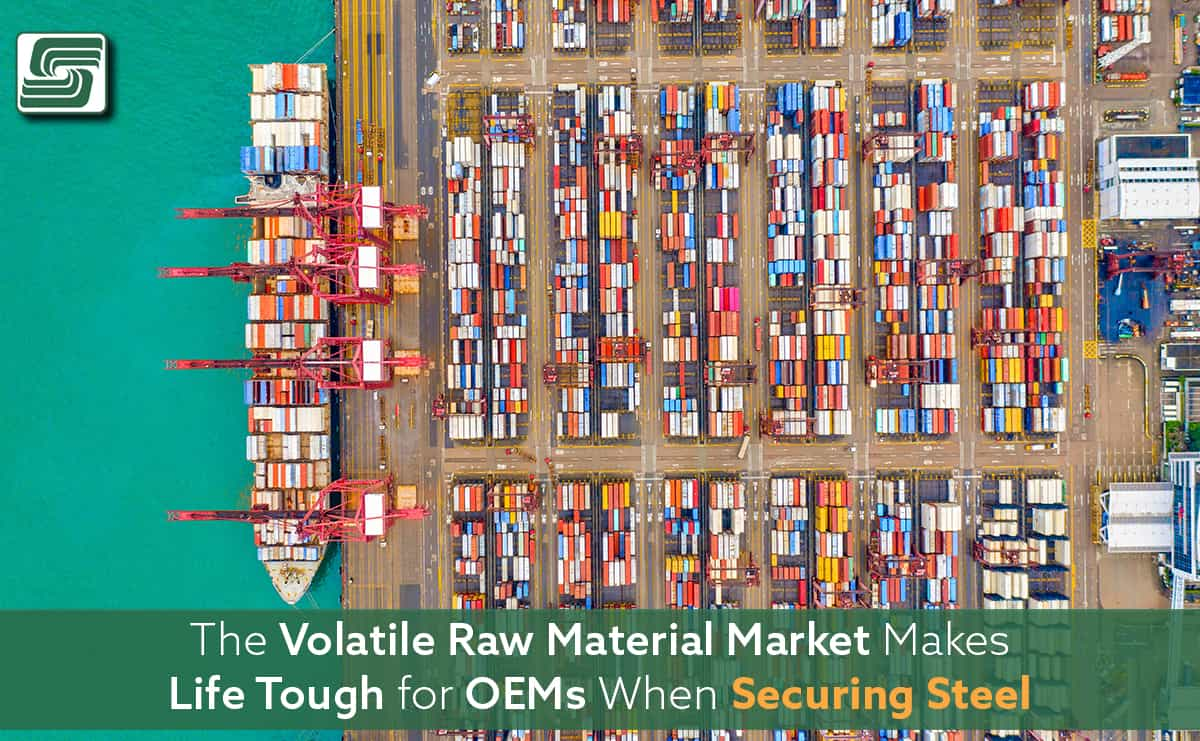
Finding and keeping a steady supply of high-quality steel is paramount for original equipment manufacturers (OEMs) engaged in metal fabrication.
The availability of steel significantly impacts production schedules, product quality, and, ultimately, the bottom line. Therefore, addressing many factors influencing steel availability is essential to successfully overcome procurement challenges.
One critical factor affecting steel availability is market demand. As the global economy fluctuates, so does the demand for steel across various industries such as automotive, construction, and manufacturing.
During periods of robust economic growth, the demand for steel surges as OEMs ramp up production to meet customer needs. Conversely, during economic downturns or market slumps, demand decreases as projects are delayed or shelved altogether.
These market demand fluctuations directly impact steel availability and create challenges in procuring sufficient quantities within desired timeframes. Another issue related to steel availability is its sourcing origin.
Steel is sourced locally or internationally, depending on cost-effectiveness and quality requirements. Locally sourced steel offers several advantages, including reduced transportation costs and shorter lead times.
Local Sourcing
Sourcing from local suppliers establishes closer relationships that foster better communication channels and opportunities for collaboration on quality control measures. However, relying solely on local sources may not always be workable because of limited capacity or specific technical requirements that cannot be met domestically.
