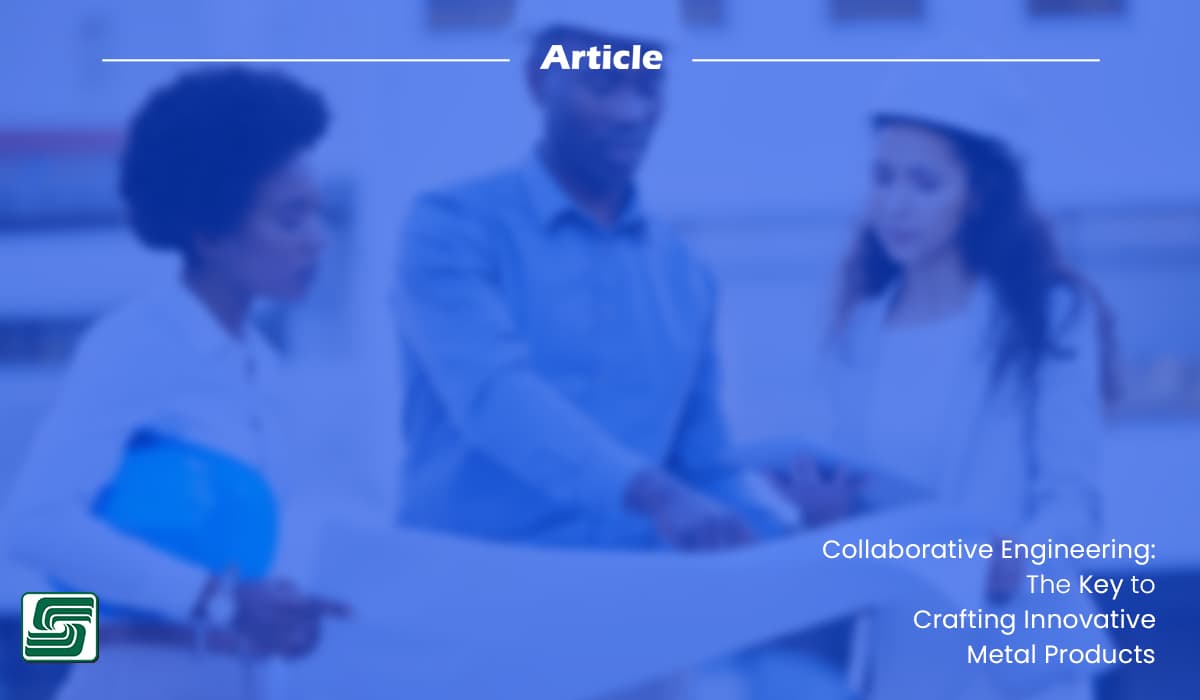
Collaborative engineering is a manufacturing method in which engineers and designers collaborate to create products. This approach combines the best features of traditional engineering and manufacturing, allowing each team member to collaborate on creating a single product from start to finish.
The Basics of Collaborative Engineering
In collaborative engineering, people work together using a combination of their skills and expertise. This involves sharing ideas, solving problems early, and working collectively towards a common goal. Their tools facilitate seamless collaboration, allowing them to share design data and simultaneously work on the same project.
Why It Matters in Making Things
Collaborative engineering is crucial in making better products by leveraging diverse team members' collective knowledge and experience. Combining different disciplines allows for new solutions that may not have been possible otherwise. This approach contributes to finishing projects faster by streamlining the decision-making process and reducing the risk of project failure.
Collaborative engineering helps reduce the risk of project failure and improves business continuity by ensuring all involved parties understand the project. It's an effective way to improve employee experience by ensuring everyone feels included.
The Role of Collaborative Engineering in Metal Fabricating Projects
Collaborative engineering plays a pivotal role in metal fabricating projects, offering a seamless approach to planning and executing tasks. By leveraging the collective expertise of engineers and designers, this method fosters an environment where innovative ideas are brought to life through effective collaboration.
Planning Together
In collaborative engineering, sharing ideas is at the core of the planning process. Teams brainstorm and exchange thoughts, generating diverse perspectives and contributing to comprehensive project plans. This approach ensures that all potential angles are considered, resulting in well-rounded solutions that cater to various requirements.
Solving problems early is a key advantage of collaborative engineering in metal fabrication. By identifying potential challenges early, teams proactively address them, minimizing the risk of delays or setbacks during the manufacturing process. Adopting a proactive problem-solving approach improves project efficiency and delivers high-quality products on time.
