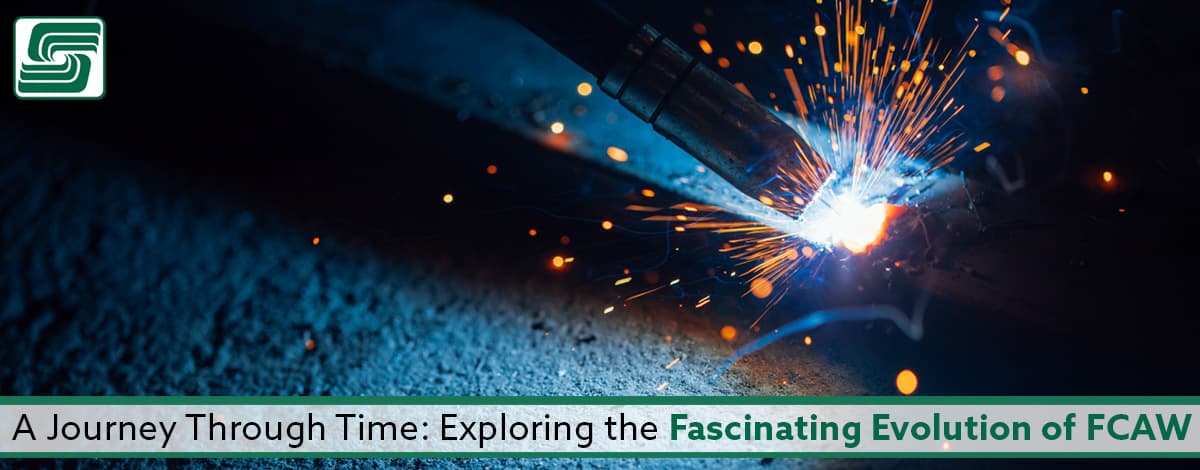
Flux-core arc welding (FCAW) is a type of arc welding process that has become a popular choice for metal fabrication and repair projects. It has been around since the 1940s and is still used today, making it one of the oldest and most reliable welding techniques.
Let's take a journey through time and explore the fascinating evolution of FCAW.
Introduction to Flux-Core Arc Welding (FCAW)
Flux-core arc welding is an arc welding process using a consumable electrode, or wire, to join two pieces of metal together. The wire is flux-cored, meaning it contains a flux-like substance, which helps to protect the welded joint from oxidation and contamination.
The flux also helps to provide an even, consistent heat distribution, allowing the weld to be stronger and more durable.
FCAW is a semi-automatic welding process requiring an operator to control the welding process. The operator feeds the wire into the weld pool and controls the speed and voltage of the welding current, allowing the operator to customize the weld to suit the project's specific requirements.
History of FCAW
FCAW has been around for over 70 years and has been used for a variety of welding projects. The development of the process has been quite dynamic and has changed significantly over the years.
FCAW Origins
The origins of FCAW can be traced back to the 1940s when it was first developed in the United States. At the time, it was a revolutionary welding process that allowed welders to join two pieces of metal quickly and easily. It was also less expensive than other welding processes, which made it a popular choice for many welding projects.
Originally, FCAW was only used for carbon steel welding applications. However, as the technology advanced, it became possible to use the process for a wider variety of materials, such as stainless steel, aluminum, and other alloys, making FCAW a much more versatile welding process and opening up new possibilities for metal fabrication and repair projects.
FCAW's World War II Legacy
The use of FCAW in shipbuilding during World War II allowed for the construction of Liberty ships, Victory ships, and T-2 tankers. The Liberty ships, in particular, were constructed with speed unrivaled in the history of merchant shipping because of the efficiency of FCAW and the number of welders employed.
For example, the California Shipbuilding Corporation delivered 20 Liberty ships in one month with the help of 6,000 welders and 160 FCAW operators! This production was a far cry from the days of riveting, which was much slower and less efficient.
FCAW was also beneficial in terms of safety. During this period, brittle fractures caused the loss of 140 ships. However, using FCAW allowed for the installation of crack arrestors, which prevented cracks from propagating. The result was a dramatic reduction in casualties, from 140 to 20 per month.
In addition to its use in shipbuilding, FCAW was also used to construct pressure vessels. This process allowed for higher pressures and temperatures and thick-walled vessels. To ensure safety, the American Society of Mechanical Engineers (ASME) issued a construction code in 1915, which they revised in the 1930s to accept welded vessels that had been judged safe by radiographic testing. In the 1940s, magnetic particle testing detected surface cracks missed by radiographic inspection.
