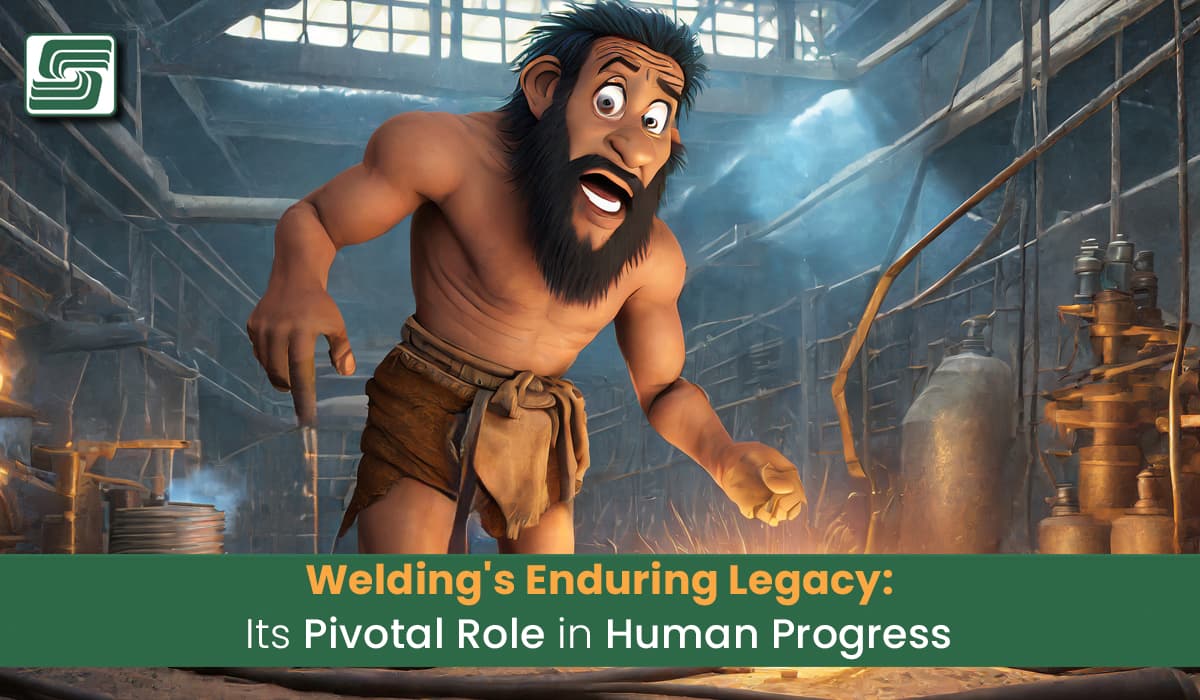
The Gifts of Modern Welding
The contemporary welding landscape is transformed by cutting-edge techniques that have elevated this craft to unprecedented heights. Automation, advanced filler materials, and robotic integration are but some improvements that have accelerated efficiency and precision dramatically. The magnitude of progress also encompasses sustainability and safety, as ingenious new methodologies aim to reduce wastage and protect human operators.
Modern welding has proven instrumental in constructing our modern world, shaping iconic structures like skyscrapers and enabling nanosecond processes inside electronic devices. Its multifaceted impact spans industries to fulfill demands for strength, versatility, accuracy, and speed.
The revolutionizing impact of modern welding techniques has manifested itself in several beneficial ways. One of the most pivotal advantages lies in the enhanced strength of the welded joints.
This enhanced strength is primarily because of the application of advanced welding techniques such as Friction Stir Welding (FSW). The metal-to-metal bonding through FSW leverages a solid-state joining process that eschews the melting and subsequent solidification of metal, eliminating common weaknesses related to traditional fusion welding.
This results in a weld that often surpasses the base material regarding tensile strength and durability. Yet another advantage of contemporary welding practices is their provision for greater precision.
With technologies such as laser beam welding or electron beam techniques, welders achieve pinpoint accuracy even on minute components. This amount of control has opened new avenues, especially within industries where precision is paramount, such as aerospace, where components must withstand extraordinary pressures while minimizing weight.
