
Powder coating is a modern method of applying a decorative and protective finish to various objects, ranging from metal furniture to automotive parts. Unlike traditional liquid paint, made from solvents and binders that need to be evaporated or dried, powder coating involves the direct application of dry powder onto the surface of an object. The process starts with finely ground particles of pigmented resin being electrostatically charged, creating a strong bond between the powder and the object.
The application process typically involves two steps: spraying and curing. The charged powder particles are propelled onto the grounded component during spraying through an electrostatic gun, allowing for even distribution and adherence to all surface areas, including corners and edges. Once applied, the coated component is heated to melt and fuse the powder particles into a continuous film.
Advantages Over Traditional Liquid Paint
Using powder coating offers several advantages over traditional liquid paint methods, powder coating:
- Provides exceptional durability and resistance against chipping, scratching, corrosion, UV rays, chemicals, and even extreme weather conditions, making it ideal for outdoor applications such as fences or vehicle parts constantly exposed to harsh environments.
- Are available in several colors and finishes, including glossy, matte, textured, or metallic options.
This versatility allows for creative freedom in design choices while maintaining consistency in appearance across different surfaces. Powder coating is an environmentally friendly option compared to liquid paint because it lacks volatile organic compounds (VOCs).
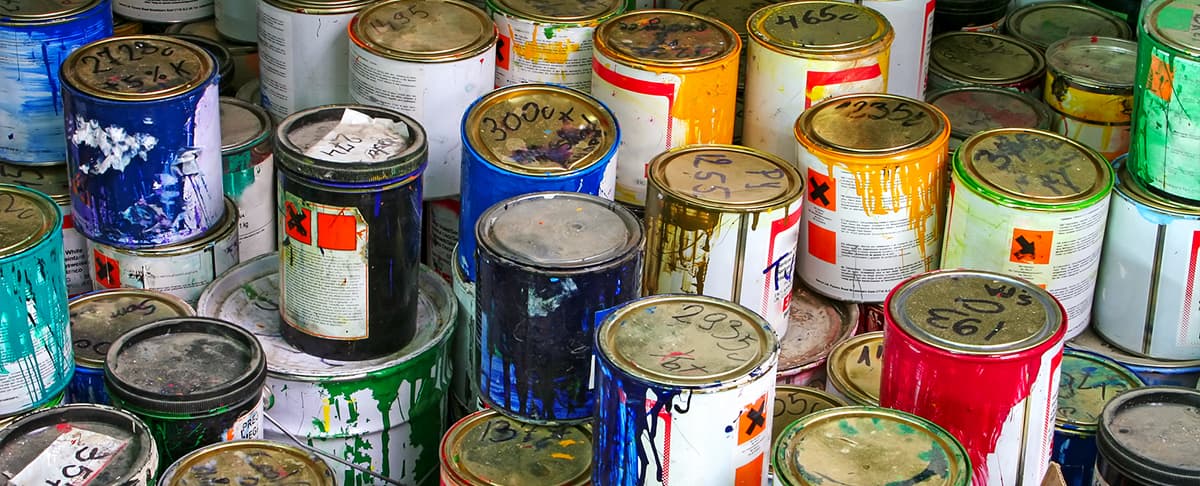
VOCs in liquid paints contribute significantly to air pollution as they evaporate during drying. In contrast, powders do not contain any solvents or harmful substances that harm human health or pollute the environment.
Another advantage is the efficiency and cost-effectiveness of the application process. With proper equipment, powder coating can be applied quickly and accurately, reducing wastage and saving time.
The absence of drying or curing time also increases productivity and shorter turnaround times. Powder coating is highly effective for applying durable finishes to various objects.
Its advantages over traditional liquid paint, including superior durability, versatility in finishes, environmental friendliness, and efficiency, make it a preferred choice in many industries. In the following sections, we delve deeper into the powder coatings available and the surface preparation and application processes involved in achieving optimal results.
Types of Powder Coatings
Powder coating is a versatile finishing technique that offers a wide range of options, depending on the desired application and performance characteristics. Understanding the different powder coatings available is essential for making informed decisions in various industries. Two major categories are commonly used: thermosetting powders and thermoplastic powders.
Thermosetting Powders
Thermosetting powders are the most widely used type of powder coating because of their exceptional durability and resistance to heat, chemicals, and weathering. Among the thermosetting powders, three prominent variations stand out: epoxy-based powders, polyester-based powders, and polyurethane-based powders.
Epoxy-Based Powders
Epoxy-based powders are known for their excellent mechanical properties and exceptional corrosion resistance. These coatings provide a tough, protective layer withstanding harsh environments. Epoxy powder coatings find applications in the automotive, aerospace, and electronics industries, where resistance to chemicals and abrasion is crucial.
Polyester-Based Powders
Polyester-based powders offer outstanding outdoor durability with good UV resistance and color retention. They provide excellent protection against fading caused by exposure to sunlight or harsh weather.
Polyester powder coatings come in various finishes, like smooth, textured, or metallic effects. They are commonly used in architectural applications such as window frames, fencing, and outdoor furniture.