In summary, flux-cored arc welding was crucial in speeding up shipbuilding during World War II. The process was more efficient, faster, and safer than traditional SMAW and riveting processes. The use of FCAW allowed the construction of larger and more complex ships in less time and with fewer welders.
After the War
In the 1950s, FCAW underwent several important changes that helped make it more reliable. For example, the flux-cored wire used in the process was improved to provide better protection from oxidation and contamination.
Additionally, the machines used to power the welding current were updated to provide more precise control over the welding process.
The 1960s saw the introduction of the self-shielded FCAW process, which eliminated the need for an external shielding gas, made the process much easier to use, and allowed welders to work in places where it was difficult to use traditional welding processes.
Major Milestones
In the 1970s and 1980s, several major developments further improved the FCAW process. For example, the introduction of the wire feed motor allowed welding speed and voltage to be precisely controlled, allowing welders to produce more consistent, high-quality welds with less effort.
In the 1990s and 2000s, FCAW was further refined by introducing more advanced machines and wire feed systems. These allowed welders to produce even better quality welds with greater efficiency. Additionally, robotic welding systems were developed, which allowed FCAW to be used for automated welding projects.
Key Characteristics
FCAW is a reliable and versatile welding process thanks to its many key characteristics. Let’s look at some of the most important characteristics of FCAW.
- FCAW is relatively fast and efficient compared to other welding processes. The process is semi-automatic, requiring an operator to control the welding process, but it is still much faster than manual welding. Additionally, the flux-cored wire used in the process helps to provide an even, consistent heat distribution, which helps to reduce welding time and improve weld quality.
- FCAW is inexpensive compared to other welding processes, using, and reusing, an inexpensive consumable electrode. Additionally, the process requires minimal setup and preparation, which helps to reduce costs.
- FCAW is easier to use than other welding processes, and the process is forgiving for inexperienced welders with minimal training. Additionally, the process is fairly safe, as the flux-cored wire used in the process helps to protect the weld from oxidation and contamination.
Popular Applications for FCAW
FCAW is a popular and common choice for various welding projects, including metal fabrication and repair projects, such as building or repairing structures and components made from steel, stainless steel, aluminum, and other alloys.
The process is also commonly used for pipe welding projects because the flux-cored wire provides a strong, consistent weld.
FCAW is also popular for automotive welding projects, where it's used for welding frames, exhaust systems, and components made from steel and aluminum parts.
Modern FCAW Techniques
FCAW has evolved over the years and evolved into several modern welding techniques. For example, the process can be used for automated welding projects, thanks to robotic welding systems.
The evolution of FCAW led to the development of a few important welding techniques: hardfacing, submerged arc welding, and atomic hydrogen welding.
Hardfacing Applications
Welding hardface applications is a difficult process because of the unique properties of the materials involved. Hardfacing is a welding process creating a wear-resistant surface on a metal component.
Materials used for hardfacing applications include high carbon and low alloy steels and non-metallic materials such as ceramics, carbides, and tungsten.
These materials often require special techniques, such as flux-cored arc welding (FCAW), to create a successful hardfacing application.
However, there are some difficulties associated with hardfacing applications that FCAW must overcome to succeed.
- Hardfacing materials are often brittle and prone to cracking. Carefully controlled welding parameters, which include monitoring the voltage, amperage, travel speed, and the type of electrode used, help prevent cracking.
- Hardfacing materials often require a high level of preheating before welding due to their high carbon content, which can cause cracking if the material is not heated sufficiently. Preheating also helps reduce the risk of weld porosity, which impurities can cause in the atmosphere.
- Shield the weld from the atmosphere to protect it from oxidation, especially with FCAW, since the flux in the electrode core provides the shielding. If the flux is insufficient, use an external shielding gas to provide additional protection.
Submerged Arc Welding
Submerged arc welding (SAW) is a welding process that uses a continuously fed consumable electrode and an arc shield to produce a high-quality weld. The concept of SAW began in the early 1900s and has since become one of the world's most widely used welding processes. It is used in many industries, from shipbuilding to automotive, because of its high speed, efficiency, and low cost.
The SAW process involves the formation of an electric arc between an electrode and the workpiece, shielded by a blanket of granular fusible material known as flux, which is laid directly over the weld area. The arc's heat melts the base metal's surface and the electrode's end, which travels through the arc to the workpiece, forming the deposited weld metal.
The SAW process uses current, either alternating or direct. It is also possible to use gas-shielded arc processes, such as FCAW; however, the SAW process is easier and cheaper. It has a higher deposition rate than other welding processes and produces a smoother, uniform weld than other arc welding processes.
For example, shipbuilders use the SAW process for welding thick plates in shipbuilding applications and surfacing and buildup work, maintenance, and repair. In SAW welding, the flux and wire are separate, and both impact the properties of the weld, requiring the selection of the optimal combination by the engineer for each project.
