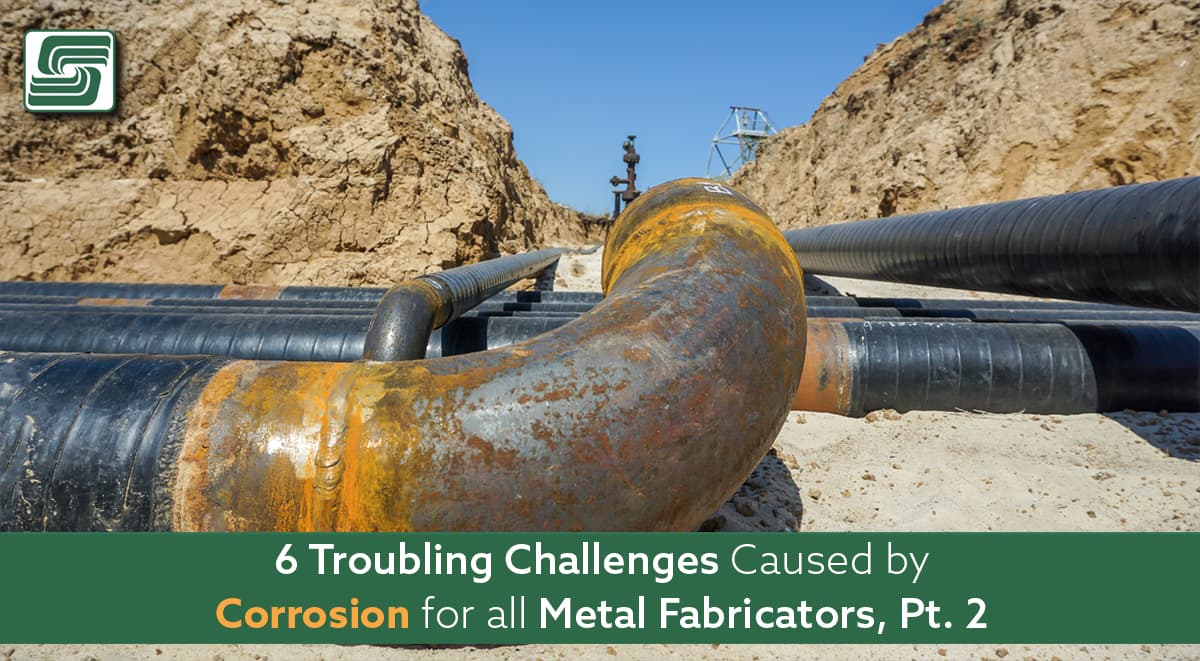
Safety and quality form the backbone of the metal fabrication industry. But there's a common adversary that poses risks to both - corrosion.
This follow-up article aims to spotlight the dangers of unmanaged corrosion, which compromises the structural integrity of your products, endangers the safety of your workplace, and affects your commitment to the environment. We discuss these issues and provide insights into controlling corrosion effectively.
Quality Concerns
In the realm of metal fabrication projects, quality concerns related to corrosion are of paramount importance.
Corrosion compromises the aesthetic appeal of fabricated metal products and undermines their structural integrity and functional performance. Ensuring high-quality finishes that resist corrosion requires meticulous attention to detail and adherence to industry best practices.
One crucial aspect of addressing quality concerns is the selection of coatings. Electrostatic coating, for instance, is a commonly used technique that involves applying a charged powder coating to a grounded metal surface.
This process ensures uniform coverage and minimizes overspray or uneven application issues. Powder coating offers excellent corrosion resistance because of its durable and protective nature, making it an ideal choice for metal fabrications exposed to harsh environments.
E-Coat/Top Coat
Another effective method is e-coat/topcoat systems, where the fabricated metal parts undergo a two-step coating process. The first step involves electrocoating (e-coating), where the parts are immersed in a bath containing a water-based paint solution with electrically charged particles.
The electrostatic attraction ensures uniform deposition on all surfaces, including tight corners or recesses inaccessible by traditional spray methods. The second step involves applying a topcoat layer for protection and aesthetic appeal.
Stringent quality control measures should be implemented at every fabrication stage to fully address quality concerns. Before coating application occurs, each component should undergo thorough surface preparation techniques, such as cleaning, degreasing, and abrasive blasting. This dedication to surface preparation ensures optimal adhesion between the substrate and coatings while preventing potential contaminants from interfering with the overall finish. Regular inspections throughout the production are vital in identifying potential defects or imperfections that could impact corrosion resistance or compromise product durability.
Implementing visual inspections under controlled lighting conditions reveals imperfections like pinholes, runs, sags, or other surface irregularities that may hinder long-term performance. Besides coatings and quality control measures during fabrication, it is essential to consider the proper storage and transportation of finished metal products.
Corrosion still occurs if adequate precautions are not taken. Effective packaging, including protective coatings, wraps, or desiccants to control moisture levels during shipping and storage, significantly minimizes the risk of corrosion damage.
Addressing quality concerns in metal fabrication projects involves selecting appropriate coatings, such as electrostatic or e-coat/topcoat systems. Rigorous quality control measures throughout the production process are crucial in ensuring optimal corrosion resistance and product durability.
Proper storage and transportation practices are vital to prevent corrosion from occurring after fabrication. By prioritizing these considerations, fabricators deliver high-quality metal products that will withstand the test of time and environmental challenges.
Safety Risks
Safety risks associated with corrosion are a matter of paramount concern.
Corrosion poses threats to the structural integrity of fabricated metal components and puts the safety of workers and end-users at stake. This section will delve into various safety risks arising from corrosion and highlight their potential consequences.
