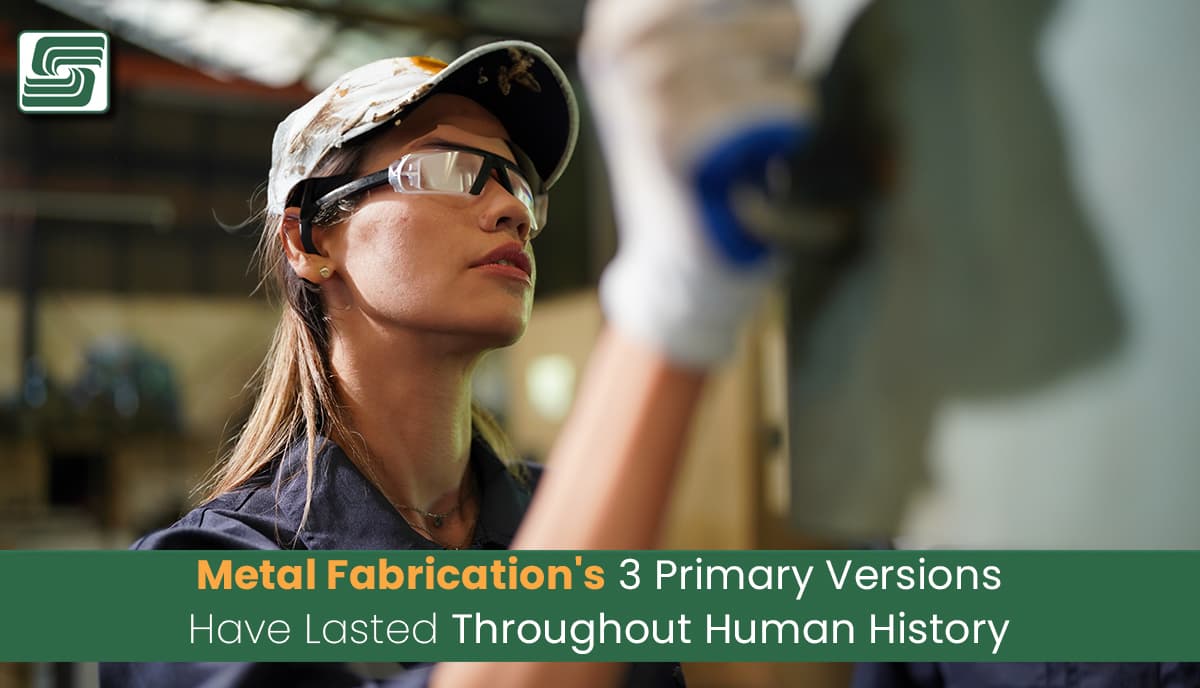
Metal fabrication is a complex and essential process that involves transforming raw metal materials into various structures and components through cutting, shaping, and joining techniques. It plays a pivotal role in numerous industries, such as construction, automotive manufacturing, aerospace engineering, and many more. The art of metal fabrication dates back centuries and has continuously evolved with advancements in technology and techniques.
Metal fabrication can be defined as the process of shaping metal materials into desired forms by utilizing various tools, equipment, and technical skills. It encompasses a broad range of operations, including welding, cutting, bending, forming, machining, powder coating, and additive manufacturing. These techniques are employed to create products that range from simple household items to complex machinery parts.
Metal Fabrication's Role in Various Industries
The significance of metal fabrication cannot be overstated, as it serves as the backbone for multiple industries worldwide. In the construction sector, metal fabrication is crucial for fabricating structural steel beams and columns used in building bridges. Additionally, it plays a vital role in manufacturing heavy machinery for agricultural purposes or industrial applications like mining equipment.
In the automotive industry, metal fabrication is indispensable for producing car bodies and frames that ensure safety and functionality. Without efficient metal fabrication techniques like welding or forming processes such as press braking or roll forming, these vehicles would not exist.
Moreover, the aerospace industry heavily relies on precise metal fabrication to manufacture aircraft components that meet stringent safety standards. Every aspect requires meticulous attention to detail during fabrication, from engine parts to fuselage panels to landing gear systems.
3 Types of Metal Fabrication
Metal fabrication can be broadly categorized into three main types:
- Traditional techniques encompass welding, cutting/shearing, and forming/bending.
- Advanced techniques, including CNC machining, powder coating, and additive manufacturing (3D printing).
- Niche subtopics that delve into specific areas within metal fabrication.
