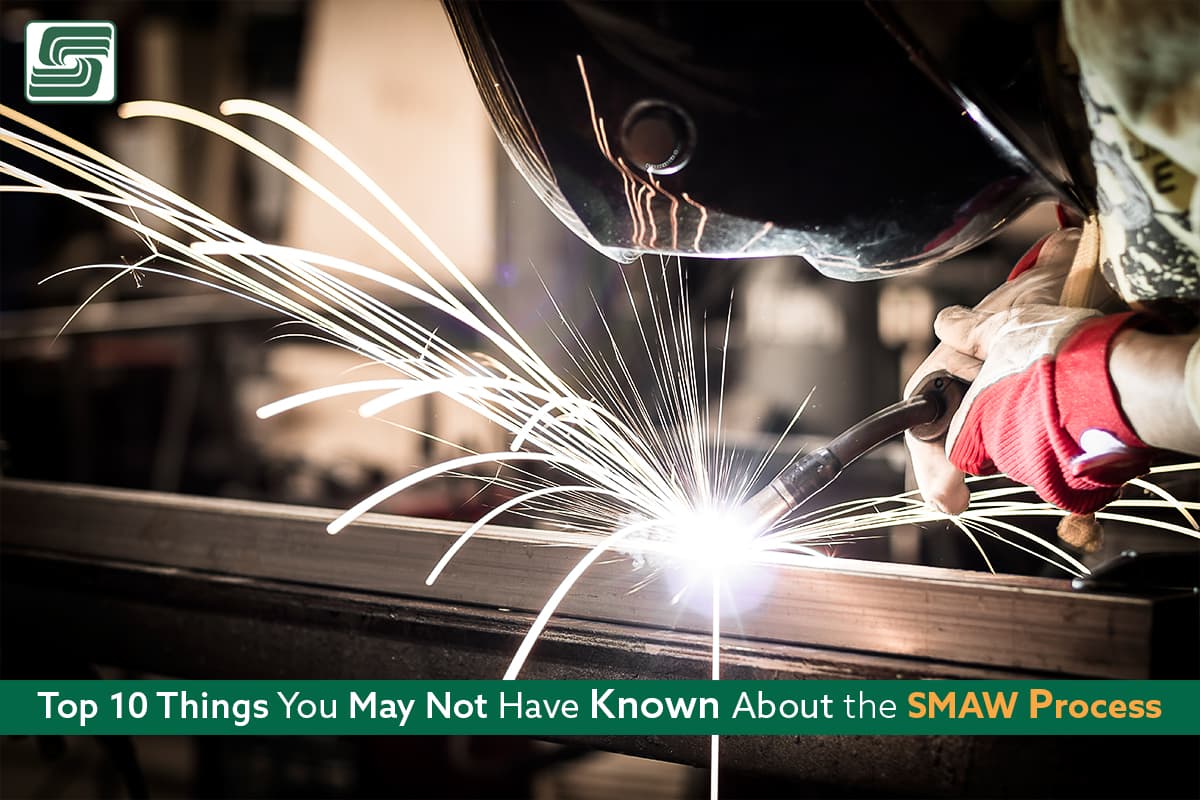
Shielded Metal Arc Welding (SMAW), often called stick welding, is a widely used welding process that uses an electrode with a flux coating to create an electric arc between the electrode and the workpiece. This arc generates the heat necessary to melt the electrode and the base metal, forming a molten pool.
The weld pool solidifies, creating a strong and durable bond between the materials. SMAW is renowned for its simplicity, versatility, and reliability.
It has been a cornerstone of the welding industry for over a century. Despite advancements in other welding techniques, SMAW continues to hold its ground because of its ability to weld in various positions and work under challenging conditions like high winds and adverse weather.
SMAW's Role in the Welding Industry.
SMAW is crucial in multiple industries where strength, reliability, and durability are paramount. From construction projects that require sturdy steel structures to fabrication operations that demand robust joints on heavy machinery, SMAW is consistently relied upon by skilled welders worldwide.
One key reason behind SMAW's continued prevalence lies in its adaptability across different metals. Whether carbon steel or stainless steel, cast iron or aluminum alloys — SMAW offers exceptional versatility for securely joining disparate materials.
SMAW is often preferred for repair and maintenance tasks because of its convenience. With minimal equipment requirements and portability advantages compared to other welding processes, SMAW is executed successfully even in remote locations or tight spaces with limited access.
Origins and Development of SMAW
SMAW has a rich history from the late 19th century. The process was first developed to join metals for industrial purposes.
It was initially used in shipbuilding and construction industries, where its versatility made it highly valuable. The simplicity and effectiveness of SMAW quickly gained popularity, leading to its widespread adoption in various sectors.
The concept behind SMAW is relatively straightforward: an electric current is passed through a consumable electrode coated with flux. The heat generated by the electric arc melts the electrode and forms a weld pool that fuses the base metals upon solidification.