Making Things Together
Collaborative engineering facilitates a smooth transition from design to reality, from initial design concepts to bringing ideas into reality. This involves a cohesive effort from all team members who work collectively to transform designs into tangible products. Each individual's contribution is valuable in this process, ensuring every aspect is meticulously executed with precision and attention to detail.
Everyone has a part to play in collaborative engineering projects. Every team member's unique skill and expertise are harnessed to contribute meaningfully towards achieving project objectives. Working together promotes a sense of ownership among team members and guarantees effective utilization of each person's strengths in completing metal fabricating projects.
Building Big Structures
Enormous structures like bridges and buildings stand as testaments to the impact of collaborative engineering. Engineers and designers work together seamlessly to conceptualize, plan, and execute these monumental projects. The collaborative approach allows for a fusion of diverse expertise, resulting in structurally sound designs that meet safety standards while pushing architectural creativity's boundaries.
The insights from interviews with engineers and project managers shed light on the benefits and challenges associated with collaborative engineering. They emphasize that this method combines different disciplines to create a single product, reducing the risk of project failure, improving business continuity, and encouraging creativity and innovative thinking. However, it leads to lengthier decision-making processes and invites conflict and tension.
How Teams Worked Together
In building something, teams collaborate at every stage, from initial design discussions to the actual construction phase. Each member brings unique insights and skills, contributing to a holistic approach that addresses various structural requirements. This process ensures all aspects are thoroughly considered, leading to robust structures that stand the test of time.
Everyday Items Made Better
Collaborative engineering extends its influence beyond structures to everyday items such as bikes and cars. These common yet essential transportation modes have significantly improved through collaborative efforts.
Interviews with industry experts highlight how collaborative engineering has enhanced product development in everyday items like bikes and cars. By combining different disciplines early in the design phase, teams create products that cater to diverse user needs while incorporating innovative features for improved performance.
The Magic Behind the Scenes
The magic behind these everyday items lies in the seamless integration of ideas from various team members. Engineers collaborate with designers to ensure the form meets function while addressing safety standards and ergonomic considerations. This integrated approach results in products that meet consumer demands and exceed expectations through continuous innovation.
The Future of Collaborative Engineering in Metal Fabrication
As the metal fabrication industry continues to evolve, new tools and technologies are shaping the future of collaborative engineering. These advancements are revolutionizing the way metal fabricating projects are approached, offering unprecedented opportunities for innovation and efficiency.
New Tools and Tech
Integrating automation and robotics is redefining the landscape of metal fabrication. Automation equipment such as robotic total stations, multi-access cutting and milling machines, and CNC-driven devices allow for more precise:
- Measurements
- Fabrication Cuts
- Bend
- Installation Tolerances
Future advancements in robotics and automation are heavily pointing towards robotic folders, press breaks, and even robotic welding and finishing processes. Fiber lasers equipped with fully automated towers allow cutting, etching, perforating, sorting, and storing metal without human intervention.
Working from Far Away
Collaborative engineering is also embracing remote work capabilities through advanced technologies. Integrating IoT and Industry 4.0 technologies allows teams to collaborate seamlessly from different locations. This enhances flexibility and enables experts from diverse geographical areas to contribute their unique perspectives to metal fabricating projects.
The emergence of these advanced tools and tech is reshaping the collaborative engineering landscape in metal fabrication by:
- Enhancing Precision
- Streamlining Processes
- Cultivating a Connected Approach to Carrying Out Projects
Making Cooler Things
Adopting new technologies in collaborative engineering opens doors to creating complex geometries and shapes that were previously challenging or impossible to achieve. This paves the way for innovative designs that push the boundaries of traditional metal fabrication methods. These advancements, from intricate architectural structures to precision-engineered components, enable manufacturers to bring cooler things into reality.
Making the World Better
By harnessing the power of collaborative engineering alongside advanced tools and tech, manufacturers contribute to making the world a better place. Integrating advanced materials with innovative design approaches leads to products with improved properties, such as:
- Increased Strength
- Lightness
- Resistance to Corrosion
- Heat Resistance
These developments enhance operational efficiency while reducing environmental impact through sustainable manufacturing practices.
The future holds immense promise for collaborative engineering in metal fabrication as it continues to embrace technological advancements that drive efficiency, precision, and innovation while contributing positively towards a sustainable future.
In Sum
As technology advances and industries evolve, collaborative engineering remains at the forefront of driving innovation and efficiency in metal fabrication. Embracing a future where interdisciplinary collaboration thrives holds immense promise for creating groundbreaking products while contributing positively to a sustainable future.