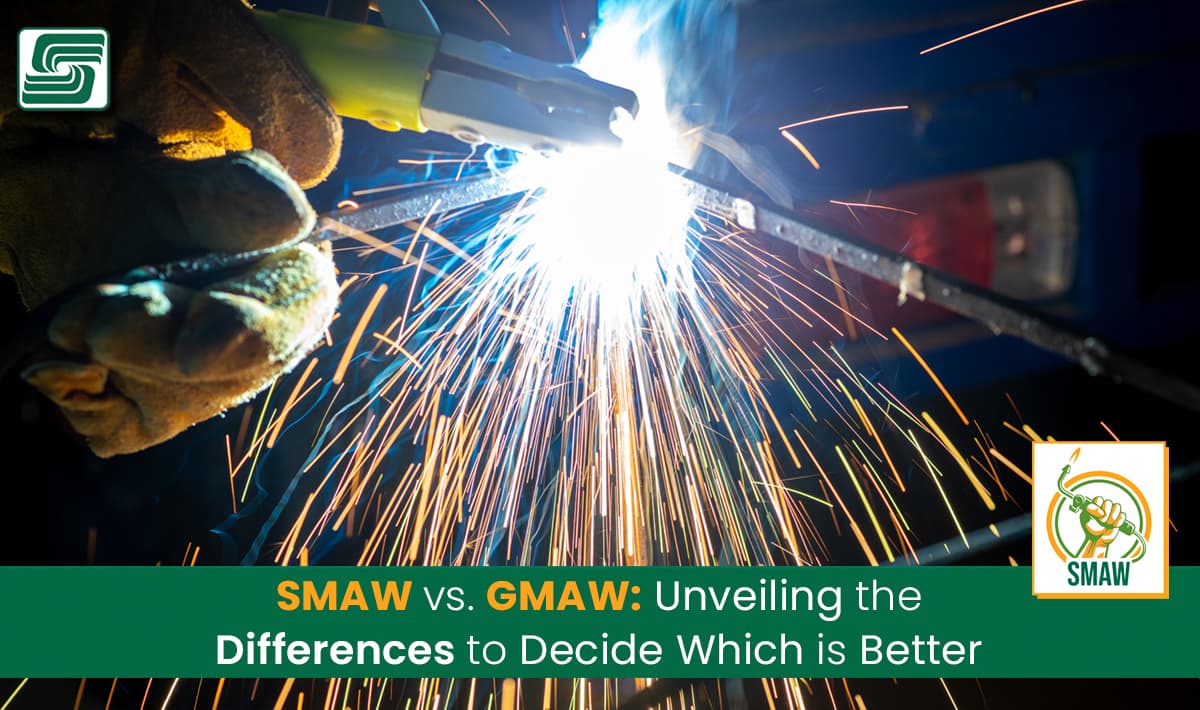
FAB Times SMAW Series
In our recent series on FAB Times, we delved deep into the world of Shielded Metal Arc Welding (SMAW). We focused on SMAW's nuances, starting with an overview of popular welding methods. The series also pits SMAW against other welding techniques, such as FCAW, GMAW, GTAW, and SAW, to help you understand which method best suits your needs.
Articles in the Series:
- How Well do You Know the 5 Most Popular Welding Methods?
Get a broad view of the top welding methods, including SMAW. Read More
- What Does it Take to Master the Art of Shielded Metal Arc Welding?
Learn what makes SMAW unique and how to master it. Read More
- SMAW vs. FCAW: Sparking a Debate About These Popular Welding Methods
Compare SMAW and FCAW to find out their pros and cons. Read More
- SMAW vs. GMAW: Unveiling the Key Differences to Decide Which is Better
Explore the differences between SMAW and GMAW. Read More
- Anyone Ever Teach you the Differences Between Stick and TIG Welding?
Understand how SMAW differs from GTAW, also known as TIG welding. Read More
- Speed Matters: How SAW Outpaces SMAW in Welding Efficiency
Learn why SAW is faster than SMAW and when to use each method. Read More
In the world of welding, two prominent processes stand out: Shielded Metal Arc Welding (SMAW) and Gas Metal Arc Welding (GMAW). SMAW, also known as stick welding, has been a cornerstone of welding practices for over a century.
SMAW uses a consumable electrode coated in flux to create an electric arc that melts the base metal and forms a weld in the joint. On the other hand, GMAW, commonly referred to as MIG welding (Metal Inert Gas), employs a continuous wire electrode fed through a welding gun and an inert gas shield to protect the weld pool from atmospheric contamination.
SMAW is renowned for its simplicity and versatility. It can be performed in various positions and weld diverse materials such as carbon steel, stainless steel, cast iron, and low alloy steel. However, these metals require their own specific electrode.
