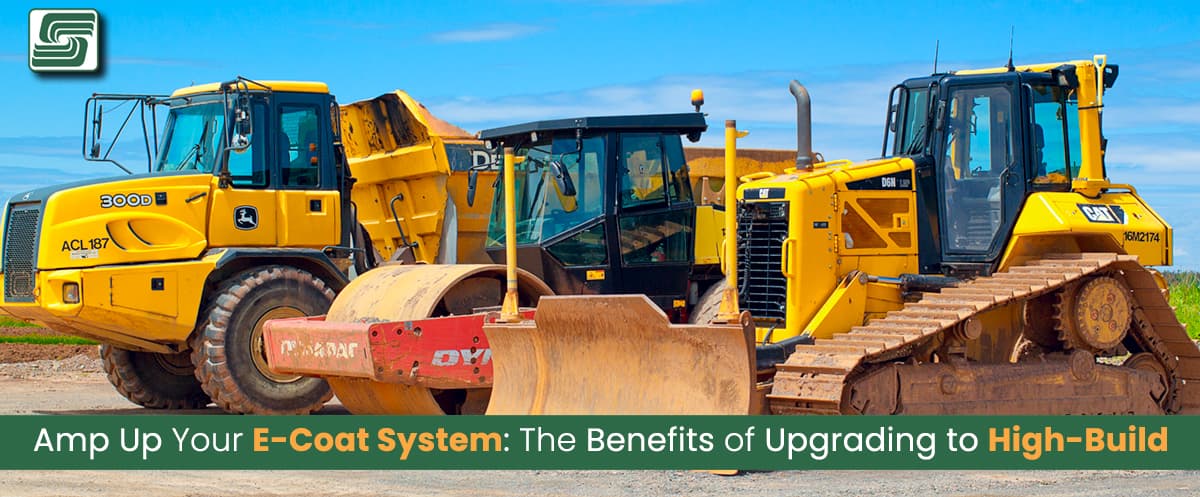
The earliest days of e-coating, electrodeposition coating, or electrophoretic deposition can be traced back to the 1930s. During this period, e-coating was primarily used for painting automobiles and industrial parts. However, the technology was still in its infancy and lacked the sophistication we witness today.
The Early E-Coating Process
The process involved immersing parts or components into a bath containing an electrically charged coating material. In those early years, e-coating systems used low-build coatings with limited thickness capabilities. The coatings were thin and had relatively low resistance to environmental factors such as UV radiation and chemicals. The corrosion protection these early coatings provided was inadequate for demanding applications.
The Shift Towards High-Build Systems
As time passed, industries realized a need for high-build e-coat systems to enhance performance and durability. This realization led to a surge in research and development efforts towards improving e-coat technology.
Factors Driving the Demand for High-Build Systems
Various factors contributed to the demand for high-build e-coat systems. One such factor was the start of more complex product designs in industries like automotive manufacturing. These designs required thicker coatings to protect against corrosion and other external stressors. Another driving force was increasing environmental regulations imposed by government agencies worldwide.
Technological Advancements in High-Build E-Coat Systems
High-build systems allowed manufacturers to achieve better coverage while minimizing material waste, reducing their environmental footprint. Technological advancements played a pivotal role in shaping high-build e-coat technology over time. Researchers started exploring different techniques, such as electrostatic assistance, pulsed voltage modulation, and modified resin formulations to improve coating thickness control and enhance overall performance.
The Impact on Various Industries and Sustainability
Innovative equipment designs enabled better paint film build-up on surfaces with complex geometries or recessed areas. These advancements allowed manufacturers from various sectors like automotive, aerospace, electronics, and appliances to fully use e-coating technology for enhanced protection and aesthetics. The evolution of high-build e-coat technology revolutionized how industries protect their products and paved the way for greater sustainability.