Polyurethane-Based Powders
Polyurethane-based powders combine the advantages of epoxy and polyester materials. These coatings offer exceptional toughness along with excellent chemical resistance and flexibility.
Polyurethane powder coatings withstand impacts without chipping or cracking while providing good color retention even under prolonged exposure to ultraviolet light. They are commonly used in the automotive industry for applications such as wheels, bumpers, and interior trim parts.
Thermoplastic Powders
Thermoplastic powders differ from thermosetting powders in that they can be repeatedly melted and solidified without chemical change. This characteristic makes them highly versatile and allows for easy reprocessing. Two commonly used types of thermoplastic powder coatings are nylon-based powders and polyethylene-based powders.
Nylon-Based Powders
Nylon-based powders offer excellent mechanical properties, including high-impact resistance and flexibility. These coatings exhibit good resistance to chemicals, solvents, and abrasion. Nylon powder coatings find applications in various industries, such as healthcare, appliances, sporting goods, and electrical components, where a combination of durability and aesthetics is required.
Polyethylene-Based Powders
Polyethylene-based powders provide exceptional electrical insulation properties along with good chemical resistance. These coatings have low surface energy, making them highly resistant to dirt or staining. Polyethylene powder coatings are widely used in the wire & cable industry for insulation or as functional coatings on metal substrates where lubricity or non-stick properties are desired.
Surface Preparation for Powder Coating
Proper surface preparation is essential for achieving a high-quality, long-lasting powder-coating finish. Inadequate or improper surface preparation leads to adhesion issues, poor coating performance, premature failure, and wasted time and resources. Ensuring thorough surface preparation creates an optimal foundation for the powder coating process.
Steps involved in the surface preparation process:
Cleaning and Degreasing the Surface
The first step in the surface preparation process is cleaning the substrate to remove contaminants that could interfere with adhesion—including dirt, oil, grease, dust, fingerprints, and other residues that may be present on the material's surface.
Various methods can be employed for cleaning, depending on the size and characteristics of the substrate. These methods include solvent wiping, alkaline cleaning solutions, pressure washing, or abrasive blasting.
Removing Rust, Scale, and Old Coatings
It is crucial to eliminate any rust or scale on metal surfaces to achieve a smooth and even powder-coating finish. Rust undermines adhesion and leads to coating failure over time.
Mechanical methods such as sanding or wire brushing are commonly used to remove loose rust or scale. For more extensive rust or thicker scale buildup, abrasive blasting techniques using materials like aluminum oxide or steel grit may be necessary.
Besides rust removal, any old coatings or layers on the substrate should also be removed before powder coating application, which typically involves stripping off previous paint layers through processes such as sandblasting or chemical stripping.
Etching or Chemical Treatment for Better Adhesion
Etching or chemical treatment may be required for certain substrates, like aluminum or galvanized steel, that do not offer ideal conditions for adhesion because of their inherent properties (oxidation resistance). Etching involves applying an acidic solution to the substrate's surface, which creates a microscopically rough texture and promotes better powder coating adhesion. Chemical treatments, on the other hand, involve applying specific solutions that chemically react with the substrate's surface, creating an anchoring effect for the subsequent powder coating.
These treatments are particularly useful when dealing with challenging or non-porous materials. Surface preparation is a critical step in achieving a successful powder coating application.
It ensures proper adhesion and helps maximize the performance and longevity of the finished product. By thoroughly cleaning and degreasing surfaces, removing rust and old coatings, and employing etching or chemical treatments when necessary, you create an ideal foundation for a flawless powder coating finish that will withstand the test of time.
Powder Coating Application Methods
Electrostatic Spraying Technique
The electrostatic spraying technique is one of the most widely used methods for powder coating application. It involves using an electrostatic charge to enhance the adhesion and uniformity of the powder on the surface. Two common methods for charging the powder particles are corona charging and tribocharging.
The Corona Charging Method
This method applies a high voltage to a metal electrode near the powder spray gun. As the powder passes through this electric field, it becomes charged with positive ions. The charged particles are then attracted to grounded or negatively charged surfaces, ensuring an even and consistent coverage.
The Tribocharging Method
Unlike corona charging, tribocharging does not rely on external electrical sources. It involves frictional contact between the powder particles and a material electrostatically charged with the opposite polarity. The friction causes electrons to transfer between surfaces, resulting in a charge imbalance that attracts the powder particles toward grounded or oppositely charged surfaces.
Efficiency
The wonders of the fluidized bed dipping technique offer an alternative method for applying powdered coatings. In this process, preheated parts are immersed into a bed of fine powdered material kept in a fluid-like state by forced air or gas flow through tiny holes in a permeable membrane at the bottom of the bed.
Overview
As parts are dipped into the fluidized bed, they displace some powdered material that adheres to their surface because of static electricity from thermal energy transfer during immersion. Excess powder is later removed using compressed air or other methods before curing.
This technique is especially suitable for coating objects with complex shapes, as the fluidized bed allows for uniform coating even on recessed or difficult-to-reach areas. It also enables the application of thicker coatings compared to other methods.
