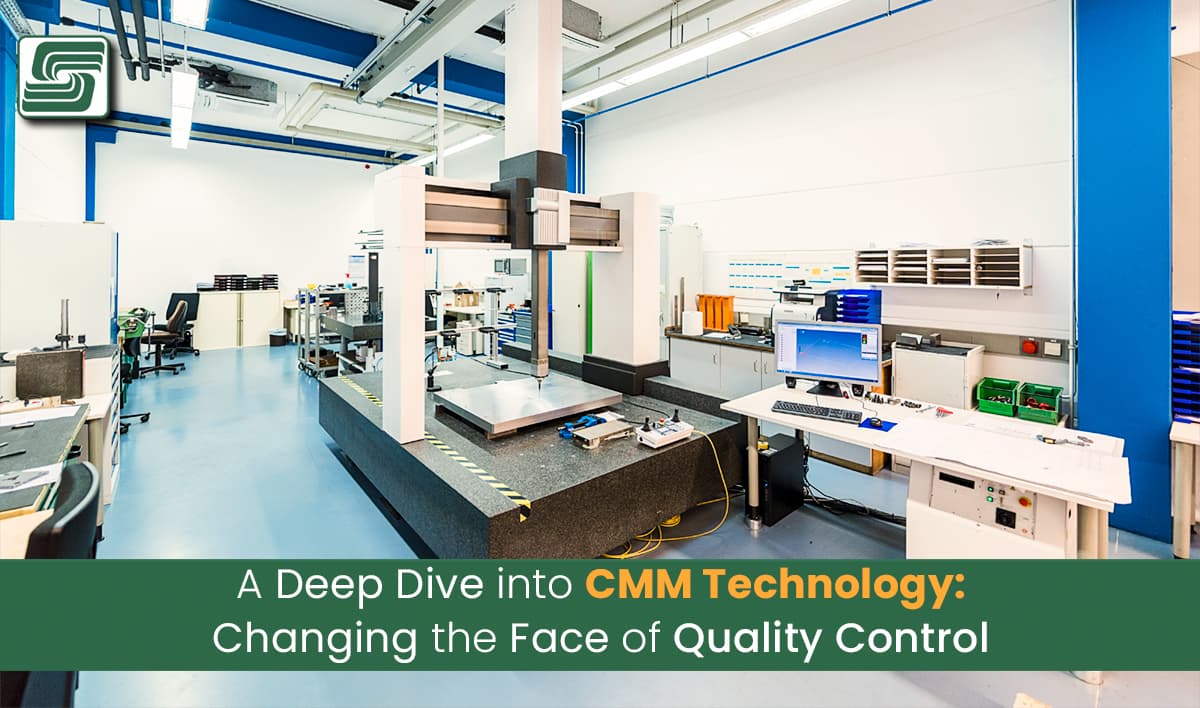
Coordinate measuring machines (CMMs) play a vital role in manufacturing today. But how did this technology develop over the years? When did it become crucial for quality control? This article explores the history of CMMs and how they transformed precision industries.
The Birth of CMM Technology
CMM technology first emerged in the late 1950s. Manufacturers recognized the need for accurate and repeatable measurements. Traditional inspection methods proved time-consuming, prone to human error, and lacked consistency. Engineers and scientists began searching for automated approaches to improve this process.
One pioneer was Dr. Carl Zeiss, a German physicist. He introduced the idea of a probe attached to a measuring head that could move along three axes. This breakthrough concept laid the foundations for early CMM prototypes.
The First CMM Machines
These first CMM machines were bulky, occupying entire laboratories because of their size. As computer technology advanced in the 1970s, CMMs benefited tremendously. Integrating computers enabled precise software control over machine movements and positioning. This development drastically improved accuracy and speed.
Rapid Evolution in the 1980s
As computing power expanded, so did CMM capabilities. Improved sensors, high-resolution encoders, and sophisticated algorithms made CMMs incredibly versatile. They could easily handle complex geometries and provide detailed measurements. The 1980s also saw the introduction of non-contact technologies like laser scanning. This expanded CMMs beyond tactile probing, enabling rapid surface digitization.
