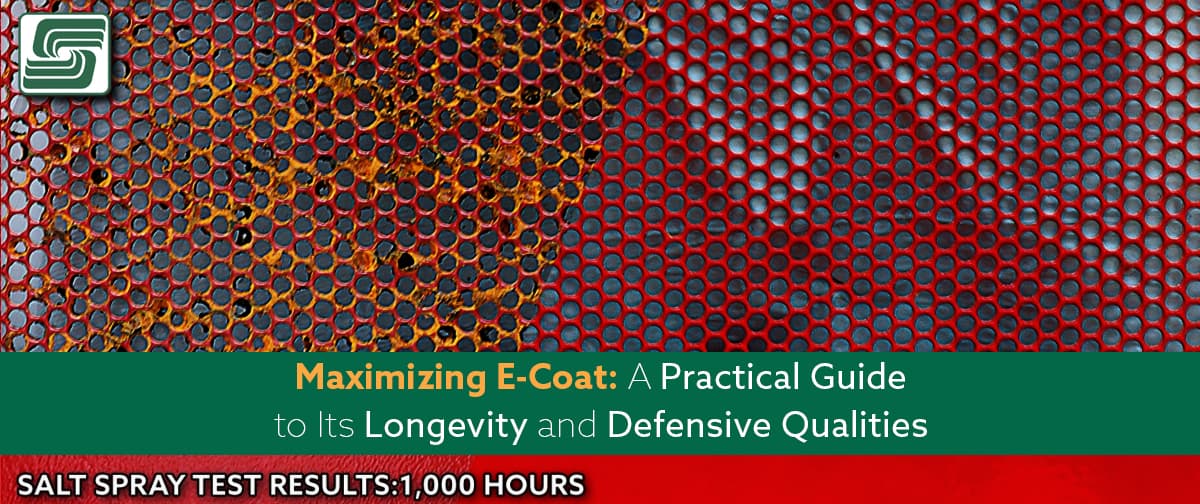
[Editor's Note: This article was originally published on the Central Wisconsin Finishing Website. A version is also being syndicated here to provide the content to a wider audience of readers who may be interested in the topic.
Schuette Metals Incorporated owns the two sites and often shares content and resources.
Both sites contain unique content not found on the other, but some popular evergreen articles are published on both sites if deemed highly relevant for the respective audiences. This article you are currently reading is one such piece that has been duplicated between the sites. You can find the original version here. The content is mostly the same between the two, with minor tweaks made.]
It's a relatively simple and inexpensive option, yet not all OEMs consider an e-coat an important part of their fabrication process. As the advantages and benefits of this protective metal coating grow, so does its implementation.
What follows is a comprehensive look at the process of e-coating.
How E-Coating Works
E-coating, also known as electrocoating or electrophoretic deposition, is a highly efficient and technologically advanced method of applying a protective coating to various materials.
The E-Coating Process
This process involves several key steps that ensure a thorough and efficient coating application. Understanding these steps will provide insight into the complexity and effectiveness of this coating method.
Pre-Treatment
Before the actual e-coating process begins, proper pre-treatment is essential to prepare the substrate for coating. This step typically involves cleaning the surface to remove contaminants such as dirt, grease, or rust.
The goal is to create a clean, uniform surface to promote adhesion and enhance corrosion resistance. Common pre-treatment methods include degreasing, alkaline cleaning, acid etching, phosphating, or sandblasting.
Masking
Certain substrate areas may need to be protected from being coated because of functional requirements or design specifications. Masking involves applying specific materials like tapes, plugs, or specialized coatings in these areas before entering the e-coating tank.
Masking ensures that only desired surfaces receive the protective coating while preserving critical features or sensitive components.
Electrolyte Bath Immersion
Once prepared and masked, the substrate is immersed in an electrolyte bath containing electrically charged particles of paint known as colloidal particles or a paint emulsion called slurry.
These particles consist of resin binders and pigments dispersed in water-based solutions.
Electrodeposition
Metal Substrate Being E-Coated.
The heart of e-coating lies in electrodeposition: an electrical current applies to drive the charged paint particles toward the oppositely charged substrates.
The positively charged anodes are present throughout the tank, while substrates act as negatively charged cathodes. As current flows through the electrolyte bath between these electrodes under carefully controlled conditions (voltage and time), electrochemical reactions occur at both ends, resulting in paint deposition on the substrate surface through an attraction force known as electrophoresis.
