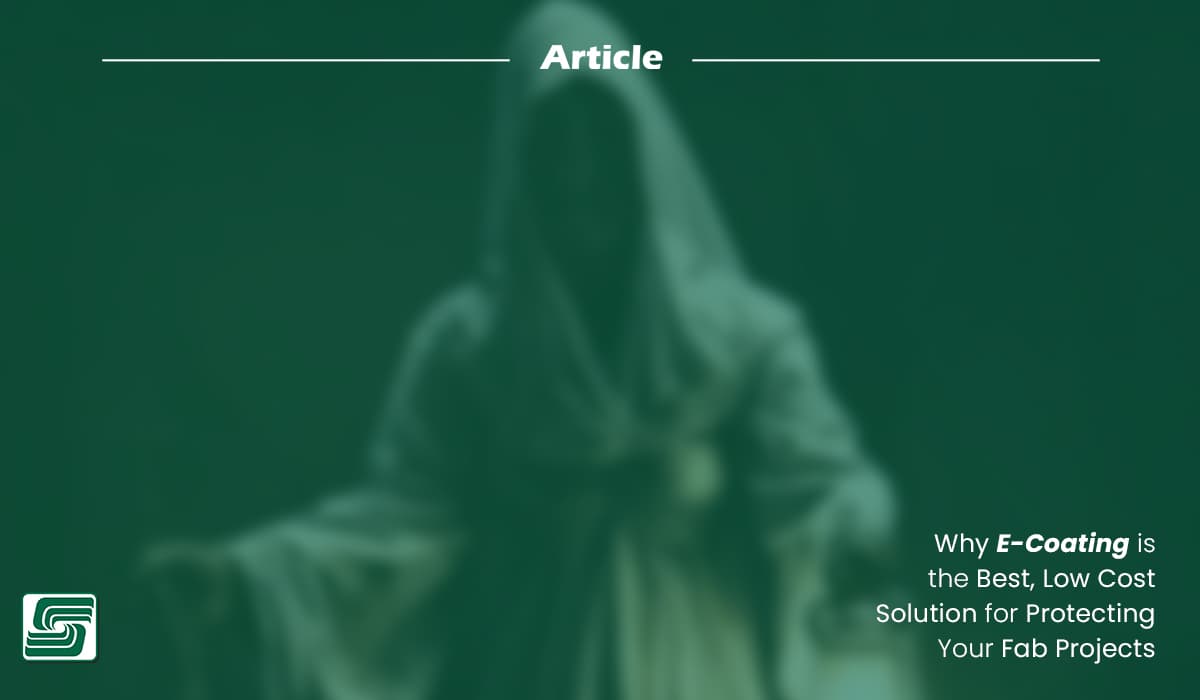
E-coating, also known as electrophoretic deposition, plays a crucial role in metal fabrication. This process involves immersing metal parts in a water-based solution, creating a uniform and durable coating. E-coating offers several advantages over traditional methods. It provides complete coverage and corrosion resistance, ensuring longevity.
What is E-Coating?
E-coating represents powerful protection for metal fabrication. This process involves immersing metal parts in a water-based solution. An electrical current applies a uniform coating to the metal surface. The result is a durable, protective layer that enhances the metal's longevity. E-coating stands out because of its ability to provide complete coverage, even in hard-to-reach areas. This method ensures that every part of the metal receives protection from environmental factors.
The science of e-coating revolves around the principles of electrochemistry. When metal parts are immersed in the water-based solution, they become charged. The electrical current causes the coating particles to migrate and attach to the metal surface. This process ensures a consistent and even layer across the entire piece. The coating's thickness remains uniform, contributing to its effectiveness in preventing corrosion. E-coating's scientific foundation offers superior protection to traditional methods—it enhances durability and improves the metal's appearance.