This process creates a strong and durable bond. Over time, advancements in technology improved the efficiency and performance of SMAW.
Innovations in electrode compositions, coatings, and welding equipment allowed for better control over the welding process. These developments increased productivity, high-quality welds, and greater ease of use for welders.
Pioneers and Contributors
Several notable individuals have significantly shaped the SMAW process into what it is today. One of the early pioneers was Charles L. Coffin, who patented an arc welding method using metal electrodes coated with flux in 1890. His work laid the foundation for future advancements in this field.
In 1904, Oscar Kjellberg introduced coated electrodes containing iron powder that improved weld quality by reducing porosity and increasing deposition rates. Kjellberg's contributions revolutionized SMAW by enhancing its versatility across different applications.
Another prominent figure in SMAW's development was James F. Lincoln, who founded The Lincoln Electric Company in 1895. Lincoln played a pivotal role in popularizing SMAW by advancing the technology, developing new electrode compositions, and providing comprehensive training programs for welders.
The American Welding Society (AWS) has helped standardize and promote SMAW. Through their research, publications, and certification programs, they have disseminated knowledge and best practices to ensure SMAW's safe and effective application in industries worldwide.
SMAW Equipment
SMAW uses a specific set of equipment to perform the welding process. The primary components include a power source, electrode holder (a stinger or torch), and welding cables. The power source is essential in SMAW, providing the electrical energy required to create an arc between the electrode and the workpiece.
Typically, welders use a transformer-based or inverter-based machine as their power source. Transformer-based machines are robust and reliable but are larger and heavier.
In contrast, inverter-based machines are more compact and portable, offering improved control over the welding process. The electrode holder holds and guides the consumable electrode during welding.
It includes an insulated handle that protects against electric shock and a clamp that securely holds the electrode. The holder enables welders to precisely manipulate the electrode's position, ensuring accurate placement of molten metal onto the workpiece.
SMAW requires appropriate welding cables to connect the power source to the electrode holder. These cables act as conductors for electric current during welding operations.
They are typically made from copper because of its excellent conductivity properties. It is crucial to use cables with sufficient thickness (gauge) based on the amperage used during welding to reduce voltage drop and maintain consistent performance.
Welding Circuit and Components
Understanding how the electrical circuit functions in SMAW is fundamental for achieving successful welds. The basic components of a typical SMAW circuit include:
- A power source.
- Workpiece (or base metal).
- Grounding clamp.
- Electrode holder with consumable electrodes.
- An air gap between electrodes/workpiece.
When starting an arc, electricity flows from one terminal of the power source through a set path toward completing a circuit by returning through the grounding clamp. The power source supplies direct current (DC) for SMAW, with either direct current electrode positive (DCEP) or direct current electrode negative (DCEN) configurations, depending on the electrode type and welding requirements.
The current flows from the power source through the welding cables into the electrode holder, where it encounters the consumable electrode. As welding begins, an arc is established when the electrode tip is near the workpiece surface.
This arc creates extremely high temperatures that cause the end of the electrode and the workpiece to melt, creating a pool of molten metal. The molten metal then solidifies to form a weld bead as it cools.
Simultaneously, a protective shield is generated by vaporizing flux within the electrode coating. This shield prevents atmospheric contamination of molten metal and weld pool during solidification.
The resulting weld bond is strong and durable. Understanding this welding circuit and its components is crucial for proper technique execution in SMAW.
It ensures optimal control over variables such as arc length, amperage selection, travel speed, and heat input—all essential factors contributing to high-quality welds. By understanding these principles underlying SMAW's equipment and wiring circuitry, welders learn how to manipulate variables effectively during welding operations using this versatile process.
Advantages of SMAW
Versatility in Various Welding Positions and Environments
Shielded Metal Arc Welding offers a remarkable advantage in its versatility across several welding positions and environments. Unlike other welding processes limited to specific positions, SMAW can be effectively used in horizontal, vertical, overhead, and flat positions.
This versatility allows welders to easily perform their tasks, regardless of the orientation or angle required for the job. Besides its flexibility in various positions, SMAW excels in diverse environmental conditions.
Whether indoors or outdoors, on land or underwater, this welding process adapts to different atmospheres without compromising the quality of the weld. An electrode coating helps protect the molten metal from impurities and atmospheric gases during welding.
As a result, SMAW remains reliable even when faced with adverse conditions, such as wind, rain, or high humidity. SMAW's versatility extends beyond standard welding scenarios.
It is commonly used for repair and maintenance tasks because of its ability to weld on dirty surfaces and rusty materials. This advantage makes it particularly valuable for field repairs, where surfaces may not be perfectly clean or prepared beforehand.
Welding Versatility
Another significant advantage of SMAW is its ability to weld assorted metals effectively. Whether you're dealing with carbon steel, stainless steel, cast iron, nickel alloys, or other exotic metals like titanium or copper, SMAW is a reliable choice—the secret lies within electrode selection.
