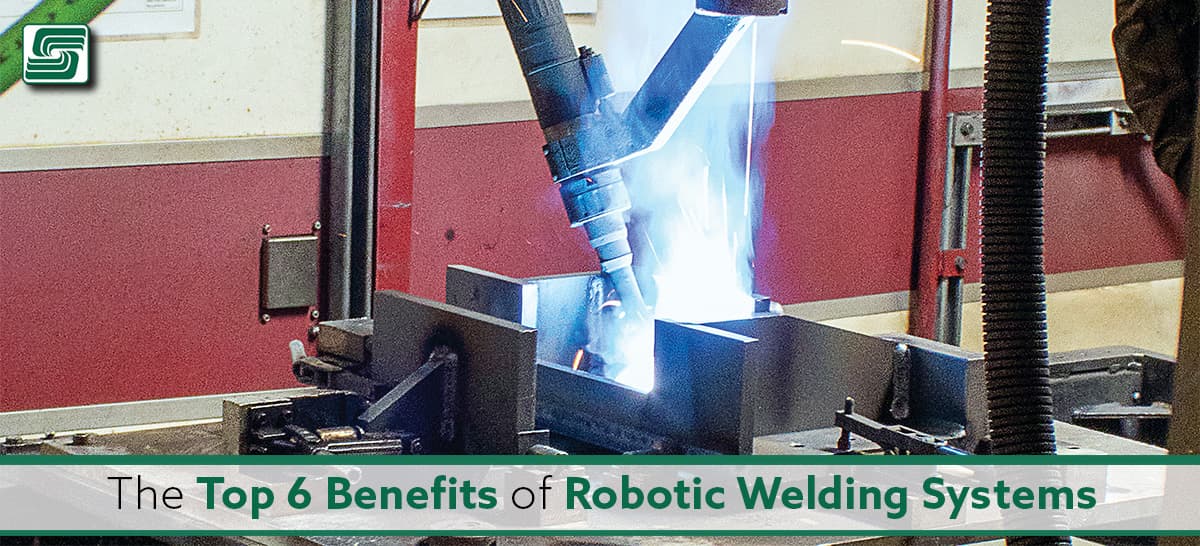
With manufacturing processes, there are plenty of options available. Each has its advantages and disadvantages, which is why so many manufacturers take a balanced approach that combines different production methods.
There is no perfect process for every job and every manufacturer. But that doesn’t mean you shouldn’t focus on streamlining operations and finding the right balance between methods.
Welding is a fundamental manufacturing process and an essential part of an assembly, and it can also directly produce finished products from raw materials. For example, when using a robotic welding system, you reduce operating costs and optimize your team’s performance by automating this process. A robotic welding system is an automated system that performs the duties of a human welder.
There is a myriad of benefits of a robotic welding system, but we’re listing six for your consideration.
Benefits of Robotic Welding Systems
Improved Quality Control
For production, quality control is critical. Suppose you cannot guarantee the quality of the end product. In that case, customers will shy away, creating missed sales opportunities and even losing customers. If that's not bad enough, think of the terrible reputation your company could develop.
Even if you're making something for internal use, poor quality control may result in a lack of confidence for those parts. Poor quality leads to more expenses and time spent attempting to repair or replace the faulty items.
Robotic welding systems offer greater quality control compared to manual welding because of the level of monitoring, documentation, and testing they perform. This level of oversight means quickly identifying and dealing with weld issues before the project moves to its next stage.
Speed and Efficiency
The most common benefit of a robotic welding system is its speed and efficiency. Robotic welders perform quickly, with some systems able to handle hundreds of welds per hour.
The speed at which robots weld significantly impacts the bottom line. In today’s competitive manufacturing environment, speed is king; however, many manufacturers struggle to speed up production.
Robotic welding systems quickly increases the speed at which a team can produce parts—especially true when working with complex parts. Robots can weld multiple parts simultaneously, eliminating worry about slowing production down because one part takes longer to complete than the others.
Using multi-head welders extends the speed and efficiency of robotic welding systems. Multi-head welders weld multiple parts simultaneously, improving speed and efficiency even further.
Reduced Costs
Robotic welding systems offer significant reductions in costs because they work with various materials, eliminating possible restrictions for welding certain metals.
Programming the robots to use different welding techniques to suit the material and part means there’s no need to invest in additional equipment. This programmability helps reduce the upfront costs of purchasing the robotic weld systems and may even reduce the cost of operation.
Robotic welding systems are simpler to operate, resulting in fewer maintenance costs. And those reduced costs aren’t the only way that robotic welding systems help reduce the overall manufacturing costs. They also increase productivity, allowing manufacturers to operate at a greater capacity, producing more parts with the same amount of money invested.
Automation of Repetitive Tasks
Another benefit of robotic welding systems is their ability to automate repetitive tasks, especially true when the same movements are required for every weld. Programming these tasks includes positioning the robot, the axes, the torch, and more, and repeating the same actions ensures accurately repeating each weld.
Robotic welding systems also carry out other repetitive tasks, such as:
- Feeding materials into production
- Measuring parts
- Testing finished products
- Simplifying and repeating the tasks on each part or product
Repeating each weld in the same way while measuring and testing parts in the same manner, every time helps increase productivity and reduce costs.
Greater Flexibility for Manufacturers
One of the significant benefits of robotic welding systems is their flexibility. This flexibility applies to several processes, such as programming, material handling, and more. Streamlining the many welds and tasks from programming the robotic weld system helps reduce the overall cost of ownership of robotic welding systems.
If materials are hard to move and weld, a robotic weld system makes things easier for us lowly humans. The less things we touch, productivity goes up while overall production costs go down.
Reduce Waste
In welding, the odds of weld imperfections is greater than zero. Those imperfections may be the result of the metal type or the system setup. Even when using the best welding techniques and materials, imperfections are still possible.
Robot welding systems help reduce waste in a variety of ways. For example, program them to use the ideal settings for the specific type of metal, reducing the chances of creating imperfections in the weld.
Programming the robots to perform several quality checks also ensures sound welds that lowers the chances of mistakes resulting in waste.
Reduce Human Error
We make mistakes: it’s just a fact of life. For this reason, robotic welding systems help reduce human error in production.
Programming a robotic welding system to follow a set path allows it to move in a pre-determined pattern. This helps reduce the risk of human error, like dropping materials or moving the torch at the wrong angle. Programming the robot’s sensors to identify whether the parts are being placed in the correct position stops the process if it senses a problem.
By reducing human errors, robots help create high-quality products, boosting your brand image, improving customer satisfaction, and even extending your product lifecycle.
In Sum
In production, quality control is vital. If you can't guarantee quality, your customers will shy away, resulting in missing sales opportunities, losing customers, and creating a terrible reputation.
Important benefits of using a robotic welding system include:
- Increasing speed and efficiency
- Reducing costs
- Greater flexibility
- Automating repetitive tasks
- Reducing of waste
And, most importantly, they reduce the chances of those pesky human errors!