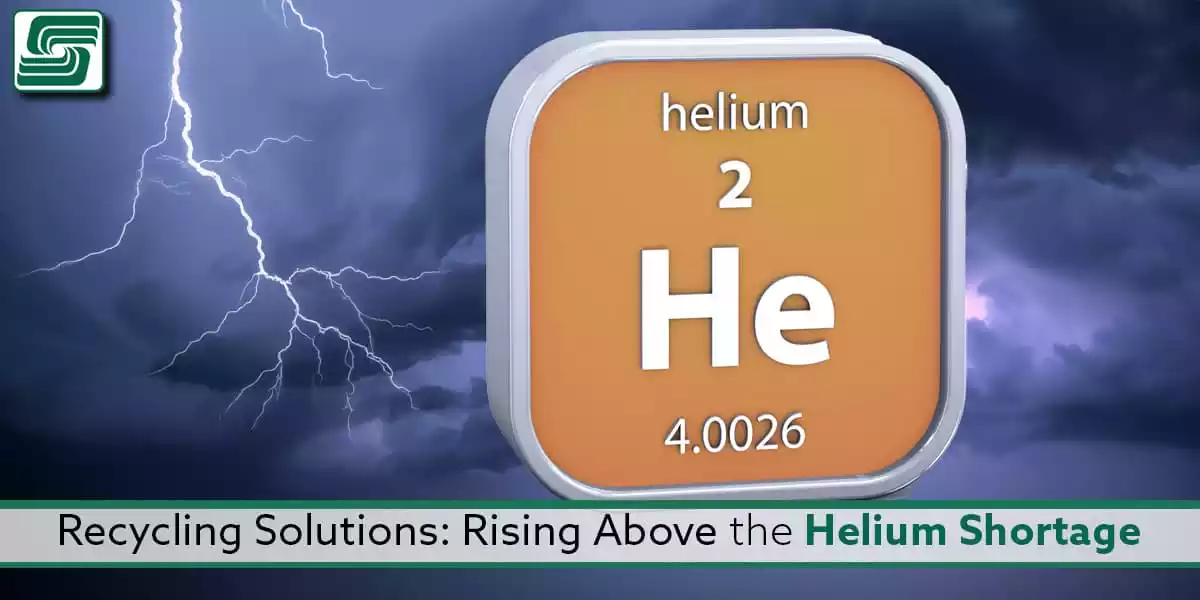
The Helium Shortage Crisis: Causes and Effects
Helium, a gas widely used in various industries, is experiencing a shortage crisis. This gas has critical applications in healthcare, aerospace, and electronics. The reason for the helium shortage crisis is twofold - it is both a natural resource with limited availability and a byproduct of natural gas extraction.
The depletion of helium resources has been an ongoing issue with increasing demand from emerging markets. As a result, the supply chain for helium has been disrupted, leading to shortages in various countries worldwide.
Additionally, the cost of extracting helium is high, which makes it difficult to produce enough to meet demand. The impact of this shortage can be felt across numerous industries.
Healthcare providers depend on helium for Magnetic Resonance Imaging (MRI) machines to diagnose conditions like cancer or brain injuries. The aerospace industry uses it for space missions and surveillance activities, while electronic manufacturers use it in LCD screen production.
Importance of Helium in Various Industries
Helium is essential in many industries due to its unique properties, such as being non-reactive, inert, and low-density. In healthcare, MRI machines require cryogenic cooling, which can only be achieved using liquid helium, highlighting its importance. In aerospace, helium provides critical lift capacity that enables balloons and blimps to maintain their altitude during flights while also being used as fuel in rocket engines due to its high energy content.
In electronics manufacturing processes where LCD screens are produced, precise control over temperature is necessary for proper functioning. Liquid helium offers stable temperatures making it ideal for meeting these requirements.
Recycling Innovations that can Help
Recycling innovations provide hope for resolving the current helium shortage crisis. The three most commonly used recycling methods are cryogenic distillation, adsorption, and membrane separation. Cryogenic distillation is a process that uses low temperatures to separate and purify gases from a mixture.