Table: E-Coating's Features, Advantages, Benefits
Feature |
Advantages |
Benefits |
Electrostatic Application |
Uniform Coating |
Even coating thickness, especially in hard-to-reach areas |
Immersion Process |
Complete Coverage |
All surfaces, including internal cavities, are coated |
Water-Based Chemistry |
Environmentally Friendly |
Low VOC emissions and reduced waste |
Cathodic Protection |
Superior Corrosion Resistance |
Long-lasting protection against rust and oxidation |
Controlled Film Thickness |
Optimized Performance |
Precise control over coating properties and durability |
Rapid Curing |
Increased Productivity |
Shorter cycle times and faster turnaround |
Versatility |
Wide Range of Applications |
Suitable for various materials and industries |
Excellent Adhesion |
Durable Finish |
Strong bond between the coating and the substrate |
The Electrocoat Process
The e-coating process begins with cleaning the metal parts to remove any contaminants. Once clean, the parts are dipped into the electrocoat bath. The electrical current causes the electrodeposition coating to form a uniform layer on the metal. This method ensures a consistent and even coating, providing superior protection against corrosion.
Key Steps in the Electrocoat Process
The electrocoat process contains several key steps that ensure the quality and durability of electrocoat products:
- Pre-Treatment: The process starts with cleaning the metal parts. This step removes oils, dirt, and other impurities that might affect the coating's adhesion.
- Electrocoat Bath: After cleaning, the parts are dipped into the electrocoat bath, which contains the charged particles necessary for the coating process.
- Electrodeposition Coating: An electrical current passes through the bath, causing the particles to migrate and adhere to the metal surface. This step forms the electrodeposition coating, ensuring a consistent layer across the entire part.
- Rinsing: After coating, the parts go through a rinsing process. This step removes any excess paint and ensures a smooth finish.
- Curing: The last step involves curing the coated parts in an oven. This process hardens the coating, enhancing its durability and resistance to environmental factors.
The electrocoat process offers several advantages over traditional methods. It provides complete coverage, even in hard-to-reach areas, and ensures a uniform thickness. This consistency makes electrocoat products highly reliable and effective in protecting metal surfaces.
Unique Features of E-Coat
Corrosion Resistance
E-coating provides exceptional corrosion resistance, making it a preferred choice of metal fabrication. This process involves acrylic electrocoating that forms a protective barrier on metal surfaces. The barrier prevents moisture and other corrosive elements from reaching the metal, ensuring that the metal remains free from rust and degradation. E-coating's corrosion protection ensures that metal parts maintain their integrity. This feature proves especially valuable in harsh environments where metals face constant exposure to corrosive agents.
Complete Coverage
One of the standout features of e-coating is its ability to offer complete coverage. Acrylic electrocoatings envelop every part of the metal, including hard-to-reach areas. This comprehensive coverage ensures that no part of the metal remains exposed to potential damage. The process involves immersing the metal in a solution, allowing the coating to adhere uniformly. This method guarantees that each section of the metal receives the same level of protection. Complete coverage enhances the durability and longevity of the coated metal parts.
Uniform Thickness
E-coating achieves a consistent thickness across the entire surface of the metal. This uniformity is crucial for maintaining the structural integrity of the coated parts. Acrylic electrocoatings ensure the thickness remains even, preventing weak spots that could lead to corrosion. Consistent thickness also contributes to the aesthetic appeal of the finished product. The smooth and even coating enhances the appearance of the metal, making it more visually appealing. This feature of E-Coat provides functional benefits and improves the overall quality of the metal fabrication.
Benefits of E-Coat in Metal Fabrication
Enhanced Durability
E-coat significantly enhances the durability of metal parts. The electrocoat process creates a robust layer that offers exceptional corrosion resistance. This layer is a barrier, preventing moisture and other corrosive elements from reaching the metal surface. Both anodic and cathodic E-coat methods provide superior protection. Anodic E-Coat forms a protective film, while cathodic acrylic electrocoating offers additional strength. Consistent coating application ensures that every part of the metal receives uniform protection. This durability extends the lifespan of metal components, making them suitable for harsh environments.
