly precise and consistent welds.
Humans may vary in their technique or experience lapses in concentration, leading to variability in their welds' quality. Robotic welding systems have advanced sensors and cameras that detect defects or inconsistencies in real time.
These sensors identify deviations, such as improper joint fit-up, insufficient penetration, or inadequate heat input. As a result, errors are corrected immediately by adjusting parameters or stopping the process until the issue is resolved.
In contrast, manual welders may not always catch these errors during visual inspection since they rely heavily on their perception. Contrary to popular belief, robotic welding also ensures superior repeatability compared to manual welding techniques.
Once a robot program is established for a specific task, it executes it repeatedly with exceptional accuracy and precision. This level of repeatability eliminates variations caused by human factors, such as hand tremors or inconsistent techniques among different operators.
Another advantage of robotic welders is their easy access to tight spaces. Robots are designed with slim arms and compact maneuverability capabilities that allow them to reach into confined areas that may prove difficult for human welders to access comfortably.
This enhanced accessibility allows robots to perform intricate welds and improves overall quality since they achieve proper positioning for optimal heat distribution. Ultimately, it must be emphasized that while robotic welding may differ from manual welding in its execution, it should not be regarded as an inferior alternative.
With the advancements in technology and the continuous improvement of robotic systems, weld quality has reached impressive levels comparable to or even surpassing what can be achieved manually. The precision, consistency, repeatability, and ability to access tight spaces make robotic welding an excellent choice for obtaining high-quality welds efficiently and reliably.
Myth #4: Robots Can't Access Confined Spaces Like Human Welders
Robotic welding has often been criticized for its inability to access confined spaces, a task that human welders excel at. However, this myth fails to consider the advancements in robotic technology and the flexibility of modern robotic welding systems. Contrary to popular belief, robots access and maneuver within confined spaces.
One key advantage of robots over humans is their ability to operate in hazardous environments. Confined spaces often pose risks such as toxic fumes, extreme temperatures, or cramped conditions that compromise the safety of human welders.
In contrast, robots are unaffected by these factors and effortlessly navigate tight spaces without compromising their health or performance. Robotic welding systems feature innovative designs with compact structures and versatile arm configurations.
These attributes enable them to adapt to various angles and positions required in confined spaces. Many robotic arms have multiple joints that provide exceptional agility and articulation capabilities, allowing them to reach into narrow gaps or tight corners that might be challenging for human welders.
Robotic welding technology incorporates advanced sensors and vision systems that enhance spatial awareness. These sensors allow robots to perceive their surroundings accurately and avoid collisions with obstacles while operating in confined areas.
Robots execute welds even in the most challenging confined space scenarios with precision by using precise motion control algorithms and real-time feedback from these sensors. It is a misconception that robots cannot access confined spaces as human welders do.
The continual evolution of robotic technology has addressed this concern by making substantial strides in adaptability and maneuverability within tight areas. With their ability to operate safely in hazardous environments, refined arm designs, and advanced sensory capabilities, robotic welding systems have repeatedly proven that they are more than capable of carrying out precise welding tasks even within the most restricted spaces imaginable.
Myth #5: Robotic Welding Can't Handle Deviations in Parts or Materials
Robotic welding has often been criticized for its alleged inability to handle deviations in parts or materials. However, this is a common misconception that cannot acknowledge the advancements in robotic technology and the capabilities of modern robotic welding systems. Robots are equipped with sophisticated sensors and advanced software algorithms that enable them to adapt and adjust to variations in parts or materials, ensuring consistent and high-quality welds.
One of the key features that allows robotic welders to handle deviations is their ability to perform real-time monitoring and feedback during the welding process. Robots accurately detect variations in part dimensions or material thickness by integrating sensors, such as vision systems or laser scanners.
By continuously analyzing this data, the robot adjusts its welding parameters, such as torch angle or wire feed rate, to compensate for any variations encountered during the process. Robotic welding systems often come equipped with intelligent software that enables them to decide based on predefined criteria.
By programming specific tolerance ranges for part dimensions or material properties into the system, robots determine whether a particular part is within acceptable limits. If a deviation exceeds these limits, the robot can either pause and alert an operator or automatically make adjustments to ensure proper weld quality.
Many robotic welding systems are designed with flexible fixturing capabilities that accommodate variations in part geometry. Robots can securely hold parts regardless of their shape or size through advanced gripping mechanisms or articulating fixtures while maintaining precise control during the welding operation.
This flexibility ensures consistent contact between the electrode and the workpiece, even when facing irregularities or deviations. Overall, it is important not to underestimate the adaptability of modern robotic welding technology.
Robotic welders have evolved significantly and handle deviations in parts or materials with exceptional precision and reliability. Their ability to monitor real-time data, make informed decisions based on set criteria, and accommodate variations through flexible fixturing contributes to their versatility and effectiveness in a wide range of welding applications.
Myth #6: Robotic Welding is Too Expensive for Small Businesses
Robotic welding is often perceived as an expensive investment that is out of reach for small businesses. However, this myth cannot consider the many cost-saving benefits and long-term advantages that robotic welding offers, even to smaller operations. While the initial purchase and setup costs for a robotic welding system can be substantial, examining the bigger picture and considering the return on investment (ROI) over time is important.
