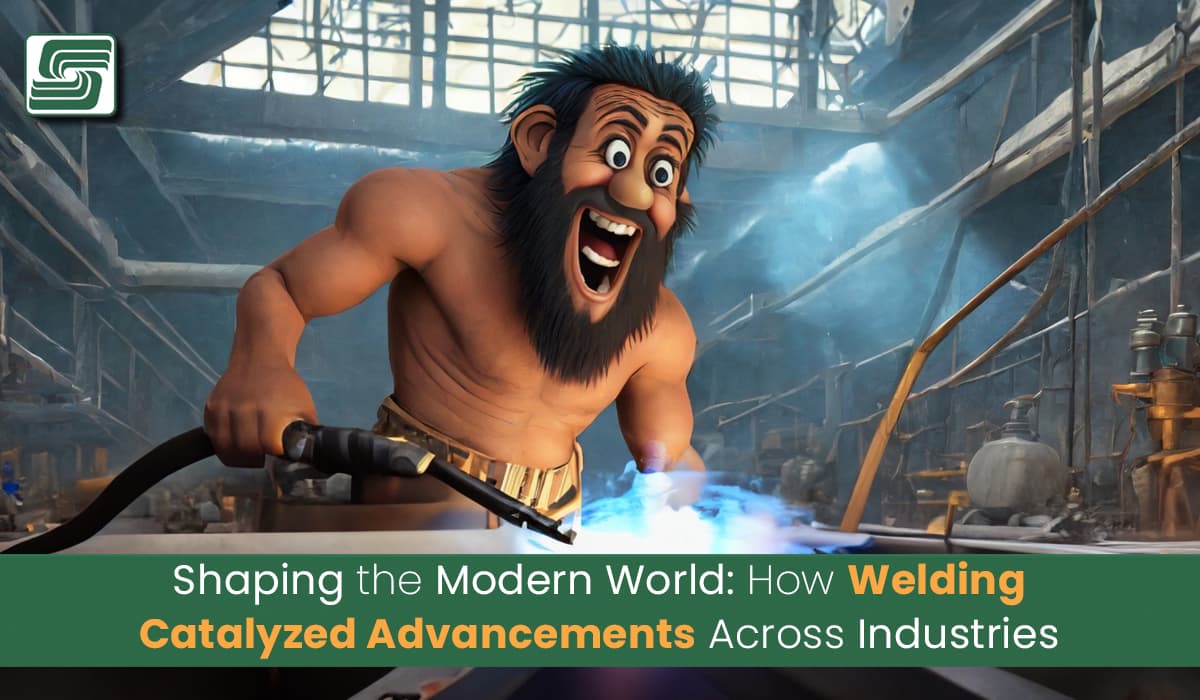
Second in a 2-Part Series
This two-part article explores the rich history and ongoing evolution of welding technology. Part 1 provides a comprehensive perspective on how this integral fabrication process has transformed human civilization by tracing its origins, pivotal milestones, and development.
Introduction
From the inception of civilization, human progress has hinged on our ability to manipulate materials. One craft that has enabled this capability, elevating societies across millennia, is welding - fusing metals. This seemingly simple act has empowered humanity's aspirations, allowing us to construct monumental and intricate creations that steer the direction of history.
Welding conjures visions of ubiquitous industrial environments today. However, its origin traces back to the most primal human urge to build and create. Through determined perseverance and resourcefulness, we have refined this craft across centuries, overcoming limitations at each juncture to arrive at the advanced welding technologies of the modern era.
The evolution of welding has been prolonged and captivating, marked by incremental breakthroughs that have profoundly impacted industry and society. In this two-part article, we will traverse the rich history of this technology to appreciate not just the milestones it represents but also the silent ways in which it has and continues to shape our world.
Welding technology, an indispensable part of technological evolution, has witnessed a monumental transformation since its inception. Pioneering the fabrication and construction industry, it has been the backbone of myriad developments over centuries. From the construction of colossal architectural wonders to the minute intricacies of delicate artifacts, welding technology's contribution remains unparalleled.
The genesis of welding conjures images of blacksmiths fusing iron and steel, using open fires in antiquity. However, modern welding technology traces its roots back only around 200 years, a fleeting moment compared to human history's vast expanse. From then till now, it has evolved continually to adapt to civilization's unending demands.
Today's innovative techniques have revolutionized manufacturing processes across industries like automobile manufacturing, aerospace engineering, shipbuilding, pipeline fabrication, and more. In this comprehensive exploration into the world of welding technology, we will not only traverse through its illustrious timeline but also cast light on how it continues to shape our lives today—often unnoticed but always appreciated upon reflection.