In such cases, OEMs may need to look beyond their borders and explore international markets for sourcing raw materials like steel. Geopolitical factors also influence the availability of imported steel.
Trade policies and tariffs governments impose disrupt supply chains by increasing costs or limiting access to certain markets. For instance, political tensions between countries may cause trade barriers or embargoes that restrict the importation of steel from one nation to another.
Impacted Supply Chain
Natural disasters or unforeseen events severely impact global supply chains and affect steel availability. Disruptions caused by hurricanes, earthquakes, or pandemics halt steel production and transportation, leading to shortages in the market.
In recent years, the COVID-19 pandemic has highlighted the vulnerability of global supply chains and underscored the need for contingency plans to ensure a steady steel supply during unforeseen crises. Steel availability is an intricate issue that OEMs must navigate to overcome procurement challenges in metal fabrication.
Market demand fluctuations, sourcing origin considerations, geopolitical factors, and natural disasters play significant roles in determining whether an OEM can access sufficient quantities of high-quality steel. By closely monitoring market trends, diversifying local and international sourcing strategies, and implementing robust contingency plans for potential disruptions, OEMs can proactively address steel availability challenges and sustain smooth operations in metal fabrication processes.
Steel Pricing
One of the major challenges OEMs face when sourcing raw materials for metal fabrication is the volatile nature of steel pricing. Various factors influence steel prices, including global demand and supply dynamics, currency fluctuations, trade policies, and production costs.
These factors make it crucial for OEMs to have a deep understanding of these factors to effectively manage their procurement processes and mitigate the impact of price fluctuations. Quality is another significant consideration for steel pricing.
Steel Grades
Different steel grades vary in composition and properties, ultimately affecting their market value. For instance, high-grade stainless steel with exceptional corrosion resistance will generally cost more than lower-grade carbon steels used in less demanding applications.
OEMs must carefully evaluate their specific requirements and balance quality and cost when selecting the appropriate steel grade for their fabrication needs. Besides the quality aspect, OEMs also need to consider different methods of steel production as they influence pricing.
For example, Steel Melted And Welded (SMAW) is a popular technique for its reliability and flexibility.
It's Not Who You Know, But Where You Are
OEMs must carefully assess their priorities and determine which method aligns best with their budgetary constraints without compromising quality standards. The geographical location also plays a role in determining steel prices, as transportation costs significantly impact overall procurement expenses.
Steel mills closer to industrial hubs or ports offer more competitive prices because of reduced transportation costs compared to those farther away from major manufacturing centers. Hence, OEMs should strive for proximity when selecting suppliers to enhance cost efficiency within their supply chain.
Regularly monitoring steel market trends and staying updated on global factors affecting steel pricing is essential for OEMs to stay ahead in the procurement game. OEMs gain valuable insights into current and projected steel price trends by leveraging resources like industry publications and market reports and engaging in discussions with suppliers and industry experts.
With this knowledge, they can negotiate better pricing agreements with suppliers or explore alternative sourcing options when necessary. Steel pricing is a complex aspect of sourcing raw materials for metal fabrication that requires careful consideration of factors such as quality, production methods, geographical location, and market trends.
OEMs must balance cost efficiency and desired quality levels while also understanding the steel market dynamics. Doing so allows them to navigate pricing challenges effectively and optimize their procurement processes for successful metal fabrication operations.
Supply Chain Difficulties
One of the major challenges that OEMs face in sourcing raw materials for metal fabrication is dealing with supply chain difficulties.
The complexity of the supply chain in the manufacturing industry often leads to delays, disruptions, and increased costs. These difficulties are amplified in metal fabrication because of raw materials' specific requirements and characteristics, such as steel.
One common supply chain difficulty is the limited availability of high-quality raw materials. Steel, a primary material used in metal fabrication, is susceptible to fluctuations in availability—attributed to various factors such as market demand, geopolitical issues impacting imports and exports, and even natural disasters affecting production capacity.