The equipment needed for SMAW is relatively basic; it usually includes a power source or welding machine capable of producing direct current (DC), electrode holders or clamps, cables for electrical connections, and personal protective equipment like gloves and helmets.
Equally, GMAW is recognized for its efficiency and high productivity rate, which offers excellent control over parameters such as wire feed rate, voltage settings, and shielding gas composition, resulting in precise welds with minimal spatter. It is primarily used for joining thin to medium-thickness metals such as aluminum alloys or mild steel in industrial applications.
Understanding the Differences
While SMAW and GMAW are widely used in various industries, ranging from construction to automotive manufacturing, understanding their differences is crucial when selecting the most suitable method for specific applications.
By comprehending these divergences, welders, and fabricators make informed decisions regarding project requirements, material compatibility, time constraints, and cost-effectiveness.
Each process has distinct advantages and limitations that significantly impact the success of a welding project.
By gaining knowledge of these differences, welders optimize their welding practices and achieve superior results. Understanding the dissimilarities between SMAW and GMAW enables professionals to expand their skill sets and versatility.
By learning both techniques, welders broaden their capabilities and become proficient in performing different welds on various materials. Becoming acquainted with SMAW and GMAW is essential for anyone in the welding industry.
These two processes offer unique characteristics that cater to different requirements regarding simplicity, productivity rate, material compatibility, and cost-effectiveness.
By exploring the nuances of each method comprehensively, welders make educated choices that ensure optimal outcomes for their projects while enhancing their proficiency as skilled artisans in this skilled trade.
SMAW: Unveiling the Basics
SMAW, also known as Shielded Metal Arc Welding or stick welding, is one of the oldest and most versatile welding processes. Dating back to the early 20th century, SMAW has stood the test of time because of its simplicity and reliability.
The process involves creating an electric arc between a flux-coated electrode and the workpiece, which generates intense heat to melt the base metal and form a strong bond upon cooling, which is equivalent to the tensile strength of the applicable electrode.
SMAW has become an integral part of the welding repertoire, with its widespread adoption across the construction, fabrication, and repair industries.
SMAW Required Equipment
Certain essential equipment is required to perform SMAW successfully.
- Power Source capable of providing direct current (DC) is needed—an AC/DC transformer or a DC generator. The choice depends on portability requirements and power availability at the worksite.
- Electrodes are crucial in SMAW as filler material and flux coating. These consumable electrodes come in various types based on their composition and intended application.
- Protective gear is vital when engaging in any welding activity to ensure safety. Welders must wear proper attire, including flame-resistant clothing or leather jackets with long sleeves for protection against sparks and radiating heat.
- Welding gloves made from heat-resistant materials provide hand safety while maintaining dexterity.
- Helmets equipped with auto-darkening filters safeguard welders' eyes from harmful ultraviolet (UV) rays emitted during arc generation.
Performing SMAW Welds
Executing a successful SMAW weld involves several sequential steps that require attention to detail:
- Electrode Selection: Choose an appropriate electrode based on the base metal and the specific welding application. Factors to consider include electrode composition, diameter, coating type, and tensile strength.
- Surface Preparation: Clean the base metal surface thoroughly by removing rust, dirt, and contaminants that may hinder proper fusion during welding, achieved through wire brushing, grinding, or chemical cleaning methods.
- Electrode Positioning: Hold the electrode at a suitable angle relative to the workpiece, typically between 15 to 45 degrees. The angle depends on joint configuration and the desired weld bead shape.
- Arc Initiation: Strike an arc between the electrode tip and the base metal by momentarily tapping or scratching it against the workpiece surface while maintaining a safe distance.
- Welding Technique: Control the arc length by maintaining a consistent distance between the electrode tip and the workpiece surface throughout the welding process. Move steadily along the joint while employing proper weaving or dragging techniques to ensure adequate penetration and uniform bead appearance.
- Post-Weld Inspection: Once welding is complete, inspect the weld for defects such as cracks, porosity, or incomplete fusion using visual inspection or non-destructive testing techniques, such as ultrasonic testing (UT) or X-ray examination (RT).
By following these steps, welders achieve high-quality SMAW welds exhibiting excellent strength and durability in various applications.
Understanding SMAW's definition, historical significance, and required equipment components and mastering its step-by-step process is foundational to exploring differences between SMAW and GMAW more comprehensively in pursuit of informed decision-making regarding their comparative merits within specific welding scenarios.
GMAW: Delving into the Essentials
Gas Metal Arc Welding (GMAW), also known as Metal Inert Gas (MIG) welding, is a widely used process that employs a continuous solid wire electrode, an inert shielding gas, and a welding gun. GMAW was first developed in the 1940s to increase productivity and reduce post-weld cleanup time compared to traditional welding methods. This innovative process revolutionized the industry by providing faster and more efficient ways of joining metal components.
