
Entering the world of metal fabrication highlights many complexities that become even more intricate with time.
The core of this industry lies in the complex metal fabrication process, which involves creating metal structures through:
- Cutting
- Bending
- Assembling
Complex fabrication is an extensive process that demands expertise in precision engineering to execute successfully. This work often entails large-scale projects, custom designs, and complex assemblies.
Complex metal fabrication is vast as it serves multiple industries, from construction to automotive and everything in between.
This discipline commands a precise understanding of various metals and their properties - how they bend, react under heat or pressure, and combine.
It's an art as much as a science, requiring the careful consideration of design specifications while respecting the natural laws governing metals.
The Genesis: A Brief History and Evolution of Metal Fabrication
Metal fabrication is rooted in ancient times when man first discovered copper. Over time, this gave way to bronze, iron, steel, and now an array of diverse metals used across industries worldwide.
It was during the Industrial Revolution that Precision Engineering was born, transforming metalworking into a meticulous science.
As technology progressed through centuries, so did the techniques used for fabricating metals; where people relied solely on manual labor, now there are machines designed for precision cutting or robotic arms capable of assembling complex structures within minutes.
Today's technological advancements offer laser-cutting techniques catering to large-scale projects seamlessly, ensuring operational efficacy.
The Importance: Metal Fabrication's Crucial Role Across Various Industries
Metal fabrication is crucial across various industries because it creates custom designs with precise measurements which are impossible using traditional methods. Industries such as aviation, construction, automotive, and naval require metal parts designed to fit specific purposes and meet certain specifications. As its role becomes increasingly critical, complex metal fabrication has grown exponentially, fostering innovation by providing solutions for large-scale projects demanding high detail and precision.
Whether creating intricate components for aerospace utilities or crafting durable frameworks for architectural marvels, complex metal fabrication holds the key.
Unveiling the Metallic Backbone: Steel, Aluminum, Copper, and Brass
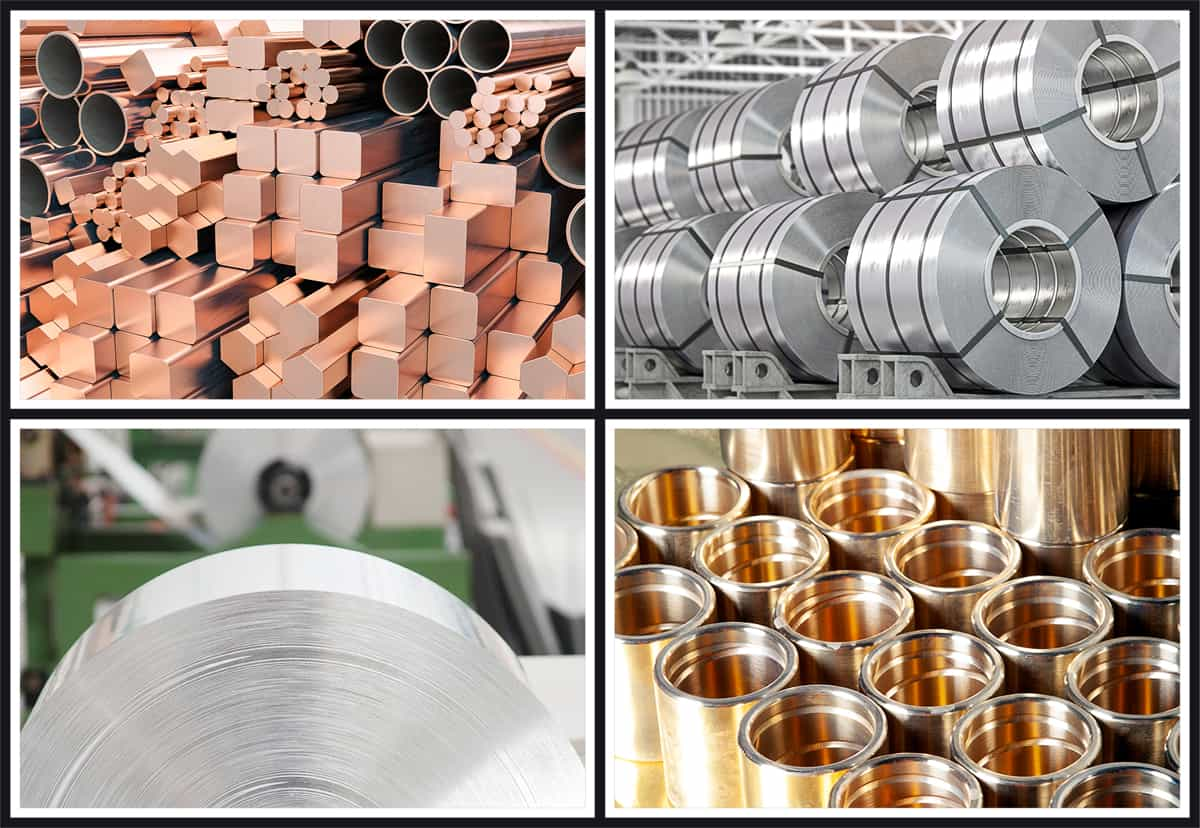
In metal fabrication, the material choice is essential.
- Steel: Known for its superior strength and durability, it has long been a stalwart in large-scale projects ranging from skyscraper construction to automobile manufacturing. Its versatility in alloy combinations further enhances its utility in complex metal fabrication.
