The fifth protective coating in this series is autodeposition. Although the finished surface resembles the results of E-Coating, the autodeposition process differs in several ways.
We’ll explore the differences between autodeposition and e-coating in a future article. For now, though, we’ll define the process.
Autodeposition
Autodeposition has several aliases, the most common being a-coating.
A-coating differs from the classical e-coating because it doesn’t need metal pre-treatment with electricity forming the coating. Instead, an organic layer forms from degreasing the metal surface with a mixture of water, water vapor, and a combination of natural and non-organic compounds.
Dipping makes coating complex components evenly possible from the inside out, covering a complete assembly of different materials. It coats the sediment with a mixture of two iron ion chromosomes in a set of four with a mild acid by an electrically driven coating process.
The wet solution forms the coating while flowing and continually refilling. The layer reacts with the metal’s surface and only requires cleaning and rinsing, preparing the parts for deposition.
The Autophoretic® coating process chemically deposits an organic polymer emulsion on the surface of a clean metal substrate using a water-based method. There’s no direct contact between the metal and the organic material, only a chemical compound.
The ions interact with the latex, causing the coating to deposit on the surface of the steel part and creating an organic polymer emulsion.
Process
The sequence and process of a-coating are simple. Figure 1 illustrates the sequence:
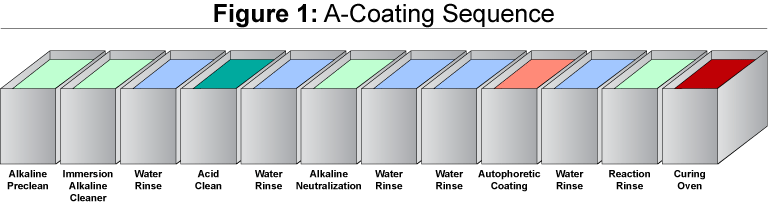
A mild acid bath cleans slight amounts of iron from the steel. The exposure to the acid causes an immediate surface reaction, releasing iron ions. The interaction between the ions and latex in the solution deposits the coating on the steel.
Despite the excellent adherence, the surface is very porous, allowing the dispersal of chemical activators reaching the surface of the steel. The layer provides superior corrosion resistance and surface protection resulting from the repeated coating process.
Thickness Control
It’s important having the ability to control the amount of material deposited on the metal. Many specialized industries require specific thickness for their component, plus maintaining consistent thicknesses reduces material waste.
Here are three methods for controlling the amount of thickness on the substrate:
Time
The protective coating depends on the diffusion of ferrous ions from the surface and ferric ions to the surface; the coating process slows down and self-limits. The more time the steel spends immersed, the more material deposits on the surface.
Mixers
Mixers agitate the fluid in the chemical bath, bringing fresh ions to the surface. Adjusting the speed of the mixer significantly affects the number of ions deposited.
Activator
Using activators increases the reactivity of the chemical bath.
Industries Used
A-coating compares to other coating technologies. Some applications and markets include:
- Defense and machine supporting industries
- Automotive and ancillaries
- General engineering
- Heavy earth moving equipment manufacturing
- LCV/MCV/HCV auto service
- Heavy earth moving equipment
- Power equipment
- Aviation and marine components
Advantages
There are several advantages to the a-coating process. These are:
Unlimited Throwing
Electromagnetic radiation results from the coupling of electric and magnetic fields. When applied to the surface of a conductor, the electrical field influences a current leading to the displacement of the conductor’s charge. Electrical shielding doesn’t limit the a-coating process, whatever the coating reaches gets coated.
Coating Complex Components
The a-coating process allows for complete coverage of complex components because of the immersion process.
Resistance to Abrasion
The hardness and direct bond to a substrate offer exceptional wear resistance.
Environmental
The a-coating process is VOC free and has a minimal environmental impact.
Cure Temperature
Curing at 220 ºF coats composite parts and assemblies with rubber and plastic components as full assemblies.
Electricity Free
The process doesn’t require any electricity. Instead of relying on the current, a chemical reaction completes the job.
In Sum
The process of a-coating compares to other primer coatings, yet it differs. Because there’s no electrical input needed at all, it’s perhaps the most environmentally friendly of all protective coating processes. The process itself is reliable and straightforward and used successfully for decades in a variety of industries.