Evolution of Welding Technology
The fascinating journey of welding technology began as early as the Bronze Age when our ancient ancestors began the practice of forge welding. This rudimentary procedure entailed heating metals until they were malleable before hammering them together to create a unified piece. It was a labor-intensive task requiring not only physical strength but also a skilled hand and eye to ensure successful fusion.
This method was used prolifically in creating weapons, tools, and even artworks that are now invaluable historical artifacts. Despite its primitive nature, forge welding was integral to technological advancement.
It enabled societies to make significant leaps in infrastructure and cultural development, revealing the transformative power of welding technology even in its infancy. The process remained unchanged for centuries until the Industrial Revolution.
During this era, groundbreaking innovations heralded an unprecedented change in many areas, including welding. With the onset of the 19th century, oxyfuel welding emerged as a revelation in industrial operations.
This technique involved burning a gas (usually acetylene) with pure oxygen to produce a fiery flame to melt metal pieces and join them in one cohesive unit. Compared with their forge-welding predecessors, oxyfuel welders had greater control over their work due to better heat regulation capabilities provided by adjustable torches.
They could also work faster and more efficiently than before—an essential requirement in an age where mass production has become increasingly prevalent. A more profound evolution occurred during the late nineteenth and early twentieth centuries with arc welding's invention—considered one of modern metallurgy's marvels.
In this advanced method, an electric current passed through an electrode to generate an intense heat source that could melt metal surfaces instantaneously upon contact, creating molten pools that solidify into robust joints after cooling down. Arc welding brought about revolutionary changes: it not only dramatically improved productivity rates but also changed our worldview on construction possibilities—bridges grew longer, skyscrapers soared higher, and ships became more formidable.
Arc welding was the catalyst that propelled us into the modern architectural age. Each stage in welding technology's evolution has been a testament to human ingenuity and adaptability.
We have continuously refined our methods, from rudimentary hammering techniques to precision-controlled lasers and electron beam welding. This relentless drive for improvement reflects our innate desire to shape our environment according to our needs and aspirations—a trait embodied by the transformative power of welding technology.
The evolution of welding technology has been a captivating journey marked by incremental improvements that have radically altered its landscape over millennia. From its humble beginnings in primitive forges to the sophisticated techniques employed today, each stage represents a milestone in industrial development—a testament to human ingenuity and the integral role of this versatile craft in society's fabric.
History of Welding
The history of welding is an intricate tapestry woven through countless eras in human civilization. Its origins can be traced back to the Bronze Age when pressure welding lap joints together made small gold circular boxes. This practice evolved during the Iron Age, as blacksmiths started to heat and hammer metal pieces together, employing a technique known as forge welding.
Forge welding was the dominant method employed throughout much of our ancient history. It involved heating two pieces of metal to a high temperature and hammering them together.
The heat, combined with the mechanical force, caused the metal pieces to bond at a molecular level, facilitating the creation of various tools and weapons. However, this method was limited; it required immense physical effort and couldn't weld large or complex structures.
Subsequent technological advancements in the 19th century precipitated monumental shifts in welding practices. The rise of gas-powered tools created better-controlled heating processes, birthing oxyfuel welding.
This approach used pure oxygen to increase combustion efficiency in a fuel gas flame, enabling higher working temperatures, which expanded possibilities for manipulating hard metals like steel. However, it wasn't until mankind entered an era marked by electrification that modern forms of welding began their ascent.
Arc welding emerged as a beacon amidst this industrial revolution in the late 1800s and early 1900s. By generating an electric arc between an electrode and base material, this technique achieved temperatures sufficient to melt most metals.
Arc welding facilitated greater control over procedures while delivering superior strength in welded joints. In contrast with former methods requiring laborious physical endurance or combusted gases, arc-based procedures used electrical energy for fusing materials - proving significantly more efficient and versatile.
As technology advanced further within this genre during the mid-20th century, we saw the development of more specialized forms, such as Metal Inert Gas (MIG) and Tungsten Inert Gas (TIG) welding processes, which revolutionized industries from automotive manufacturing to aerospace. In the late 20th century, mankind was yet again on the brink of a technological revolution—this time in precision and automation.
Laser and electron beam welding were introduced as highly accurate, clean, and efficient joining materials. These processes used concentrated high-energy beams to melt and fuse materials at precise locations with minimal distortion or contamination.
Through each epoch of human civilization, welding technology has evolved with our understanding of the universe. From heating pieces over fire pits to controlling concentrated energy beams with computers, welding has been a testament to humanity's ceaseless pursuit of progress.