The Emergence of Portable CMMs
Recent decades have witnessed remarkable progress in portable CMMs. Miniaturization enabled lightweight, battery-powered devices with comparable accuracy to larger CMMs. Portable CMMs provided new flexibility, allowing use directly on factory floors or even on-site customer locations.
The aerospace, automotive, and medical device industries leveraged these portable CMMs to enable rapid, targeted inspections without moving parts unnecessarily.
Relentless Innovation
The pursuit of accuracy and precision continues driving CMM innovation today. Modern CMMs incorporate technologies like multi-sensor systems, advanced data analysis software, and integrated automation. This evolution transformed quality control, enabling manufacturers to achieve stringent standards and optimize processes.
Key CMM Features
CMMs include specialized features that make them invaluable for quality control. Here are some of the most important capabilities:
Precision 3D Measurements
CMMs capture 3D measurements, not just linear or angular data. This allows comprehensive inspection of the most complex geometries to ensure total accuracy.
Measurement Versatility
CMMs accommodate various probes, lasers, and sensors to measure size, form, texture, and more. This adaptability suits CMMs to diverse applications across many industries.
Powerful Metrology Software
CMMs include specialized software for sophisticated analysis, visualization, and reporting of measurement data. This enables identifying production trends and optimizing processes.
Automation
Modern CMMs feature programmable inspection routines and robotic integration for automated workflows. This boosts productivity and consistency.
Benefits of CMM Technology
CMMs provide manufacturers with several compelling benefits:
Enhanced Precision
Advanced sensors and probing systems enable CMMs to capture measurements with micron-level precision. This ensures conformance to specifications and quality standards.
Faster Inspection
Automated CMM inspection routines complete measurements significantly faster than manual approaches. Multi-point scanning also speeds up data collection.
Handling Complexity
CMMs measure intricate geometries and free-form surfaces without custom fixtures. This versatility suits the inspection of complex components.
Data-Driven Decisions
The detailed data from CMMs facilitates statistical process control and trend analysis. This supports data-driven decisions to optimize production.
By leveraging these advantages, manufacturers improve quality, efficiency, and productivity.
Limitations of CMM Technology
While CMMs deliver significant benefits, some limitations exist:
High Costs
CMMs carry substantial upfront investment costs. Regular calibration and maintenance also add expenses.
Space Requirements
Traditional CMMs occupy considerable floor space because of their large footprint. This presents facility layout challenges.
Lack of Mobility
Conventional CMMs remain fixed in place, requiring moving parts to their location for inspection. This adds time and material handling risks.
Programming Complexity
Creating effective CMM inspection programs requires specialized training and expertise. This demands additional resources.
Organizations must weigh these limitations against their specific needs when evaluating CMM technology.
Dispelling Myths About CMMs
Several common myths surround CMMs. But current facts and data dispel these misconceptions:
Myth: CMM inspections waste time.
Reality: CMMs provide objective precision impossible manually. Automation also improves productivity.
Myth: CMMs have steep learning curves.
Reality: Modern CMMs feature simplified user interfaces and control software.
Myth: CMM automation doesn’t suit small shops.
Reality: Compact CMMs are now cost-effective for small-batch manufacturing.
Progress Marches On
The coordination measuring machine will continue evolving. But already, this technology has revolutionized quality control and precision manufacturing. By automating complex measurements with absolute accuracy, CMMs enable leaner, more efficient processes. Their analytical capabilities provide invaluable process insights.
With ongoing progress expanding CMM accessibility and usability, manufacturers of all sizes stand to benefit from integrating this remarkable technology.
