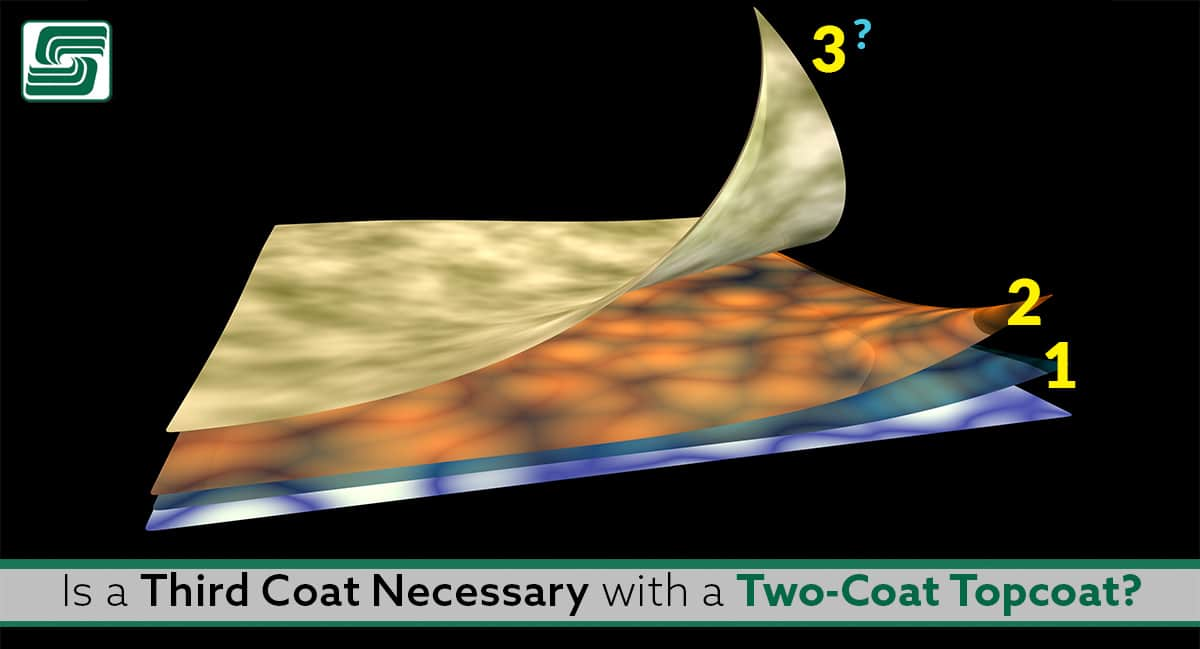
When using two-coat topcoats on a fabricated metal project, the question that comes up frequently is, "do I need a third coat?"
The standard response to this question is almost invariably, "No, two coats of topcoat are sufficient."
The reasons for that are:
- Two-coat topcoats have excellent hiding properties
- Two-coat topcoats are highly effective at hiding surface imperfections.
In addition, two-coat topcoats have a very high degree of lightfastness. A painted surface that resists fading when exposed to sunlight and other types of ultraviolet light is said to be lightfast. That high lightfastness makes two-coat topcoats suitable for protecting metal fabrications exposed to sunlight in service. Combining these two factors makes it possible to get excellent protection with an e-coat/topcoat.
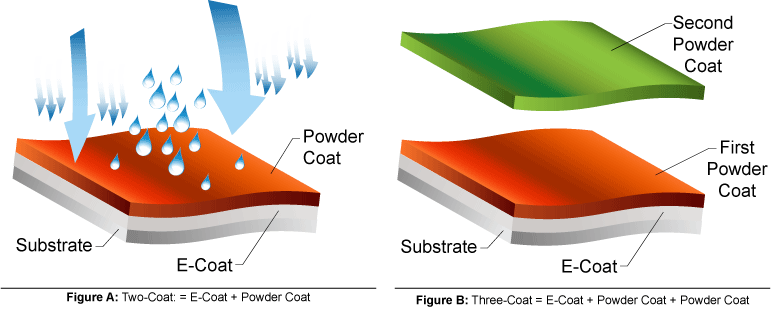
Note: This article is the first of a series exploring the e-coating process.
