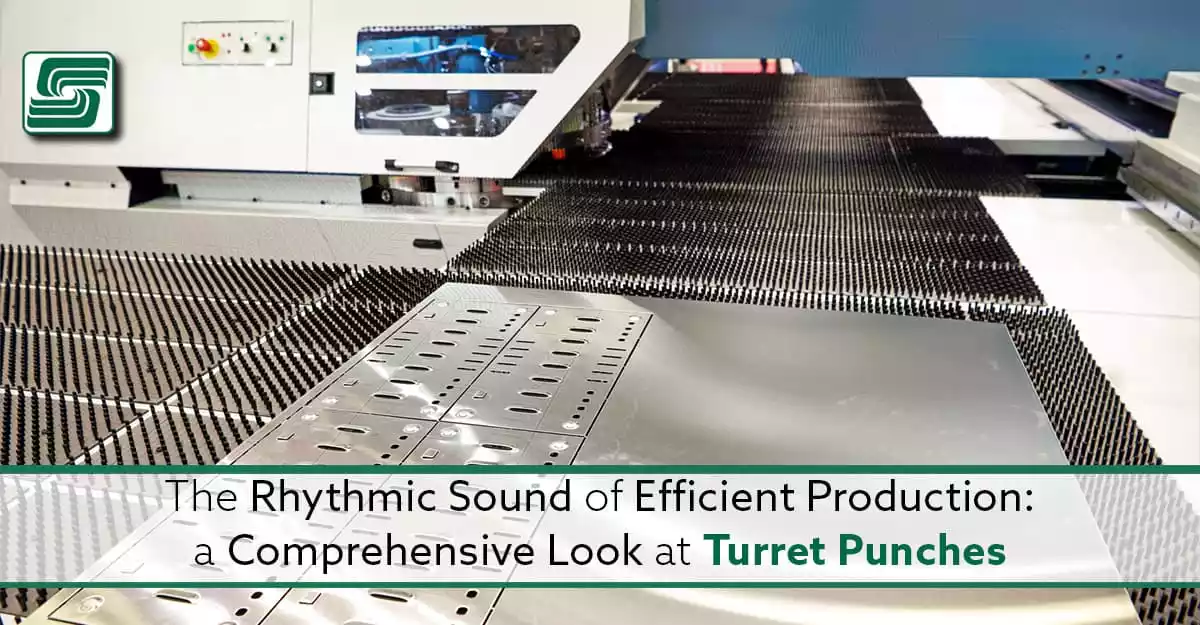
Industrial turret punches are versatile machines widely adopted in the manufacturing industry, and they can punch holes and shapes of different sizes and shapes in metal sheets of different thicknesses.
In this comprehensive overview, we'll take a deep dive into the technology behind industrial turret punches and explore how they help your business maximize its production efficiency.
Turret Punch History
The history of the turret punch dates back to the early 20th century, when various inventors and companies were exploring ways to automate sheet metal punching.
One of the earliest pioneers of the turret punch was a German engineer named Friedrich Bodmer, who filed a patent for a "revolving turret with multiple punches" in 1923. This design involved a rotating turret with several punching tools that could be quickly and easily changed to create different hole patterns.
However, it was the American company Strippit, founded in 1923, that is generally credited with developing the first commercially successful turret punch.
Strippit Turret Punch
Strippit's founder, Alfred Strippel introduced a range of innovations, including a hydraulic power source and a computer-controlled indexing system.
The first Strippit turret punch was introduced in the early 1950s, and the company continued to refine and improve its design over the next several decades.
By the 1970s, Strippit had become a leading manufacturer of turret punches, with its machines widely used in the automotive, aerospace, and electronics industries.
Other companies, including Amada and Finn-Power, also entered the market, introducing their versions of the turret punch.
Today, turret punches remain a vital tool in the metalworking industry, with modern machines offering advanced features such as CNC control and automatic tool changers.
How do Turret Punches Work?
Industrial turret punches use several tools, including punches and die, to punch holes and shapes in metal sheets. The machine holds several different tools in a turret, which rotates to select the right tool for the job.
The sheet is held in place by clamps and moved around to different positions as the punch works its way across the sheet.
A computer operates the machine, which controls the movement of the sheet and the selection of tools.
The punch tooling is the heart of the turret punch, consisting of a punch and a die to create a hole or shape in the sheet. The punch is a cylindrical tool inserted into the die, a flat piece of metal with a hole in it.
By forcing the punch through the sheet, it creates a hole or shapes the same size and shape as the punch.
Industrial turret punches can punch holes and shapes of different sizes and shapes in metal sheets. The size and shape of the hole or shape are determined by the size and shape of the punch and die, meaning one machine punches a wide range of holes and shapes, making it a versatile tool for any manufacturing operation.
Turret Punch Capabilities
Industrial turret punches poke holes and shapes of different sizes and shapes in metal sheets of different thicknesses—punching sheets of metal up to several millimeters thick and creating holes and shapes of different sizes and shapes.
The size and shape of the hole or shape are determined by the size and shape of the punch and die.
Industrial turret punches punch a wide range of holes and shapes, including round, square, rectangular, and oblong holes, and punch shapes, such as triangles, circles, and squares.
Turret Punch Main Components
The main components of a turret punch include:
- Punch Tooling: Consisting of a punch and die, they punch holes and shapes in the sheet.
- Turret: Holds the tools and rotates to select the proper tool for the job.
- Sheet Clamps: Holds the sheet in place during the punching operation.
- Sheet Movement System: Moves the sheet around to different positions while the punch works its way across the sheet.
- Control System: The computer and software that controls the movement of the sheet and the selection of tools.