Forge Welding
In its most rudimentary form, welding traces its origins back to the Bronze Age, when metals were joined through the forge welding process. This primitive technique entailed heating two metal pieces until they reached an incandescent state, followed by forcefully hammering them together to merge the bond. A flux layer facilitated the amalgamation - typically from sand or borax - which shielded the welded area from impurities in the surrounding atmosphere.
Forge welding bore significance because of its historical inception and because it laid down the foundational principles for modern welding processes. It showcased an understanding of heat and pressure as essential components for successful bonding, a concept further developed and refined over subsequent centuries.
It showed that different metals could be fused with proper equipment and technique—a revelation that led to several applications, from blacksmithing to shipbuilding. However, this old-fashioned method also had its share of flaws, which impeded consistent weld quality.
The operation required high skill and finesse for maintaining precise temperature control and hammering competency—variables difficult to standardize across different artisans. Also, unlike modern techniques like arc or gas welding, where filler material can be added if needed, forge welding relies solely on existing parent metal for forming joints with no potential for fillers.
Despite these limitations and its nearly obsolete status today, forge welding undeniably shaped human civilization's ability to manipulate materials according to their needs. From swords in feudal times to horseshoes in agricultural societies, this age-old craft has bonded not just metals but cultures over time and space—giving birth eventually to more advanced forms of fusion technology we see around us today.
MIG/TIG Welding
In the vibrant tapestry of welding's illustrious history, two techniques stand out prominently because of their profound impact on industry and craftsmanship: Metal Inert Gas (MIG) and Tungsten Inert Gas (TIG) welding. These two methods, developed in the mid-20th century, transformed the field of welding with their novel use of inert gases to shield and protect molten metal from atmospheric contamination.
MIG welding, also known as Gas Metal Arc Welding (GMAW), was introduced during the Second World War as a rapid means of constructing military equipment. The technique uses a continuous solid wire electrode fed through a welding gun into the weld pool, merging the base material with the melting wire.
Simultaneously, an externally supplied gas shields the weld area from airborne contaminants. MIG's inherent speed and efficiency made it an ideal process for assembly lines churning out war material on an unprecedented scale.
Over time, it found favor in various sectors, such as automobile manufacturing, construction, and repair, because of its versatility and ease of use. TIG welding, or Gas Tungsten Arc Welding (GTAW), is another revolutionary development that emerged.
This technique employs a non-consumable tungsten electrode that delivers current to the welding arc while a protective envelope of inert gas shields against oxidation or other atmospheric contamination. Unlike MIG welding, which uses filler metal directly supplied by a wire feeding mechanism, TIG may be used with no filler if required - marking a fundamental difference between these two techniques.
TIG is recognized for its precision and high-quality finishes, which make it suitable for intricate tasks in aerospace fabrication, piping systems, or sculptural work where aesthetic appeal is critical. Both MIG/Tungsten have not only shaped but continue to contribute significantly towards advancements in the fabrication industry owing to their unique capabilities and adaptability across different applications.
Laser & Electron Beam Welding
Laser welding in the industrial sector became a paradigm shift. Laser welding, primarily known for its precision, was first introduced in the 1960s. The process involves generating a highly concentrated light beam that melts and fuses materials.
The energy density of the laser beam is colossal and penetrates deep into the workpiece, thus producing a narrow, deep weld with minimal heat-affected zones. This technology transformed how industries approach intricate operations requiring meticulous precision.
For instance, in the automotive industry, its applications range from seam welding of tailored blanks to spot welding in component assembly. Similarly, in medical device inventions and improvements where millimeter precision is paramount, such as pacemakers or hearing device production, laser welding has been monumental.
It offers flexibility: it can be operated under normal atmospheric conditions or underwater; it works on dissimilar and refractory materials to reach areas otherwise difficult to reach by conventional methods. However potent laser technology may be for industrial purposes, electron beam welding emerged as an equally formidable player across manufacturing sectors.
Electron beam (EB) welding was developed during the World War II era but only came to prominence around 1958 when its commercial viability was realized by industries globally. This process operates on scientific principles whereby a high-velocity stream of electrons directed towards the workpiece generates intense heat, causing localized melting and fusion of material.
EB welding's core strength lies in its ability to provide superior weld quality with exceptional depth-to-width ratio—leading to narrower yet deeper weld seams, which ultimately translates into stronger joints than any other fusion method. This attribute made EB welding attractive for high-integrity applications like nuclear power generation equipment manufacturing or aerospace component fabrication, where both safety standards demand robust joint integrity.
Unlike most other processes operating under normal atmospheric conditions, EB welding happens inside vacuum chambers, eliminating common issues such as oxidation or contamination by atmospheric gases. It offers unparalleled cleanliness and purity to the weld, making it highly desirable for applications requiring the highest precision and purity, such as in semiconductors or the photonics industry.
