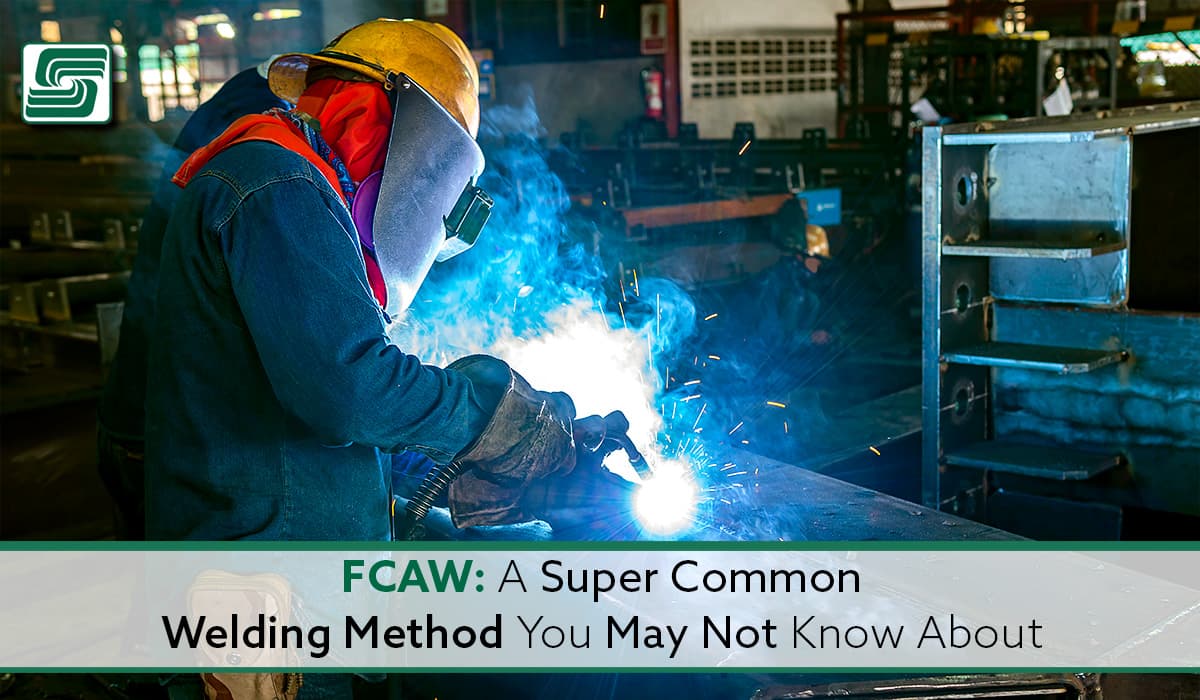
Welding is one of the most commonly used industrial practices in manufacturing. There are many welding, so it may seem strange that something so commonplace can still be under-recognized.
Welding is a process that joins two pieces of metal together by melting them at a very high temperature to become one piece. There are several welding processes, but today we'll be going over an advanced type called Flux-Core Arc Welding.
So what exactly is Arc Welding?
A Quick Welding 101
Arc welding is an electric welding process using a power source to create an electrical arc between a consumable electrode and the joined metal parts. The heat from the arc melts and combines the metals into one piece, and the consumables used in the welding process increase the process's efficiency.
Flux is an extremely common material made up of a mixture of iron, water, and other minerals common in nature. Adding flux to the electrode core protects it from the environment and increases its life and welding efficiency, which is why it's commonly used.
FCAW is also called manual metal arc welding, short circuit arc welding, or just arc welding when used in the construction or shipyard industries. It welds materials like zinc, copper, aluminum, lead, magnesium, silver, and steel.
Where did FCAW come from?
Arc welding is a very old welding method, and it's thought that ancient civilizations may have used it as early as 1700 B.C. However, the first documented use of arc welding was in 1775, when Benjamin Franklin combined iron pieces.
But the modern version of arc welding didn't come along until the mid-1900s. At the time, many welding processes were still fairly new, and engineers worked hard to figure out new and better ways to do things.
The first arc welding process was an electric arc between two electrodes, but there were many variations of the electric arc process.
In the 1950s, engineers developed a specific variation of electric arc welding called the short-circuit or manual metal arc welding process. This process was used to weld materials like zinc, copper, aluminum, lead, and magnesium.
Over time, the process was modified, including adding a flux core to protect the electrode. The process is now used for welding many materials, including steel, silver, and stainless steel.
Why Is FCAW So Common?
There are a few reasons FCAW is so common:
- It's a straightforward process to learn. Proficiency is possible after only a few hours of hands-on training, making it ideal for inexperienced welders.
- It's ideal for quick and easy repairs.
- It produces a high-quality weld.
Key Advantages of FCAW
- Very easy to learn. Since the FCAW process is so simple, it's easy to learn, making it ideal for beginners and people with little welding experience.
- Short time to produce. While the time to produce a weld varies depending on the type of materials being welded and the size of the weld, FCAW is generally a very quick process.
- Short setup time. This is similarly true of the time to produce welds. While there may be some variation depending on the size of the weld and the materials being welded, FCAW generally has a very short setup time.
- Excellent for making repairs. Since FCAW is so quick and easy, it's ideal for quick repairs, making it great for fixing broken parts in a pinch.
- Excellent for small welds. While FCAW isn't always the best option for larger welds, it's great for smaller welds, especially true when welding materials like aluminum, magnesium, and copper.
- Ideal for welding thin materials. While we can use FCAW for thicker materials, it's best for welding thinner materials.
- Excellent for welding porous materials. While we can use FCAW for many material types, it's especially good for welding porous materials together because the flux core protects the electrode.
Disadvantages of Flux Core Arc Welding
- Some materials can damage the electrode, especially if the materials are high in silica content, like limestone and sandstone. While the flux core protects the electrode from the materials being welded together, it damages the electrode if it's too porous.
- The welds may not be 100% solid. While the welds created through FCAW are generally very solid and have little risk of falling apart, there is a risk that the welds won't be 100%.
- The welds may contain slag. While this is true for most welding processes, it's especially true with FCAW by pulling the electrode through the weld so quickly it doesn't have time to cool completely. Thus, the weld may contain some slag.
- The electrode may have to be replaced frequently; see above.
In Sum
FCAW is a common welding process used to weld various materials. It's a simple learning process and quickly performed, making it an ideal choice for quick repairs, producing very high-quality welds used for many different applications. However, it has its disadvantages. While the flux core protects the electrode during the welding process, it can damage the electrode if the materials are too porous. In addition, the welds created through flux core arc welding may not be 100% solid, and the welds may contain slag.