The scarcity of high-quality steel significantly impacts an OEM's ability to meet production deadlines and maintain consistent product quality.
Another challenge within the supply chain is ensuring a steady flow of raw materials at competitive prices. Steel pricing is subject to market dynamics, causing significant fluctuations.
OEMs must navigate this volatility while striving to secure cost-effective raw materials without compromising quality. Engaging with reliable suppliers with strong relationships with mills and access to diverse sourcing options help mitigate this issue.
Logistics
Managing logistics within the supply chain poses additional challenges for OEMs sourcing raw materials for metal fabrication. Transportation is crucial in ensuring the timely delivery of materials from suppliers' locations to manufacturing facilities.
However, factors like limited shipping options or disruptions in transportation networks because of unforeseen circumstances cause delays or inventory shortages. OEMs often need to coordinate with multiple suppliers across different regions for their raw material needs, which introduces complexities related to communication, coordination, and consistency across the supply chain network. Ensuring seamless collaboration between suppliers becomes vital, as discrepancies or misalignments hurt production schedules or compromise quality standards.
Creating Necessary Paper Trails
Maintaining transparency and traceability throughout the supply chain is crucial for OEMs when sourcing raw materials, which involves tracking the origin of materials, ensuring compliance with regulations, and verifying quality certifications.
Establishing robust quality control measures and working closely with suppliers who adhere to internationally recognized manufacturing standards, such as SMAW (Shielded Metal Arc Welding), helps OEMs mitigate potential risks associated with inferior or non-compliant raw materials. Supply chain difficulties present significant challenges for OEMs in sourcing raw materials for metal fabrication.
The limited availability of high-quality steel, fluctuating prices, logistics management, coordination with multiple suppliers, and maintaining transparency are key issues that must be overcome. By developing strong relationships with reliable suppliers, implementing effective logistics strategies, and prioritizing quality control throughout the supply chain, OEMs can optimize their procurement processes and successfully navigate these challenges to ensure a steady flow of raw materials for metal fabrication projects.
Denique
Buying raw materials for metal fabrication presents several challenges OEMs must overcome to ensure a smooth and efficient supply chain.
The availability of steel, a critical raw material in metal fabrication, is influenced by several factors, such as global demand, production capacity, and trade policies. OEMS must establish strong relationships with reliable suppliers and have proactive strategies in place to mitigate potential disruptions caused by steel shortages.
Steel pricing fluctuations significantly impact the cost of production for OEMs. Rising steel prices erode profit margins and strain budgets.
Companies must implement effective price monitoring mechanisms to navigate this challenge successfully and explore alternative sourcing options without compromising quality, requiring careful analysis of market trends, negotiation skills, and continuous evaluation of supplier performance.
Supply chain difficulties pose yet another obstacle for OEMs in the procurement process. These complexities arise because of logistics constraints, transportation delays, and unforeseen disruptions.
To address these challenges comprehensively, OEMs should:
- Invest in robust supply chain management systems that optimize efficiency and minimize bottlenecks.
- Collaborate closely with suppliers and, using technological advancements, provide real-time visibility into the supply chain network while enabling timely decisions to enhance productivity.
Navigating the intricacies of sourcing raw materials for metal fabrication requires strategic planning, adaptability to market dynamics, and strong collaborative relationships with suppliers. OEMs effectively mitigate risks associated with steel availability challenges by adopting proactive measures, such as diversifying sourcing options based on quality standards and price competitiveness, while considering alternative materials or processes (such as SMAW).
While procurement challenges may seem daunting, they also present opportunities for innovation and growth. Embracing digital advancements like automation tools or AI-powered analytics streamlines processes while enhancing accuracy in demand forecasting or supplier selection criteria—ultimately improving overall operational efficiency.
By staying informed about industry trends and investing in sustainable supplier partnerships built on transparency where the emphasis is placed on maintaining quality standards, OEMs successfully position themselves to overcome procurement challenges. With careful planning, diligent execution, and a commitment to continuous improvement, OEMs can thrive in the ever-evolving landscape of metal fabrication procurement.