The SAW process is relatively simple and requires minimal operator involvement, making it an ideal choice for many applications. The process involves using a welding machine, a wire feeder and control system, a welding torch or welding gun, a flux hopper, and a travel mechanism.
The power source for SAW must be rated for a 100% duty cycle because operations are continuous, and the length of time for making a weld may exceed 10 minutes.
Atomic Hydrogen Welding (AHW)
Atomic Hydrogen Welding (AHW) is a thermo-chemical arc welding process invented by Nobel Prize winner Irving Langmuir in the early 1920s. The process uses an electric arc between two tungsten electrodes in the presence of hydrogen gas to create a strong weld bond. The process is known for its superior welds, high speed, and minimal distortion.
Atomic Hydrogen Welding (AHW) combines electric arc and gas welding techniques. In the AHW process, two tungsten electrodes produce an electric arc in a shielding atmosphere of hydrogen. The arc produces atomic hydrogen that recombines and releases tremendous heat. This heat melts the base metal and the tungsten electrode, and the metal melted off the electrode is transferred through the arc to the workpiece, where it forms the deposited weld metal.
This process requires a welding machine, an electrode holder, a welding torch, hydrogen gas cylinders, a filler rod or metal, and a controller with a 300V power supply. An AC power supply is used in the AHW because it provides an equal heat supply at both ends of the electrode, preventing any issues during the welding process.
Applications needing faster welds and a low level of distortion use AHW. It is well suited for stainless steel and hardfacing applications, as well as for welding tungsten.
The advantages of AHW include its high speed and low distortion, ability to produce wear-resistant surfaces, and ability to weld tungsten. However, the process is limited to flat positions and requires skilled operators, and AHW is expensive and more dangerous because of the presence of hydrogen gas.
Advantages of FCAW
FCAW has many advantages over other welding processes.
- The process is relatively fast and efficient, thanks to its semi-automatic nature, making it a popular choice for welding projects requiring speed and efficiency.
- The process is relatively inexpensive because the consumable electrode used in the process can be reused multiple times. Additionally, the process requires minimal setup and preparation, helping reduce costs.
- The process is relatively easy to use, even for inexperienced welders. The flux-cored wire used in the process provides an even, consistent heat distribution, which helps to reduce welding time and improve weld quality.
- The process is relatively safe, as the flux-cored wire helps to protect the weld from oxidation and contamination. Additionally, the process produces minimal fumes and smoke, helping reduce the risk of exposure to hazardous materials.
Disadvantages of FCAW
FCAW also has some disadvantages compared to other welding processes.
- It is unsuitable for welding thin materials because the flux-cored wire easily burns through them. Additionally, the process produces a large spatter, which is difficult to clean up.
- The process is unsuitable for welding projects requiring high accuracy and precision levels, as the welds can be uneven and inconsistent.
- The process is unsuitable for welding projects requiring a high level of strength and durability, as the welds can be weaker than those produced by other welding processes.
Safety Guidelines
FCAW is a relatively safe welding process requiring safety guidelines, including the following.
- Welders should always wear the appropriate safety gear, such as a welding helmet, gloves, and a welding jacket.
- Welders should be aware of their surroundings and any potential hazards.
- Welders should always use the correct welding machine for the project. Set the machine up properly, and adjust the current and voltage to the correct levels.
- The welding area should be kept clean and free from flammable materials.
- Welders should always use the correct, consumable electrode for the project. Inspect the consumable electrode before use and replace it if it is damaged or contaminated.
- Adjust the wire feed speed to the correct level to ensure a consistent weld.
In Sum
Flux-core arc welding is a reliable and versatile welding process that has been around for over 70 years. It is a semi-automatic welding process that uses a consumable electrode to join two pieces of metal together. The flux-cored wire used in the process helps to provide an even, consistent heat distribution, allowing the weld to be stronger and more durable.
FCAW is a popular choice for various welding projects, from metal fabrication and repair projects to automotive welding. The process is relatively fast, efficient, inexpensive, and easy to use. Additionally, the process is relatively safe, as the flux-cored wire helps to protect the weld from oxidation and contamination.
However, FCAW also has some disadvantages, such as its need for more suitability for thin materials and projects requiring high accuracy and precision levels. Additionally, welders should always follow the appropriate safety guidelines when using the process.
Flux-core arc welding is a reliable and versatile welding process that has changed significantly over the years. It is a popular choice for welding projects due to its many advantages, such as speed, efficiency, and cost-effectiveness. However, welders should always follow the appropriate safety guidelines when using the process.