It offers high purity levels but requires large amounts of energy to operate. Adsorption is another method using materials like activated charcoal or zeolites to capture and release gases with different properties when subjected to specific conditions.
This method is cost-effective but has a lower purity level than cryogenic distillation. Membrane separation uses membranes with varying permeability characteristics that allow for the separation of gases based on their size and solubility in polymers.
It is commonly used in smaller-scale applications due to its relatively lower efficiency. The helium shortage crisis poses significant challenges across numerous industries globally.
The importance of helium in various industries cannot be overstated, making it crucial to find solutions for this issue. Recycling innovations such as cryogenic distillation, adsorption, and membrane separation are offering hope for resolving this crisis by providing an avenue for sustainable helium supply chains.
The Helium Shortage Crisis: Causes and Effects
Causes of the Helium Shortage Crisis
Helium is a non-renewable resource, so that a limited amount can be extracted from natural gas fields. The main cause of the current helium shortage crisis is the under-investment in new helium extraction projects, particularly over the last decade, which has an imbalance in demand and supply, leading to a global scarcity of this vital element.
Another contributing factor to the shortage is that many countries have been stockpiling helium for use over the years, further reducing global supply. Furthermore, production facilities are often located in politically unstable regions, further increasing supply uncertainties.
Effects on Various Industries
The helium shortage crisis's effects are felt across several industries that rely heavily on this noble gas. In healthcare, liquid helium is used to cool Magnetic Resonance Imaging (MRI) machines.
Without sufficient quantities of this gas - which keeps MRI machines at very low temperatures - hospitals are forced to reduce their patient intake or shut down some MRI units altogether. In aerospace engineering and defense industries - where high-performance balloons and airships are critical for reconnaissance missions – there has been a significant reduction in helium supply, limiting design possibilities due to lower lift capabilities.
Likewise, in manufacturing sectors such as electronics production, where helium plays an important role as a coolant during semiconductor fabrication processes - reduced or absent supplies can negatively impact overall productivity due to increased equipment temperatures leading to issues with accuracy and consistency during production runs. Overall, suppose solutions aren’t found soon for replacing traditional methods. In that case, these industries will continue to face challenges caused by Helium shortages impacting research & development efforts while stifling economic growth worldwide.
Recycling Innovations: An Overview
Recycling
Recycling is a vital component in resolving the helium shortage crisis. The scarcity of helium is a growing concern worldwide, and recycling can help alleviate this problem.
The demand for helium surpasses the supply rate, leading to increased prices and limited usage in industries that rely on it. Recycling innovations provide a solution by enabling us to reuse and recover this valuable gas.
Recycling Methods
There are several methods for recycling helium, including cryogenic distillation, adsorption, and membrane separation. Cryogenic distillation is one of the most popular methods for large-scale helium recovery due to its high efficiency and effectiveness.
Adsorption uses materials like activated carbon or molecular sieves to collect and recover helium from gas streams. Membrane separation separates gases based on their molecular size through a semi-permeable membrane.
Cryogenic Distillation: Advantages and Disadvantages
Cryogenic distillation has several advantages over other recycling methods. It has high efficiency, with recovery rates reaching up to 99% in some cases.
It also consumes less energy than other methods like adsorption or membrane separation. Cryogenic distillation is also widely used in industries requiring large-scale helium extraction.
However, cryogenic distillation also has some disadvantages. It requires high capital investment costs due to complex equipment requirements like compressors, heat exchangers, storage tanks, etc., which makes it less practical for small-scale operations or individual users who need low volumes of helium.
Adsorption: Advantages and Disadvantages
Adsorption is another method that can be used to recover helium from gas streams effectively. One of the main advantages of this method over cryogenic distillation is that it can be used for small-scale recovery operations.
Adsorption also has a lower capital investment cost than cryogenic distillation, making it more practical for individual users or small-scale recovery operations. However, adsorption also has some disadvantages.