Modern welding equipment also permits intricate automation, enhancing precision and repeatability. Besides heightened strength and precision, material versatility is another boon brought forth by modern developments in welding technology.
Unlike traditional methods that proved incompatible with certain metals or alloys because of high thermal conductivity or varying melting temperatures - an issue particularly prevalent when dealing with dissimilar materials - new-age techniques have significantly broadened the range of weldable materials. For instance, friction stirs welding exhibits commendable adaptability to various materials, including but not limited to:
- Aluminum Alloys
- Copper Alloys
- Steel Grades
- Titanium
Efficiency stands tall, among other benefits reaped from modern-day advancements in welding technology. Using cool new methods like laser hybrid processes, we combine fast laser welding with deep penetration arc processes to speed up production without sacrificing quality. This confluence was hard to achieve using earlier practices.
Waste reduction has emerged as a blessing from these contemporary procedures since they involve fewer consumables than conventional methods, leading to substantial material savings. Since many modern methods generate lower heat inputs and less distortion than their predecessors, the need for post-weld rectification decreases correspondingly — facilitating a more resource-efficient process.
Operator safety has seen considerable improvements as well. As automation and robotics have become more intertwined with welding processes, human exposure to potentially hazardous conditions has decreased significantly.
This layer of protection not only ensures better protection for the workers but also circumvents issues like human error and fatigue, uplifting overall operational safety standards. In summation, the progressive evolution of welding technology has ushered many benefits that encapsulate elevated strength and precision, amplified material versatility, and amplified efficiency alongside waste reduction while also propelling improvements in operator safety.
Modern Welding Benefits
In the contemporary world, welding has emerged as a field of great significance owing to its great and diverse benefits. Welding, an art form that fuses materials using heat, is no longer confined to the constraints of traditional metalwork.
With technology and innovative methodologies, modern welding offers several advantages over conventional methods. It paves the way for revolutionary architectural feats, automotive advancements, and spacecraft assembly, thus becoming an indispensable tool in various industries.
One of the most noteworthy benefits of modern welding is its versatility. It's not just restricted to metals anymore; with newer techniques like laser welding and ultrasonic welding, materials like plastic can also be welded efficiently.
This breakthrough has broadened the horizons of this field and opened doorways to endless possibilities in terms of material application. Devices as minuscule as microchips or as massive as skyscrapers - all owe their existence to this versatile practice.
Modern welding techniques bring a level of precision that was hitherto unattainable with traditional methods. Techniques such as TIG (Tungsten Inert Gas) or MIG (Metal Inert Gas) provide superior control over the weld area, particularly helpful when dealing with thin or delicate materials.
The remarkable precision these techniques offer contributes significantly to reducing waste production and increasing efficiency - another testament to how modern welding is shaping our industrial landscape. An additional benefit of modern welding practices is higher strength imparted on the resultant structures or products - leading to enhanced durability and longevity.
This strength often surpasses that provided by conventional fastening methods, such as bolting or riveting. This results in sturdier constructions that withstand rigorous use over extended periods without succumbing to wear and tear.
Thus, encapsulated within these four walls of text are some significant benefits offered by modern welding practices: versatility regarding materials used, precision that reduces waste production and increases efficiency, and imparting higher strength leading to enhanced structural integrity. Each of these factors substantiates the vital role welding plays in our modern industrial framework, making it a cornerstone of industries ranging from construction to automotive, aerospace, and beyond.
Higher Strength
Welding, in its most fundamental definition, is joining two pieces of metal together. Among the various methodologies employed in manufacturing industries, welding stands out primarily for its ability to produce joints of higher strength.
The resulting amalgamation of two metals fused through welding often surpasses the individual strength of the component materials. This heightened fortitude is because of a thorough melding at a molecular level, creating an integrated bond that is not attainable through other methods, such as bolting or riveting, which only fastens materials at specific points.
