A common site in most manufacturing facilities and home workshops is the arc associated with welding.
Although ubiquitous in the modern world, the welding process has evolved over thousands of years. Until a couple of hundred years ago, forge welding was the only way of connecting different pieces of metal.
What is forge welding and its story? Continue reading.
Forging Metal
Forge welding requires heat. How mankind developed fire has two origins.
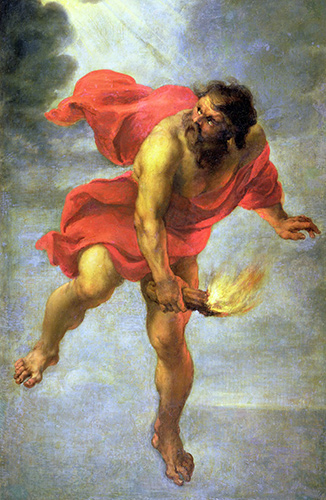
Prometheus
After being tricked by Prometheus, the Greek god, Zeus, punished man by taking fire away from us. Fortunately for us, Prometheus, called the benefactor of man, wasn't going to let mankind suffer for his trickery. He traveled to the gods' workshops and from Hephaestus, took a fennel stalk containing fire.
Prometheus returned to earth and showed mankind how to make and use fire. With this knowledge, mankind would never again be without fire. For this, and previous acts against him, Zeus chained him and sent an eagle to eat Prometheus's liver. Unfortunately for him, the liver re-grew each night; and the eagle returned each day, to eat the new organ.
Nature
The pantheon of Greek gods and their mythology makes for compelling reading. The most likely source of the fire was nature in the forms of lightning strikes and volcanoes. People used myths to explain why fire became such a powerfully destructive force.
Fire became mankind's tool for cooking, heat, and protection. Eventually, fire became the impetus for other purposes.
Early Metalwork
There are two aspects of forge welding: fire and metal. We've already talked about fire, now it's metal's turn!
Bronze Age
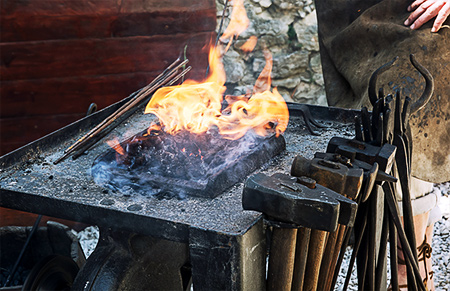
The Bronze Age began between 3300 to 2100 BC. The earliest bronze artifact created by hot forging was found in the Iranian Plateau between 5000 to 4001 BC. Archeologists determined the oldest tin alloy bronze-work occurred around 4500 BC in Serbia.
In other words, bronze has been around for a long time.
Interesting facts regarding bronze:
- Bronze was the first alloy used by humans.
- Today, bronze makes nearly all professional cymbals, giving them a desirable balance of durability and timbre.
Iron Age
The Iron Age began around 1300 to 1200 BC. Iron grew in popularity as it became less expensive to work with than bronze.
Meteorites were likely the first iron source, although it's hard tracing iron's history because quickly iron rusts. Among the earliest known meteorite artifacts were found in Egyptian graves containing iron beads around 7000 years ago.
The evolution from the Bronze Age to the Iron Age resulted from the metalworker's ability to make improvements on the iron itself, such as making carbon steel. It's thought carbon steel was an accidental discovery around 1000 BC by accidently combining molten iron and charcoal from the smelting fire. Another famous example of an accidental discovery was champagne.
Two interesting facts regarding iron:
- The earth contains enough iron to make three planets with the same mass as Mars
- It's the first magnetic metal discovered.
The Metal Forge
The generic term forging defines all the ways of using heat and pressure for the metalwork process. Metal forming is among the oldest working techniques used for creating weapons, ships, and farming tools.
What is forge welding?
Basically, it's where heat is generated, usually using coal or gas as the heat source, and then the metals are joined using pressure (hammering) to bind the metals together. Forging is also known as blacksmithing…
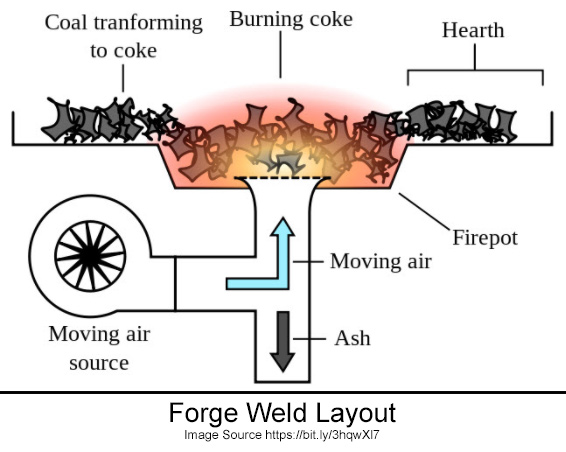
The primary tool used in forging metal is forge, which has four primary components:
- Hearth: location of generated heat
- Blower: oxygen source for increasing heat
- Tuyere: path the oxygen follows accessing the fire source
- Water Basin: for cooling the metal
Forges are either stationary or portable.
