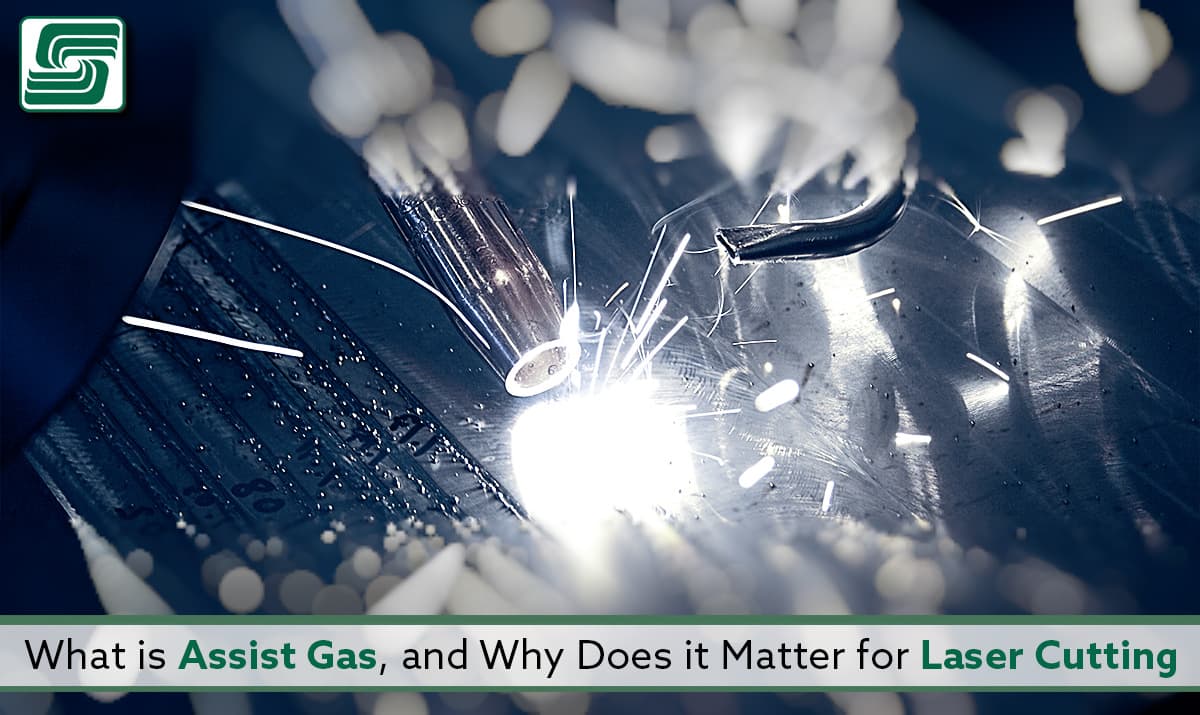
It's funny that with all the advancements in metal fabrication equipment, like the incorporation of Industry 4.0, the basics developed long ago are still critical to today's processes. Whether or not CNC or offline programming is involved, some things don't change.
For example, the use of various gases in welding and cutting. Today, we're talking about assist gas.
Laser Cutting
The laser cutting process combines optics, computer-aided design programs, and computer-controlled lasers to create detailed patterns in various materials. When laser cutting is part of a larger manufacturing process, such as digital fabrication or additive manufacturing, use an assist gas when cutting certain materials.
What is Assist Gas?
An assist gas is a secondary stream of an inert or non-reactive gas used in combination with the primary CO2 laser beam during laser cutting operations. When using standard air as the primary gas source for your laser cutter, you will see reduced rates of success and discoloration when performing laser cuts in certain types of materials.
Using an assist gas enables you to successfully cut these materials at high rates with limited negative effects.
Assist Gas During Laser Cutting
The primary source of gas used during laser cutting is the CO2 laser beam, which is the focused beam of intense light created by electrically igniting the carbon dioxide gas within the laser's chamber. When firing this laser beam, it creates a stream of extremely heated plasma that passes through the nozzle of the cutting head and into the workpiece.
The laser's heat is intense enough to melt and fuse together the materials being cut, but it is not hot enough to ignite any nearby materials found in the inert gas stream. As the CO2 laser beam passes through the inert gas, it absorbs some of the gas molecules, heating the gas and increasing its pressure and density. Directing the heated gas through the cutting nozzle comes into contact with the workpiece. It helps transfer the heat from the laser beam into the workpiece, making the materials molten and fuse together.
Assist Gases
The most common gases used to help transfer the heat from the laser beam into the workpiece are argon, carbon dioxide, and helium. These gases are all inert, meaning they do not react when coming into contact with the materials being cut and are also relatively inexpensive.