High-build systems have contributed to reducing the environmental impact of coating processes by reducing material waste and improving coating efficiency. The early days of e-coating witnessed a simple yet promising technology lacking the capabilities required for demanding applications. The need for high-build e-coat systems arose because of more complex product designs, stringent environmental regulations, and increasing demands for improved performance. Technological advancements have significantly shaped high-build e-coat technology, allowing industries to achieve better corrosion protection and overall durability while minimizing environmental impact.
The Early Days of E-Coating
It is crucial to delve into its roots and explore the early days of E-Coating to understand the evolution of high-build E-Coat technology. The concept of electrocoating, or E-Coat as commonly known, dates back to the early 1960s.
Initial Popularity and Basic Process
This revolutionary coating process quickly gained traction because it provided excellent corrosion resistance and superior coverage. During its nascent stages, E-Coat primarily involved immersing the metal parts in a bath that contained a conductive coating material suspended in water. An electric current was passed through the solution, resulting in a thin film deposition on the metal surface.
Limitations of Early E-Coat Systems
This initial technique proved effective for basic applications but had limitations when achieving thicker coatings. As industries recognized the need for increased protection against harsh environmental conditions and demanding service requirements, a demand emerged for high-build coatings.
Advancements in Coating Formulations
One of the key advancements during this period was the development of higher solids content in coating formulations. By increasing the concentration of solids, such as resins and pigments, in the bath, manufacturers achieved thicker films with improved coverage and protection.
Innovations in Electrodeposition Techniques
Another significant development involved modifications in electrodeposition techniques. Innovations like pulse electrodeposition brought forth precise control over film thickness by altering voltage levels applied during different phases of coating deposition.
Focus on Efficiency and Environmental Impact
Besides improving formulation and application techniques, research efforts were also focused on enhancing the E-Coat process's overall efficiency and environmental impact. Various pretreatment methods, such as phosphate conversion coatings, further improved corrosion resistance and adhesion properties.
The Role of Pretreatments
These pretreatments prepared the metal surfaces for optimal coating deposition and paved the way for more durable and long-lasting coatings. The early days of E-Coating set the stage for the evolution of high-build E-Coat technology by laying the foundation for advancements in formulation, application techniques, and pretreatment methods.
These developments addressed industry demands and paved the way for future innovations that would revolutionize protective coating processes. As we move forward in this article, we will explore how these early breakthroughs led to the emergence of high-build E-Coat technology as we know it today.
The Need for High-Build E-Coat
Introduction: The Shortcomings of Traditional E-Coating
As industries increasingly relied on efficient and durable coating solutions, the limitations of traditional e-coating methods became apparent.
Industry Demands for Robust Coatings
Traditional e-coating methods provided a certain level of protection but were often insufficient in harsh environments. Industries such as automotive manufacturing and infrastructure development demanded more robust coatings.
The Rise of High-Build E-Coats
High-build e-coats were developed to meet these stringent requirements by offering thicker film builds that provided superior barrier protection against corrosion. Improved adhesion properties were crucial in driving the demand for high-build e-coat technology.
Solving Adhesion Challenges
Traditional e-coats sometimes struggle to adhere to complex geometries or low-energy surfaces, leading to coating defects. High-build e-coats were engineered with enhanced adhesion characteristics, expanding their application potential.
The Importance of Aesthetics
Besides functional benefits like corrosion resistance and adhesion, aesthetics also played a vital role. Industries like consumer electronics and architectural design sought visually appealing coatings.
Advancements in Aesthetic Quality
High-build e-coats introduced advancements such as improved leveling capabilities and color consistency, elevating their aesthetic appeal without compromising protection.
Environmental Considerations
The environmental impact of coating technologies became a key consideration. Traditional methods often involved solvent-based compounds, releasing volatile organic compounds (VOCs) into the atmosphere.
Innovations for Sustainability
Reducing VOC emissions led to high-build e-coat technologies that offered low or even zero VOC options, addressing sustainability concerns and improving workplace safety.