CMM Development Timeline
To fully appreciate the evolution of coordinate measuring machines, it helps to visualize key milestones in their development:
1950s
- Origin of the CMM concept, pioneered by Dr. Carl Zeiss
- Early CMM prototypes built as large machines requiring dedicated labs
1970s
- Integration of computers enables software control of CMMs
- Improved accuracy and speed compared to manual measurements
1980s
- Sensors, algorithms, and software boost the versatility of CMMs
- Non-contact laser scanning introduced for surface digitization
1990s
- Portable CMMs emerge, offering arm-based articulated designs
- Isostatic arms keep probe orientation fixed as arms move
2000s
- Multi-sensor technology combines tactile and optical measurements
- Scanning probe speeds increase to 250 measurements per second
2010s
- Photogrammetry techniques enable full 3D point clouds
- Automation improves through robotic integration and AI
The 2020s and Beyond
- Ongoing miniaturization and portability improvements
- Point cloud-based software and connectivity with smart factories
- Integration of metrology-grade additive manufacturing
This timeline illustrates the ongoing evolution of CMMs over six decades. Each advancement is built upon the last, continually expanding the capabilities of this versatile inspection technology.
CMMs in Action
To appreciate the impact of CMMs, it helps to look at real-world applications across manufacturing:
- Aerospace: Jet engine turbines and airframe components require ultra-precise measurements to guarantee safety and performance. CMMs handle these complex geometries. Portable CMMs allow inline inspections.
- Automotive: CMMs measure engine blocks, gearboxes, and assemblies to ensure fit and function—Multi-sensor CMMs scan sheet metal panels for designing dies and stamps.
- Medical Devices: Hip and knee implants rely on CMM inspection to verify precision surface geometries for proper fit and articulation. Dental drill guides and surgical instruments are also measured.
- Electronics: CMMs confirm the precision manufacturing of semiconductors and PCB assemblies. Portable arm CMMs even inspect large LCD panel assemblies directly on production lines.
These examples show the versatility of CMMs across essential manufacturing sectors. By leveraging their strengths, manufacturers ensure quality and optimize processes.
The Next Dimension
Coordinate measuring technology will continue evolving. Emerging trends point toward:
- Shop-floor CMMs with small footprints and easy mobility
- Increased adoption of non-contact scanning for speed
- More automated programming and guided workflows
- Advanced software analytics and machine learning integration
- Connectivity with smart factory ecosystems
While already delivering huge benefits today, CMMs will expand in capability and accessibility going forward. The future looks bright for this indispensable manufacturing technology.
Realizing the Potential of CMM Technology
While exploring how CMM technology improves operations, consider:
Assess Needs
- Identify current quality control pain points
- Review inspection bottlenecks and challenges
- Note needs for improved data collection/analysis
Evaluate Options
- Research different CMM types (bridge, arm, optical)
- Consider size, precision, and workload requirements
- Factor in costs, training, facility, and integration needs
Run Pilot Trials
- Arrange demos from CMM vendors using sample parts
- Test potential throughput and performance firsthand
- Clarify software learning curve and automation capabilities
Create Implementation Plan
- Determine optimal CMM model and specifications
- Plan space, installation, and integration requirements
- Budget for machine, software, and training costs
Leverage Capabilities
- Develop inspection routines for different product lines
- Use software analytics for process insights
- Continually refine programming and workflows
By following a thoughtful process, manufacturers can successfully adopt CMM technology and realize significant quality and efficiency gains.
The Future with CMMs
CMMs will continue playing an integral role in manufacturing quality and precision. Exciting developments on the horizon include:
- Completely portable CMM solutions using photogrammetry
- Machine learning to automate CMM programming with minimal training
- Wireless connectivity with factory networks and cloud-based analytics
- Integrated modules for closed-loop machining adjustments
- Further industry adoption of contactless optical scanning techniques
While already invaluable today, CMMs are poised for even greater capabilities in the future. Manufacturers who leverage this evolving technology will maintain a competitive edge.
In Sum
For over 60 years, the coordinate measuring machine has profoundly impacted manufacturing. CMMs enabled tighter quality control and process improvements across critical industries by automating complex dimensional inspection with exceptional accuracy.
Ongoing innovations continue expanding CMM versatility, precision, and accessibility. There is still tremendous untapped potential to leverage CMMs across an increasing range of applications. With competitive pressures rising globally, manufacturers must adopt the latest quality assurance technology aggressively. Coordinating measuring machines represents a strategic investment in the future.