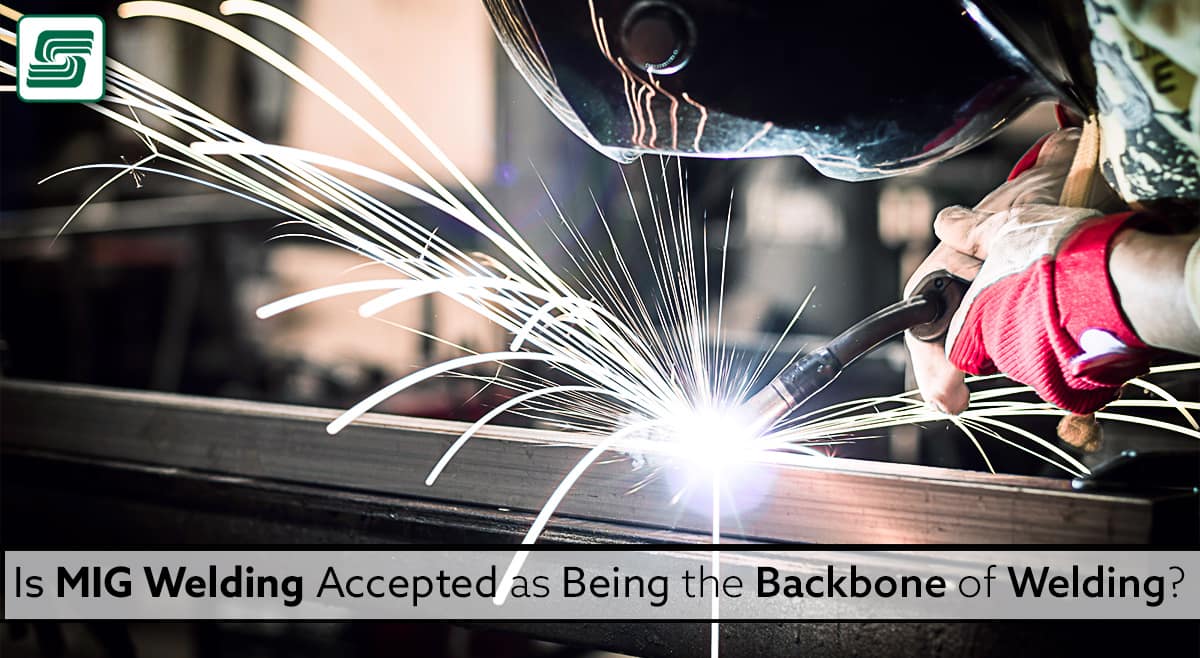
One of today's most versatile welding methods is Gas Metal Arc Welding (GMAW). GMAW, arguably, maybe the most important welding method in manufacturing. Its development improved welding speed, quality, and production. In fact, it accounts for more than 50% of all weld metal deposited.
Gas Metal Arc Welding
Gas Metal Arc Welding (GMAW), commonly referred to as MIG Welding, is a welding method where an electric arc is created between a base metal and wire electrode-heating the metal. The creation of the arc causes each to melt and eventually join.
MIG Welding Development
We commonly know MAW as MIG (Metal Inert Gas) welding, and it is less commonly known as MAG (Metal Active Gas) welding. In either case, the GMAW process lends itself to welding a wide range of both solid carbon steel and tubular metal-cored electrodes. The alloy material range for GMAW includes carbon steel, stainless steel, aluminum, magnesium, copper, nickel, silicon bronze, and tubular metal-cored surfacing alloys. The GMAW process lends itself to semiautomatic, robotic automation, and hard automation welding applications. GMAW's Story.
As we've previously discussed, Sir Davy's discovery of the electric arc was the impetus for future welding advancements.
When MIG welding was invented, the Battelle Memorial Institute created the modern incarnation of GMAW, an early version of MIG welding, in 1948. However, it was initially only used for welding aluminum.
This early version of MIG welding used smaller diameter electrodes than those used today, using constant voltage resulting in a high deposition rate. As important as this development was, the high cost of inert gasses prevented the wide use of MIG welding. Cost savings didn't exist because non-ferrous materials were the only game in town for MIG welding. It wasn't until 1953 that MIG welding became economical by developing carbon dioxide as a welding atmosphere.
