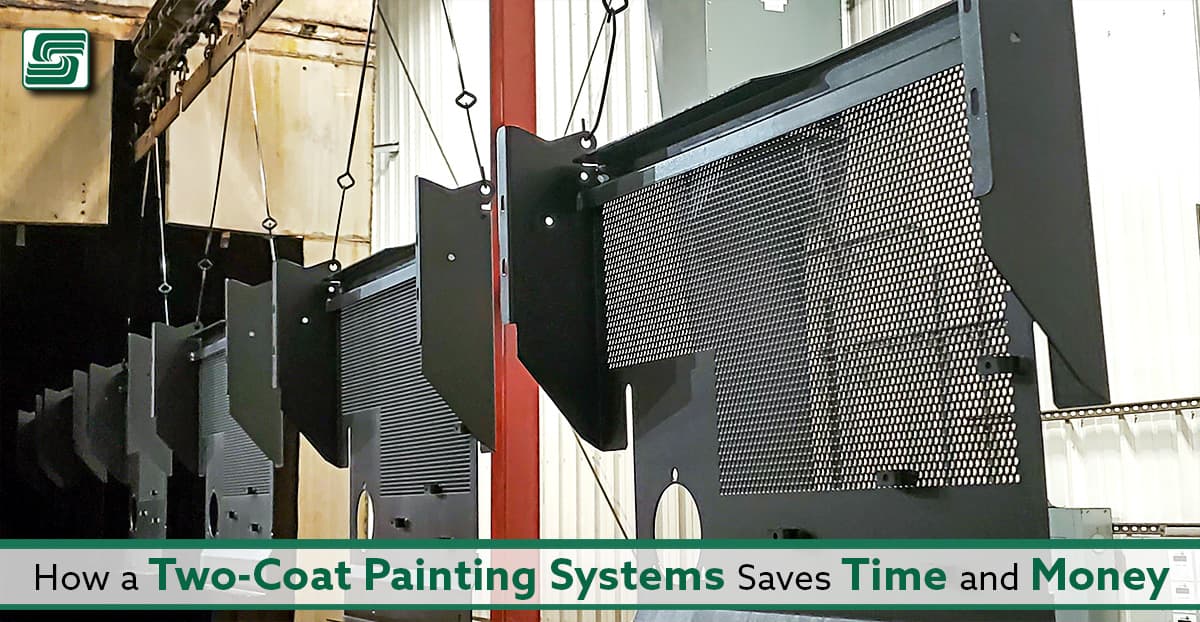
It's freezing and raining out, and your kids want to go outside to play. Would you let them go out there without coats?
I wouldn't either.
Consider this situation: it's the same weather, but instead of your kids, it's an expensive piece of fabricated metal. That metal spends a great deal of time outside. How long before it starts corroding?
Both situations need layer protection. It's a simple solution for your kids, make them wear their coat. What's the answer for the fabricated part?
Note: This article is the first of a series exploring the e-coating process.
Part 1: Two-Coat Systems Using E-Coating
Part 2: Is a Third Coat Necessary?
Part 3: Testing Topcoat Strength
The Two-Coat Finishing Process
What is a two-coat system? The simple definition of a two-coat system is a method of applying two coatings to the same component. The two-coat completely covers the material's surface improving corrosion resistance.
Although there are many ways of applying finish to a component, only one provides the best material coverage: e-coatings.
What is E-Coating?
Electrophoretic deposition (e-coating/electric coating) is like electroplating. The electroplating process uses electric current reducing dissolved metal cations, forming a thin, coherent metal coating.
E-coating occurs while dipping the parts in a bath of epoxy, water-based solutions, or paint while adding an electric current.
The current causes a reaction within the bath, depositing floating particles on the component. The amount of time using the electric current determines the coating thickness. After coating the part, it's moved to a curing oven to finish the process.
There are many similarities between powder coating and e-coating. Both methods use electric current to bond coatings to a substrate. E coatings are usually better options than powder coating because the submersion coats hard-to-reach areas of the part.
Controlling the thickness of the coating becomes easier to manage when e-coating, too. This process applies a consistent and repeatable coating over most finishing methods.
2 Common E-Coating Processes
Two of the most common e-coating processes are anionic and cationic.
The anionic process applies a positive charge on the component, while the fluid in the bath is negatively charged. Anionic methods are standard in the general metal industry, need color control, have easy operation, and are cheaper.
If using a component in a non-corrosive environment, the odds are the anionic process coated the part.
The cationic process provides a surface more resistant to corrosion and reverses the anionic process. The component is negatively charged, while the fluid is positively charged. The chemistry involved in the cationic process is based on acrylics or epoxies. If corrosion protection is critical, use epoxy chemistries. If applications need color control or durability, then acrylic systems are typically used.