One significant advantage of robotic welding for small businesses is increased productivity and efficiency. Robotic welders work continuously without breaks or fatigue, resulting in significantly faster production times than manual welding.
This increased productivity translates into higher output levels, allowing small businesses to fulfill larger orders in less time. Ultimately, this efficiency gain leads to increased revenue generation and stronger competitiveness in the market.
We have to consider the potentially reduced labor costs associated with robotic welding. While manual welders require ongoing salary or wages, benefits packages, and training expenses, robotic welders only require routine maintenance and occasional reprogramming.
By implementing a robotic welding system, small businesses reduce their dependence on human welders and allocate those resources to other areas of their operations or invest them in further growth opportunities. Another aspect contributing to the affordability of robotic welding for small businesses is the availability of flexible financing options provided by manufacturers or equipment suppliers.
These financing plans allow smaller enterprises with limited capital resources to gain state-of-the-art robotic systems without making a significant upfront investment. By spreading the payment over time through installment plans or leasing agreements, companies can effectively manage their cash flow while enjoying all the benefits of implementing a robotic welding solution.
It's important to note that technological advancements have significantly reduced both maintenance costs and energy consumption associated with modern-day robots. Manufacturers now offer compact robot models specifically designed for smaller workspaces or facilities with space constraints.
These compact robots occupy less floor space and require less peripheral equipment, such as safety barriers and fencing, further reducing the overall implementation costs. The belief that robotic welding is too expensive for small businesses is a misconception that overlooks the long-term benefits and cost-saving advantages that come with automation.
While initial investment costs may seem daunting, increased productivity, reduced labor expenses, flexible financing options, lower maintenance costs, and compact robot models specifically tailored for smaller workspaces make robotic welding a viable and affordable option for small businesses. By carefully evaluating the potential ROI and exploring available financing options, smaller enterprises can harness the power of robotic welding to increase their competitiveness and thrive in today's dynamic market.
Myth #7: Robotic Welders Require Extensive Programming Knowledge
Robotic welders require extensive programming knowledge. This common misconception often discourages businesses from considering the implementation of robotic welding systems.
While it is true that programming plays a crucial role in operating these machines, advancements in technology have made the process much more user-friendly and accessible. Modern robotic welding systems are designed with intuitive interfaces that allow operators to easily program and control the robots' movements.
Software packages, such as offline programming tools, enable users to create welding programs on a computer without extensive coding knowledge. These tools use graphical user interfaces (GUIs), visually representing the welding process and allowing operators to drag-and-drop commands effortlessly.
Many robotic welding systems have built-in libraries with pre-programmed weld procedures. These libraries contain varied welding techniques for different materials and applications.
Operators simply select the procedure from the library, making it unnecessary to start from scratch every time. Besides simplified programming interfaces and pre-programmed libraries, robotic welders have features like automatic seam tracking and adaptive control systems.
These technologies help compensate for potential parts deviations or material thickness variations during welding operations. By dynamically adjusting their movements based on real-time sensor feedback, robotic welders maintain precise control over the welding process without constant human intervention.
It is important to note that while some training is required to operate robotic welders efficiently, it does not need extensive programming knowledge. Most manufacturers offer training programs specifically tailored for operators who may not have prior experience with robotics or computer programming.
These programs provide hands-on instruction on how to set up, program, operate, and maintain the equipment effectively. Overall, while some complexity is initially involved in programming robotic welders, advancements in technology have simplified this process.
With user-friendly interfaces, pre-programmed libraries, and advanced features like automatic seam tracking available on modern systems, businesses overcome the myth that extensive programming knowledge is required. The focus should be on providing operators with the training to use the tools effectively and optimize their productivity rather than being deterred by the misconception of complex programming requirements.
Myth #8: Robotic Welding Stations Take up Too Much Space
Robotic welding stations take up too much space. One of the common misconceptions about robotic welding is that it requires a large amount of floor space, making it impractical for smaller manufacturing operations. However, this myth fails to consider the advancements in robotic technology that have led to more compact and space-efficient systems.
Modern robotic welding stations are highly versatile and adaptable, allowing them to fit into various production layouts. To begin with, manufacturers now offer smaller and more streamlined robot models specifically designed for limited spaces.
These compact robots occupy less floor space and have a reduced footprint because of their slim design. This new design allows businesses with limited real estate to integrate robotic welding into their operations without compromising productivity or workflow.
Advancements in robot arm architecture have significantly reduced the footprint of robotic welding stations. Collaborative robots, or cobots, are an excellent example of this innovation.
Cobots work alongside human operators safely. They have a considerably smaller arm reach compared to traditional industrial robots, resulting in a reduced spatial requirement for installation.
Integrating robotic welding cells optimizes floor space by eliminating the need for large safety enclosures around each workstation. Traditionally, manual welders require significant safety buffers because of the inherent risks involved in welding processes.
In contrast, robots can be programmed and equipped with advanced sensors that ensure accurate weld placement and prevent collisions or accidents without extensive enclosures. The perception that robotic welding stations take up too much space is outdated and no longer applicable in today's manufacturing landscape.