The Multifaceted Evolution of High-Build E-Coat Technology
These advancements allowed industries to meet growing demands for durable, visually appealing, and environmentally friendly coatings. High-build e-coat technology has revolutionized multiple sectors, continuing to evolve to meet emerging challenges.
The Evolutionary Path of High-Build E-Coat Technology
Over the years, various technological advancements have shaped high-build e-coat technology, improving its efficiency and expanding its corrosion protection and aesthetics capabilities.
Breakthrough in Pretreatment Systems
One significant advance was the development of automated pretreatment systems. These systems prepare metal surfaces more efficiently than traditional manual methods, improving adhesion and corrosion resistance.
Advancements in Electrodeposition Paint Formulation
Another key development is in the area of paint formulation. Innovations in polymer chemistry have led to new formulations that significantly enhance performance, including superior corrosion resistance properties.
Customization in Coating Formulations
Technological advancements now allow for customization options like tinting or adding functional pigments, meeting specific industry needs more effectively.
The Role of Automation in High-Build E-Coating
Automation has revolutionized the high-build e-coating process by increasing productivity and reducing errors. Automated conveyors and robots ensure uniform coating, especially on complex parts.
Innovations in Electrical Control Systems
Significant improvements in electrical control systems have optimized coating quality. Advanced technologies help maintain optimal process conditions and uniform coating, even in hard-to-reach areas.
Advances in Curing Technology
Recent innovations in curing technology, like low-temperature infrared or UV curing systems, have made the process faster and more eco-friendly, reducing energy consumption and stress on substrates.
The Multifaceted Impact of Technological Advancements
These technological leaps have made high-build e-coating an indispensable solution across various industries. They offer manufacturers greater flexibility and contribute to higher-quality corrosion protection, confirming the technology's crucial role in modern manufacturing.
Broad Impact of High-Build E-Coat Technology
Over the years, high-build e-coat technology has significantly impacted various industries, from automotive to aerospace, revolutionizing corrosion protection and product durability.
Automotive Industry: Enhancing Longevity and Performance
High-build e-coating has improved the lifespan and performance of vehicles. Exceptional adhesion properties ensure uniform coatings on complex parts, resulting in aesthetic and functional benefits like safer, longer-lasting cars.
Construction Sector: Prolonged Lifespan and Reduced Costs
High-build e-coating has been crucial in protecting structural steel components in the construction industry. This has extended the lifespan of bridges and buildings while also reducing maintenance costs.
Appliance Industry: Corrosion Resistance and Energy Efficiency
The appliance industry has also seen significant benefits from high-build e-coat technology. Advanced coatings offer enhanced corrosion resistance and an additional insulation layer, reducing energy consumption in home appliances.
Aerospace Applications: Safety and Reliability
Recent years have seen the adoption of high-build e-coating in aerospace. The technology offers resistance against various environmental stressors, ensuring the safety and reliability of aircraft components.
Expanding Applications: Marine, Electronics, and Renewable Energy
High-build e-coat technology is not confined to the above mentioned sectors; it has applications in marine, electronics, and renewable energy industries, providing durable and long-lasting protection against corrosion.
The Growing Utilization of High-Build E-Coat
As more industries recognize the benefits of high-build e-coating, its use is expected to grow exponentially, reinforcing its importance across several applications.
Modern High-Build E-Coat
Introduction: The Evolution of Modern High-Build E-Coat
In recent years, technological advancements have significantly changed high-build e-coating, improving various aspects, from corrosion resistance to aesthetics.
Enhanced Coating Properties
Manufacturers have engineered coatings with improved corrosion resistance, adhesion, and aesthetics. These coatings are specifically designed to maintain superior performance while offering higher film thickness.
Modern Color and Gloss
Modern high-build e-coats showcase excellent color retention and gloss, making them ideal for the automotive, aerospace, and architecture industries.
Advancements in Application Process
The application process has seen notable advancements, such as advanced spray equipment and electrostatic technologies. These technologies allow precise control and consistent coverage, especially on intricate parts.