- Aluminum: Lighter than steel but equally robust, aluminum distinguishes itself through its resistance to corrosion and pliability. These attributes render it optimal for applications where weight considerations are critical, such as aerospace engineering and vehicle production.
- Copper: While not typically associated with its relatively lower-strength structural components, copper's exceptional thermal and electrical conductivity earmarks it as an essential material within electrical systems and heat exchangers — areas where precision engineering truly shines.
- Brass: An alloy of copper and zinc boasting malleability, machinability, corrosion resistance, and aesthetic appeal. Its golden hue has made it a favorite for custom designs in ornamental fixtures while also being utilized in musical instruments owing to its acoustic properties.
Fundamental Processes: Cutting-Edge Precision
The basic processes within metal fabrication are cutting, bending, and assembling; each process is intrinsically entwined with precision engineering.
Cutting
In cutting operations, whether using traditional methods like shearing or advanced laser cutting techniques, the objective remains unaltered: achieving clean cuts with minimal waste material or thermal distortion.
Work of this nature requires meticulous calibration of parameters such as feed rate or laser power density depending on the type of metal and the desired cut quality.
Bending
Compared to cutting operations, which remove material from workpieces, bending seeks to deform the metal instead.
Here, the challenge lies in controlling the plastic deformation of the metal to achieve the target bend angle and radius without cracking or buckling. This process is vital in shaping metal components for applications such as HVAC ductwork or auto body paneling.
Assembly
The final stage of basic metal fabrication is assembly, where individual components are joined to form a coherent product or sub-assembly. Assembly may involve approaches ranging from simple fastening using bolts or screws to advanced welding methods that fuse surfaces at a molecular level.
Complex metal fabrication combines metals and fundamental processes orchestrated with precision engineering, whether for custom designs or large-scale projects. Despite its inherent complexity and challenge, it continues to form an integral part of our engineered world — from the vehicles we drive to the buildings we inhabit.
Exploring Advanced Techniques in Complex Metal Fabrication
The world of metal fabrication is laced with intricate advanced techniques pivotal for efficient and precision engineering.
Laser-Cutting
Laser-cutting technology, for instance, has redefined the landscape of fabricating complex metal parts. This method employs a high-powered laser beam to cut precise shapes and designs on various types of metals.
This technology guarantees accuracy and consistency, especially for large-scale projects requiring duplicate parts.
High-Definition Plasma Cutting
High-definition plasma cutting is another advanced technique that allows fabricators to cut through thick metal sheets with incredible accuracy.
This technology relies on a plasma torch loaded with an inert gas blown at high speed out of a nozzle; simultaneously, an electrical arc is formed within that gas from the nozzle to the surface being cut, turning some of the gas into plasma.
Waterjet Cutting
Waterjet cutting adds another feather to the cap of complex metal fabrication technologies.
Waterjet cutting uses a high-pressure stream of water or water combined with an abrasive substance to cut through metal material. It's ideal for cutting heat-sensitive or delicate materials without causing distortion or damage.
The Art and Science of Welding in Complex Metal Fabrication
Welding forms the backbone of any complex metal fabrication process as it facilitates joining separate pieces into coherent custom designs.
MIG Welding
MIG welding, also known as Gas Metal Arc Welding (GMAW), is popular for its versatility and ease of use.
Particularly notable for its application in automotive repair and construction projects, MIG welding offers strength and durability even under harsh conditions.
TIG Welding
TIG welding (Tungsten Inert Gas) or Gas Tungsten Arc Welding (GTAW) stands apart because of its precision - it produces high-quality welds on thinner materials or delicate assembly jobs where precision is paramount.
SMAW
Shielded-Metal Arc Welding or Stick welding is a traditional method that, although less sophisticated than MIG and TIG, is highly effective in outdoor conditions and for heavy-duty materials.
Each welding technique requires appropriate safety measures and precautions during application to ensure operator safety.
CAD/CAM's Role in Complex Metal Fabrication
Computer-Aided Design (CAD) and Computer-Aided Manufacturing (CAM) have emerged as game changers in complex metal fabrication. These technologies enable precision engineering by creating detailed 3-dimensional designs that guide automated machining tools.
The advantages of CAD/CAM technology are manifold - from eliminating human error to improving production timings, these systems have revolutionized how fabricators approach project execution.
CAD/CAM technologies have dramatically improved efficiency and precision from automotive industries to aviation.
Quality Control and Testing Methods for Complex Metal Parts
Quality control is essential to the complex metal fabrication process, ensuring flawless manufactured parts.
Non-destructive testing methods like Ultrasonic Testing detect internal flaws or inconsistencies without damaging the part.
Magnetic Particle Testing is another non-destructive method to reveal surface cracks or subsurface discontinuities in ferromagnetic materials such as iron, nickel, cobalt, and certain alloys. Besides these non-destructive tests, destructive testing methods such as Tensile Strength and Bend Tests are employed under controlled environments to understand how materials behave under extreme conditions.
In Sum
With advanced techniques integrated into traditional processes and robust testing protocols ensuring high-quality outputs, the future looks promising for complex metal fabrication.
The industry continues its march towards greater efficiency through innovations like CAD/CAM, reshaping how large-scale projects are executed.
Combining art and science in welding techniques allows custom designs to be brought to life, ensuring that the future of complex metal fabrication is grounded in precision engineering.