The principle behind GMAW is straightforward. A direct current (DC) power source supplies electricity to the wire electrode, continuously fed through the welding gun.
Simultaneously, an inert shielding gas, such as argon or a mixture of argon and carbon dioxide, is released from the gun's nozzle to protect the molten weld pool from atmospheric contamination. The electric arc formed between the wire electrode and the workpiece melts both materials, creating a bond when they solidify.
Equipment Needed for GMAW
Several essential pieces of equipment are required to perform GMAW effectively. The centerpiece is the welding gun or torch—a handheld device that holds the wire electrode and nozzle for gas delivery.
The torch must be compatible with specific wire sizes and types to ensure proper feeding during the welding process. GMAW also relies on shielding gases to prevent oxidation and improve weld quality.
Commonly used shielding gases include pure argon for non-ferrous metals like aluminum or a mixture of argon and carbon dioxide for steel applications. Another vital component is the wire electrode itself.
It comes in various thicknesses or diameters depending on your project's requirements—typically ranging from 0.6 mm to 1.6 mm—each with specific characteristics and applications. For instance, solid wire electrodes are suitable for general welding, while flux-cored wires with an inner flux coating offer self-shielding capabilities, eliminating the need for external shielding gas.
Welding Using GMAW
- The GMAW process involves a series of steps to create a successful weld. The power source must be properly adjusted to deliver the right voltage and amperage according to the welded material, ensuring proper melting of both the electrode wire and workpiece metal.
- Wire feed rates must be carefully controlled to maintain a stable arc length. Wire feed speed determines how quickly the electrode is consumed during welding. An optimal wire feed rate ensures steady heat input and deposition of molten metal, avoiding issues such as excessive spatter or lack of fusion.
- Arc length control is crucial in GMAW as well. Generally, a short arc length provides better control and higher penetration levels while minimizing spatter. However, if the arc becomes too short, it may cause undue heat concentration leading to burn-through or distortion. Protecting the weld pool from atmospheric contamination is vital throughout the GMAW process.
- The shielding gas flow rate should be adequately adjusted to provide sufficient coverage over the weld area while preventing excessive turbulence that could negatively impact overall weld quality.
By attentively managing these aspects—voltage and current settings, wire feed rates, arc length control, and shielding gas flow—the GMAW operator precisely controls their welds' quality while ensuring that all necessary parameters are met for successful joint formation.
Key Differences between SMAW and GMAW
With electrical characteristics, SMAW and GMAW differ significantly. SMAW, known as stick welding, uses a constant current power source—meaning the amperage remains relatively stable.
At the same time, the voltage fluctuates depending on factors such as electrode length and arc length. On the other hand, GMAW employs a constant voltage power source.
In this process, the voltage is set at a fixed level, while the current varies based on factors like wire feed speed and diameter. The distinction in electrical characteristics between these two processes has implications for their practical applications.
Because of its ability to adapt to varying arc lengths, SMAW is better suited for welding thicker materials or in environments where maintaining a consistent arc length may be challenging.
Conversely, GMAW's constant voltage setting makes it ideal for welding thinner materials with more precision since it ensures a steady heat input throughout the weld.
Skills Needed for Both
Because of its manual nature, proficiency in SMAW requires a certain level of skill and experience. The welder carefully controls the electrode position and angle while simultaneously managing other variables, such as travel speed, rod manipulation, and puddle control.
The complexity of achieving optimal results with SMAW often requires extensive training and practice. In contrast, GMAW is considered easier to learn and execute effectively, making it more accessible to novice welders.
A welding gun equipped with continuous wire feeding simplifies the technique considerably compared to SMAW's manual electrode manipulation and puddle control.
However, even though GMAW may be easier for beginners to grasp initially, mastering this process at an advanced level still demands an understanding of various parameters, gas mixtures, and proper technique.
Industries Using SMAW or GMAW
SMAW finds widespread application in the construction, shipbuilding, and pipeline welding industries. Its portability and adaptability make it suitable for outdoor projects where conditions may be less controlled.
SMAW's ability to penetrate through rust or other surface contaminants makes it advantageous to repair existing structures.
It is often the preferred choice for heavy-duty welding tasks that require high-quality welds and high deposition rates. GMAW has found favor in automotive manufacturing, aerospace fabrication, and general metal fabrication industries because of its versatility and ability to produce visually appealing welds with excellent control over the bead appearance.
The process is well-suited for thin sheet metal applications since it minimizes distortion and heat-affected zones. Its efficiency in producing cleaner welds also lends itself to mass-production environments.