Traditional metal fabrication techniques have been practiced for centuries and remain fundamental to the industry. These methods predominantly involve welding, which involves joining two or more pieces of metal by melting them together.
Cutting and shearing techniques involve separating metal using various tools such as lasers, plasma cutters, or water jets. Forming and bending methods transform metal into desired shapes using specialized equipment like press brakes or roll formers.
On the other hand, advanced metal fabrication techniques have emerged with technological progress. CNC machining employs computer-controlled machines to precisely shape metal parts based on digital models.
Powder coating is a process where a fine powder is electrostatically applied onto the surface of an object to create a durable and aesthetically pleasing finish. Additive manufacturing, commonly known as 3D printing, allows for creating complex metal structures by building layer upon layer.
Niche subtopics within metal fabrication explore specific areas, such as artistic blacksmithing or architectural sheet metalwork, that require specialized skills and expertise. Understanding the intricacies of metal fabrication is vital for appreciating its significance in various industries.
This article will delve deeper into each type of fabrication technique - traditional, advanced, and niche - exploring their intricacies, applications, benefits, and impact on different sectors. By unraveling the complexities of these processes, we gain insight into the artistry behind transforming raw metals into essential components that drive innovation across countless fields.
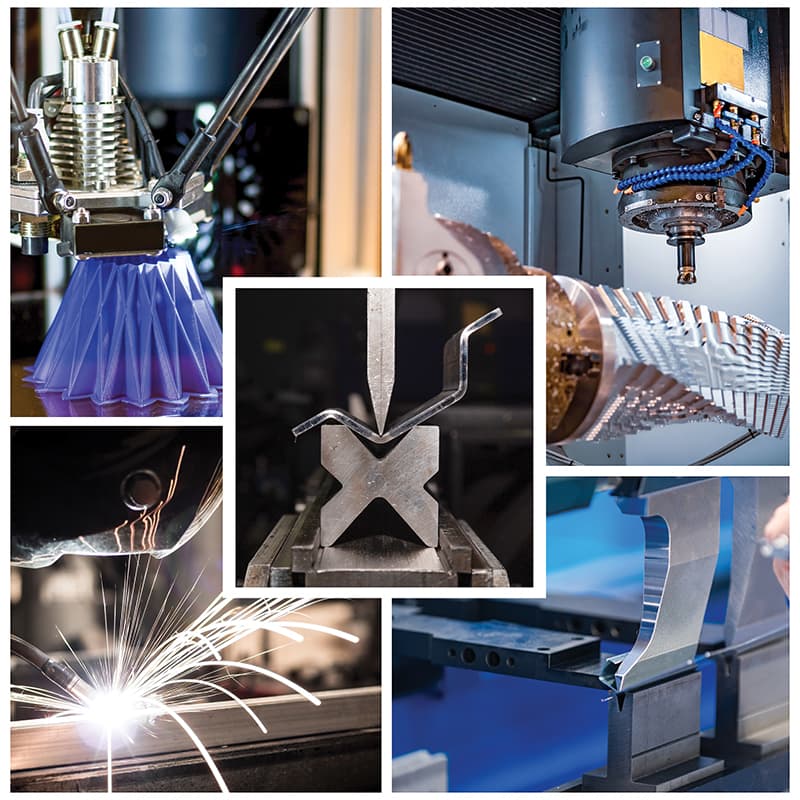
Traditional Metal Fabrication Techniques
Welding
Welding is one of the most widely used traditional metal fabrication techniques, encompassing various processes such as MIG (Metal Inert Gas), TIG (Tungsten Inert Gas), and Stick welding. Each process has its unique characteristics, making it suitable for different applications within diverse industries.
MIG welding, or Gas Metal Arc Welding (GMAW), is a versatile process commonly used in automotive manufacturing and construction industries. It uses a consumable wire electrode that melts and fuses with the base metal, creating a strong joint.
MIG welding offers high productivity from its continuous wire feed system but may produce a spatter and require shielding gas. TIG welding, or Gas Tungsten Arc Welding (GTAW), is renowned for its precision and ability to create clean welds.
This process uses a non-consumable tungsten electrode to generate an electric arc that melts the base metal while an inert gas protects the weld area from atmospheric contamination. TIG welding's advantages include excellent control over heat input and accurate weld bead formation, making it ideal for aerospace applications where precision is crucial.
Stick welding, technically termed Shielded Metal Arc Welding (SMAW), relies on an electrode coated in flux that melts during the process to create protection against atmospheric impurities. This technique is known for being relatively simple and portable compared to other methods; thus, it finds ample application in construction projects, pipelines, and repair work.