E-Coating Evolution
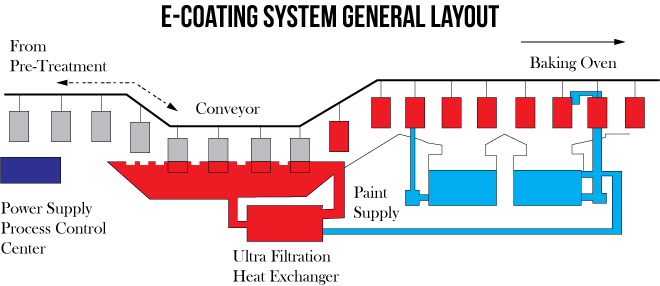
With a history dating back to the 1930s, e-coating provided a coating inside steel food containers. Around 30 years later, many industrial applications started using the e-coating system.
Ford Motor Company was at the forefront of e-coating technology. In the early 1960s, Ford scientists created an anodic process for e-coating an assembled auto giving anti-corrosion protection. A few years later, domestic appliances and architectural aluminum successfully used the e-coating system.
In the mid-1970s, Ford advanced e-coat technology by replacing anodic with cathodic processes where a continual DC circuit in the bath applies the e-coatings.
Since then, recent advancements in e-coating technology led to improved edge protection, low-voltage organic compounds, and more protection from UV light. E-coating is now used when making electrical components and heavy equipment needing corrosion protection.
Typical E-Coat Process
There are four main parts to the e-coating process including:
- Cleaning and pre-treating the component: a phosphate is applied to the surface of the component, preparing the piece for e-coating
- Immersing the component into a bath containing direct current and applying the coating to the part's surface
- A complete rinse
- Baking the part for at least 20 minutes while the component is around 375 ºF
E-Coating Advantages
The debate between powder coating versus e-coating is an entirely different article. Instead of highlighting that discussion, we're only exploring the advantages of using the e-coat system.
Some of the significant advantages of using e-coating include:
- A greater coverage when a component is e-coated. Total immersion covers all the hard-to-reach places.
- More thickness control using varying levels of DC.
- A reduction of rework, paint usage, and VOC emission
Salt Spray Testing
I was one of those parents who believed touching a hot lightbulb is one of life’s best lessons. I warned my kids often to stay away, but being curious kids, they kept pushing the envelope, learning as much as possible.
They ignored my fantastic advice, and several ice cubes melted against an injured, tiny finger.
Here’s where I’m going with this. You reading all the advantages e-coating provides results in forgetting about them in a short amount of time. We explore the different testing methods for the strength of a topcoat in another article.
Pictures, as they say, are worth a thousand words. Because visiting us isn’t convenient for you, here’s a photo of an e-coated sample before and after 500 hours of a salt spray test.
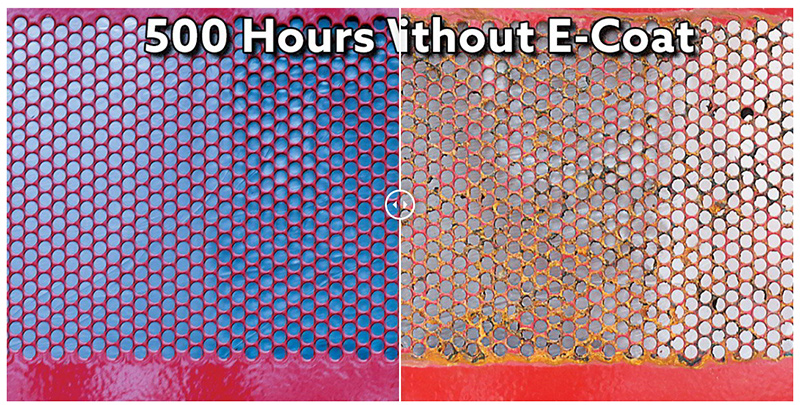
Check out our E-Coat Top Coat page. This page provides before and after sliding scales for 500, 1,000, and 1,500 hours of salt spray testing.
Reading about e-coating's effectiveness is one thing; seeing it is another.
In Sum
The two-coat finishing process is excellent for reducing both corrosion and surface imperfections. It's cost-effective, easy to maintain, and one of the best ways to protect your investment.
E-coating offers a wide range of protection. Electrolytic and anodic processes help reduce corrosion, while cationic and organic processes can protect against UV light and impact. The best part about e-coating is that you can change the coating in the future to provide more protection or durability.
If corrosion protection is the primary need, use a preferred process, such as a cationic or anodic process. This finishing process coating is always looking for more applications in the manufacturing industry. If you're interested in more information about e-coating, contact us using our contact form.