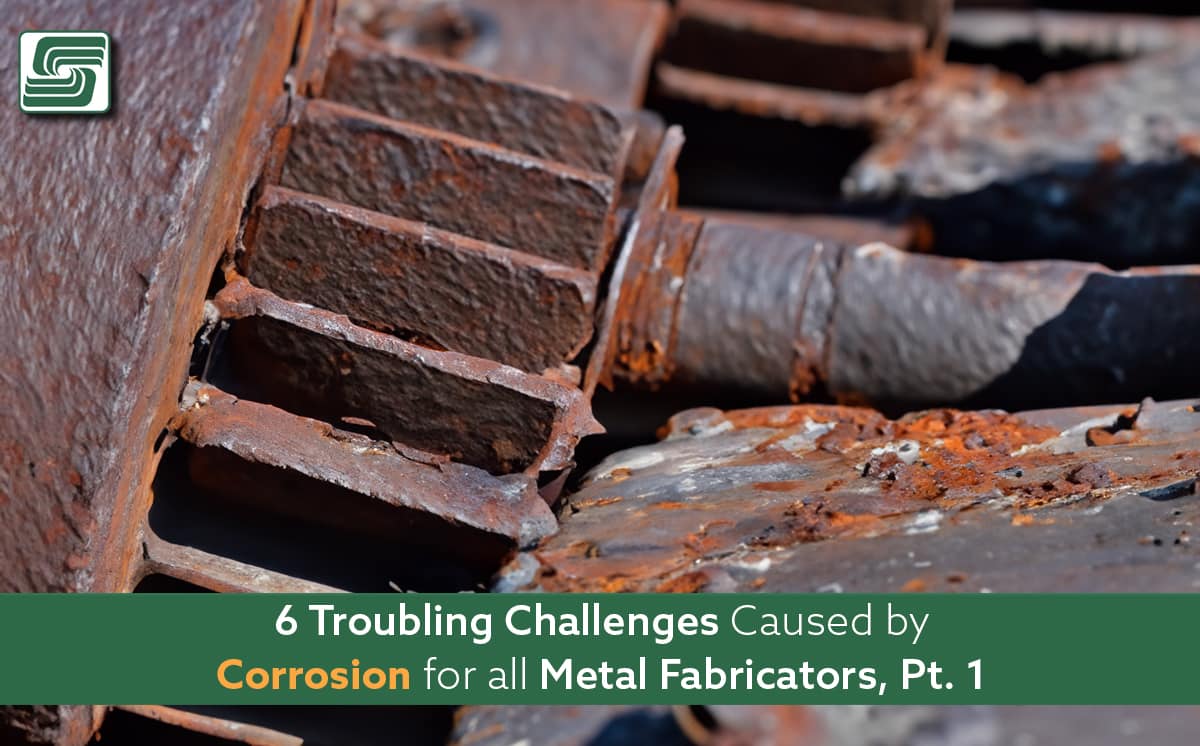
Corrosion is a quiet enemy in the world of metal fabrication. This subtle yet relentless process can lead to unexpected costs and delays, eating into profits and timelines.
Welcome to a two-part series where we talk about the challenges metal fabricators face when dealing with corrosion. In this first part, we explore the tangible impact of corrosion on material costs, production delays, and repair expenses. We delve into how corrosion can slow down your manufacturing process and cause material waste and why it’s essential to manage it proactively.
Material Costs
Material costs are one of the primary challenges engineers and project managers face with metal fabrication projects. The selection of materials used in these projects can significantly impact the endeavor’s overall budget and financial viability.
Various factors come into play when considering material costs, including the type of metals used, their availability, and their corrosion resistance. Different metals have varying degrees of corrosion resistance.
While some metals like stainless steel and aluminum are inherently more corrosion-resistant, they often come at a higher price point than other options, such as carbon steel. However, weighing this cost against potential long-term corrosion repair or replacement expenses is essential.
Additional protective coatings may be necessary for metal fabrication projects where parts or structures are exposed to harsh environmental conditions or corrosive substances such as chemicals or saltwater. These coatings provide an extra defense against corrosion and add to the material costs.
Considerations like powder coating, e-coat/topcoat systems, or electrostatic coatings might be required – each involving its expenses. Fluctuations in raw material prices affect the overall cost of a metal fabrication project.
Metals like steel are subject to market forces that dictate their pricing, including global demand, supply dynamics, and geopolitical factors. As a result, project managers must remain vigilant and stay abreast of market trends while planning for material procurement.
Selecting less expensive materials solely based on initial cost savings sometimes proves costly in the long run because of increased maintenance requirements or early failure because of corrosion. Therefore, an accurate estimation of total project costs must consider both immediate expenditures and potential future expenses associated with addressing corrosion issues.
Material costs play a significant role in determining the feasibility and success of metal fabrication projects. Choosing materials with optimal corrosion resistance is crucial for minimizing long-term expenses.
Selecting appropriate protective coatings enhances the durability of metal structures, albeit at an additional cost. When planning metal fabrication projects, project managers and engineers must carefully assess the trade-offs between material costs, corrosion resistance, and long-term maintenance.
Production Delays
One of the significant challenges faced in metal fabrication projects is the potential for production delays caused by corrosion.