In the late 1950s, welding's versatility increased because of the development of the short-arc variation of GMAW. Welding thin materials became possible by using smaller electrode wires and an advanced power supply. Soon after, the short arc became the most popular GMAW variation.
What is a MIG Welder?
MIG/MAG welding is a welding process in which a wire is continuously and mechanically fed during welding. The basic MIG welding techniques include the contact sleeve sending the wire directly to the workpiece by the contact sleeve, forming an electric arc between this wire and the workpiece. The welding wire serves as an electrode while melting and serving as filler material.
Adding a shielding gas protects the weld pool from the influence of oxygen and ensures an oxide-free connection of the workpieces. The active gas, unlike inert gas, also reacts with the weld pool. The disadvantage of this is that it affects the quality of the weld. We often use this because an active gas (MAG) is cheaper than an inert gas (MIG).
In contrast to TIG welding, where manually supplied welding consumables close to the electrode, in MIG/MAG welding, the welding wire is both consumable and electrode. Quickly adding the filler material also improves the welding speed.
There are four ways in which the material transfers from the wire to the weld pool takes place:
Short-Circuit: used for thin sheet metal or welding under challenging positions. By creating a fine droplet, the smooth material transfer allows little spattering.
Spray: used for thicker sheet metal. It can achieve high deposition and high welding speeds with an argon mixture. The material transfer is short-circuit-free, fine-droplet, and almost splash-free.
Pulse: suitable for all plate thicknesses as long as welders use an argon-rich gas mixture. Welders apply another impulse current over the primary current. The material transfer's droplet size is adjustable in intensity, resulting in a fine, evenly distributed droplet and spatter-free material transfer.
Globular: Like a short-circuit, it occurs when the wire arcs, creating a glob hanging off the wire. The glob falls to the metal, filling the joint. The globular transfer method creates a violent arc and large amounts of spatter.
MIG Welding Advantages
MIG welding is one of the most used welding techniques because of its versatility and quick production. Welders achieve a high temperature and high deposition with MIG welding. Besides, it is possible to mechanize the process or even have it carried out entirely by robotic welders. This welding process takes place in all welding positions.
Other advantages of MIG welding include:
Increased Productivity: Not needing to continually change rods, brush the welds, or deal with slag increases welding speed, leading to increased productivity.
Learning Curve: Learning the MIG welding process takes a few hours because of its simplicity.
Great Welds: MIG welding allows the welder to see the weld pool better. This increased visibility allows for better-looking welds.
Cleanliness: Shielding gases protect s the arc, eliminating slag and reducing splatter.
Versatility: Its able to weld a variety of metals and alloys. MIG welding is also possible in various methods, such as manually, semi, and fully automatic.
Speed: Using the continually fed wire increases welding speed, control, and quality.
This welding process is often used to produce vehicles, military tanks, pipes, or machine construction. MIG welding is also indispensable in the shipbuilding and offshore industry.
Because the process is suitable for robotization, high welding speeds become possible while welding in difficult welding positions. The welds are firm with little deformation, meaning finishing operations are unnecessary.
MIG Welding Disadvantages
Metal welding with active gases is sensitive to wind and can only occur in closed rooms. For wind and weather influences, the shielding gas can blow away, producing oxidation at the weld seam and porosity. A weld seam damaged by oxidation is of inferior quality, sensitive to rust formation, and not sufficiently robust.
Other disadvantages of MIG welding include:
No Outdoors: Location is also essential for MIG welding; it is unsuitable for the outdoors. The wind disrupts the shielding gas flow, negatively affecting the weld.
Thickness: MIG works great for thin metal but not so for thick. Any thick steel requiring a solid weld has to be performed by a different welding method.
Expensive: Cost is another mitigating factor of MIG welding. The equipment is more expensive and complicated. Replacing electrodes, shielding gas, and nozzles and tips are not cheap, either.
Cooling: Since the completed welded metal is not covered by slag, the metal cools much faster than average.
Gas: Replacing bottles of shielding gas takes time, plus the canisters tend to get in the way in the work area.
Prep: Any corrosion or dirt needs to be removed before welding
In Sum
When weighing the pros and cons of MIG welding, one thing to me stands out: efficiency. Welding with MIG simplifies the process, making it easy for people to learn how to do it. Its streamlined approach increases productivity while retaining quality welds.