This deposition process enables a uniform and even coating thickness, reaching even the most complex shapes and recessed areas.
Post-Rinse and Curing
Once the desired coating thickness is achieved, the coated parts are rinsed with clean water to remove any excess paint particles or electrolyte residue.
This step ensures a clean, residue-free surface while preventing any potential contamination or adverse effects during subsequent curing processes. Following rinsing, the coated substrates undergo curing to complete the coating's mechanical properties and overall performance.
The curing process involves baking the coated parts in ovens at specific temperatures for a predetermined duration. This thermal treatment promotes cross-linking of the paint particles, enhancing adhesion, durability, corrosion resistance, and other desirable final coating properties.
The e-coating process encompasses these steps meticulously to ensure a high-quality and consistent outcome. From pre-treatment to electrodeposition and post-rinse with subsequent curing, these sequential stages play a crucial role in achieving exceptional protection for various substrates across multiple industries while offering environmental advantages because of their water-based nature.
E-Coating Types
There are several types of e-coating, each offering unique advantages and applications. This section explores the most commonly used e-coating types:
Cathodic Epoxy E-Coating
Cathodic Epoxy E-Coating is among the most widely employed because of its excellent corrosion resistance properties. This type of coating uses a negatively charged electrode as the substrate and a positively charged paint bath containing epoxy resin.
The electric current pushes coating particles toward the substrate, producing a uniform protective layer. Cathodic epoxy e-coating finds extensive use in automotive parts manufacturing, metal furniture production, and various industrial applications where exceptional durability is required.
Anodic Acrylic E-Coating
Anodic Acrylic E-Coating is another popular type that offers outstanding UV resistance. Unlike cathodic epoxy coatings, anodic acrylic coatings employ a positively charged electrode as the substrate and a negatively charged paint bath containing acrylic resin.
This e-coating provides excellent color retention and aesthetic appeal while delivering superior corrosion protection. Anodic acrylic coatings are commonly used for outdoor equipment such as fencing, agricultural machinery, and signage.
Cathodic Acrylic E-Coating
Cathodic Acrylic E-Coating combines the benefits of both epoxy and acrylic systems by providing excellent corrosion resistance along with enhanced color retention properties. This type of coating uses a negatively charged electrode as the substrate and an acrylic-based paint bath with positive charges.
Cathodic acrylic coatings find extensive application in industries such as appliance manufacturing (e.g., refrigerators), architectural structures (e.g., bridges), and electrical equipment.
Waterborne Systems
Waterborne Systems have gained significant popularity because of their environmental friendliness compared to solvent-based coatings.
These systems employ water as the primary solvent instead of organic solvents that harm human health and the environment. Waterborne e-coatings offer similar performance characteristics to other types while significantly reducing VOC emissions during application.
They are widely used in automotive manufacturing, metal packaging, and consumer electronics industries. It's essential to note that selecting the appropriate e-coating type depends on various factors, including the intended application, desired performance characteristics, and environmental considerations.
Manufacturers must carefully evaluate these factors to choose the most suitable e-coating type. E-coating types, such as cathodic epoxy, anodic acrylic, cathodic acrylic, and waterborne systems, offer a range of benefits to various industries.
An e-coating type is available to meet specific requirements: exceptional corrosion resistance, UV stability, color retention properties, or reduced environmental impact. Understanding these different types allows manufacturers to make informed decisions when selecting the most appropriate e-coating solution for their applications.
Coating Thickness by Method
The coating thickness is a crucial factor in determining the effectiveness and durability of the e-coating process. Depending on the method used, the thickness varies significantly, impacting the overall performance and appearance of the coated surface.
Dip Coating
Dip coating is one of the earliest methods employed in e-coating processes. In this technique, parts are immersed into a tank filled with electrically charged paint particles suspended in a liquid solution.
The coating thickness achieved through dip coating typically ranges from 0.5 to 2 mils (12 - 50 microns). This method is often used for small or intricately shaped components.
Spray Coating
Spray coating uses pressurized air to atomize paint particles into fine droplets propelled onto the coated surface.
The resulting thickness varies based on factors such as nozzle size, spray pressure, and distance from the substrate. Spray coatings achieve a range of 1 to 4 mils (25 - 100 microns), making them suitable for larger or more complex parts.