The recovery efficiency of this method is lower than cryogenic distillation, and the process requires frequent maintenance due to the high risk of contamination and fouling. Moreover, adsorbent materials need frequent replacement to maintain efficiency and effectiveness.
Membrane Separation: Advantages and Disadvantages
Membrane separation is another method that can be used for recovering helium from gas streams. This method has some advantages over other methods, like low capital investment costs, ease of maintenance, and flexibility in design since it can be scaled up or down depending on the required gas volumes.
However, membrane separation also has some disadvantages, and it has lower helium recovery rates than other methods like cryogenic distillation or adsorption.
The membranes used in this process have a limited lifespan and require regular replacement to maintain efficiency. Recycling innovations provide an opportunity to recycle and recover helium gas effectively.
Several methods are available for recovering helium from gas streams, such as cryogenic distillation, adsorption, and membrane separation, each with advantages and disadvantages. The choice of recycling method depends on factors such as the scale of operation required or the demand for recovered helium gas by different industries.
Cryogenic Distillation: A Detailed Look
How Cryogenic Distillation Works
Cryogenic distillation is a recycling method that separates helium from other gases based on their boiling points. This process involves cooling the gas mixture to extremely low temperatures, causing the helium to liquefy and separate from the other gases. The liquefied helium is then collected and refined for reuse.
The cryogenic distillation process typically involves several steps. The first step is pre-cooling, in which the gas mixture is cooled using a heat exchanger and then passed through a series of compressors and expansion valves to achieve ultra-low temperatures.
Next, the gas mixture enters a distillation column, separating it into different components based on their boiling points. Helium has the lowest boiling point among all gases, so it tends to rise to the top of the column and can be easily collected.
Advantages and Disadvantages Compared to Other Recycling Methods
Cryogenic distillation offers several advantages over other recycling methods for helium recovery. Firstly, this method provides high-purity helium with minimal impurities compared to other recycling methods.
Secondly, cryogenic distillation allows for large-scale helium production suitable for industrial applications. However, this method also has some disadvantages that must be considered when deciding which recycling method to use.
One major disadvantage is that it requires significant energy input due to its reliance on cooling processes. Additionally, this method has higher capital costs than alternative methods such as adsorption or membrane separation.
Case Studies on Successful Implementation in Different Industries
Several industries have successfully implemented cryogenic distillation to recover helium from gas mixtures. In healthcare applications such as magnetic resonance imaging (MRI), cryogenic distillation provides a reliable source of high-purity helium for cooling MRI equipment.
In aerospace applications like rocket propulsion and space exploration, cryogenic distillation has also been utilized for helium recovery. Cryogenic distillation is commonly used to produce liquid hydrogen fuel for spacecraft, where helium is produced as a byproduct.
Cryogenic distillation offers an efficient way to recover helium from gas mixtures, making it suitable for many industries requiring high-purity helium. While energy demands and high capital costs must be considered before implementing this method, its proven success in various industries makes it a viable option for resolving the ongoing helium shortage crisis.
Adsorption: A Detailed Look
How Adsorption Works
Adsorption is a process that involves the adhesion of gas or liquid molecules to a solid surface. In helium recovery, adsorption involves passing the helium-containing gas through a bed of adsorbent material, such as activated carbon or molecular sieves. The helium molecules selectively adhere to the surface of the adsorbent material, while other gases pass through and are not captured.
Once all the helium has been adsorbed, the adsorbent bed is heated to release the captured helium for collection and purification. One advantage of this method is its ability to achieve high purity levels in recovered helium.
Adsorbents can be tailored to selectively capture specific gases, allowing for efficient separation from other components in a gas mixture. Additionally, since it operates at near-ambient temperatures and pressures, it requires less energy than cryogenic distillation.
Absorption Advantages and Disadvantages
Compared to cryogenic distillation and membrane separation methods, adsorption has several advantages. Adsorption allows for the efficient separation of individual gases in complex mixtures and can achieve high recoveries with high-purity output streams.
