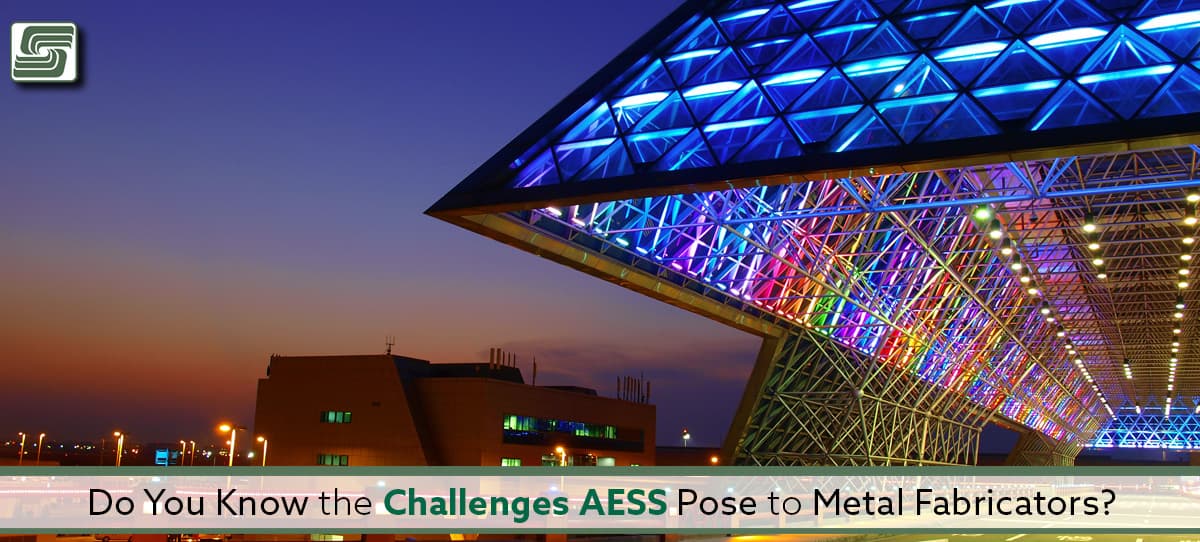
Architects love to use steel in their designs for a good reason. Steel is a material that can transform completely. Engineers integrate metal into nearly any design, from exposed rafters to hidden girders.
However, as with any piece of construction equipment or materials, there are some limitations to using structural steel in projects. After working on several projects that required exposed steel and learning about issues presented by architects in other projects, it’s clear that there is a bit of a learning curve when designing with structural steel.
In this blog post, we’ll understand why that is and what you should know before moving forward with such a project.
What is AESS?
Steel to a building is like a skeleton is to a body. Think about it: there's a reason those modern buildings aren't made from wood.
The critical aspect of AESS is in part of the name: 'Exposed.' Architects using AESS in projects don't want their prize designs turned ugly by rusting metal. Simultaneously, the aesthetics partner with structural specifications resulting in pieces of art made from steel.
In her CICS AESS Guide, Terri Meyer Boake, a Canadian architecture professor, explains why the evolution was necessary:
"If the creation of connections requires an excessive degree of unique fabrication details, the designer can price the project out of existence. The method of preparing and finishing the connections can also radically increase costs. Specialized welds and unnecessary ground and filled finishes increase fabrication and erection expenses."
Boake created this video giving us an introduction to the concepts behind AESS designs:
AESS Evolutionary Issues
Another problem facing the advent of AESS was communication and consistency. What one architect would call a great-looking connection may not be what a different person says. Creating a set of guidelines levels the terminology field so different fabrication companies would work on identical specifications.
The question remains, what criteria should be considered while creating these guidelines? Boake listed seven:
- Connections mostly bolted or welded: different aesthetics requiring differing levels of finish tolerances required at fabrication and erection: different as a function of scope and complexity.
- Access to detail to perform required finish: greater concern for workmanship may mean altering the detail or its location to allow access for different types of tools
- Degree of expression: the complexity of structure and connections
- Size and shape of structural elements: different detailing requirements and use infers a different approach to detailing and finish
- Interior or exterior setting: weathering issues, need to fire protect, the potential for impact damage
- Paint finish, corrosion resistance, fire protection: depending on the relative thickness of the finish material, more or less care may be required when preparing the surface, edges, and welding of the steel.
Form, Fit, Finish
Boake condenses these seven factors into Form, Fit, and Finish.