Electrostatic Spray
Electrostatic spray deposition relies on positively charged paint particles attracted to negatively charged substrates through an electrical field.
This technique enables highly controlled application and uniform distribution, resulting in consistent coating thicknesses ranging from 1 to 4 mils (25 - 100 microns). Electrostatic spray is often preferred for products requiring precise coverage.
Powder Coating
Although powder coating is not strictly classified as e-coating, it shares similarities with electrostatic spray deposition techniques because it relies on electrostatic forces to apply dry powder coatings onto substrates.
Typically consisting of thermosetting polymers or thermoplastic powders, powder coatings provide thicker films ranging from approximately 2 to 10 mils (50 - 250 microns), making them ideal for heavy-duty applications and environments.
Immersion Coating
Immersion coating, flooding, or cascading involves submerging an object into a tank containing the e-coat solution. The thickness achieved through immersion coating varies depending on factors such as dwell time and the viscosity of the coating solution.
Typically, immersion coatings result in thicker films ranging from 2 to 8 mils (50 - 200 microns) and are commonly used in large-scale industrial applications. The selection of a specific method for e-coating depends on factors such as part size, complexity, performance requirements, and cost considerations.
By understanding the varying thickness ranges associated with different techniques, manufacturers make informed decisions to ensure optimal results in terms of both aesthetics and protective properties. It is important to note that these thickness ranges are approximate values and may vary depending on specific process parameters and product specifications.
Coating thickness is a critical parameter in determining the effectiveness of the e-coating processes. Dip coating typically achieves a range of 0.5 to 2 mils (12 - 50 microns), while spray coatings achieve approximately 1 to 4 mils (25 -100 microns).
Electrostatic spray techniques yield consistent film thicknesses within the same range. Powder coatings offer thicker films ranging from around 2 to 10 mils (50 -250 microns).
Immersion coating produces thicker films ranging between approximately 2 to 8 mils (50-200 microns). Understanding these variations enables manufacturers to select the most suitable method for their specific application requirements while ensuring adequate protection and desired aesthetic effects.
Comparing E-Coating with Other Methods
With protective coatings, there are various methods available in the industry. Each method has its own merits and limitations.
Powder coating involves applying a dry powder onto the substrate's surface and curing it in an oven. While both methods provide excellent corrosion protection, there are distinct differences.
E-coating offers superior coverage and uniform film thickness, ensuring even protection in complex geometries or hard-to-reach areas. Powder coating may cause uneven coverage because of Faraday cage effects or difficulties in achieving appropriate film thickness on intricate parts.
Another prevalent method is liquid spray painting. While spray painting offers versatility in color options and finishes, it often falls short compared to e-coating regarding corrosion resistance.
The electrochemical process of e-coating ensures that all substrate areas receive an even coating thickness, reducing the risk of premature failure because of corrosion spots or thinning.
Galvanizing
Galvanizing is a popular corrosion protection technique used primarily for metal substrates such as steel structures or components.
Galvanizing involves immersing the substrate into molten zinc or applying a zinc-rich paint system through spraying or brushing. Although galvanizing provides excellent long-term protection for harsh environments, it is limited by its thickness and coverage uniformity on complex shapes compared to e-coating.
Anodizing
Besides these methods, anodizing is commonly employed for aluminum surfaces, where a protective oxide layer is formed through electrolytic processes. While anodizing offers good corrosion resistance for aluminum components, it may not be suitable for other metals or substrates like steel that require robust protection against rust formation.
Although electroplating shares some similarities with e-coating, it is primarily used for decorative purposes and does not provide the same level of corrosion resistance. E-coating surpasses electroplating to provide a uniform coating thickness across complex parts, offering better substrate adhesion.
While various coating methods are available in the industry, e-coating distinguishes itself through its exceptional coverage, uniform film thickness, and superior corrosion protection. Compared to alternatives such as powder coating, liquid spray painting, galvanizing, anodizing, or electroplating, e-coating is a top choice for industries requiring high-quality, long-lasting protective coatings.
Coating Efficiency
Efficiency is a key consideration when evaluating any coating method, and e-coating has proven highly efficient in many applications.
One of the primary factors contributing to its efficiency is achieving a uniform coating thickness in complex shapes. Unlike traditional methods like painting, where manual application leads to uneven coverage, e-coating employs an automated process that ensures consistent and uniform coating distribution over the entire surface.
