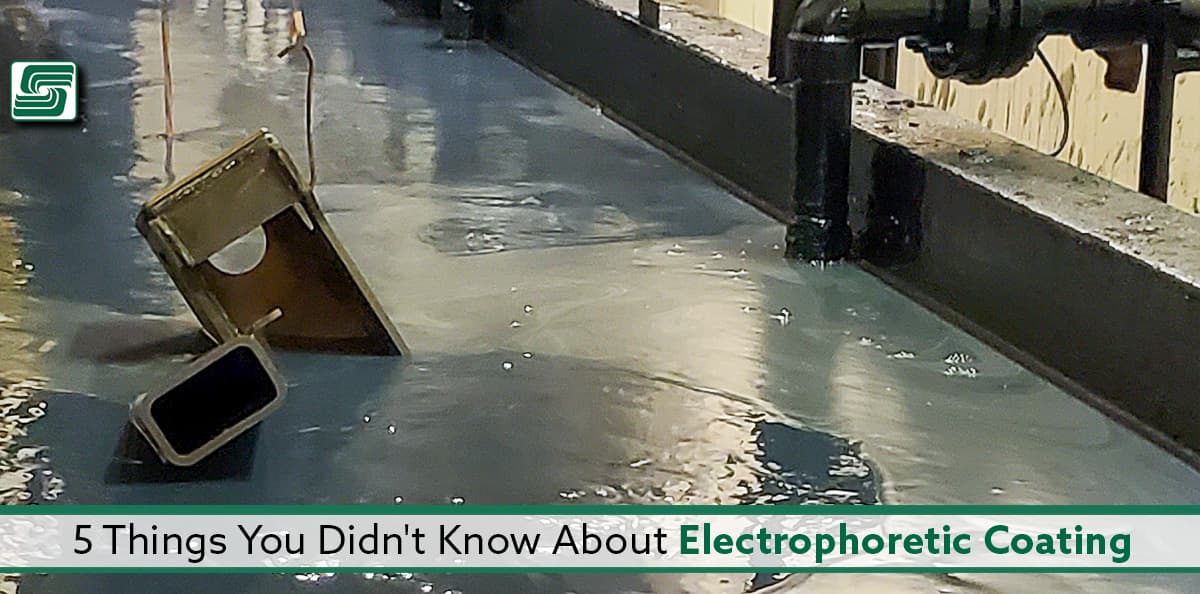
Electrophoretic coating started appearing inside steel food containers in US manufacturing in the 1930s. It took another 30 years before the other industries started e-coating, too.
It's an excellent history. However, e-coating wasn't contained just to the metal fabrication industry; it spread.
Here's an overview of the electrophoretic process.
What is Electrophoretic Coating?
We define electrophoretic coating as:
Electrophoretic deposition (e-coating/electric coating) is like electroplating. The electroplating process uses electric current reducing dissolved metal cations, forming a thin, coherent metal coating.
Electrophoretic Coating Applications
- Paper and Paperboard Coating: Used on paper and paperboard to finish the paper to get a matte finish and high gloss and for printing on different papers and board substrates—as long as they can accept a coating.
- Metal Coating: Used for coating metals for corrosion resistance, paint adhesion, and decoration in industries like automotive, aerospace, marine, and solar.
- Plastic Films: Used for coating plastic films and sheets for increased strength, toughness, and barrier properties.
- Printing on Fabrics: Used for fabric printing to get water-repellent properties.
Pros of Electrophoretic Coating
- Works with many substrates
- It's inexpensive: pennies on the dollar
- Applied by immersion, roll coating, and web coating
- No solvents are involved in this process, which means it is eco-friendly and doesn’t generate harmful fumes
- Results in a smooth coating with a high gloss
- It is highly effective for the decorative finishing of paper
Cons of Electrophoretic Coating
- Limited color range compared to other coating processes.
- The process takes longer if finishing companies have separate lines for their powder coat and e-coat. Operators must transfer the parts to the powder coat line after curing the parts.
- It is not good for porous coating substrates.
- It is not suitable for coating substrates sensitive to heat.
5 things you didn't know about electrophoretic coating
- The positive and negative charges in curable e-coat originate from ions present naturally in water-based coating compositions. They attract the ions to opposite poles of a charged electrode.
- EPC is a water-based process that uses positively charged particles suspended in a liquid to create a charged image on the surface of the substrate. In an EPC coating system, a negatively charged electrode attracts the positively charged particles, which are then attracted to the positively charged electrode.
- Using a strong electric field speeds up the charged particles' movement, allowing them to adhere to its electrode. The e-coating process ends with a trip through curing ovens.
- Industries also e-coat finishing paper to get a matte finish and high gloss for printing on different substrates like plastics, metals, and fabrics.
- It is important to note that e-coating doesn't work well with porous substrates.
Test e-coat strength
To test the strength of an e-coat, the companies use one or some of these tests:
- Taber Abrasion: Taber Abrasion is a test using a wheel containing sandpaper and applying it on the product's finish to see how many times the wheel goes before completely wearing it out. When placing the part vertically with a flat surface, the wheel is in contact with the entire surface simultaneously, and the test lasts longer.
- The DIN Abrasion: The DIN Abrasion is a test done for the same purpose as the previous one. The only difference is the wheel—it's smaller and made of rubber.
- The Pin and Swell Test: The Pin and Swell Test is a bottle production quality control test. In this test, QA techs poke a hollow needle into the product to check whether the e-coat has come in contact with the product or not.
- Salt Spray Testing: Another method for measuring the strength of a topcoat is an extended salt spray test. (Author's Note: One of our clients requires us to use this testing method, which you see on our testing page.)
Conclusion
Don't you hate it when someone asks you a question with many different answers, yet the only thing you can say is, "it depends."
An e-coat's durability depends on the type of metal, the ability of the company to apply the coating, and the environment the metal finds itself.
Companies do their best to replicate those environments, giving themself a chance to test their methodologies.
So, in this case, when asking how long an e-coat last, sigh, it depends.