The evolution from conventional welding methods to laser and electron beam technology is seen as a major leap in welding technology. Their specific strengths have enabled industries across domains to expand their horizons further into new territories that would otherwise remain untouched by more traditional methods.
Emergence of Friction Stir Welding
Friction Stir Welding (FSW) was a revolutionary breakthrough that marked a significant inflection point in the evolution of welding technology. It saw the light of day in 1991, courtesy of The Welding Institute (TWI) in the UK. Unlike traditional fusion welding processes that relied on heat generation to melt and join materials, FSW introduced an entirely new concept.
The process involved using a non-consumable rotating tool that mechanically intermixes two workpieces' materials, creating a solid-state joint without reaching a melting point. The inception of Friction Stir Welding was stimulated by demands from high-tech industries for superior weld quality, especially in aluminum alloys, which presented considerable challenges with conventional techniques.
FSW offered improved mechanical and thermal properties because of its solid-state nature. The technique also minimized common defects associated with fusion welding techniques, such as porosity, cracking, and distortion; it opened up new possibilities for industrial applications ranging from aerospace to automotive manufacturing.
However, like any pioneering technology, Friction Stir Welding wasn't without its challenges initially. Its adoption caused fresh approaches toward equipment design and required unique skill sets for operation.
Early-stage resistance was encountered because of the need for significant investment in those areas and fears regarding patent restrictions hindering mass acceptance; perseverance paid off over time, as evidenced by its ubiquitous usage now across various industries. The transformative journey embarked upon by Friction Stir Welding is an eloquent testimony of how innovation pushes boundaries within established norms.
From being initially developed as a niche technique specifically targeting aluminum alloy welded components, it has grown into a universally accepted method of finding applications with diverse engineering materials, including steels, titanium, polymers, and even composites. Today's innovative high-speed trains, fuel-efficient automobiles, or next-generation space vehicles owe their existence partly to FSW's emergence on the metal joining scene some three decades ago.
When Was Friction Stir Welding Invented?
The emergence of friction stir welding marked a monumental shift in the welding domain, a revolutionary technique conceived as recently as 1991. The Welding Institute (TWI), a distinguished body in the United Kingdom, brought this innovative method to life. The conception of this technique ushered in an era of advanced physical joining processes and firmly established the 20th century as a golden age of engineering advancements.
Interestingly, friction stir welding was initially developed to address challenges encountered in industries where conventional fusion welding methods were insufficient. These sectors included aerospace, marine, and automotive manufacturing, where aluminum alloys were extensively used.
Because of their high thermal conductivity and relatively low melting point, these alloys posed significant drawbacks when used with standard fusion welding techniques. As a result, TWI's ingenious invention offered an effective solution to these hurdles by providing an alternative method that didn't rely on the conventional principles of melting and solidification.
Friction stir welding emerged from its inventors' desire for purity: its name derived from its unique process, which involves spinning a non-consumable tool into two tightly butted metal workpieces. The friction between the rotating tool and workpiece materials generates heat sufficient to soften but not melt them.
This softened material is "stirred" together by the tool's mechanical action, creating a joint free from common defects associated with fusion-based techniques. This process represented an extraordinary departure from traditional methods and heralded friction stir welding's arrival onto the global manufacturing stage.
In Sum
The transformational welding journey has been an enthralling testimony of human ingenuity, overcoming challenges through perseverance. From rudimentary beginnings in primitive forges to electron beams transmitting concentrated energy with absolute precision, each breakthrough has elevated fabrication possibilities to unprecedented heights.
Welding will continue its perpetual evolution, driven by demands for materials joining industries old and new. However, its history provides invaluable perspective, illuminating how far progressive thinking can stretch what is achievable. The technologically advanced world we inhabit today is indebted hugely to the advent of modern welding practices.
By understanding this heritage, we can appreciate the incremental leaps of progress that collectively amount to giant strides when viewed through the lens of time. The brilliance of welding technology lies in its functionality and the innovative spirit it has kindled and preserved across generations. If this spirit persists, we can expect welding to unlock new frontiers in manufacturing, fostering a future rich with possibilities.
In Part 1, we uncovered welding's origins during antiquity and its persevering refinement across centuries, overcoming limitations to arrive at today's cutting-edge techniques. In the next installment, we will discover how these modern technologies have elevated welding to unprecedented heights through augmented speed, precision, versatility, and sustainability while improving operator safety.
Coming Up, Part 2
In the next installment, we will discover how these modern technologies have elevated welding to unprecedented heights through augmented speed, precision, versatility, and sustainability while improving operator safety.