In industries where structural integrity is paramount, such as construction, aerospace, and shipbuilding, the robustness rendered by welding offers unparalleled assurance. Structures like bridges and skyscrapers leverage this property extensively to withstand significant loads and external forces.
Aerospace applications also benefit from this attribute; welded aircraft parts enhance durability and resistance against extreme atmospheric conditions. The strength augmented through welding does not compromise flexibility.
Despite their fortified toughness, welded structures keep a good level of ductility, depending on the materials used and the type of welding applied. High-strength steel welds absorb energy well under dynamic loading conditions - a characteristic crucial in withstanding earthquakes or storms, for example - contributing substantially to overall structural resilience.
The second element enhancing the appeal of welding in contemporary manufacturing processes relates to superior precision achievable through advanced techniques like laser or electron beam welding. These high-tech methods allow precise control over penetration depth and heat input - key factors influencing weld quality - enabling highly accurate joints within even minute components.
This level of precision serves particularly well in technology-driven sectors where components are increasingly miniaturized yet demanded to deliver high-performance levels. In microelectronics manufacturing, for instance, small-scale complex welds enable the integration of intricate circuitry into compact devices, such as smartphones or tablets, without compromising functionality.
Major advancements have been made toward automating these precise processes using robotic systems equipped with sophisticated sensor technology for real-time monitoring and feedback. This sensor technology provides consistent quality control, ensuring weld precision across volume production lines.
The versatility of welding provides another significant advantage over other bonding methods. It's not restricted to specific materials or types. It joins many metals, including but not limited to steel, aluminum, titanium, and even exotic metals like Inconel or Hastelloy.
This flexibility extends beyond material types to include varied thicknesses, from thin sheet metal commonly found in automotive bodywork to heavy plates used in shipbuilding or infrastructure projects. In addition, different welding techniques can be employed depending on the materials involved and the desired outcome - leading to optimal results tailored for each application.
The realm of welding is dynamic and ever-evolving - constantly adapting to industry demands while pushing the boundaries of what was achievable. The strengths it presents - physically through robust bonds it forms, technologically via precise methodologies it employs, and materially by its extensive adaptability - are all testament to its continued relevance in the modern-day manufacturing landscape.
Greater Precision
There is something inherently gratifying and awe-inspiring about the sheer precision that modern welding methods achieve. It is an aspect that underscores the beauty of this craft, showcasing the skill and exactitude necessary to wield these tools proficiently.
With advanced techniques such as laser or electron beam welding, minute details are no longer a daunting challenge but a welcome possibility. The close control over the beam size and intensity allows these processes to be as accurate as a fraction of a millimeter, broadening what can be accomplished in this field drastically.
This heightened level of precision has not only made intricate designs achievable but also increased overall efficiency by reducing errors and subsequent reworks. The consequences of misguided welds in manufacturing industries could be dire; such mistakes may lead to product failure or even pose safety hazards in severe cases.
But with greater precision comes fewer errors and, thus, higher consistency in results. This reliability has considerable implications for industries where accuracy cannot be compromised under any circumstance, including aerospace, automotive, and medical device manufacturing, among others.
The attribute of precision offers another dimension: it significantly widens material versatility - a topic we will delve into further. Many delicate materials that might have been damaged under older welding techniques can now be handled with care.
Likewise, various combinations of materials are considered incompatible with welding because their varied melting points can coexist harmoniously within a single construction, thanks to precise heat control systems used in modern welding practices. This exceptional precision is akin to an artist being given finer brushes and more vibrant colors—it opens up new avenues for creativity while minimizing potential pitfalls associated with human error or technical inconsistencies inherent in older methodologies.
Material Versatility
The versatility of welding as a fabrication process is unparalleled, which stands prominently apparent when we delve into the discussion of material versatility. Welding, under its broad spectrum of techniques, applies to an array of materials - be they ferrous or non-ferrous metals, alloys, or even some types of plastics. This jack-of-all-trades ability makes it an incredibly valuable utility in a world where design and construction regularly involve various materials.