Cost-Effectiveness
E-coat presents a cost-effective solution for metal fabrication. The electrocoat process requires minimal material usage, reducing overall costs. Providing complete coverage eliminates the need for additional coatings or treatments. The efficiency of the process also reduces labor costs, as it involves fewer steps than traditional methods. The consistent quality of the coating minimizes the risk of defects, leading to fewer reworks and waste. The long-lasting corrosion protection reduces maintenance costs. Manufacturers benefit from these cost savings, making E-coat an economically viable choice.
Environmental Benefits
E-coat offers several environmental benefits. The electrocoat process uses water-based solutions, reducing the reliance on harmful solvents. This approach minimizes volatile organic compound (VOC) emissions, creating a cleaner environment. The process generates less waste as the coating adheres efficiently to the metal surface. Conversion coating techniques further enhance environmental sustainability by reducing the need for additional treatments. The ability to apply a dry film thickness with precision ensures minimal material wastage. By choosing E-coat, manufacturers support eco-friendly practices while maintaining high-quality standards.
Comparing E-Coat with Other Coating Methods
E-Coat vs. Powder Coating
E-coat and powder coating are protective layers for metal surfaces, yet they differ in application and benefits. E-coat involves immersing metal parts in a water-based solution, using an electrical current to create a uniform layer. This method ensures complete coverage, even in hard-to-reach areas, and provides excellent corrosion resistance. The process results in a consistent thickness, enhancing the durability of the coated parts.
Powder coating applies a dry powder to the metal surface using an electrostatic charge. The powder adheres to the metal and cures under heat, forming a solid layer. While powder coating offers a durable finish, it may not reach every crevice as effectively as an E-coat. E-coat provides a more uniform and consistent coating, especially for complex shapes.
In terms of cost, E-coat often proves more economical because of its efficient use of materials and reduced waste. Its water-based nature also contributes to environmental benefits, minimizing volatile organic compound emissions. Manufacturers seeking a reliable, cost-effective solution for corrosion resistance often prefer E-coat over powder coating.
E-Coat vs. Solvent-Based Spraying
E-coat and solvent-based spraying differ significantly in their approach to metal protection. E-coat uses an electrical current to deposit a uniform layer on metal surfaces, ensuring complete coverage and superior corrosion resistance. This method provides a consistent thickness, enhancing the longevity of the coated parts.
Solvent-based spraying involves applying a liquid coating through a spray gun. This technique results in uneven coverage and may require multiple layers to achieve the desired protection. Solvent-based coatings often contain volatile organic compounds, posing environmental concerns.
E-coat offers a more environmentally friendly alternative, utilizing water-based solutions that reduce harmful emissions. The process also ensures a more consistent and durable finish, making it a preferred choice for manufacturers prioritizing quality and sustainability. E-coat's ability to provide comprehensive protection with minimal environmental impact sets it apart from solvent-based spraying.
Applications of E-Coat in Manufacturing
Automotive Industry
The automotive industry relies heavily on E-coat for its superior corrosion resistance and durability. Manufacturers use the electrocoat process to protect vehicle components from rust and wear. This method ensures a consistent coating for parts exposed to harsh environments. E-coat provides complete coverage, even in complex shapes, ensuring that every part of the vehicle remains protected. The process also enhances the aesthetic appeal of automotive parts, contributing to a sleek and polished finish. The automotive industry achieves long-lasting protection and reduced maintenance costs using e-coating.
Construction and Infrastructure
In construction and infrastructure, E-coat plays a vital role in extending the lifespan of metal structures. The electrocoat process offers a robust barrier against environmental factors, such as moisture and pollutants. This protection is essential for bridges, buildings, and other structures exposed to the elements. E-coat's consistent application ensures that all surfaces receive uniform protection, reducing the risk of corrosion. The cost-effectiveness of E-coat makes it an attractive option for large-scale projects, where durability and longevity are paramount. By incorporating E-coat, the construction industry enhances the resilience and safety of its structures.
Consumer Goods
E-coat finds numerous applications in the consumer goods sector, where appearance and durability are key. Manufacturers use the electrocoat process to apply a smooth and even coating on products like appliances, furniture, and electronics. This method ensures a consistent finish, enhancing the visual appeal of consumer goods. E-coat also provides excellent corrosion resistance, protecting items from wear and tear. The process's efficiency and cost-effectiveness make it a popular choice for mass production. The consumer goods industry delivers high-quality products that meet customer expectations for aesthetics and longevity using an e-coat.