Automation for Efficiency
Automated systems enhance production efficiency and reduce human error, benefiting industries with time-sensitive production schedules.
Environmental Friendliness
Modern high-build e-coats have made strides in environmental sustainability by reducing VOC emissions. Water-based formulations are increasingly popular due to their low toxicity and reduced environmental impact.
Innovations in Curing Technology
Advancements in curing methods, such as infrared ovens or UV-curable formulations, have significantly reduced cure times while maintaining film integrity. Faster curing enables shorter production cycles.
Improved Film Adhesion and Flexibility
Innovations in resin chemistry have led to coatings with enhanced cross-linking capabilities, ensuring better adhesion across a range of substrates. Improved flexibility prevents issues like cracking or delamination.
The Transformative Impact and Future Prospects
Modern high-build e-coat technology has seen remarkable advancements that have impacted various industries. As research continues, further improvements are expected, particularly in meeting evolving industry needs and global sustainability goals.
The Revolutionary Impact of High-Build E-Coat Technology
High-build e-coating technology has revolutionized the coatings industry but presents several challenges to its continued success.
Challenge 1: Consistent Film Thickness on Complex Geometries
Achieving uniform film thickness on complex parts is a significant challenge. Manufacturers are turning to advanced application techniques to overcome this hurdle.
Challenge 2: Substrate Preparation for Optimal Performance
A clean surface is crucial for high-build e-coats to adhere properly. Contaminants can interfere with this, making thorough cleaning and preparation essential.
Challenge 3: Curing Complexities Due to Increased Film Thickness
Curing high-build e-coats comes with challenges, such as longer curing times and potential defects like gelling or blistering.
Challenge 4: Environmental Considerations
Traditional high-build e-coats have relied on toxic heavy metals, prompting a shift towards environmentally safe alternatives due to regulatory concerns.
Challenge 5: Cost Implications
The costs associated with equipment, materials, and specialized training can hinder the widespread adoption of high-build e-coat technology.
The Path Forward
Despite its advantages, high-build e-coat technology faces challenges that must be overcome for its continued growth. Manufacturers must focus on R&D and innovative solutions to successfully navigate these challenges.
The Promising Future of High-Build E-Coat Technology
The high-build e-coat industry is on the brink of significant growth and innovation, with advancements in several key areas shaping its future.
Advancements in Coating Materials and Formulations
Researchers are focusing on improving e-coat performance, durability, and environmental impact. This includes shifting towards low-VOC coatings and enhancing corrosion resistance with innovative additives.
Integration of Robotics and Automation
Automation and robotics will play a crucial role in the industry's future. These technologies can improve production speeds, eliminate human error, and optimize coating quality.
Focus on Energy Efficiency
There is a growing emphasis on developing energy-efficient e-coating technologies. This includes optimizing curing methods to consume less energy and designing systems to reduce overall process times.
Digitalization and Data Analytics
Digitalization, powered by AI, ML, and IoT advancements, is set to revolutionize the high-build e-coat industry. Data analytics will enable real-time process optimization, predictive maintenance, and proactive decision-making.
Substrate Adaptability and Multifunctional Coatings
The future will see greater adaptability in coating systems for diverse materials and industries. Coatings will offer additional functionalities like enhanced conductivity or self-healing capabilities.
A Bright Future Ahead
The future of high-build e-coat technology looks promising with advancements in multiple areas. These developments will contribute to more sustainable manufacturing and open the door for technology to revolutionize several industries.
In Sum
High-build e-coat technology has transformed from its early days of offering limited protection to becoming a crucial process in industries like automotive and aerospace. It excels in providing uniform, durable coatings on complex parts.
While the technology faces challenges such as inconsistent film thickness and environmental concerns, ongoing research aims to solve these issues. Innovations in materials and application techniques are driving the field toward more sustainable and efficient solutions.
The future of high-build e-coat technology is promising, with the potential for further breakthroughs that will continue to meet evolving industry standards and customer needs.