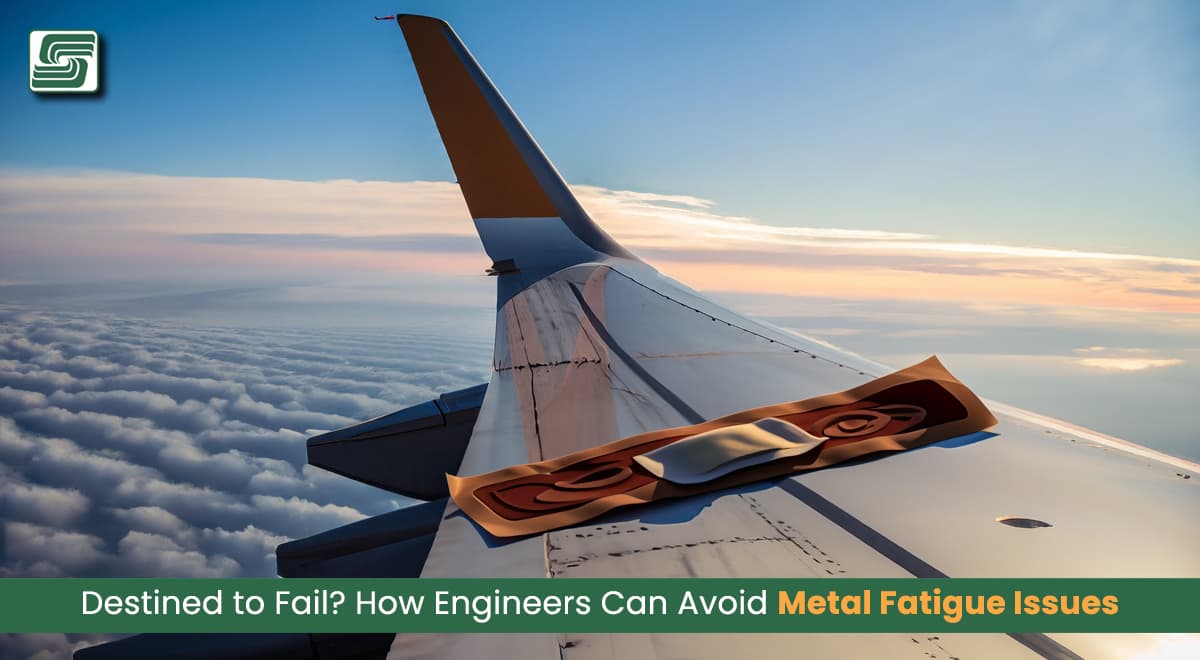
Metal fatigue happens when metal gets weaker and breaks from repeated stress. This occurs when metal parts experience on-and-off stress below their breaking point.
The repeated stress causes small damage in the metal that leads to cracks. The cracks grow until the part fails.
For example, imagine an aircraft wing going through many takeoffs, flights, and landings. The repetitive stress on the wing slowly damages it from the inside until even a moderate load makes it fail.
Why Metal Fatigue Matters
Many industries, like aerospace, cars, construction, energy, and ships, rely on strong metal parts. Understanding metal fatigue helps engineers design safe components after many load cycles.
This knowledge helps prevent fatigue failures in aircraft, bridges, power plants, and other critical structures.
We will be taking a look at the science behind metal fatigue. It explores how stress and strain affect metals at a microscopic level. This understanding forms the basis for the later sections.
We'll cover the two main forms of metal fatigue:
- Mechanical fatigue: failure after many cycles at lower stress
- Thermal fatigue: failure after fewer cycles, but a drastic temperature swings
The causes and contributions metal fatigue:
- Material factors like impurities and the environment
- Design factors like improper assembly
Techniques used to detect metal fatigue:
- Visual inspection of surfaces
- Non-destructive testing like X-rays and ultrasound
The Science of Metal Fatigue
To understand metal fatigue, we need to look at the science of stress, strain, and how metals deform.
Stress is the internal resistance in a material when a force is applied. Strain measures how much the material changes shape due to stress.
When metal stretches within its elastic limit, the deformation is elastic. This means it returns to its original shape after the stress is removed. The relationship between stress and strain here follows Hooke’s Law.
If stress exceeds the elastic limit, the metal undergoes permanent plastic deformation. This is because the atoms move out of place in the crystal structure. Dislocations allow the atomic planes to slide past each other when stressed.
The arrangement of atoms and impurities in the metal’s microstructure also affects its mechanical properties. Smaller grains improve fatigue resistance. Impurities enhance or reduce fatigue resistance depending on the alloy.
In cyclic loading, stress is repeatedly applied and removed. This leads to microscopic cracks in high-stress spots. Over many cycles, the cracks grow until the final failure. Factors like stress levels, frequency, temperature, and corrosion impact the fatigue life.
Grasping these concepts allows engineers to design metals resistant to repeated stresses, improving reliability.
Types of Metal Fatigue
Mechanical Fatigue Attacks Metals Through Repeated Stresses
Mechanical fatigue batters metals through repeated stresses like a boxer delivering blow after blow.
- Micro-cracks and defects silently emerge within the material's structure with each bending, stretching, and squeezing cycle.
- Machinery components and structural elements subjected to these cyclic loads often fall victim to mechanical fatigue's relentless assault.
- To withstand its punishing onslaught, they require careful engineering and design.
Thermal Fatigue Weakens Metals Through Extreme Temperature Shifts
Thermal fatigue also wages war against metals but with drastic swings in temperature as its weapon.
- Rapidly heating and cooling down, metals relentlessly expand and contract under thermal fatigue's extreme conditions.
- Exhaust systems, aerospace components, and other metals exposed to intense heating/cooling cycles are at risk for crack formation and failure from these thermal shocks. Like a tennis player sprinting and stopping repeatedly, the whiplash takes its toll.
- To protect against thermal fatigue's temperature barrage, materials selection, stress analysis, and design modifications must buttress metals' defenses.
Causes of Metal Fatigue
Material Factors
Impurities cluster at grain boundaries, creating weak spots for cracks to start. Fine-grained metals resist fatigue better than coarse grains.
High temperatures speed up metal weakening. Corrosion-like pitting creates stress concentration sites. Moisture absorption causes hydrogen embrittlement, resulting in micro-cracks.
Design Factors
Not accounting for cyclic loading in designs leads to poor long-term fatigue performance. Designers must accurately predict loading patterns and incorporate safety margins.
Misalignment and improper assembly induce localized and residual stress concentrations. Strict quality control during manufacturing and assembly is important.
Detecting Metal Fatigue
Visual inspection looks for surface cracks, pitting, and deformation. However, human error and limited visibility reduce effectiveness.
Non-destructive testing like X-rays and ultrasound reveals hidden internal flaws missed by visual inspection. Their data is crucial for defect severity assessment.
Using both initial visual checks and non-destructive testing gives comprehensive fatigue detection. This enables early identification of failures so preventive action can be taken.
In Sum
Understanding metal fatigue is crucial for aerospace, automotive, and energy engineers. Comprehending the science behind fatigue allows for designing components resistant to repetitive stresses.
Knowing what kind of fatigue helps identify issues before failure in parts, seeing cyclic loading. Addressing material-related and design-related factors minimizes risks. Detection methods like visual inspection and non-destructive testing reveal flaws that could lead to catastrophic failures if unnoticed.
Overall, a strong grasp of metal fatigue principles enables effective prevention strategies. This knowledge, combined with robust design, testing, and maintenance, ensures the safety and reliability of critical metal components subjected to fluctuating demands. With vigilance and care, industries tackle the formidable challenge of metal fatigue.