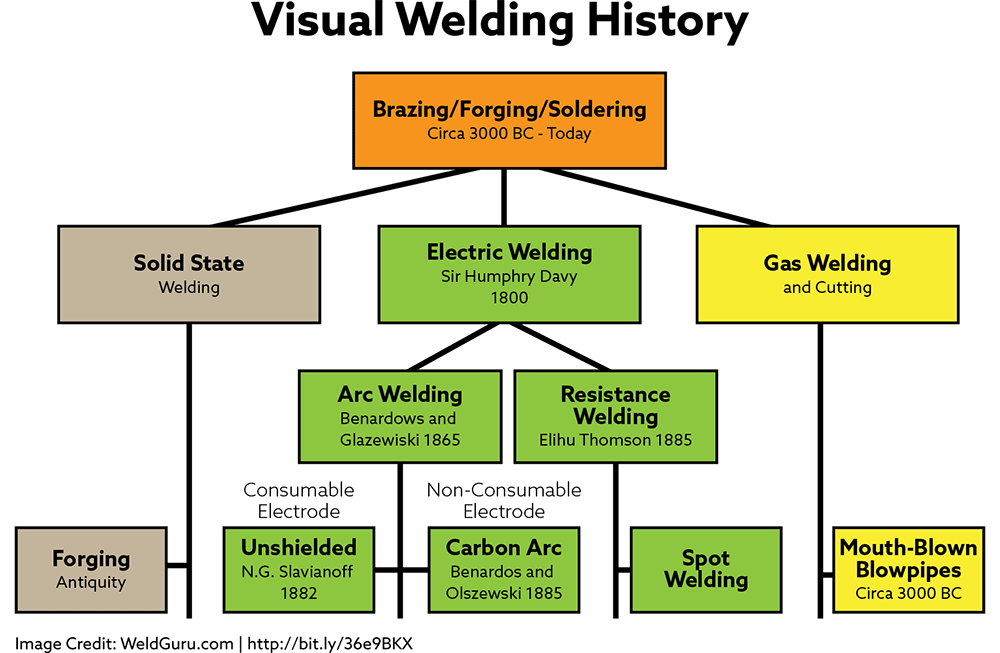
Starting this journey, I mentioned there are several dozen welding methods to choose from. Helping to keep us on a steady course, I followed the Visual Welding History, illustrated by WeldGuru.com:
So far, we’ve explored nearly the whole welding family tree, leaving us with arc welding. In this category alone, there are dozens of arc welding varieties with enough information to fill libraries.
Of that myriad of arc welding methods, four are the most commonly used:
- Flux Cored Arc Welding (FCAW)
- Gas Metal Arc Welding (GMAW/MIG)
- Gas Tungsten Arc Welding (GTAW/TIG)
- Shielded Metal Arc Welding (SMAW)
These are the next four articles in our series on welding. We’ll finish things up with a look at how welding is developing.
Arc Welding Basics
Regardless of the method, arc welding uses the same method. Illustrated in the figure below is a power source connected to the working piece and referred to as a hot cable to an electrode holder. The holder contacts with the welding electrode, creating an arc across the gap.
The arc itself is a current flowing between two electrodes through ionized gas. Negatively charged cathodes and positively charged anodes create temperatures approaching 6,600 ºF at the tip, hot enough for melting the base metal and electrode, creating a pool of melted metal. The pool solidifies, resulting in a fusion bond.
An arc during the welding process has more than one job:
In welding, the arc not only provides the heat needed to melt the electrode and the base metal but, under certain conditions, must also supply the means to transport the molten metal from the tip of the electrode to work. Several mechanisms for metal transfer exist. Two (of many) examples include:
Surface Tension Transfer—a drop of molten metal touches the molten metal pool and is drawn into it by surface tension.
Spray Arc—the drop is ejected from the molten metal at the electrode tip by an electric pinch propelling it to the molten pool.
Since there must be an ionized path to conduct electricity across a gap, the mere switching of one of the welding currents with an electrically cold electrode posed over it will not start the arc. The arc must be ignited. This is caused by either supplying an initial voltage high enough to cause a discharge or touching the electrode to work and then withdrawing it as the contact area becomes heated.
In Sum
The information above provides a general summary of arc welding. The next four articles explore the four most common methods in-depth.