Part 1: Two-Coat Systems Using E-Coating
Part 2: Is a Third Coat Necessary?
Part 3: Testing Topcoat Strength
The Hiding Properties of Topcoats
When we talk about the hiding properties of a topcoat, we are referring to the ability of a topcoat to cover surface imperfections. This is a function of many factors, including the type of metal, coating thickness, and the application method.
The metal surface has a large role in determining the hiding ability of a topcoat. For example, a topcoat applied to steel hides surface imperfections better than a topcoat applied over aluminum because the steel surface is porous and has a lower density than aluminum. The porosity of the steel surface enables the topcoat to wick into the pores and fill the gaps, thereby providing a smooth, uniform surface.
The application method for the topcoat also affects its hiding ability. Generally, a topcoat applied by spray covers surface imperfections better than a topcoat applied by brush because a spray topcoat flows better over the imperfections and fills the gaps. The effectiveness of the ability of the topcoat to hide imperfection makes it possible to achieve sufficient protection with just two coats of topcoat.
UV Protection Provided By A Two-Coat Topcoat
Another important function of a topcoat is to protect against ultraviolet radiation.
The reason the color of a metal substrate fades results from UV radiation. A two-coat topcoat provides excellent protection against UV radiation. A two-coat topcoat is usually formulated with a UV inhibitor to provide better UV protection.
The level of UV protection provided by a two-coat topcoat depends on the type of basecoat and the type of topcoat. A two-coat system with a solvent-based basecoat and an acrylic topcoat provides better protection against UV radiation than a two-coat system with a water-based basecoat and an acrylic topcoat.
The level of UV protection provided by a two-coat topcoat is high. However, it is not adequate for all metal fabrications. This is because the level of UV protection provided by a two-coat topcoat depends on the thickness of the coating. The thicker the coating, the higher the protection against UV radiation.
A two-coat topcoat has a thickness of about 18-25 microns, which may not be suitable for metal fabrications that are exposed to intense sunlight.
One Coating Method For All Surfaces Is Not Practical
The traditional approach to coating a metal fabrication is to apply one coating method to all surfaces.
Using a single coating method for all surfaces is not practical because a single coating method is not suitable for all surfaces. For example, epoxy coating is not suitable for surfaces subject to a lot of wear, like the edges of walls, columns, stairways, and floors. For example, in applications like marine, where coating thickness is critical, they give the entire metal structure a single coat of epoxy.
Topcoat Drying Time
The application of a topcoat works through several stages, including:
- Applying the topcoat
- Drying time
- Curing time
Depending on the properties of the topcoat and the ambient temperature, the drying time varies between three to eight hours.
A Third Coat Provides No Additional Value Or Protection
As discussed above, two coats of topcoat hide surface imperfections and provide UV protection, making it unnecessary to apply a third coat. In fact, a third coat of topcoat provides no additional value or protection.
The only purpose of a third coat is to extend the drying time, which has no significance. However, there could be some advantages in extending the drying time if the substrate has to be kept in a clean room. This is because the length of time that the substrate needs to be kept in a clean room is usually 6 hours.
Consider These Results Before Applying the Third Coat
Electrostatic Problems
The first layer of powder insulates and reduces the electrostatic attraction to the metal surface, and this problem requires ensuring proper ground.
The second powder coat layer won't usually attract as quickly to the part as the first, resulting in more application time. The second coat must cover the piece and use the recommended minimum thickness. Otherwise, the top layer of powers is rough, like liquid paint overspray.
Thick Layers
Using more powder coating doesn't mean more protection. A ruined finish occurs with an excess of powder or a thick layer. Two of the most common issues relating to thick layers are orange peel and sagging.
Orange Peel
The powder forms tiny pockmarks and uneven texture, ruining any reflective finish. Orange peel with powder occurs when powder does not flow because of possible thin film or formulation. Back ionization from the application usually creates small pockmarks.