Stainless steel, aluminum, brass, bronze, or copper each offer unique properties and challenges when bonding them permanently. For instance, stainless steel has exceptional corrosion resistance, which makes it ideal for situations where resilience against weathering is critical.
Aluminum is lightweight yet strong, making it suitable for applications requiring a balanced strength-to-weight ratio, such as in the automotive industry. Welding technologies have evolved to adeptly handle these different materials while maximizing their inherent attributes.
While traditional welding practices were limited predominantly to metals and alloys, modern welding technologies have expanded their scope, encompassing certain plastic and composite materials. Techniques such as ultrasonic welding or friction stir welding are used to create robust joints in plastics without introducing fillers, which alters the properties of the parent material.
The ability to weld such a diverse range of materials drives new possibilities in design and engineering fields where amalgamation variety often forms the crux of innovative solutions. Moving forward from material versatility towards improved efficiency, which comes next on our list, here lies another area where modern welding shines brightly.
It's no secret that time equals money in any commercial production process - and here's where speediness maintained without compromising quality becomes paramount. Welding automation systems are revolutionizing how projects are being executed across industries by cutting down turnaround times drastically while still delivering impeccable quality.
Whether using automated welders or implementing robotic welding systems, the efficiency gains are massive. And it's not just about speed either - automated and robotic welding systems also produce more consistent results than manual techniques, leading to overall improvements in the quality of finished products.
Besides saving time and improving output quality, advanced welding technologies also increase resource efficiency. The preciseness of these methods means they require less material input for the same output when compared to traditional methods.
This precision not only translates into cost savings but also aligns with sustainability objectives by reducing waste production. Let's explore how modern welding does its part in enhancing operator safety - an aspect that has evolved rapidly over recent decades because of technological advancements and regulatory changes.
Inherently, welding involves certain hazards, including exposure to intense light and heat, harmful fumes, electrical risks, and injuries from flying sparks or debris. However, modern safety equipment such as auto-darkening helmets provides better protection against harmful light emissions without compromising visibility at work.
Fume extraction systems help keep the air clean from toxic particulates while proper grounding techniques mitigate electrical risks significantly. Using robotic welding systems reduces human interaction with hazardous processes, thus enhancing operator safety considerably.
Modern welding offers many benefits spanning various aspects - material versatility to higher strength components, improved efficiency, less waste generation, and enhanced operator safety. It is undoubtedly a crucial cog in today's manufacturing landscape, shaping future innovations across industries around the globe.
In the current era of technological advancements and the industrial revolution, welding's contribution is indisputably pivotal. Modern welding methods have catapulted industries like automotive, construction, and aerospace to new heights.
Advancements, such as the automation of the welding process and the introduction of high-quality filler material, have been instrumental in this productivity surge. The automation of the welding process is indeed a remarkable achievement.
It allows for precision and consistency unattainable by human hands alone. Automated machines work around the clock without succumbing to fatigue or lapses in concentration, which are typical human traits.
Automation leads to an increase in output without increasing costs or resources used, thus improving overall efficiency significantly. Alongside automation, another notable advancement that contributes to improved efficiency is the development and use of high-quality filler material.
Welding's essence lies in its ability to join two distinct materials seamlessly, making filler materials crucial for quality welds. Modern technology has fostered the creation of superior filler materials that yield stronger, more durable joints than their predecessors — resulting in less need for rework or repairs further down the line.
Not only does this reduce costs associated with defects or failures, but it also streamlines operations by minimizing interruptions because of equipment downtime. The combination of these factors paints a clear portrait: modern welding practices have led to a significant boost in efficiency across multiple industries where they're applied.
Less Waste
In modern welding technologies, the concerted efforts to mitigate waste are revolutionary. Reducing waste is a crucial aspect that propels the industry towards sustainable practices. It is indispensable not only for manufacturing enterprises but also for preserving our fragile ecosystem from further degradation.
Traditional welding methods have been notorious for abusing raw materials, leading to substantial wastage. Contemporary procedures such as Tungsten Inert Gas (TIG) and Metal Inert Gas (MIG) welding have overturned this precedent by offering remarkable precision in controlling material usage.
