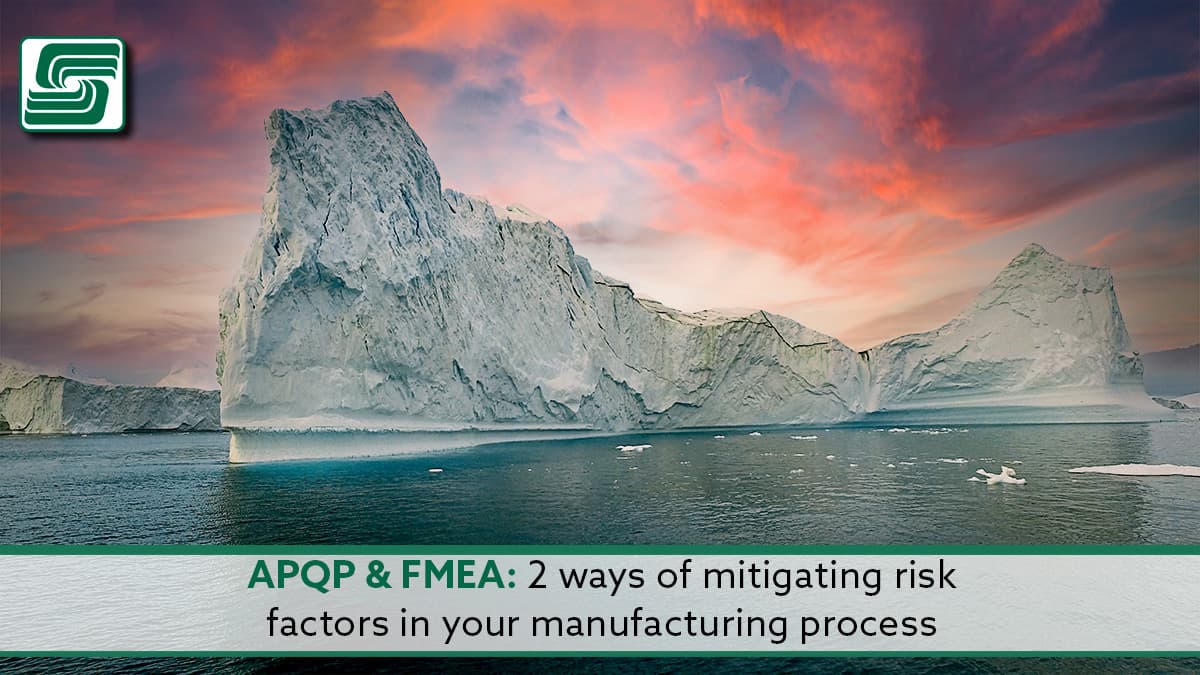
As is usually the case, Benjamin Franklin was right. In this case, his famous quote, "If you fail to plan, you are planning to fail," accurately summarizes mechanical designs.
Manufacturers that don't assume failure in their design process soon become ex-manufacturers. Taken a step further, a manufacturer implementing a risk mitigation process becomes a success, provided, of course, they correct the failures caught before they begin producing components.
Risk mitigation identifies and reduces risks during product development's design and engineering stages. Failure to identify or manage risks resulting in production disruptions, product recalls, and unplanned inventory write-offs.
Risk management is a broad term referring to strategies for dealing with potential problems before they happen. Risk management involves:
- Identifying and analyzing potential hazards.
- Determining their probability of occurring and their potential impact.
- Implementing measures to reduce the risks.
- Monitoring indicators to check whether these measures are effective.
- Adjusting risk management strategies if necessary.
A Process Quality Program (APQP) helps mitigate the risk of manufacturing problems before they occur. At the same time, Failure Mode and Effects Analysis (FMEA) is a great technique for identifying potential failure points during a new product design phase. Look at this overview to learn more about APQP and FMEA risk mitigation tools.
What is APQP?
APQP is the acronym for the eight-step process of product quality planning. In a nutshell, this process identifies the potential failure points of a new product, starts corrective actions, and verifies that such actions are effective. The APQP process is a fundamental component of a process quality program (PQP).