Advancements in robotics technology have led to more compact and efficient systems that easily fit into smaller production environments while maintaining high levels of productivity and safety standards. By embracing these modern solutions, businesses of all sizes benefit from the advantages offered by robotic welding without sacrificing valuable floor space or hindering operational efficiency.
Myth #9: Robotic Welders Have No Use Outdoors
Robotic welders have long been associated with indoor manufacturing settings, leading to the misconception that they have no use outdoors. However, technological advancements and the development of ruggedized robotic systems have shattered this myth. In fact, robotic welders are increasingly being deployed in outdoor environments where welding tasks are required.
One main reason robotic welders find utility outdoors is their ability to withstand harsh weather. These machines have protective enclosures and sealing mechanisms that safeguard them from dust, moisture, and temperature variations. They also have advanced cooling systems to prevent overheating in extreme temperatures, making them suitable for outdoor applications, such as construction sites, shipyards, oil rigs, and pipelines.
Many industries require welding operations in remote locations or areas that pose safety risks to human welders. Robotic welders offer a safer alternative by eliminating the need for manual intervention in hazardous environments, such as high altitudes or underwater welding tasks.
They can be programmed to perform complex welding operations while minimizing human exposure to dangerous conditions. Another advantage of using robotic welders outdoors is their ability to adapt to various terrains and work surfaces.
These machines have mobility features like tracks or wheels that enable them to easily navigate uneven terrain or rough surfaces. Whether it's a wind turbine blade requiring repair at height or a large structural component needing on-site welding, robotic systems handle these challenges efficiently.
Outdoor welding often involves larger-scale projects where precision and consistency are crucial for high-quality results. Robotic welders excel in meeting these demands by consistently reproducing accurate welds without operator fatigue or human error.
Advanced sensors and vision systems allow these machines to detect deviations from the intended path and adjust accordingly within milliseconds—ensuring precise positioning of the welding torch even on irregular workpieces. Dismissing the notion that robotic welders have no use outdoors would be a grave oversight.
Ruggedized systems, their ability to withstand harsh conditions, navigate challenging terrains, and perform in hazardous environments has expanded their application beyond traditional indoor manufacturing settings. The deployment of robotic welders outdoors not only ensures improved safety for workers but also enhances productivity and weld quality in various industries.
Myth #10: Robotic Welders are Incompatible With Existing Equipment
Robotic welders are often considered incompatible with existing equipment because of concerns about integration and adaptability. However, this belief is a misconception that doesn't recognize the tremendous advancements in robotic technology.
Modern robotic welders are designed with significant flexibility and compatibility in mind, making them capable of seamlessly integrating into existing manufacturing setups. One of the key reasons robotic welders are compatible with existing equipment is their ability to adapt to various welding processes and techniques.
They can be programmed to mimic the exact movements and actions of skilled human welders, ensuring a smooth transition from manual welding to automated systems. Modern robotic welders have advanced sensors and vision systems that precisely detect and adjust for variations in workpieces or materials.
Integration concerns also stem from worries about communication between different machinery within a manufacturing environment. However, many robotic welding systems come equipped with open architecture control software that enables seamless connectivity with other equipment on the production line.
Robots easily communicate and exchange data with other machines, such as CNC cutting systems or material handling devices, streamlining operations and ensuring compatibility. Manufacturers often fear retrofitting their existing infrastructure to accommodate robotic welders will be overly complicated or costly.
However, many robotics companies offer flexible solution packages that include modular robot cells specifically designed for easy integration into various production environments. These pre-engineered cells fit into floor space while providing all the functionalities for efficient welding operations.
It is important to note that compatibility issues arise when there is a lack of understanding or expertise in implementing robotics within an existing setup. Collaborating closely with experienced integrators specializing in robotic automation eases these concerns by offering customized solutions tailored to specific needs.
These experts possess extensive knowledge about integrating robotic welders seamlessly into different manufacturing processes while maximizing productivity. The belief that robotic welders are incompatible with existing equipment is unfounded, given the current state of robotic technology.
Programming, control software, and modular design advancements have made these systems highly adaptable and versatile. By leveraging integrators' expertise and investing in flexible solutions, manufacturers confidently incorporate robotic welders into their existing infrastructure, ensuring compatibility and reaping the benefits of increased productivity and efficiency in their welding operations.
In Sum
Debunking myths about robotic welding has been like learning to ride a bike - a little shaky at first, but WOW! what a fun and exciting ride it turned out to be!
We wobbled through claims that robots steal jobs and fumbled with worries about costs. But after cruising through the facts, we've seen that robotic welding offers a smooth and thrilling ride ahead. Like mastering your balance on two wheels, we've uncovered the immense potential of robotic welding when embraced fully.
Integrating this technology promises greater efficiency, higher precision, and enhanced productivity - just like zipping around on a bike opens up new adventures and possibilities. By welcoming robotic welding into manufacturing, instead of letting misconceptions cause a crash, industries can look forward to a bright future of innovation.
Did I miss any myths? Let me know!