Weakened Metal
One significant safety risk resulting from corrosion is the weakening of metal structures. When metals corrode, they gradually lose strength and load-bearing capacity, leading to structural failures.
For example, in construction projects where corroded steel beams or columns support heavy loads, there is an increased chance of collapse, jeopardizing the safety of workers on-site and potentially causing severe injuries or even fatalities. Corrosion also introduces hazards related to sharp edges and protrusions.
As metal surfaces deteriorate because of corrosion, they may develop rough patches or sharp edges, causing cuts or puncture wounds if not handled cautiously. Workers involved in fabrication processes such as cutting, welding, or handling corroded metal parts must be vigilant to avoid accidental injuries caused by exposed rusty surfaces.
Chemical Exposure
Another concerning aspect regarding safety is the potential for chemical exposure during surface preparation or repair activities on corroded metals. Many traditional methods used in surface treatment involve chemicals, such as solvents and acids—which are hazardous when mishandled or improperly disposed of.
Workers need proper training and equipment (including personal protective gear) to minimize the risk of chemical-related injuries such as skin burns or respiratory problems. When corrosion affects industrial equipment or machinery involved in manufacturing processes, workplace safety has cascading effects.
For instance, if a critical component like a pump undergoes corrosive degradation without proper maintenance measures being taken promptly, it could lead to leaks or malfunctions that compromise worker safety by causing accidents like fires or explosions. It is crucial for industries engaged in metal fabrication projects to proactively address these safety risks associated with corrosion—achieved through implementing preventive measures such as regular inspections, maintenance programs, and protective coatings. E-coat/topcoat systems, powder coating, or electrostatic coating techniques create a barrier between metal surfaces and corrosive elements, thus significantly reducing the potential for deterioration and subsequent safety hazards.
Corrosion in metal fabrication projects poses various safety risks that must not be overlooked. The weakening of metal structures, sharp edges and protrusions, chemical exposure hazards, and impacts on industrial equipment increases the likelihood of accidents and injuries.
These safety risks can be mitigated effectively by adopting preventive measures like regular inspections and protective coatings, such as e-coat/topcoat or powder coating techniques. Ensuring a safe working environment is critical for safeguarding workers’ well-being and maintaining the integrity and reliability of fabricated metal components in a corrosive environment.
Environmental Impact
Environmental Impact Corrosion in metal fabrication projects poses significant challenges to productivity and profitability and harms the environment. The environmental consequences of corrosion cannot be overlooked, as they extend beyond the immediate financial implications.
In this section, we will explore some key aspects of the environmental impact caused by corrosion in metal fabrication projects. One of the most concerning environmental effects of corrosion is the release of harmful substances into surrounding ecosystems.
When metals corrode, they often produce toxic byproducts that contaminate soils and bodies of water. These byproducts include heavy metals such as lead, cadmium, and mercury, which have severe health effects on both humans and wildlife.
When these contaminants leach into water sources, they disrupt aquatic ecosystems and harm marine life. Corrosion may lead to increased energy consumption and greenhouse gas emissions.
When metal components degrade prematurely because of corrosion, they often require more frequent replacements or repairs. This results in higher manufacturing demands for new materials and increased energy consumption for transportation and production processes.
One effective approach is applying protective coatings such as powder coating or electrostatic coating (e-coat/topcoat). These coatings are a barrier between the environment’s metals and corrosive elements, reducing their exposure to moisture, chemicals, and oxidation processes that cause corrosion.
Powder coating offers an eco-friendly alternative as it does not use solvents or emit volatile organic compounds (VOCs) during application. Proper waste management practices are crucial for minimizing the environmental impacts of corroded materials.
Handling corrosive substances safely and disposing of them, then effectively following regulatory guidelines, is essential. Recycling programs should be established whenever possible to reduce the need for new metal production and conserve valuable resources.
The environmental impact caused by corrosion in metal fabrication projects cannot be understated. The release of toxic substances into ecosystems and the increased energy consumption associated with corrosion have far-reaching implications for humans and the environment.
However, through the use of protective coatings, effective waste management practices, and promoting recycling initiatives, we mitigate these environmental impacts. Metal fabrication industries must prioritize sustainability to minimize carbon footprint and preserve our natural resources for future generations.
Denique
Implementing a proactive approach through regular inspections and timely repairs prevents small issues from escalating into major problems that require costly replacements or extensive repairs. Fostering a culture of awareness among all stakeholders involved in metal fabrication projects is vital to ensure that minor damages are identified and addressed early on.
Quality concerns arising from corrosion-related issues should not be taken lightly. Corrosion affects the aesthetic appeal of metal components and compromises their structural integrity.
Implementing thorough quality control measures throughout fabrication is essential to identify potential defects or vulnerabilities that may speed up corrosion rates. Addressing safety risks associated with corroded metal components is paramount to protect workers’ well-being and avoid accidents or injuries.
Regular inspections of equipment and structures should be conducted to identify any signs of degradation caused by corrosion. Proper training programs should also be implemented to educate employees about potential hazards related to corroded materials and how to handle them safely.
Considering the environmental impact of corroding metals is crucial for sustainable practices in metal fabrication projects. Corrosion often releases toxic substances into the environment, posing risks to ecosystems and human health.
Metal fabricators can minimize their ecological footprint using corrosion prevention strategies like environmentally friendly coatings and implementing proper waste management practices. Although challenges exist, incorporating effective corrosion prevention measures throughout metal fabrication projects yields long-lasting and durable results.
These challenges can be overcome by investing in corrosion-resistant materials, implementing preventive maintenance routines, adhering to rigorous quality control standards, prioritizing safety protocols, and adopting sustainable practices. With careful planning and attention to detail, metal fabricators achieve successful outcomes that meet clients’ expectations and contribute towards a more sustainable future.