Advantages and Limitations
One major advantage of fluidized bed dipping is its ability to create thick, durable coatings in a single operation. The process is relatively quick and requires little operator skill.
The excess powder is easily reclaimed and reused, reducing waste and costs. However, this method may not be suitable for all surfaces or objects because of limitations in controlling film thickness and achieving precise coating thicknesses.
It is more commonly used for larger parts instead of smaller components because of equipment size requirements. The electrostatic spraying technique (through corona charging or tribocharging) and fluidized bed dipping offer effective ways to apply powder coatings.
Choosing the right method depends on several reasons, such as part size, shape complexity, desired coating thickness, and overall production requirements. By leveraging these advanced application methods, manufacturers achieve high-quality finishes that are visually appealing and provide excellent durability and protection against corrosion.
Curing Process in Powder Coating
Heat Curing
Heat curing is a common method used to cure powder coatings and is known for its reliability and effectiveness. The process involves exposing the coated component to elevated temperatures in a curing oven.
Different curing ovens are used in the industry, each with its own characteristics and benefits. One commonly used type of curing oven is the convection oven.
These ovens use heated air circulation to disperse heat throughout the oven chamber, ensuring uniform powder coating curing. Another type is the infrared (IR) oven, which uses infrared radiation to rapidly heat the coating surface.
IR ovens are preferred when quick curing times are required or when coating heat-sensitive substrates. The temperature and time requirements for heat curing vary depending on several factors, such as the type of powder coating, substrate material, and desired finish properties.
Typically, the curing temperature ranges from 300 to 450 ºF (150 to 230 ºC), lasting around 10 to 30 minutes. Following manufacturer recommendations for specific powder coatings is crucial to achieve optimal results.
Ultraviolet Curing
In recent years, ultraviolet (UV) curing has gained popularity in certain applications because of its unique advantages. This method involves using UV light sources instead of heat for polymerization and cross-linking of the powder coating. UV-curable powders consist of photo-initiators that react when exposed to UV light, resulting in rapid cure times.
UV curing is preferred in industries where fast production turnaround time is essential, such as electronics or automotive manufacturing. The instantaneous nature of UV curing allows for immediate handling and packaging after application without waiting for cooling down periods like with heat-cured coatings.
While UV-cured powder coatings offer many advantages, such as energy efficiency because of no heat requirements and reduced volatile organic compound (VOC) emissions, there are also challenges to consider. UV curing requires specific equipment, such as UV lamps or LEDs, which is costly to install and maintain.
UV curing is best suited for flat or relatively uniform surfaces because of the limited penetration of UV light. Complex shapes or deep recesses may not receive adequate curing, compromising coating quality.
Heat and UV curing play essential roles in the powder coating industry. Heat curing provides reliability and versatility, whereas UV curing offers rapid cure times and energy efficiency benefits.
The choice between the two depends on factors such as production requirements, substrate compatibility, and desired finish properties. Understanding these differences allows for informed decision-making when selecting the appropriate curing process for specific applications in powder coating.
Powder Coating Quality Control
Quality Control Inspection Techniques
Visual Inspection
Visual inspection is a fundamental step in ensuring the quality of powder coating. A trained eye detects imperfections such as bubbles, pinholes, or uneven coating application.
Inspectors meticulously examine the surface of the coated component under proper lighting conditions to identify any flaws that may compromise the final finish. This process involves checking for color uniformity, texture consistency, and any visible defects that could affect the overall appearance and durability of the coating.
Film Thickness Measurement
Accurate film thickness is crucial to achieving optimal performance and protection. Specialized devices like electronic gauges or magnetic induction instruments are used to accurately measure film thickness.
These instruments gauge the thickness by analyzing variations in electrical resistance or magnetic fields caused by powder coatings on a substrate. Regular monitoring ensures compliance with industry standards and avoids issues such as inadequate protection against corrosion or excessive material usage.
Adhesion Testing
Adhesion testing assesses how well powder coatings bond with a substrate surface. Various methods are available depending on factors like coating type and intended application. For instance, crosscut tape tests involve making precise cuts through the coated surface with a defined pattern before applying an adhesive tape that is quickly removed.
The extent of coating removal shows adhesion strength. Another method uses pull-off testers that measure adhesion strength by applying a force perpendicular to the coated surface until separation occurs.
Environmental Considerations
As responsible stewards of our environment, we must consider proper disposal methods for excess powder coatings. Unusable powders should never be discarded carelessly but collected and disposed of according to local regulations governing hazardous waste materials.
Recycling programs for powder coatings are available in some areas, allowing for the recovery and reuse of unusable or excess powders. Adhering to these practices minimizes the environmental impact and promotes sustainable powder coating practices.
Denique
Quality control is integral to powder coating processes to ensure that the final product meets the desired standards. Manufacturers identify and rectify flaws or deviations through meticulous visual inspection, film thickness measurement, and adhesion testing.
Environmental aspects, such as proper disposal of excess powder, promote sustainable industry practices. By upholding rigorous quality control measures and caring for our environment, we are committed to excellence in powder coating applications while safeguarding our planet for future generations.