It also requires less energy than cryogenic distillation because it operates at near-ambient temperatures. However, there are also some disadvantages associated with this method.
The main disadvantage is that over time the efficiency of the adsorbent material decreases due to saturation by impurities or chemical reactivity with gases in contaminated streams, leading to lower recovery rates or more frequent replacement of spent material. Another disadvantage is that it performs poorly on off-specification feed streams (volatile organic compounds), which tend to break down under elevated temperatures over time, leading eventually complete failure where no more Helium is recovered from these feedstreams.
Successful Implementations
One success story in adsorption-based helium recovery is Oak Ridge National Laboratory's (ORNL) development of a compact helium recovery system for use in gas chromatography. The system uses a proprietary adsorbent material to selectively capture helium from the carrier gas stream and achieve high purity levels. The technology has been further developed for other applications, including recycling from MRI Helium Vent streams.
Another example is Air Products and Chemicals, Inc., which has developed an adsorption-based helium recovery system that captures 99.999% pure helium from natural gas streams. The system also includes a regeneration process that allows for continued operation without replacement of the adsorbent material and can recover about 80% of the Helium present.
Adsorption is one of several promising recycling innovations for resolving the global helium shortage crisis. While it has limitations, it offers advantages over other methods in certain applications. It has been successfully implemented in various industries, such as natural gas processing plants and petrochemical and scientific research facilities. With ongoing research and development efforts, we can expect improvements in efficiency and cost-effectiveness to help address this critical resource challenge today and into the future.
Membrane Separation: A Detailed Look
How Membrane Separation Works
Membrane separation is a process that uses a semi-permeable membrane to separate and collect helium from gas mixtures. This membrane has tiny pores that allow only small molecules, such as helium, to pass through. In contrast, larger molecules, such as nitrogen and oxygen, are separated and collected in a different chamber.
The separation process is based on the principle of pressure-driven diffusion, where gas molecules move from areas of high concentration to low concentration. The most common type of membrane used for helium separation is polymeric membranes made from materials such as cellulose acetate or polyamide.
These membranes have high selectivity for helium, allowing for efficient separation even at low pressures. Membrane separation technology has been successfully implemented in various industries, such as aerospace, healthcare, and electronics.
Membrane Separation Advantages and Disadvantages
One of the main advantages of membrane separation is its simplicity compared to other recycling methods like cryogenic distillation or adsorption. It operates at room temperature and requires less energy input than cryogenic distillation.
Furthermore, polymeric membranes are durable and can be used for extended periods without significant performance degradation. However, one limitation of membrane separation technology is its limited scalability due to the size limit of commercially available membranes, making it suitable only for niche applications with relatively small helium requirements. Additionally, polymeric membranes can be susceptible to fouling by impurities in the gas mixture.
The Future of Membrane Separation Technology
Despite its limitations, research in membrane technology continues to advance rapidly, with new materials being developed with even higher selectivity towards helium. One promising development uses nanoporous carbon membranes that exhibit excellent performance while being more resilient to impurities than polymeric ones.
The future looks bright for membrane separation technology, with companies like NuMat Technologies and Air Products investing heavily in research and development. In the long term, it could become a more prevalent recycling method in industries like healthcare and semiconductor manufacturing, where helium is essential.
In Sum
Helium is essential for industries such as aerospace, healthcare, and electronics. The current helium shortage crisis has highlighted the need for more efficient recycling methods to ensure a sustainable supply. Cryogenic distillation, adsorption, and membrane separation are three promising technologies that can help resolve the crisis by recovering usable helium from gas mixtures.
While each of these technologies has advantages and limitations, there is a bright future ahead with advancements in materials science enabling even greater selectivity towards helium. Membrane separation technology offers simplicity and ease of use compared to other methods, making it ideal for specific applications, but scalability remains a challenge.
Overall, we can remain optimistic about the future of helium recycling with breakthroughs in technology continuously being made that promise to make our production processes cleaner and more efficient. As innovation continues to drive progress within the industry, we can look forward to resolving the helium shortage crisis through new methods like membrane separation technology.