"Unlike standard structural steel that is hidden from view, architecturally exposed structural steel is a key element of the expression of the architectural design."
Form
The design implies a greater emphasis on the form of steel. The look of welded or bolted connections may have greater importance than structural integrity. However, structural integrity is still a vital overall design consideration.
Fit
The more intricate the design, the more difficult it is to fit. Accuracy is vital; any mistake early in the erection of a structure carries downstream, making the initial error something significant.
Finish
Although the finish is the last construction phase, Boake wrote that early planning stages must include this final step.
"Finishes will vary in exposed steel both as a function of the design intention and issues relating to weathering, interior or exterior exposure and fire protection….high-gloss finish will reveal every imperfection so will require more fastidious fabrication…galvanizing itself has issues with consistency of finish, and its selection may accompany a less polished selection of details."
AESS Categories
Architecturally exposed structural steel falls under five categories:
- AESS 1: Basic Elements – basic elements needing enhanced quality
- AESS 2: Feature Elements not in Close View – details further than 20 feet away
- AESS 3: Feature Elements in Close View – details up to 20 feet away
- AESS 4: Showcase Elements – dominant elements used where the designer intends the form is the only element featured
- AESS C: Custom Elements – Allowing for a custom selection of any characteristics or attributes used to define other categories
Bill Andrews, from the structural engineering firm Walter P Moore, explains how the creation of these categories clarifies previous code editions:
"This is a dramatic improvement over the previous code edition in terms of better clarity, articulating expression… and giving everyone a better understanding of relative costs when choosing AESS and at what level."
That same article from Modern Steel Construction illustrates some context on the factors influencing the decision to categorize the level of AESS.
Visibility
If the steel can't be seen, then it isn't AESS. If the structural steel is specified as AESS, expect longer lead times and increased costs in fabrication. Those times and costs are significantly reduced by taking the time to make informed decisions.
Viewing Distance
Picking out details on an object becomes tougher the further away that object is viewed. When considering the viewing distance, 20 feet is essential. Category 2 occurs when structural steel is greater than 20 feet away. Category 3 represents distances up to 20 feet.
Location
Placing the structural steel inside or out significantly impacts the kinds of coatings and protection added to the surface. For example, outside steel needs corrosion protection. Regardless of location, connections and joints need extra work to hide seams. That extra sealing also creates another layer of weather protection by keeping water out.
Lighting
Lighting and sight lines impact AESS regardless of where the structural steel is located. High ceilings with low lighting hide details, and better lighting expose more imperfections. Sightlines become important when exposed steel is outside.
Coatings
Coating types need to be coordinated with design intents for AESS. Glossy surfaces show more blemishes, doubly so when combined with good lighting. Thicker layers do a better job of hiding any imperfections. The location of the AESS and how its viewed needs to be decided in the planning stage.
Style
Tectonic and Plastic are the two basic styles regulating the type of designs of AESS. Tectonic styles show more details of the steelwork and emphasize bolted construction. When using the plastic style, the look is uniform and smooth, giving a seamless appearance. The desired finished level is an important piece of the puzzle when determining the AESS characteristic.
Adjacency
Structural steel is an excellent material for creating higher tolerances with greater precision during fabrication. The AISC Code distinguishes between precision and tolerance levels when determining the appropriate AESS category. Tighter tolerances may not be needed, but that's dependent on the composition's structure.
Plan for the Best: Prepare for the Worst
Because AESS surfaces damage easily, the more fabrication performed in the shop, the better. One result of this decision adds headaches for the fabrication shop. They need to figure out how to fit large pieces of structured steel on the back of a semi-flatbed.
Moreover, protective layering needs room to effectively protect the AESS during its road trip. Avoiding contact between heavy pieces of steel is challenging. Often, large constructs are shipped separately, exponentially increasing shipping costs.
Despite the preparation and protection, there's no guarantee the AESS will arrive in pristine condition at the job site. Once the truck drives away, neither the metal fabrication company nor the construction crew controls highway events.
Life happens despite our best planning.
In Sum
AESS fabricators plan for the best yet prepare for the worst. They include a few gallons of the matching finish, so if any portions of the steel have blemishes, installation crews touch those areas up. AESS metal fabricators know they packaged the structural steel securely, so it arrives at the job site without catastrophic damage, and the architect is happy.
Architecturally exposed structural steel is considered when architects and planners decide to use it. If everything goes as planned, the result is a beautiful piece of artwork.