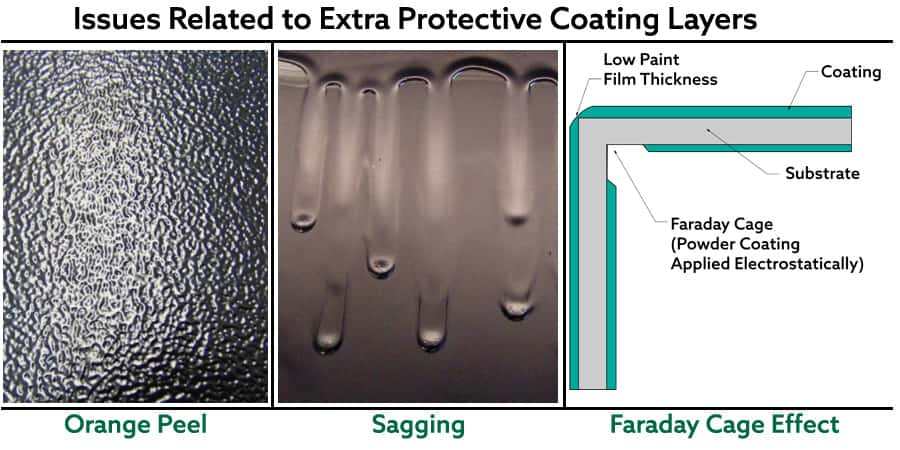
Sagging
If the powder weight is too much, the layer sags, like paint, leaving ripples and dips on the powder-coated surface.
Improper grounding is the usual suspect for thick coats. If the powder coating company doesn't have the right tools to apply a consistent ground properly, they typically use more powder to compensate. Adding more powder is more expensive and may not have a smooth finish.
Bulky Edges
Excess powder can build up around the part's edge, forming a fat rim called picture framing. This excess material may also experience the orange peel.
Faraday Cage Effect
Static may impede tight internal corner coverage, leading to thick streaks, thin patches, and inconsistent buildup. The Faraday Cage Effect is common, especially with complex parts. Everything from poor grounding to fine powder makes it hard to cover corners.
Bubbly Outgassing
Nearly every substrate has tiny pockets of moisture below the surface. Once covered, escaping moisture forms bubbles, breaking the surface and leaving it vulnerable to oxidation. Bubbly outgassing is usually associated with castings and can be moisture or air pockets, and outgassing rarely occurs with hot- or cold-rolled steel.
Overcoming Poor Intercoat Adhesion
Any delay in applying the third coat increases the chance of the material getting dirty. If there's a delay, then extra cleaning steps are needed. However, lightly sanding the surface is also recommended.
Many substrates have small amounts of water trapped beneath the exterior, breaking the surface and exposing the substrate to oxidation.
Castings and those with moisture or air pockets are likely to outgas, and hot- and cold-rolled steel are difficult to outgas. Outgassing is periodically noticeable in castings and results from moisture or air trapped in the metal. If applying the third coat too late, the material is more prone to contamination.
In Sum
A two-coat topcoat has excellent hiding properties and is highly effective at hiding surface imperfections. A two-coat topcoat protects against UV radiation and lasts longer in service. The standard response to the question "Is a third coat necessary?" is "No, two coats of topcoat are sufficient." A two-coat topcoat has excellent hiding properties and is highly effective at hiding surface imperfections. A two-coat topcoat protects against UV radiation and lasts longer in service. The standard response to the question "Is a third coat necessary?" is "No, two coats of topcoat are sufficient."
Don't forget that a third layer differs from a topcoat. The best way to achieve the third layer is to apply it to the bare metal substrate, and a third layer isn't as effective when applied to an existing two-coat layer.
Adding a third layer is a proven way to increase the corrosion resistance and harden the finish of most metals. A good after-market powder coating application is a good way to combine the best of both worlds. When properly applied by a trustworthy company with an automated coating machine and the right tools, you can create an even coat of protective finish for the metal surface.