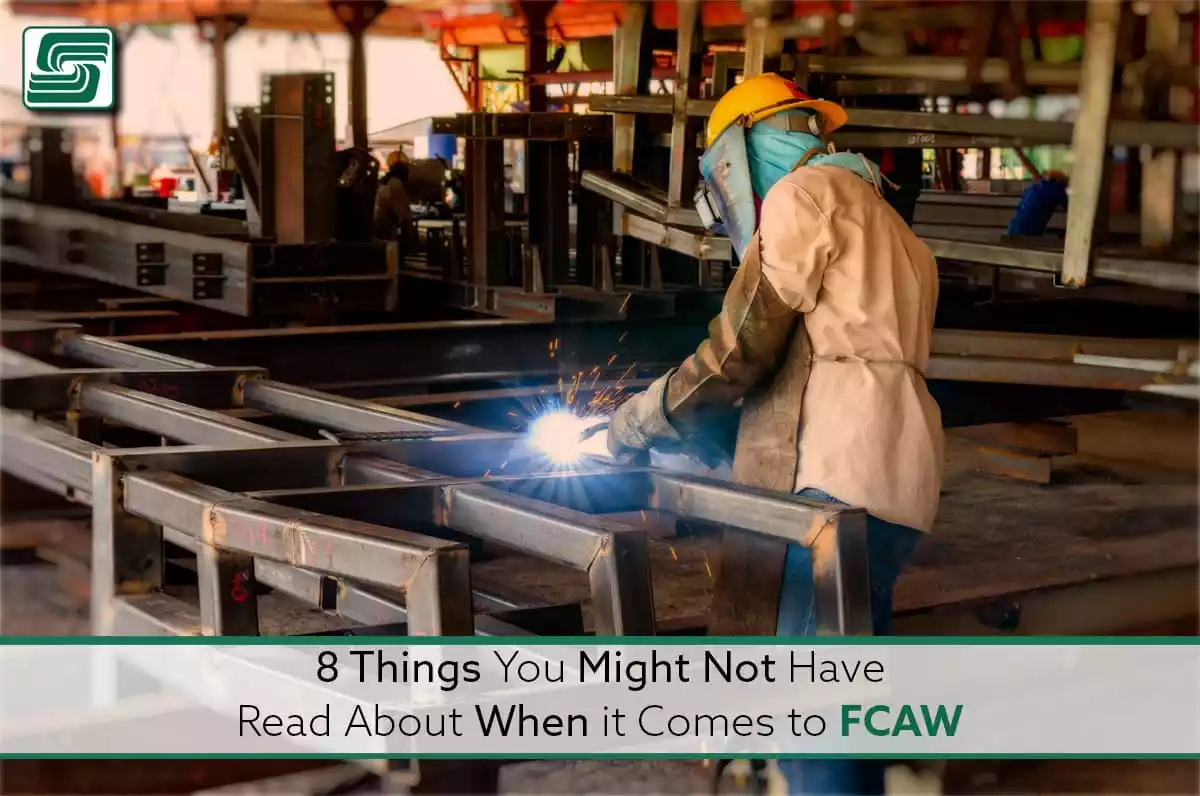
Welding is a complicated process requiring skill, experience, and knowledge. One of the most challenging aspects of welding is mastering the unseen, which refers to the aspects of the welding process that are not immediately visible. Flux-cored arc welding (FCAW) is a technique that has become increasingly popular in recent years because of its versatility and effectiveness. However, to get exceptional results with FCAW, you need to deeply understand the topics surrounding it.
This article—first of a series of three on FCAW—explores the essential FCAW topics that every welder needs to know.
FCAW's Deposition Rate
One of the most significant advantages of FCAW is its high deposition rate. Compared to other welding processes, FCAW can deposit more metal in a shorter amount of time because of the continuous electrode wire used in FCAW, which allows for a higher rate of metal deposition.
The high deposition rate of FCAW makes it an ideal choice for welding projects requiring fast metal deposition. For example, heavy machinery or large structural construction often uses FCAW as the preferred welding process.
However, it's important to note that the high deposition rate of FCAW can also lead to some challenges. For instance, the high metal deposition rate causes issues controlling the weld pool and maintaining the desired bead shape. To overcome these challenges, welders need an understanding of the factors affecting penetration and bead shape.