Flywheel
A flywheel is a critical component of a punching press—it's a heavy, rotating disk that stores energy and helps regulate the movement of the punch.
When the punch is activated, the flywheel releases its stored energy, providing the force necessary to punch through the metal sheet.
The flywheel also helps regulate the punch's speed, ensuring it moves consistently.
The size and weight of the flywheel vary depending on the size and model of the punching press. Larger machines generally have larger flywheels, requiring more energy to deliver the necessary force.
The flywheel is an essential component of the punching press, and regular maintenance is necessary to ensure it continues to function correctly.
Turret Punch Accuracy
Industrial turret punches are incredibly accurate, with some models can punch holes with a tolerance of ±0.005 inches. This level of accuracy is necessary when working with complex designs or precision parts.
The accuracy of a turret punch depends on several factors, including the quality of the machine, the type of tool used, and the operator's skill.
Choosing a high-quality turret punch and using the right tools is essential to ensure the highest level of accuracy. Regular maintenance and calibration are also necessary to keep the machine functioning correctly.
Hydraulic and Mechanical Turret Punches
There are two main types of industrial turret punches: hydraulic and mechanical.
Hydraulic turret punches use a hydraulic system to power the punching operation. The hydraulic system uses oil under pressure to power the punch, which is forced through the sheet to create the hole or shape.
Hydraulic turret punches are typically faster and more powerful than mechanical ones, capable of punching thicker metal sheets and producing larger holes and shapes. However, they are also more expensive than mechanical turret punches.
Mechanical turret punches use a mechanical system to power the punching operation. The mechanical system uses a motor and a series of gears to power the punch.
Mechanical turret punches are typically smaller and less expensive than hydraulic ones, ideal for smaller manufacturing operations that don't require the power and speed of a hydraulic turret punch. They are also more reliable and require less maintenance than hydraulic turret punches.
Just How Many Tools are There on a Turret Punch?
One of the significant advantages of industrial turret punches is their ability to use multiple tools for different operations.
Turret punches can mount anywhere from 20 to 60 different tools, depending on the size and model of the machine. These tools perform several operations, including punching, notching, and forming.
The number of tools mounted on a turret punch gives businesses the flexibility to perform various operations without switching machines or tools, saving time and increasing production efficiency.
What software programs an industrial turret punch?
Computer numerical control (CNC) software operates industrial turret punches. The software programs the machine with instructions on punching the sheet into holes and shapes of different sizes and shapes in many patterns. The software also controls the movement of the sheet and the selection of tools.
The software used to program an industrial turret punch is typically proprietary and provided by the machine manufacturer.
The software creates programs specific to the manufacturing operation while optimizing the punching process, reducing waste, and increasing efficiency.
Turret Punches Pack a Serious Punch
Industrial turret punches deliver a significant amount of force, with some models capable of exerting up to 30 tons of pressure. This force is necessary to punch through thick metal sheets quickly and accurately.
The amount of force a turret punch can deliver depends on the size and model of the machine, and larger machines generally exert more force than smaller ones.
The force a turret punch delivers depends on the type of material punched. Softer materials like aluminum and copper require less force to punch than harder materials like stainless steel.
Materials the Turret Punch Work With
Industrial turret punches punch several materials, including steel, aluminum, copper, and brass.
The type of material punched influences the force required and the tool needed. Softer materials like aluminum and copper require less force to punch than harder materials like steel.
When working with different materials, it's essential to choose the proper tool for the job and ensure accurate machine calibration.
Different materials may also require different safety precautions, so following the protocols when working with each material is essential.
Other Tasks for the Turret Punch
Industrial turret punches perform several different operations besides punching. These include notching, forming, and even laser cutting.
Notching removes a piece of material from the edge of a sheet, creating a clean, precise edge. Forming involves bending or shaping the metal sheet to create different shapes.
Laser cutting uses a high-powered laser to cut through a metal sheet instead of punching holes. Laser cutting is useful when working with thicker materials or when a higher level of precision is required. The ability of industrial turret punches to perform multiple operations makes them a versatile tool for many manufacturing processes.
Turret Punch Advantages
Industrial turret punches offer several advantages over other ways of punching holes and shapes in metal sheets. They are fast and accurate, capable of punching holes and shapes quickly and precisely. They are also versatile, capable of punching a wide range of holes and shapes in metal sheets of different thicknesses.
Industrial turret punches are also cost-effective, punching a wide range of holes and shapes with the same machine, reducing the need for multiple machines and tools, which is expensive. They are also efficient because they can be programmed to optimize the punching process, reducing waste and increasing efficiency.
Turret Punch Disadvantages
Industrial turret punches are not without their disadvantages. They can be expensive, particularly hydraulic turret punches, and they are also large and require a significant amount of space in a manufacturing facility.
They also require significant maintenance, particularly the hydraulic systems in hydraulic turret punches.
Safety precautions When Operating a Turret Punch?
Operating an industrial turret punch is dangerous if people ignore proper safety precautions.
Some basic safety precautions include wearing appropriate personal protective equipment (PPE), such as safety glasses and gloves.
Operators should also receive proper training on using the machine and follow all safety protocols.
Other safety precautions include:
- Ensuring that the machine is properly maintained and calibrated.
- Using appropriate tools and materials for the job.
- Never bypassing or change any safety features on the machine.
Following all safety protocols to prevent accidents or injuries while operating an industrial turret punch is essential.
In Sum
Industrial turret punches are powerful machines that have revolutionized the metal fabrication industry. They can punch holes and shapes of different sizes and shapes in metal sheets of different thicknesses. They are fast, accurate, and versatile, making them an ideal tool for any manufacturing operation.