Cutting and Shearing
Cutting and shearing techniques are indispensable in metal fabrication as they precisely shape materials into desired dimensions. Three notable cutting methods widely utilized are laser, plasma, and waterjet.
Laser cutting employs a high-powered laser beam focused through a lens to melt, burn, or vaporize the cut material. This process offers exceptional precision and handles various metal thicknesses, making it popular in automotive manufacturing, aerospace, and electronics industries.
The speed and accuracy of laser cutting enable intricate designs and complex shapes to be achieved without excessive heat distortion. Plasma cutting involves using ionized gas directed toward the metal to be cut.
The intense heat generated by an electric arc causes the metal to melt and blow away because of a high-velocity plasma jet. Plasma cutting is renowned for handling various metals, including stainless steel, aluminum, and carbon steel.
It finds applications in fabrication shops, industrial construction projects, shipbuilding, and many other heavy-duty applications. Waterjet cutting employs a powerful jet of water mixed with abrasive particles (e.g., garnet) that erode the material being cut through supersonic speed impact.
This method is exceptionally versatile since it cuts through metals with varying thicknesses and non-metallic materials like stone, glass, or composites. Waterjet cutting is extensively used in architectural design firms for precise metal shaping for intricate lettering details on metal plates or aluminum sheets.
Forming and Bending
Forming techniques play a pivotal role in creating various shapes from flat sheets or bars of metal through processes like press brake bending and roll forming. Press brake bending involves clamping the workpiece between a punch (upper tool) and die (lower tool) while applying force to produce desired bends on the material. This method allows precise control over angles and bends radii while accommodating different materials' ductility characteristics.
Press brake bending is widely used in sheet metal fabrication to create complex components like brackets, enclosures, or chassis parts in automotive manufacturing or electrical equipment production. Roll forming utilizes successive rollers to progressively shape a continuous metal strip or coil into a desired cross-section.
The process involves feeding the material through rollers, each performing a specific bending or forming operation until the final shape is achieved. Roll forming is highly efficient and cost-effective, making it suitable for large-scale production of sections with repetitive profiles such as roof panels, window frames, and steel beams.
Different metals respond differently to forming processes because of their unique properties, such as ductility and elasticity. For instance, aluminum exhibits excellent formability but has lower elastic recovery than steel.
On the other hand, steel may require higher forces for bending but possesses better elastic memory. Understanding these characteristics enables metal fabricators to select appropriate forming techniques and optimize manufacturing.
Through traditional metal fabrication techniques like welding, cutting, shearing, and forming and bending methods, manufacturers transform raw materials into diverse products seen across numerous industries, including automotive manufacturing, construction, aerospace engineering, and electronics production - to name a few. These techniques form the foundation of metal fabrication and are continuously innovated alongside emerging advanced technologies.
CNC Machining
An Evolution in Precision and Efficiency
CNC machining, an acronym for Computer Numerical Control Machining, has revolutionized the world of metal fabrication. This advanced technique involves using computer-controlled machines to precisely shape and cut metal.
Unlike traditional machining methods that rely on manual operation, CNC machines follow precise instructions programmed into a computer, resulting in enhanced accuracy and efficiency. The utilization of CNC machining has numerous advantages over traditional methods.
Firstly, it eliminates human error by ensuring consistent and repeatable results, even for complex designs. Additionally, CNC machines operate continuously without fatigue or the need for breaks, significantly reducing production time.
CNC machining spans various industries, including aerospace, automotive, and medical sectors. In aerospace manufacturing, precision is paramount for safety requirements; CNC machines fabricate intricate components such as turbine blades and aircraft fuselage sections.
The automotive industry benefits from this technology by producing high-precision engine parts and transmission components, ensuring optimal performance and longevity. Furthermore, the medical field uses CNC machining to create delicate surgical instruments with exceptional precision that aids in minimally invasive procedures.
Powder Coating
Unleashing Vibrant Colors While Protecting Metals
Powder coating is a highly effective metal finishing technique widely preferred over traditional painting methods for its durability and aesthetic appeal. This process involves applying a dry powder of finely ground particles onto a metal surface using electrostatic charge principles or compressed air sprayers. The coated metal is then exposed to heat, where the powder melts into a smooth film that adheres uniformly to the surface before cooling into a tough finish.
The benefits of powder coating are multifaceted. Firstly, it provides superior protection against corrosion compared to liquid paint as it forms a thicker barrier on the metal surface, ensuring longevity even in harsh environments.