Different electrodes are specifically designed for different base metals and applications. For instance:
- Low hydrogen electrodes: Ideal for welding low-alloy steels where high-quality welds are required.
- Cellulose-coated electrodes: Perfect for welding mild steel and providing deep penetration.
- Stainless steel electrodes: Designed for joining or repairing stainless steel materials. By handpicking the electrode, SMAW enables welders to achieve strong, durable, high-quality welds on a wide range of metals.
This versatility makes SMAW a go-to choice in various industries, such as construction, manufacturing, fabrication, shipbuilding, and more. The advantages of SMAW are vast.
Its ability to adapt to different welding positions and environments allows welders to easily work, regardless of orientation or atmospheric conditions. Its versatility in handling various types of metals makes it a valuable tool for diverse applications.
SMAW's flexibility and compatibility across different scenarios remain essential in the welding industry.
Limitations of SMAW
Lower deposition rates compared to other welding processes
Shielded Metal Arc Welding offers many advantages, but one of its limitations is the relatively lower deposition rates compared to other welding processes. Deposition rate refers to the amount of weld metal deposited per unit of time. The slower rate in SMAW is primarily because of the manual nature of the process, which requires the welder to continuously pause and replace electrodes as they are consumed during welding.
These breaks in welding result in intermittent arcs and frequent stops, reducing overall productivity. Experienced welders often employ techniques such as optimizing travel speed, angle, and arc length to mitigate this limitation.
By fine-tuning these variables, it is possible to increase the deposition rate while maintaining appropriate quality standards. Selecting electrodes with higher amperage ranges helps elevate SMAW deposition rates.
Difficulty With Thin Materials
While SMAW easily joins thick materials, it presents challenges when welding thin materials. Thin metals have a low thermal mass and are prone to distortion or burn-through if not handled carefully during welding. SMAW's intense heat causes excessive melting or warping on thin materials.
So, a skilled welder must exercise precise control over parameters, such as current intensity and travel speed, to prevent overheating and maintain consistent bead formation on delicate surfaces—thinner electrodes with smaller diameters aid in achieving quality welds on thin materials.
These smaller electrodes allow better control over heat input and reduce the risk of excessive penetration or distortion. It should be noted that while SMAW may present certain challenges with thin materials initially, experienced welders who possess a deep understanding of their equipment and settings still achieve high-quality results.
Other SMAW Limitations
The limitations of Shielded Metal Arc Welding should not overshadow its many advantages. While other welding processes may offer faster deposition rates or better suitability for certain applications, SMAW remains a versatile and widely used technique, especially when portability, simplicity, and adaptability are crucial.
By understanding these limitations and employing proper techniques and electrode selection based on the specific requirements of each project, skilled welders can overcome these challenges to ensure successful SMAW welds. It is essential for welders to continuously enhance their knowledge, refine their skills, and stay updated with the latest developments in SMAW to maximize its effectiveness while minimizing its limitations.
SMAW Joint Preparation
In the world of SMAW, proper joint preparation plays a vital role in ensuring successful and high-quality welds. While it may seem simple, neglecting or underestimating the importance of joint preparation leads to several welding issues, such as lack of fusion, porosity, and excessive distortion.
Joint preparation involves cleaning and preparing the base metal before welding, ensuring optimal conditions for the electrode to create a strong bond. By taking the time to properly prepare the joint, welders enhance the overall structural integrity and longevity of their welded components.
Various Techniques
There are several ways to prepare a joint when using SMAW. One commonly used technique is machining or grinding, which involves removing any surface contaminants, rust, or paint that may hinder proper fusion.
Another technique is beveling or chamfering, where an angle is cut into the edges of the joined metal pieces. Beveling allows for better penetration and stronger fusion between metals.
V-groove joints are often used in thicker materials to ensure sufficient space for filler metal deposition. Another important aspect of joint preparation is proper fit-up alignment, which involves accurately aligning and securing the metal pieces before initiating welding. It ensures even heat distribution during welding and prevents unnecessary strain on the joint.
Sometimes, certain joints may require preheating before welding to reduce thermal stresses that could lead to cracking or distortion in large or thick components. Preheating involves heating specific areas using torches or heating blankets to maintain uniform temperature distribution during welding.
Regardless of which technique is chosen for joint preparation in SMAW, careful attention must be paid to ensure clean surfaces are free from contaminants and adequate positioning and alignment of metal pieces.
In Sum
Proper joint preparation is crucial to achieving successful, high-quality welds in the SMAW process. By understanding the importance of joint preparation and employing cleaning, beveling, fit-up alignment, and preheating when necessary, welders enhance their welds' overall strength and durability.
Taking the time to prepare joints correctly ensures better fusion and reduces the risk of defects, such as lack of fusion or porosity. So remember to prioritize joint preparation in your SMAW projects for exceptional welding results!