E-Coat Quality Control and Testing
Importance of Quality Control
Quality control in e-coating ensures that the final product meets high standards. Manufacturers prioritize this aspect to maintain the integrity and performance of coated metal parts. Quality control involves monitoring the entire process, from pre-treatment to curing. This vigilance helps identify any deviations that might affect the coating's effectiveness. Consistent quality control prevents defects, ensuring each part receives a uniform and durable layer. By maintaining strict quality standards, manufacturers reduce the risk of corrosion and extend the lifespan of metal components. Effective quality control also minimizes production costs by reducing waste and rework.
Testing Methods for E-Coat
Testing methods play a crucial role in verifying the quality of E-coated products. These tests assess the coating's durability, adhesion, and resistance to environmental factors. Common testing methods include:
- Salt Spray Test: This test evaluates the coating's resistance to corrosion. Metal parts undergo exposure to a salt-laden environment, simulating harsh conditions. The test measures how well the coating protects against rust and degradation.
- Gravelometer Test: This test assesses the coating's resistance to impact and abrasion. Metal parts are exposed to gravel or other abrasive materials, determining the coating's ability to withstand physical damage.
- Adhesion Test: This test checks the coating's bond with the metal surface. It involves applying and removing adhesive tape to see if the coating peels away. A strong bond shows a successful coating process.
- Thickness Measurement: This test ensures that the coating maintains a consistent thickness across the surface. Tools like micrometers or ultrasonic gauges measure the dry film thickness. Consistent thickness contributes to the coating's effectiveness and appearance.
These testing methods provide valuable insights into the quality and reliability of E-coated products. Manufacturers conduct thorough tests to ensure their products meet industry standards and customer expectations.
Future Trends in E-Coat
Technological Advancements
The electrocoat industry continues to evolve with technological advancements. Researchers and engineers focus on improving the efficiency and effectiveness of the electrocoat process. They explore new materials and methods to enhance the coating's durability and corrosion resistance. Innovations in automation and robotics streamline the electrocoat application, ensuring precision and consistency. These advancements reduce production time and costs, making e-coating more accessible to various industries.
Nanotechnology plays a significant role in the future of e-coating. Scientists develop nano-sized particles that improve the coating's adhesion and protective properties. These particles create a denser barrier against environmental factors, enhancing the metal's longevity. Integrating smart technologies allows for real-time monitoring and adjustments during the electrocoat process, which ensures optimal results and minimizes waste.
Sustainability Initiatives
Sustainability remains a key focus in the electrocoat industry. Manufacturers prioritize eco-friendly practices to reduce the environmental impact of the electrocoat process. Water-based solutions replace harmful solvents, minimizing volatile organic compound emissions. This shift contributes to cleaner air and a healthier environment.
Recycling and waste reduction initiatives gain traction within the industry. Companies implement systems to recycle excess electrocoat materials, reducing waste and conserving resources. Energy-efficient curing methods lower energy consumption, further promoting sustainability. The industry also explores biodegradable materials for electrocoat applications, aligning with global efforts to reduce plastic waste.
Electrocoat's ability to provide long-lasting protection reduces the need for frequent replacements, contributing to resource conservation. By extending the lifespan of metal products, electrocoat supports sustainable manufacturing practices. The industry's commitment to sustainability ensures that electrocoat remains a viable and responsible choice for future generations.
E-Coating offers a unique advantage in metal fabrication. It provides complete coverage, corrosion resistance, and uniform thickness. These features enhance durability and cost-effectiveness. E-Coating also supports environmental sustainability. Its applications span industries like automotive, construction, and consumer goods. The future of E-Coating looks promising with technological advancements and sustainability initiatives. This process continues to evolve, offering improved protection and efficiency. E-Coating remains a reliable choice for manufacturers seeking quality and longevity in their metal products.