Mostly, CO2 laser cutters use argon, and CO2 laser cutters use carbon dioxide and helium in specific applications in rare cases when a higher level of CO2 is needed in the plasma stream. This creates a more efficient cutting process and reduces the risk of burning the workpiece.
The high level of CO2 also helps to keep laser system pressures low, which reduces the risk of maintenance and repairs.
CO2 Laser and Helium
While argon and carbon dioxide are the most common gases used for laser cutting, the use of helium as an assist gas has seen a rise in recent years.
When using CO2 for laser cutting, the laser beam heats the CO2 gas, creating a stream of hot, high-pressure CO2 that travels through the cutting nozzle and into the workpiece. When using a CO2 laser, the beam heats the CO2 gas to create a high-pressure stream of CO2, but the added pressure of the helium within the stream is not enough to cause cutting.
When mixing a helium jet with the CO2 jet, they combine the two gases into a single stream hot and dense enough to cut, directing the stream through the cutting nozzle and into the workpiece, helping to transfer heat and melt the materials. This is a very common laser-cutting gas combination because it is efficient and economical. The CO2 laser beam creates a high enough pressure to melt the materials without being too high, which enables efficient cutting that does not burn or discolor the cut materials.
Argon and CO
Welders often use argon in CO2 laser cutting applications, such as when cutting materials like acrylic, cast iron, and mild steel. They normally use CO for very brittle materials like metal and stone. Using argon or CO as an assist gas lets you cut these materials without burning or discoloring them.
Cutting these materials without an assist gas is possible, but it is more challenging and often results in poor cuts and discoloration. Using argon or CO as an assist gas helps control the plasma and helps protect the workpiece from being excessively heated while also enabling you to efficiently and cleanly cut a wide range of materials.
N2 and CH4
Nitrogen gas (N2) is a common assist gas that helps to reduce the amount of CO2 in the plasma stream, which reduces CO2-induced discoloration.
Using an N2 assist gas on materials like acrylic and wood will reduce the amount of discoloration on these materials. Carbon dioxide and methane (CH4) are often used together on materials such as copper, brass, and nickel silver.
These two gases can reduce CO2-induced discoloration and create a cleaner, more precise cut. These gases help increase the amount of power needed in the laser, but they also reduce the amount of plasma in the cutting stream, which helps to reduce the amount of discoloration.
Pure CO2
Laser welders configure a CO2 laser cutter to run with a pure CO2 assist gas or a CO2-O2 mixture.
Running the laser with a pure CO2 assist gas creates a laser cutting stream with high CO2 and low heat levels. This CO2 cutting stream is best for materials like metals and stones that are very brittle or have high thermal conductivity.
Running the laser with a CO2-O2 mixture creates a CO2 assist gas with a low CO2 and a high heat level. This CO2-O2 cutting stream is best for materials like wood and acrylics that are not very brittle.
Fumes and Exhaust Gas
Fumes are a type of gas that is created as a waste product of a chemical process, consisting of a solid, liquid, or gas; the amount of each depends on the creation process.
Fumes are often created during the chemical process of forming metals, used as an assist gas during laser cutting, and often used on materials like stainless steel and high-grade aluminum. Exhaust gas is a waste product of combustion, which is the rapid oxidation of a substance in the presence of sufficient oxygen created when an engine or turbine burns fuel, such as natural gas or gasoline, and then exhausts the waste product of this reaction out of the engine. Exhaust gas assists during laser cutting, and they often use it on stainless, mild, and nickel-based alloys.
What About Compressed Air?
The air density inside your laser cutter and the surrounding environment determine how much laser power is needed to cut materials. If your laser needs more power, you must operate the laser at a higher pressure, increasing the chance of leaks and causing the laser system to break down sooner than normal. If the laser cutter uses compressed air as the primary gas source, increasing the pressure within the laser cutter may be necessary to increase the power of the laser beam. If the laser operates at high pressures, you may lower the operating pressure by switching from compressed air to zero-grade air. Zero-grade air is a source of pure nitrogen, which has almost the same density as air. By switching from compressed air to zero-grade air, you can lower the pressure within the laser without changing the density of the air.
In Sum
As impressive as technological advances can be, they also expose vulnerabilities. Welding and cutting rely on several variations of gases to aid in cutting. Some gases, such as helium, are harder to come by, while others are a compromise until something better comes along.
Assist gas plays a critical role in laser cutting, and hopefully, this article shines some light on a piece of the manufacturing process that shouldn't be overlooked.