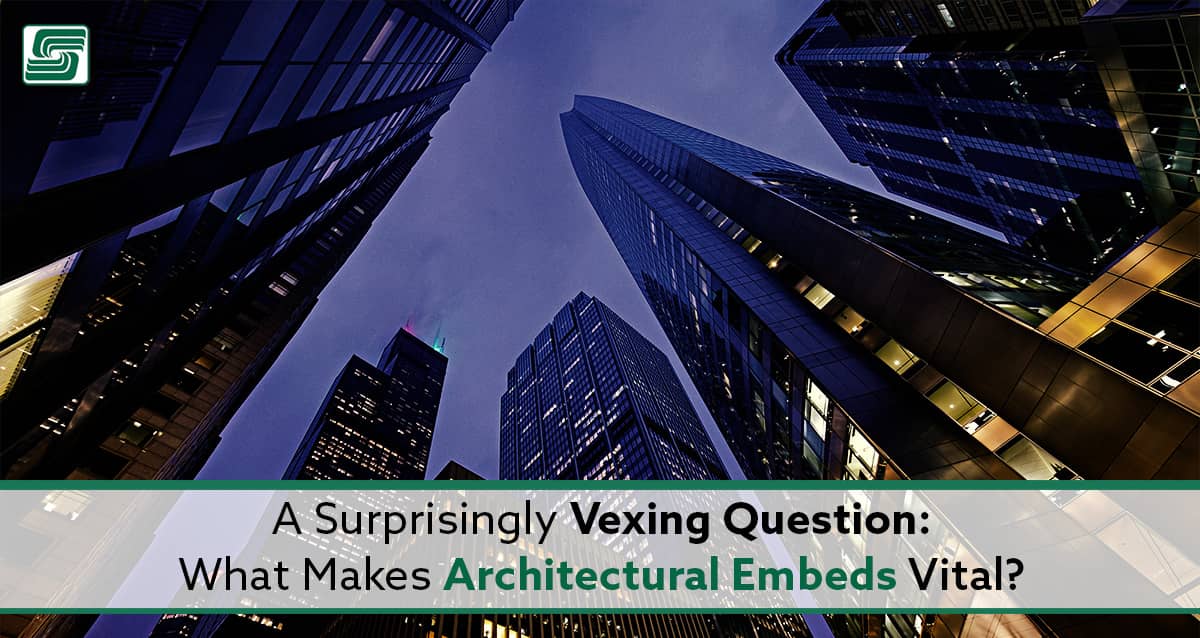
We see the result of their jobs every day, but only if we're looking.
They're something taken for granted, but for years, their job was an open riddle, hoping to be solved.
What are they? Embeds.
What are Embeds?
Considered the best method, embeds attach concrete to steel framework.
The plates, prefabricated steel with lugs welded to them, are cast inside concrete. Lugs attached to concrete reinforcements held the embed in place. The exposed plate creates the surface connecting steel to concrete.
Hot-rolled steel sections, used in construction, changed the various designs for embeds and anchors. These sections provide changes creating higher tolerances when placing the embeds.
An Important Piece of the Puzzle
Because their delivery is so far in advance, time becomes tight when making sure everything is correct. If there are no complications, the embed process makes the project go much smoother. If not, then your project falls behind because of the time inefficiencies.
Embeds play a large part in a sound anchor system. As such, there's a lot involved when engineering embeds for a project. Specifically, the following are essential considerations when designing embeds:
- How much of a load imposed on the embed?
- The strength of the concrete resisting that load
- The embed design
- Building materials
- Labor costs
Connecting embeds to footings or walls occurs in several ways;
- Precast columns
- Beams
- Plant
- Double tees
- Slabs
- Wall panels
Technically, embeds aren't individual components. Instead, they're an important piece of the structural system. How embeds became a critical aspect of construction isn't exactly clear, but their roots reach back over 160 years ago.
- 1848: Jean-Louis Lambot first used reinforced concrete when building a boat using iron bars and mesh.
- 1854: A Brit, William B. Wilkinson, made the first building using reinforced concrete of a two-story cottage he built for his servants.
- 1853: Frenchman François Coignet first used iron reinforced concrete on a widespread scale.
In his 1959 book, Concrete, Peter Collins considered Coignet as an unsung hero of the modern world.
"Coignet can justly be regarded as the man who first brought mass concrete construction to the knowledge of the modern world, and who in his lifetime exploited it to its utmost capacity. His methods were far more scientific than those practiced elsewhere in his day, and although he never undertook laboratory experiments, or attempted to ascertain theoretically the economic dimensions of the material required, he spared no pains in making practical tests."
BN Products created the following timeline showing the history of reinforced concrete. Despite the long history of concrete, the idea of reinforcing it didn't occur until the mid-19th Century.

Embeds started appearing in construction projects in Boston, Philadelphia, and New York in the 1920s. Their job was simple, provide conduits for cables and wires.
The first conduits were steel, embedded in poured concrete floors with access points for various locations. Once placed, the last step connecting electrical wiring was feeding cables through the tube.
As time passed, embeds provided an attached surface of restraints and supports for electrical raceways and equipment. Before embeds, finding locations for the walls and floors relied on on-site measurements.
"… In previous methods of construction, tape measures, levels, etc. were used to locate the position of the walls and floors to be constructed, and subsequently the equipment, piping, electrical raceways, HVAC; etc. Each of these assembly operations was performed using the stick-build construction method, with thousands of single-component fitting tasks occurring simultaneously in the same physical floor space at various distances above the floor. This meant that mazes of scaffolding were required to access locations above the floor, resulting in a progressively decreasing workspace in which to perform the tasks."
Exploring Other Types of Embeds
Curtain Walls
A curtain wall system is a non-structural external wall that comprises wall panels attached to the outside of the building's floor slabs; in plain terms, they hang on the structure like a curtain. Installers usually use curtain walls on large, high-rise commercial buildings. Unlike other exterior walls that make up an essential component of the structure, curtain walls only support themselves. External forces are transferred to the primary structure through columns or floors because curtain walls bear only their weight.
Not only do curtain walls help with the building's aesthetics, they also help contain fires for an unspecified amount of time, hopefully providing enough time for people to escape the danger.
In Sum
The history behind reinforced concrete and embeds is a bit complicated, but it all revolves around the use of steel sections through the ages.
In the 19th century, blacksmiths used iron for reinforcing structures. They embedded the iron in a concrete mix that gave the structure strength. As buildings became taller, the problem became getting iron into the structure, creating an evolution towards using steel.
Steel is much easier to work with than iron, yet it still provides the same strength. The un-reinforced concrete (or "un-reinforced masonry") was out of sight from the eye. However, this wasn't the end of the story. Steel alone isn't as strong as concrete. That's where embeds come into play.
Embeds add reinforcement and strength to the structure by holding the steel in place and providing an attached surface for other reinforcements. Using steel embeds also adds flexibility. It's possible to change designs, add connections, and move them. They're also built with a lot of room for error.
That's good because few people like surprises. Embedded technology is only beginning, so there are more questions than answers. Future research may show that the best designs are the ones that spend the most time developing, testing, and evaluating.