In an APQP process, a team examines the product, manufacturing process, and the suppliers who provide materials for the product. The team also thoroughly reviews design drawings and specifications, identifying potential quality issues. Once the team collects this information, they take corrective actions to mitigate risks and help ensure a successful product launch.
PPAP—A Critical Piece
In manufacturing, the process is just as important as the final product. Without a structured and documented production process, it's difficult to operate efficiently while producing high-quality products. The production part approval process (PPAP) is a standard documentation method that streamlines production processes and improves efficiency.
What is a PPAP?
PPAP stands for Production Part Approval Process. It is a standard documentation method that streamlines production processes and improves efficiency. PPAP is a document that outlines the approval process for all parts that go into a finished product, from sourcing raw materials to shipping finished goods.
In manufacturing, PPAP helps streamline a production process and improves quality. PPAP is important because it improves the efficiency of your production team and reduces the risk of errors occurring in the materials used to make the products you sell.
When properly documenting the materials used in a product production process and approved, there is less chance that a supplier will provide incorrect or substandard materials because all suppliers are required to follow the same documentation process and meet the same quality standards outlined in the PPAP document.
Why Is PPAP Important?
A production part approval process is important to any manufacturer's standard operating procedures. It provides a standardized way of approving the parts that go into each product and assures that the materials used to meet certain quality and quantity requirements.
PPAP helps minimize errors, improve traceability and reduce costs for manufacturers. These benefits extend to production scheduling and customer service as well. By following a PPAP documentation process, manufacturers better track their parts, from raw materials to finished products, improving efficiency because it is easier to identify which parts need rework or correction. It also helps keep customers happy by reducing the risk of shortages or late deliveries.
How Does PPAP Help?
PPAP helps manufacturers by streamlining production processes and improving quality.
Production Processes
Standardizing the production part approval process and approving raw materials selections. Manufacturers should use this process for all production materials, including steel, plastics, fabrics, adhesives, and other materials that make finished products. This documentation helps eliminate errors, improve traceability and reduce costs for manufacturers.
Quality
A production part approval process helps manufacturers ensure that the parts they use meet certain quality standards. This is important because it reduces the risk of using defective or substandard parts.
What is FMEA?
FMEA stands for Failure Mode and Effects Analysis. It's a risk management tool helping identify potential failure points and devise solutions to prevent them from occurring, completed at any stage of the product development process, including in the design phase, the prototype phase, or even during the pilot phase of production.
There are three crucial steps to the FMEA process:
- Identify likely failure points by brainstorming potential weaknesses.
- Estimate the severity of such failures (both in terms of how much damage the frequency of failures), and
- Determine potential solutions for these failure points or measures to minimize their impact.
How APQP Risk Management Differs
APQP is one of the most widely used Risk Management techniques, and it's also used the most often in connection with Six Sigma quality initiatives. Many organizations have their version of the APQP process or an APQP checklist, and the specificity of this process often varies between organizations. However, the overall goal of APQP is the same, no matter which organization uses it.
The major difference between APQP and other risk management techniques is that it provides a structured way of identifying and solving potential quality issues at all stages of a product development process. It's used at the initial stage of a product's development and during each subsequent stage. In contrast, people often use other risk management techniques at just one stage.
FMEA Pros and Cons
The chief advantage of an FMEA is that we can use it as early as the design stage before applying other risk management tools. Another advantage of FMEA is using at any stage of the product development process.
The major disadvantage of FMEA is that it's a relatively time-consuming procedure. In addition, many organizations have their version of FMEA, meaning the FMEA process may differ for different companies.
In Sum
As you can see, APQP and FMEA are great risk management tools. You can use them to identify potential failure points in the product design phase, as well as in the production phase. Doing so can help you mitigate the risk of manufacturing problems before they occur, as well as mitigate the risk of unplanned production downtime if they occur.
Like Ben wrote back in 1735, "Look before, or you'll find yourself behind."