These sophisticated techniques ensure that welders only use what's required, which dramatically reduces superfluous spending of resources and significantly lowers operational costs. Advancements in robotic welding are progressively minimizing waste with their unparalleled consistency and accuracy.
Robotic systems deposit precise amounts of filler metal during each weld, drastically reducing spatter and subsequent clean-up time factors that contribute significantly to cutting down material squandering and moving on to operator safety: an area where modern welding has made significant strides.
It is no longer characterized by endangering sparks flying around or hours spent in harmful positions in poorly ventilated, cramped spaces. Improvements in Personal Protective Equipment (PPE) have offered more comprehensive coverage of potential hazards involved.
Welders nowadays benefit from advanced auto-darkening helmets, which provide superior protection against ultraviolet and infrared light while enhancing visibility using adjustable shade levels. These helmets not only keep their eyes safe but also result in cleaner, more accurate welds due to improved visibility compared to traditional passive lens helmets.
Apart from protective gear upgrades, better-designed workplaces featuring adept ventilation systems present a further testament to how seriously operator safety is today. Ventilation plays a pivotal role as it shields operators from inhaling hazardous fumes emitted during the welding process, reducing respiratory ailments among operators.
Modern welding practices entail myriad benefits that transcend just proficiency and productivity. These advantages underscore the heightening emphasis on sustainability and safety in the industry.
By leveraging advanced techniques and equipment, welding transforms into a craft that balances efficiency, environmental consciousness, and operator well-being seamlessly. It signifies a commendable evolution not only in terms of technology but also in nurturing a more reasonable perspective toward resource utilization and worker welfare.
Operator Safety
Welding, while inherently precarious because of the intense heat and bright light involved, has seen vast improvements in operator safety with modern techniques and equipment. In the nascent stages of welding, a welder's daily task was fraught with potential hazards such as burns, eye damage, or inhaling poisonous fumes. The onset of innovative technology in recent years is revolutionizing the industry by mitigating these risks significantly.
One noteworthy development is the creation of automated welding machines performing repetitive tasks without human intervention. Not only does this free up skilled welders for more intricate assignments, but it also reduces their exposure to dangerous conditions.
These machines usually have sophisticated sensors that instantly halt operations if abnormalities are detected. This increased safety lessens the likelihood of accidents from machine malfunctions or unforeseen circumstances.
Advancements in personal protective equipment (PPE) have enhanced welder safety. Modern helmets now come fitted with auto-darkening shields that protect eyes from harmful rays without compromising visibility.
As for bodily protection, there are high-quality flame-resistant garments designed to shield workers from sparks and molten metal splatter without hindering mobility. Introducing extraction systems has had an immense impact on reducing hazardous fume exposure to operators.
These systems capture welding smoke at its source and filter it before releasing clean air back into the environment, ensuring that operators are not breathing in harmful particles. Incorporating ergonomic principles into tool design is another significant stride in promoting operator safety.
Welding tools these days are lightweight and balanced to reduce fatigue over prolonged periods of use, which helps prevent musculoskeletal disorders among welders. The path forward seems set on making the profession safer than ever, with constant research and development aimed at refining technologies even further while always keeping operator safety at its heart.
In Sum
The transformative force of modern welding comes full circle, enriched with heightened efficiency, precision, and versatility. Its benefits extend beyond physical functionality into environmental and human realms by curtailing wastage and uplifting safety. The arc of progress bends towards a sustainable and equitable future.
However, the true marvel of welding technology lies in its perpetuity - it empowers creation across time by overcoming limitations. The products forged by its flame symbolize not just human imagination but also the indomitable spirit that kindles innovation. Modern welding carries this spirit forward into the future by blending pioneering tools with noble intent.
And therein persists its real magic - manifesting visions and assembling multitudes into reality. Our modern world stands as a collective testament to this technology. Its past glories steer us while its future potential propels us onward, always aspiring to build something greater out of many unified parts.