Cost Considerations
In terms of cost considerations, both SMAW and GMAW have their own distinct aspects to consider. SMAW requires a more affordable initial investment since the equipment needed is relatively simple compared to the more complex setup required by GMAW.
However, SMAW electrodes are consumable items that need frequent replacement for a project, increasing long-term costs.
GMAW equipment is costlier upfront but offers greater efficiency because continuous wire feeding systems result in reduced downtime compared to manually replacing electrodes, as with SMAW.
GMAW has superior deposition rates to SMAW, increasing productivity in certain scenarios.
Overall cost analysis should consider factors such as project scale and material thicknesses being welded frequently since certain processes may be more economical depending on these variables.
The key differences between SMAW and GMAW are clear in their electrical characteristics, skill requirements, applications, and cost considerations.
Understanding these distinctions allows welders to decide which process suits their needs and project requirements.
Whether it be the adaptability of SMAW's electrical characteristics or the accessibility of GMAW for beginners, each process has strengths and advantages leveraged in various industries for successful weld outcomes.
Which is Better? Making an Informed Choice
Regarding weld quality, both SMAW and GMAW deliver exceptional results. SMAW produces strong welds with excellent penetration, making it suitable for heavy-duty applications, such as structural steel and pipeline welding.
GMAW provides cleaner and smoother welds because of its continuous wire feed and shielding gas protection, which makes it ideal for fabricating automotive parts or delicate sheet metal projects.
Regarding ease of use, SMAW requires more skill and practice to master. It involves manually controlling the electrode's position and maintaining the correct arc length throughout the process.
In contrast, GMAW is relatively easier to learn as it relies on automated wire feeders that automatically regulate the electrode's position. Versatility is another aspect where these welding processes differ.
SMAW can be carried out in various positions (flat, horizontal, vertical) without requiring specialized equipment or modifications. GMAW offers even greater versatility, allowing welding in all positions by adjusting parameters like wire feed speed and shielding gas composition.
When comparing the speed between SMAW and GMAW, the latter takes the lead because of its higher deposition rates. With continuous wire feeding capabilities and faster travel speeds possible with mechanized systems, GMAW significantly reduces overall welding time compared to SMAW.
Portability is an essential factor for many professionals. Here again, GMAW has an advantage over SMAW since it typically involves lighter equipment, such as welding guns, instead of heavy electrodes and power sources associated with SMAW.
Specific Project Requirements
Choosing between SMAW and GMAW ultimately depends on the specific project requirements. If the project involves heavy structural welding or working in challenging environments where portability and adaptability are crucial, SMAW is an excellent choice. Its robust nature and ability to withstand adverse conditions make it suitable for outdoor and remote welding applications.
If a project demands high precision, cleanliness, and faster production rates, GMAW should be considered. It offers consistent results on thinner materials without compromising strength.
GMAW's versatility allows for various applications, such as automotive repairs, fabrication of intricate components, or manufacturing processes that require repetitive welds.
It is essential to evaluate factors such as material thickness, joint configuration, desired weld quality and appearance, available resources (e.g., power source), budget constraints, and time limitations when determining which process aligns better with individual needs.
Future Welding Trends
The welding field constantly evolves because of technological advancements and changing industry demands. As we look into the future of welding techniques like SMAW and GMAW:
- Automation: SMAW and GMAW will continue to benefit from increased automation. Integrating robotic systems with these processes enhances productivity while maintaining high-quality welds.
- Advanced materials: With the growing use of advanced materials like lightweight alloys and composites in various industries (aerospace and automotive), welding processes must adapt to accommodate these new materials' specific characteristics.
- Energy efficiency: Future trends in welding will probably focus on improving energy efficiency by optimizing power sources and reducing overall energy consumption during the welding process.
- Hybrid processes: Hybrid welding methods that combine different techniques, such as laser beam welding with GMAW or plasma arc with SMAW, may emerge as viable alternatives for achieving superior quality welds while increasing efficiency.
- Digitalization: Welding operations will become more digitized through technologies like sensors for real-time monitoring, data collection, and analysis, enabling predictive maintenance, quality control, and process optimization.
Denique
Both SMAW and GMAW have their strengths and weaknesses, making them suitable for different applications. While SMAW excels in its ruggedness and all-position capabilities, GMAW offers cleaner welds with enhanced speed and versatility.
Individuals can make an informed choice between the two processes by carefully considering project requirements, such as material type, thickness, desired results, and constraints, such as budget or time limitations.
As welding technology advances in automation, more efficient power sources, hybrid processes combining various techniques, and digitalization of operations, the possibilities for achieving superior weld quality while increasing productivity are bright.
Embracing these future trends promises a welding industry that continually evolves to meet the needs of diverse sectors while reducing environmental impact and enhancing economic efficiency.