The definition of price lays it out nicely: “that which must be given, done, or undergone to obtain a thing. "
Wonderful home-cooked meal? The price includes buying the ingredients and our time and effort in the kitchen.
There are myriad examples to use, but I’d like to focus on the price of beautiful architecture along a picturesque coastline for this article. After all the dust settles on construction, a price that’s sometimes neglected is the battle between the metal in the structures and the corrosive environment caused by the sea.
The bane of any metal fabricator, whether it’s an artist or company, is rust. We’ve talked about rust in a previous article. We’re narrowing the focus in this article to the corrosive effects of the atmosphere.
What is Corrosion?
Corrosion results from a chemical reaction breaking down the composition of a material, typically metal. Corrosionpedia breaks it down further (pun intended):
Corrosion of metals and nonmetals occurs due to the gradual environmental interaction on the material surface. The structures and facilities of different materials are affected by this interaction. Even the ambient air, laden with moisture and oxygen, can start this process, known as rusting, on steel surfaces.
Any metal, if it’s not protected, rusts. In our next article, we’ll look at a few ways of protecting metal substrates.
Corrosion Causes
Corrosion has many causes, natural and artificial. This list isn’t complete, but it illustrates just how varied the causes are.
- Salt-saturated air and salt spray from oceans
- High humidity
- Condensation caused by morning dew
- Sunlight
- Temperature variations
- Fungus, bacteria, microbes, plant sap, and mildew
- Dust, hail, lightning, gravel impact, abrasion, and high-pressure spray
- Poor surface preparation
- Bad maintenance
- Road salt
- Vehicle exhaust
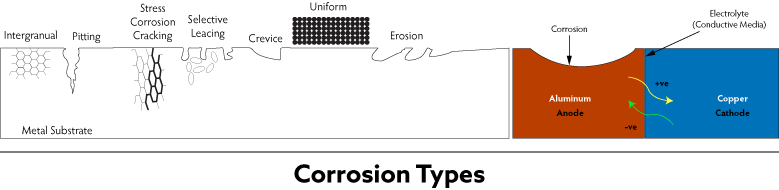
Corrosion Types
No types of corrosion are equal, and each type results from complex chemical reactions started by different mechanisms dependent on the surrounding environment.
There are eight types of metal corrosion.
Crevice Corrosion
Crevice corrosion occurs where oxygen can’t circulate in areas such as fastener heads, tight joints, and other locations where various pieces of metal are in close contact.
Salts, moisture, and pollution combine and accumulate in the crevice, leading the metal to break down.
Erosion Corrosion
Erosion corrosion describes the effect a corrosive fluid has on a metal surface. The erosion rate depends on turbulence within the fluid’s current, and the more turbulent the liquid, the more corrosive it becomes.
Soft alloys, such as aluminum, lead alloys, and copper, are also easy pickings for erosion.
The type of corrosion is most common in construction areas with blockages, pump impellers, inlet ends, and other areas with high flow rates.
Galvanic/Bimetallic Corrosion
Galvanic is perhaps the most common kind of corrosion and the most preventable. Bimetallic corrosion occurs when two different metals are submerged in a conductive solution and are connected electrically.
When the galvanic couple forms, one metal becomes the anode, which causes it to rust at a much faster rate. Meanwhile, the other metal becomes the cathode and corrodes slower.
Intergranular Corrosion
Intergranular corrosion is an attack near the grain boundaries of metals and alloys at a microscopic level.
These metals are composed of crystalline structures, meaning grains of different sizes. Grain boundaries are where those grains meet, and Intergranular corrosion goes after those boundaries, creating damage at the molecular level. Eventually, if not discovered, the damage reduces structural integrity, but with little or no visual indications of trouble.
Pitting/Filiform Corrosion
Pitting or filiform corrosion is very localized corrosion where cavities are produced in the metal. This type of corrosion is tough to find, predict, and design against.
A weak point created by damaged protective coatings is a common area to find pitting damage.
Selective Leaching
Selective leaching occurs when an element is removed from an alloy by corrosion. Probably the most common example of selective leaching is the dezincification of brass. Zinc is selectively leached from a copper-zinc brass alloy, resulting in a weakened porous copper structure.
Stress Corrosion Cracking
The combination of tensile stresses, vulnerable metal, and a corrosive environment caused stress corrosion cracking. Metallurgy For Dummies explains in better detail:
Cold deformation and forming, welding, heat treatment, machining, and grinding can introduce residual stresses. The magnitude and importance of such stresses are often underestimated. The residual stresses are set up because welding operations approach the yield strength. The build-up of corrosion products in confined spaces can also generate significant stresses and should not be overlooked. SCC usually occurs in certain specific alloy-environment-stress combinations.
Uniform Corrosion
Uniform corrosion is the most common corrosion type occurring when the entire surface of a metal is attacked simultaneously and with equal intensity. One of the best illustrations would be steel moorings on seaside docks.
Best Places to Find Corrosion
If you’re looking for places with high corrosion incidents, consider the eastern seaboard and the gulf coast, especially Florida. The amount of humidity, salt, wind, and heat are prime ingredients for corrosion.
An area from 1,500 feet to a mile inland defines a seacoast. After one mile, the concentration of salt decreases, and wind moves that sea air up to several hundred miles inland despite the drop.
Interestingly, buildings on the west coast of the United States aren’t as affected by corrosive air because the air is dry. For example, for filiform corrosion to damage metal, humidity needs to be higher than 40%.
At the opposite end of the weather, spectrum is the northeastern portion of the country. What the area lacks in humidity makes up with high usage of road salts. The tall buildings in larger cities create a wind tunnel effect. This effect carries the road salt to elevations as high as 20 stories from the ground!
In Sum
The price of outstanding architectural designs near an ocean needs to be determined early in the development stages. Disregarding environmental factors is a costly and perhaps catastrophic mistake by ignoring corrosion.
What solutions would work? I’m happy you asked! In an upcoming article, we’ll explore ways of combatting corrosion.