Factors Affecting Penetration and Bead Shape
Penetration and bead shape are two essential aspects of welding that significantly affect the weld's quality.
Several factors affect penetration and bead shape in FCAW, including:
- Welding current
- Electrode diameter
- Travel speed
- Electrode extension
Welders need to understand how these factors affect the welding process and adjust them accordingly to achieve the desired results.
For instance, increasing the welding current increases penetration depth while decreasing the travel speed causes a wider bead.
Similarly, using a smaller electrode diameter leads to deeper penetration, while using a larger electrode diameter results in a wider bead.
Welders need to experiment with these variables to find the right settings for each project, considering the metal welded, the thickness of the metal, and the desired outcome.
FCAW for Non-Ferrous Metals
While FCAW is common for welding ferrous metals like steel, it welds non-ferrous metals like aluminum and copper.
However, welding non-ferrous metals with FCAW requires some additional considerations. For instance, the electrode and flux used in FCAW for non-ferrous metals differ from those used for ferrous metals. Non-ferrous metals also have different thermal properties than ferrous metals, affecting the welding process.
To weld non-ferrous metals with FCAW, welders must use a specialized flux designed for these metals—based on the specific metal and the desired outcome.
Welders also need to adjust the welding parameters, such as the welding current and travel speed, to account for the differences in thermal properties between ferrous and non-ferrous metals.
Alternative FCAW Techniques
While FCAW is a versatile welding technique, some alternative techniques or variations are better suited for specific applications.
For instance, dual shield welding is a variation of FCAW that uses a shielding gas besides the flux—ideal for welding thick metals or metals that require deep penetration.
Another alternative technique is self-shielded flux-cored arc welding, which uses a flux that produces its own shielding gas—ideal for outdoor welding or welding in windy conditions, as the self-generated shielding gas provides better protection from the elements.
Storage and Handling Requirements
Proper storage and handling of FCAW electrodes and flux are essential for maintaining the quality of the welding process.
FCAW electrodes and flux are hygroscopic, meaning they absorb moisture from the air, affecting the performance of the electrodes and flux, which leads to porosity in the weld.
Storing the FCAW electrodes and flux in a dry, cool place and a sealed container prevents moisture absorption when not in use.
Welders should also avoid handling the electrodes and flux with bare hands because the oils and moisture from the skin contaminate the materials.
Cost-Effectiveness of FCAW
FCAW is a cost-effective welding technique saving welders time and money. Compared to other welding processes, FCAW requires fewer welding passes to achieve the desired results, which saves time and reduces labor costs. The higher deposition rate means using less filler material to complete a weld.
However, the cost-effectiveness of FCAW varies depending on the specific project and the equipment and materials used.
Consider the cost of the FCAW equipment, electrodes, and flux and the labor and time required to complete the project when determining FCAW's cost-effectiveness.
FCAW Certifications and Qualifications
FCAW welding requires appropriate certifications and qualifications. The American Welding Society (AWS) offers several certifications for FCAW welding, including the Certified Welding Inspector (CWI) and Certified Welding Educator (CWE) certifications, demonstrating the knowledge and skills required to perform FCAW welding to industry standards.
Welders should also be familiar with the safety requirements for FCAW welding, including proper ventilation and personal protective equipment (PPE), like welding helmets, gloves, and safety glasses.
Specialized FCAW Variants
Finally, there are several specialized FCAW variants designed for specific applications.
For instance, gas-shielded flux-cored arc welding is often used for welding pipelines, providing better control over the welding process and producing high-quality welds.
Underwater FCAW is another specialized variant for welding underwater structures, such as oil rigs or bridge supports.
Welders should be familiar with the specific requirements and techniques for these specialized variants of FCAW to ensure the best results.
In Sum
Flux-cored arc welding is a versatile and cost-effective technique producing exceptional results when performed correctly.
However, to master the unseen with FCAW, welders must truly understand its characteristics. From understanding the factors that affect penetration and bead shape to selecting the right equipment and materials, this article has covered everything you need to know to take your welding skills to the next level.
By mastering these essential FCAW topics, you can become a more skilled and knowledgeable welder and achieve exceptional results with every project.