E-coating boasts impressive material utilization rates. The electrostatic deposition process used in e-coating allows for a high transfer efficiency of the coating material onto the substrate.
This transfer efficiency means minimal waste occurs during application, resulting in cost savings and reduced environmental impact. Since e-coating forms a thin layer on the substrate's surface, less paint is required than other coating methods, such as powder or wet painting.
Advantages
In terms of operational efficiency, e-coating offers several advantages over conventional methods. The automated nature of the process reduces labor requirements significantly.
Safety
Once set up properly, it operates continuously with minimal human intervention. E-coating uses water-based formulations that eliminate many health risks associated with solvent-based coatings.
This reduction contributes to improved worker safety by reducing exposure to harmful chemicals. Another aspect of efficiency relates to curing time and energy consumption.
Increased Throughput
E-coatings are typically cured through baking or using infrared technology after deposition. Compared to alternative methods that require longer curing times at high temperatures or lengthy air-drying periods for solvent-based coatings, e-coatings have shorter cure times.
Short cure times increase throughput and reduce energy consumption during production. Regarding overall cost-efficiency, while initial investment costs for establishing an e-coat line may be higher than traditional painting equipment setup costs (because of specialized tanks and rectifiers), long-term savings are significant because of lower material usage rates and reduced labor requirements.
Environmentally Friendly
With advancements in technology and the availability of more environmentally friendly materials, the cost of e-coating has become even more competitive, making it an attractive option for many industries. The efficiency of e-coating is clear in various aspects.
Its ability to achieve uniform coating thickness in complex shapes, high material utilization rates, reduced labor requirements, shorter curing times, and long-term cost savings makes it an efficient choice for many applications. As industries strive for greater efficiency in their processes while maintaining high-quality standards, e-coating continues to prove its value as an efficient and effective coating method.
E-Coating Applications
E-coating, also known as electrodeposition or electrocoating, has gained significant popularity because of its versatility and effectiveness in various industries.
Automotive Industry
One of the most prominent sectors benefiting from Eco-coating is the automotive industry. Using e-coating in this field ensures exceptional corrosion resistance and durability for many automotive components, including chassis frames, suspension parts, brake systems, and exhaust systems.
The uniform deposition e-coating enhances these critical components' overall performance and lifespan.
Electronics Industry
Reliable protective coatings are essential in the electronics industry, where delicate electronic components are exposed to moisture and other contaminants. E-coating offers excellent adhesion properties when applied to printed circuit boards (PCBs), ensuring long-lasting protection against environmental factors such as humidity and chemical exposure.
Because of its thin-film nature, it does not interfere with electrical conductivity or signal transmission.
Aerospace Industry
The aerospace industry requires high-performance coatings that withstand extreme environmental conditions and provide excellent protection against corrosion and wear. E-coating meets these requirements, making it an ideal choice for aerospace applications, such as landing gear assemblies, engine components, hydraulic fittings, and structural elements.
Its ability to coat complex shapes uniformly allows for enhanced protection even in hard-to-reach areas.
Agricultural Equipment
Farm equipment faces harsh environments with exposure to corrosive substances such as fertilizers and chemicals while enduring extreme weather.
E-coating provides a durable and protective coating on agricultural machinery, such as tractors, harvesters, plows, and implements. This extra step ensures extended equipment lifespan and reduces maintenance costs to combat these challenges effectively.
Appliance Industry
In the appliance industry, e-coating is widely used for coating components in household appliances like refrigerators, washing machines, dishwashers, and ovens.
The E-coat protects against moisture, chemicals, and physical wear while offering an aesthetically pleasing finish. E-coating's versatility enables it to be applied in many other industries, such as medical equipment manufacturing, marine industry (boat components), electrical enclosures, construction materials (fencing), and many more.
Furniture Manufacturing
E-coating has found a place in furniture manufacturing because of its ability to simultaneously provide decorative finishes and corrosion resistance. It is commonly used for coating metal furniture frames like chairs, tables, bed frames, etc., providing a smooth finish that is further enhanced with additional topcoats or powder coatings.
The ability to accommodate various substrates, like steel, aluminum alloys, and zinc die-castings, further expands its application possibilities. The reliability of e-coating in providing uniform coatings with superior corrosion resistance has made it a preferred choice across multiple industries.