Corrosion harms the efficiency and timeline of metal fabrication processes, resulting in significant setbacks. This section explores the reasons behind production delays and provides insights into potential solutions.
- When corrosion infiltrates metal components, it affects their structural integrity. It compromises their functionality, leading to delays as damaged or weakened parts must be replaced or repaired before the fabrication begins. For instance, if a critical component, such as a support beam or a load-bearing structure, suffers from extensive corrosion, it may need to be removed and replaced entirely, causing substantial interruptions in production.
- Corrosion also impacts surface preparation for subsequent treatments, such as electrostatic coating (e-coat/topcoat) or powder coating. Corroded metal surfaces often require intensive cleaning and preparation before effectively treating them with these protective coatings. Failure to adequately address corrosion issues during surface preparation may lead to poor adhesion of coatings, compromising their effectiveness and causing rework or complete re-coating. These additional steps extend production time and incur extra costs.
- Metal fabrication often involves welding and joining various components together.
But corrosion in welded joints poses a serious concern as it weakens the bond between metals, making them more susceptible to failure under stress or environmental conditions. In such cases, additional measures are required to retard corrosion at welded joints through techniques like special coatings or sacrificial anodes.
However, implementing these measures requires careful planning and execution during fabrication; otherwise, delays may occur because of necessary adjustments or rework. When metal fabrications are exposed to corrosive environments during storage or transportation before installation, accelerated oxidation could compromise their performance later.
Extended exposure times may result from unforeseen circumstances, such as logistical challenges or unexpected project delays. Protecting metal components during these stages becomes crucial, using appropriate packaging or temporary corrosion prevention techniques.
Failing to account for such measures leads to production delays, as damaged or corroded parts cause repair or replacement. Production delays caused by corrosion in metal fabrication projects occur for various reasons.
These include the need for component replacement or repair, time-consuming surface preparation for coating applications, complications associated with corrosion in welded joints, and issues arising from exposure to corrosive environments during storage and transportation. By addressing these challenges proactively and implementing preventive strategies like proper surface treatment, protective coatings, and careful handling during storage and transportation, manufacturers mitigate the risk of production delays caused by corrosion in metal fabrication projects.
Repair Expenses
In metal fabrication, projects can significantly burden businesses, as corrosion damage causes costly repairs and maintenance. Corrosion, caused by various environmental factors such as moisture, chemicals, and temperature fluctuations, compromises metal components’ structural integrity.
Consequently, companies must allocate substantial resources to address these issues promptly and effectively. One of the most common approaches to repairing corroded metal components is through surface treatment techniques.
These techniques aim to remove existing corrosion and protect the metal from further damage. Electrostatic coating is often employed as a repair method, where an electric charge attracts paint particles onto the metal surface evenly.
This technique provides a visually appealing finish and acts as a protective barrier against future corrosion. Powder coating is another widely used repair technique in the industry.
A dry powder containing pigments and resins is applied electrostatically to the metal surface. The coated part is then heated, allowing the powder to melt and form a durable protective layer over the corroded area.
Powder coating offers superior resistance against corrosion while providing an attractive finish that mimics different textures or colors. Sometimes, e-coat/topcoat systems are employed for repairing corroded parts in metal fabrication projects.
E-coating involves immersing the components in an electrically charged bath containing paint particles that adhere uniformly because of their opposite charges for the coated part. After e-coating, a topcoat layer may be applied for additional protection or aesthetic purposes.
Despite these effective repair techniques, it’s important to note that repair expenses are not limited solely to material costs but include labor costs associated with disassembling parts for treatment or replacement. These costs significantly increase in complex structures or large-scale projects, such as bridges or industrial equipment.
Sometimes repairing corroded metal components may not be workable or cost-effective because of extensive damage or structural compromise caused by corrosion. Complete component replacement becomes necessary in such cases, leading to even higher repair expenses.
Repair expenses in metal fabrication projects are a significant concern because of the corrosive nature of many environments. Businesses use various surface treatment techniques, such as electrostatic coating, powder coating, and e-coat/topcoat systems, to address this challenge effectively.
However, companies must consider the material and labor costs of these repairs. Mitigating corrosion risks through preventive measures minimizes repair expenses and ensures the longevity of metal components in fabrication projects.
Denique
Addressing the challenges faced with corrosion in metal fabrication projects is crucial for ensuring successful outcomes. While material costs can be a concern, investing in corrosion-resistant materials such as stainless steel or aluminum significantly reduce long-term expenses associated with maintenance and repairs. Implementing preventive measures like proper surface preparation and applying protective coatings like powder coating, e-coat/topcoat, or electrostatic coating enhances the durability of metal components.
Production delays caused by corrosion issues can be mitigated through efficient planning and scheduling. By incorporating regular inspections and maintenance into project timelines, potential corrosion-related disruptions can be identified early, allowing prompt remedial actions.
Collaborative efforts between design engineers, fabricators, and clients must ensure adequate corrosion protection measures are incorporated from the design stage. Repair expenses stemming from corrosion damage can be minimized by promptly addressing any signs of deterioration.
Stay tuned for part two of this article explores the remaining challenges that corrosion causes!