Secondly, powder coating offers several color options and finishes, allowing for customization and creativity in architectural design and outdoor equipment manufacturing. The use of powder coating has gained popularity for its environmentally friendly nature, as it produces minimal waste, emits no volatile organic compounds (VOCs), and is recycled.
Additive Manufacturing (3D printing)
Merging Creativity with Efficiency
Additive manufacturing, known as 3D printing, has emerged as an innovative path in metal fabrication. Unlike traditional subtractive methods that involve removing material to create the desired shape, additive manufacturing builds objects layer by layer using computer-generated 3D models. This technique has numerous advantages over traditional manufacturing techniques.
It enables the production of complex geometries that would be challenging or impossible to achieve through conventional means. Furthermore, additive manufacturing reduces material waste since it only uses the amount required for each product.
The applications of additive manufacturing with metals are extensive and continue to expand across various industries. In aerospace engineering, 3D printing facilitates the creation of lightweight yet robust components that contribute to fuel efficiency and improve overall aircraft performance.
It plays a pivotal role in customizing medical implants tailored to patients' needs while ensuring biocompatibility. Moreover, additive manufacturing enables quick prototyping in product development cycles across industries by rapidly producing functional prototypes for testing and evaluation.
With CNC machining's enhanced precision and efficiency, powder coating provides durable protection with vibrant colors and additive manufacturing, pushing the boundaries of customization and innovation – advanced metal fabrication techniques have transformed how we create objects from metals. These techniques offer superior results and open new possibilities for industries seeking efficient production methods without compromising quality or creativity.
Niche Fabrication Techniques
Specialized Joining
Metal fabrication encompasses a vast array of techniques, and within this realm, specialized joining methods exist that cater to specific needs. These techniques often involve bonding metals without traditional welding, offering distinct advantages in certain applications. One such technique is soldering, which combines two metal pieces with a low-melting-point metal alloy. This method is commonly employed in electronics manufacturing or jewelry making, where precision and heat sensitivity are crucial. Another niche joining technique is adhesive bonding, which utilizes high-strength adhesives to bond metals. Unlike traditional welding, adhesive bonding does not alter the structural integrity of the base metals and allows for greater design flexibility. It finds applications in aerospace and automotive manufacturing, where weight reduction is vital.
Hydroforming and Deep Drawing
Hydroforming involves using pressurized fluid to shape metal sheets or tubes into complex forms. This technique utilizes hydraulic pressure to force the metal into a die cavity, resulting in intricate shapes with minimal distortion or wrinkling. Hydroforming offers advantages such as improved strength-to-weight ratio, reduced tooling costs, and enhanced design possibilities. Deep drawing is another specialized metal forming technique for creating hollow components with large depth-to-diameter ratios. By pulling a flat sheet of metal into a die cavity using radial forces, deep drawing enables the production of items like cans or automotive parts with exceptional precision and uniform thickness distribution.
Metal Spinning
Metal spinning is an ancient craft that remains relevant today due to its distinctive capabilities in shaping symmetrical cylindrical components from flat sheets or performed metal blanks. Skilled craftspeople create decorative bowls or lampshades with unparalleled precision and aesthetic appeal by rotating the material on a lathe while applying pressure with various tools. Metal spinning is particularly popular in the art and design industries, where intricate detailing and smooth finishes are highly sought after.
Surface Finishing
Surface finishing plays a critical role in metal fabrication, as it provides protection against corrosion and enhances the aesthetic appeal of the final product. Various techniques are employed to achieve desired surface finishes, such as polishing for a mirror-like shine or etching to create textured patterns. Electroplating is another commonly used method where a metal coating is applied to the surface of an object via an electrochemical process. This technique improves resistance to wear and corrosion while allowing for decorative enhancements like gold or chrome plating.
In Sum
Metal fabrication encompasses various techniques, each serving specific purposes in diverse industries. From specialized joining methods like soldering and adhesive bonding to niche techniques like hydroforming, deep drawing, and metal spinning, there is no shortage of options for manufacturers looking to create customized metal components. Moreover, surface finishing techniques such as polishing or electroplating add protective properties and visual appeal.
As technology advances, metal fabrication innovations emerge regularly. These advancements improve efficiency, precision, and cost-effectiveness across various industries.
With the ever-growing demand for quality metal products worldwide, it is promising to witness how these evolving techniques will shape the future of manufacturing. Metal fabrication remains a fascinating field that opens endless possibilities for creative design solutions while ensuring durability and functionality in our everyday lives.