Its ability to protect intricate parts or surfaces that are difficult to reach with traditional coating methods gives it a distinct advantage over alternative options. As technology advances and new formulations emerge, the application range for e-coating is likely to expand even further.
E-Coating vs. Painting Tradeoffs
Several factors come into play when considering the tradeoffs between e-coating and traditional painting methods. Both processes have strengths and weaknesses; understanding these tradeoffs is crucial to making an informed decision. One of the primary advantages of e-coating over painting is its superior corrosion resistance.
E-coating provides a uniform coating that covers every nook and cranny of the object being coated, including recessed areas and corners. The uniform coverage ensures comprehensive protection against rust and other forms of corrosion.
In contrast, traditional painting may leave certain areas vulnerable to corrosion because of uneven coverage or inadequate film thickness. Another important tradeoff is durability.
Durability
E-coating offers exceptional durability because of its robust adhesion properties. The electrically charged particles during the e-coating process adhere firmly to the metal substrate, creating a strong bond that withstands harsh environments, weathering, and abrasion.
Painted surfaces may be more prone to chipping, peeling, or scratching. Regarding environmental impact, e-coating is more environmentally friendly than traditional painting methods.
VOCs
Many e-coat formulations are water-based and contain lower volatile organic compounds (VOCs) levels than solvent-based paints. This method reduces air pollution during application and lowers health risks for workers involved in the coating process.
Cost-Effective
In terms of cost-effectiveness, e-coating offers advantages over painting as well. While initial setup costs for an e-coat system may be higher than conventional spray-painting equipment, e-coat systems generally have higher transfer efficiency rates, significantly reducing material waste.
Coverage
Improved coverage capabilities mean less coating material is required overall than traditional spraying methods. However, there are some limitations associated with e-coating that should be considered as well.
For instance, because of uneven film thickness, intricate parts with sharp edges or complex geometries pose challenges during the e-coat process. These challenges may require additional masking or adjustments to accommodate such complexities.
In contrast, painting methods are more flexible and adaptable to various part shapes and sizes. E-coating and traditional painting methods each have their tradeoffs to consider.
Corrosion Resistance
E-coating excels in corrosion resistance, durability, environmental impact, and long-term cost-effectiveness. However, it may have limitations with complex part geometries.
Traditional painting methods offer greater flexibility but may not match the protection and durability of e-coating. Ultimately, choosing these methods depends on the application's requirements, considering factors such as part design complexity, desired aesthetics, environmental considerations, and budget constraints.
In Sum
E-coating is a highly effective and versatile method of coating various materials, providing exceptional corrosion resistance and durability. It has proven reliable for many manufacturers seeking long-lasting and visually appealing finishes. One of the key advantages of e-coating is its ability to provide uniform coverage on complex shapes and hard-to-reach areas.
Such coverage makes it ideal for coating automotive parts, appliances, and even intricate metal components used in aerospace applications. Achieving consistent coating thicknesses gives manufacturers greater control over product quality while minimizing material waste.
When comparing e-coating with other coating methods, such as painting or powder coating, e-coating offers unique advantages. While painting may provide a wider range of color options, it often falls short regarding corrosion resistance and durability.
Powder coating is limited by its inability to coat recessed areas effectively. In contrast, e-coating excels in both aspects by providing excellent coverage and superior corrosion protection.
The production volumes by industry showcase the widespread adoption of e-coating across various sectors, such as automotive manufacturing, electronics, and agriculture equipment production. With so many industries using e-coats, it shows a growing recognition among manufacturers of the benefits offered by this technology to enhance product performance while meeting stringent industry standards.
In an era where sustainability is gaining prominence in manufacturing, e-coating is an environmentally friendly option. Its water-based composition and low VOC emissions compared to traditional solvent-based coatings or paint systems align well with green initiatives to reduce environmental impact without compromising quality.
Despite being relatively less known than other coating methods like painting or powder coating, e-coating has proven to be a highly effective and efficient solution for achieving durable, corrosion-resistant finishes. Its versatility, ability to coat complex shapes, and excellent coverage make it an ideal choice for various industries.
With its environmental advantages and potential for cost savings through increased efficiency, the future of e-coating is promising. Manufacturers who embrace this technology confidently protect their products while contributing positively to sustainability efforts in the industry.