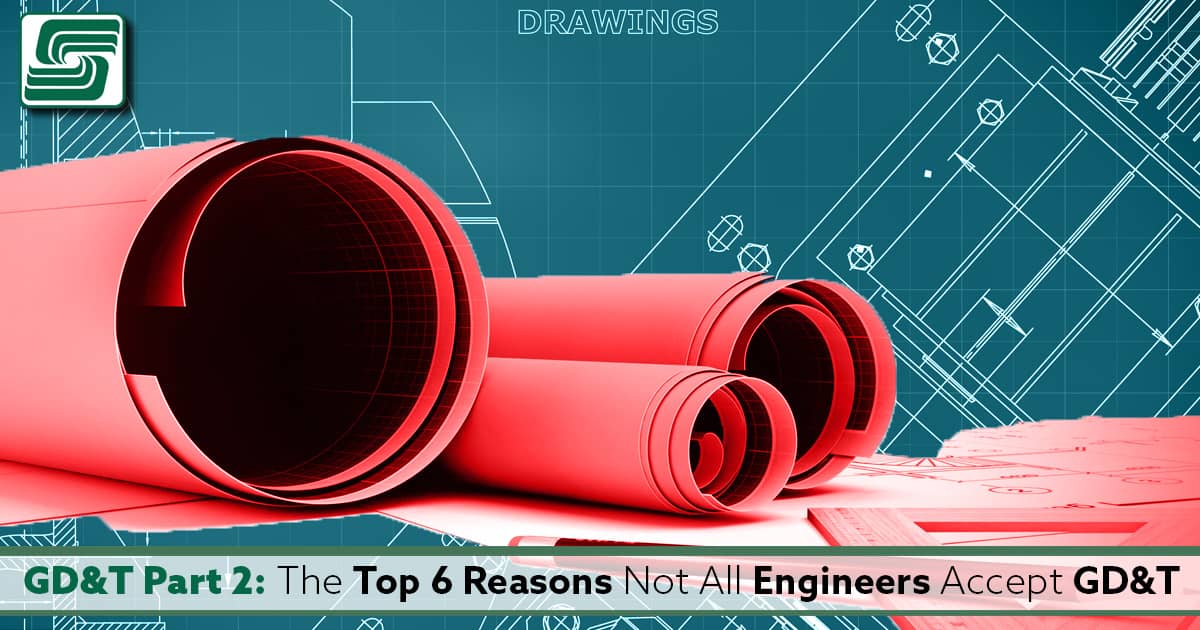
In Part 1, we explored the evolution of Geometric Dimensioning and Tolerancing as it became the communication standard in industrial development and planning. Despite its many benefits, not all engineers take advantage of GD&T. Here, in Part 2, we explore six reasons engineers don't use it.
GD&T's Use Isn't Universal
Despite the standardized uses Geometric Dimensioning and Tolerancing bring to manufacturing, many companies disregard them. Here are reasons smart engineers ignore an important tool.
If you’ve ever worked in manufacturing, you have probably heard of GD&T. Many engineers are afraid to use it because they think it is an overly complicated set of rules that only apply to aerospace or medical device manufacturers. Others don’t know where to find the standard or what it contains. There are also misconceptions about using GD&T and its impact on work.
Here are six reasons engineers avoid using GD&T in their design processes.
1. GD&T is Complicated and Confusing
GD&T is not a simple set of rules. When working with it, many engineers will find the amount of information confusing. Confusion and misunderstanding are often the sources of fear around a design tool.
When working with GD&T, engineers must understand their application’s general principles and specific rules. The relationship between the two is often what confuses people. The general principles of GD&T are specific to manufacturing and unrelated to the product’s end-use. The rules related to the specific application within the subject being designed and the two are related, and understanding them is necessary to use GD&T effectively.
Since engineers will work with GD&T differently, they need to understand how to apply the rules and principles to their specific applications. Not all rules are created equal. Some rules are more general, and some are very specific. Some rules only apply to a specific application, and some rules overlap between applications.
2. Too Many GD&T Variants
The idea of geometric tolerance being too many variants is a common misconception about GD&T.
While there are many rules for geometric tolerance, there is only one standard for manufacturing. There are no variants of geometric tolerance. There is only one standard: ISO, ASME, or SAE. There is one standard for both the principles and specific rules. There is no variant of geometric tolerance.
When people think there are too many geometric tolerance variants, they usually refer to the specific rules. While there are many rules for geometric tolerance, they only apply to specific applications. There are specific rules for applying geometric tolerance that only apply to that specific application.
For example, there are specific rules for applying geometric tolerance to an assembly, but not a variant of geometric tolerance. There are specific rules for applying geometric tolerance to a medical device. These are not variants of geometric tolerance. There is only one standard for geometric tolerance.
3. It’s Incredibly Difficult to Measure Parts to a Precision
People often think measuring parts precisely using geometric tolerance is incredibly difficult. While the design process is difficult, measuring precision parts is possible and reasonably easy.
Engineers work with tiny parts and need high precision. Using geometric tolerance helps them to create parts that fit together at a higher level of precision. GD&T allows engineers to design parts that fit with a specific amount of room for error.
When using GD&T, engineers design parts that are the correct size within specified tolerances; they know how close the parts must be to each other and how much room they need to account for manufacturing errors. They know the room they need to account for the human element in the manufacturing process.
When measuring parts to a precision, engineers use gages and fixtures. They account for all variables that could affect the measurement of the part. They account for variables like the operator, machine conditions, tool wear, and environmental conditions. They may also use measuring methods like statistical process control (SPC) to improve accuracy and precision.
4. It Masks Mistakes Instead of Helping with Corrections
Some engineers think GD&T masks mistakes instead of helping with corrections. Many engineers think they need to make the correct part the first time and design something that makes little sense.
When designing with GD&T, they expect engineers to design the correct part. They know what the correct part is supposed to do and how it functions with other parts. We expect them to design the part to meet the application’s requirements. We expect the engineer to:
- Meet the application’s requirements when reviewing the design.
- Understand the design and build the part using the correct materials
- Ensure the part functions as expected
When using GD&T, we expect the engineer to design parts that meet the application’s requirements and the reviewer to help the engineer ensure their design meets the application’s requirements.
Using geometric tolerance ensures the design functions properly but does not ensure the component looks pretty or aesthetically pleasing.
5. Engineers Don’t Feel Comfortable Using It
Many engineers don’t feel comfortable using GD&T. They are worried that they don’t use it correctly or they don’t understand it well enough to use it correctly.
When engineers don’t feel comfortable using GD&T, they are worried that they don’t know how and when to use it. We expect the engineer to know when they need to use geometric tolerance, identify situations where the use of geometric tolerance would benefit their design, and know where to find the standard for geometric tolerance.
They must understand what it contains and how to use it properly, and we expected them to have a general understanding of where to apply specific rules.
6. Some Companies Don’t Require It • Engineers are Risk Averse
Some companies don’t require the use of GD&T. Some companies use a company-specific standard. Companies use this to maintain consistency in their designs and maintain internal standards.
When a company doesn’t require the use of GD&T, many engineers are risk-averse. They are worried that they will make mistakes and cause their designs to fail.
In Sum
The idiom is that you can lead a horse to water, but you can't make it drink, which means you cannot force someone to do something if they do not want to, but you can give them the opportunity.
GD&T's symbolic language provides consistent terms and symbols, reducing confusion as a project moves from desk to desk while ensuring precision and accuracy throughout the life of that project.
That is, of course, if engineers use it.
Hopefully, by shedding some light on this topic, more engineers will reconsider GD&T's application and benefits instead.
Time will tell.