The Forging Process
Regardless if a forge is portable or stationary, there are two forge categories:
- Updraft: fumes and smoke produced during the forging process pushed through an overhead hood unit
- Downdraft: fumes and smoke produced during the forging process pushed through down through a series of ducts.
Of the two, the downdraft version provides better ventilation and air circulation.
The forging process is straightforward. Using a forge, an air blast adjusts the fire's heat to the raw metal to the correct temperature forging it into various shapes. The illustration above provides a basic overview.
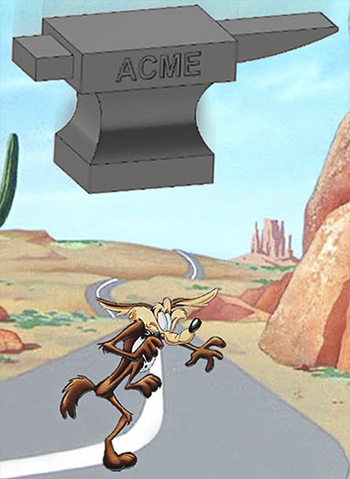
Anvil
An anvil is a primary tool used for forge welding. Originally, anvils were stones or flat rocks. Eventually, the materials comprising an anvil included bronze, iron, and steel.
Although an anathema to Wile. E. Coyote, especially the ACME brand, they're a vital tool for metalworkers and necessary for proper forge welds.
As the need for tools and implements changed over the years, so did the anvil's shape. Its shape worked through many incarnations until the 1800s when the London Pattern became common. In fact, the London Pattern is the primary shape used today.
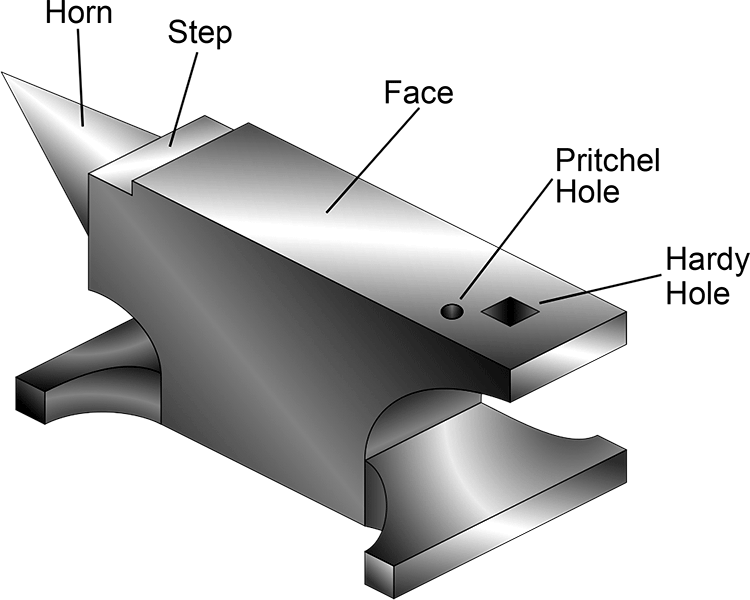
There are five essential components of anvils:
- Horn
- Step
- Face
- Hardy Hole
- Pritchel Hole
Horn
The horn is the curved piece at the front of the anvil. The blacksmith uses the horn for hammering different curves into the metal piece they're forging. Some anvils have more than one horn, varying in shape and size.
Step
The step is next to the horn and below the anvil's face, generally used to cut the metal. Cutting involves the smith setting the hot metal on the step while hammering it until it cuts. The more blacksmiths uses it, the quicker the step wears out.
Face
The business side of the anvil takes place on the face, which receives the hammer blows. The edges around the face are curved to prevent accidental cutting. The face connects the step and horn.
Hardy Hole
The square-shaped hole through the anvil is called the hardy hole. If needed, tools are attached to the anvil using this hole. The spot is also used for bending and punching holes into the metal.
Pritchel Hole
The pritchel hole functions the same as the hardy hole except it's rounded, not square.
Times are a' Changin
Forge welding was the only method of welding for thousands of years. In the 1800s, however, times, technology, and practices changed. As previously mentioned, the advent of acetylene welding represented a sea-change for manufacturing. Industrial welders were no longer welded to one spot; compressed gas containers' portability allowed them freedom for doing the work away from their shop.
In Sum
Forge welding was the only welding game in town for several millennia. As modern welding methods slowly standard, forge welding drifted to the background, existing now primarily as a blacksmith's craft. The best example of specialization in forge welding is History Channel's Forged in Fire TV series.
Prometheus's sacrifice gave mankind the gift of warmth, hot food, and the ability to improve quality of life. Although consigned to predominately hobbyists, the sound of hammering on anvils won't fade away anytime soon.