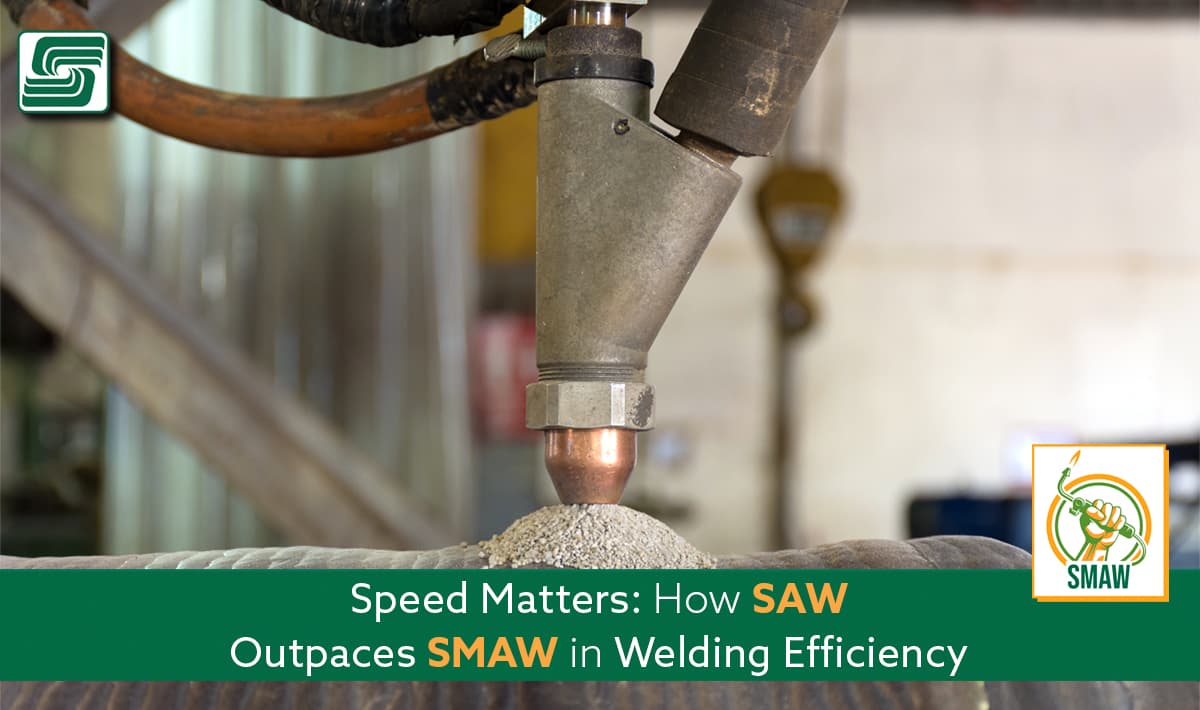
FAB Times SMAW Series
In our recent series on FAB Times, we delved deep into the world of Shielded Metal Arc Welding (SMAW). We focused on SMAW's nuances, starting with an overview of popular welding methods. The series also pits SMAW against other welding techniques, such as FCAW, GMAW, GTAW, and SAW, to help you understand which method best suits your needs.
Articles in the Series:
- How Well do You Know the 5 Most Popular Welding Methods?
Get a broad view of the top welding methods, including SMAW. Read More
- What Does it Take to Master the Art of Shielded Metal Arc Welding?
Learn what makes SMAW unique and how to master it. Read More
- SMAW vs. FCAW: Sparking a Debate About These Popular Welding Methods
Compare SMAW and FCAW to find out their pros and cons. Read More
- SMAW vs. GMAW: Unveiling the Key Differences to Decide Which is Better
Explore the differences between SMAW and GMAW. Read More
- Anyone Ever Teach you the Differences Between Stick and TIG Welding?
Understand how SMAW differs from GTAW, also known as TIG welding. Read More
- Speed Matters: How SAW Outpaces SMAW in Welding Efficiency
Learn why SAW is faster than SMAW and when to use each method. Read More
Welding, an indispensable industrial process, is pivotal in joining metallic components to create structurally sound and functional products. It involves fusing two or more metal pieces by subjecting them to intense heat and pressure.
Welding finds application in various industries, such as construction, automotive, aerospace, and shipbuilding. It is crucial to have a comprehensive understanding of different welding techniques to achieve high-quality welds.
The Required Welding Process Review
If you've followed along during this comparative series, you likely know what the welding process entails. But, in case you're new, here's a review.
Welding is the backbone of many industrial sectors, enabling the fabrication of complex structures and ensuring their durability. The process involves melting the base metals to be joined using various heat sources, like electric arcs, lasers, or gas flames.
As the molten metal cools down, it solidifies and forms a strong bond between the workpieces. The significance of welding lies in its ability to create connections that possess strength comparable to that of the base material itself, which allows for efficient load transfer between welded components and enhances overall structural integrity. Welding provides versatility by enabling connections between different metals with distinct physical properties.
Learn the Ways of Welding
A profound knowledge of various welding techniques is essential for welders and engineers. Each method’s unique characteristics make it suitable for specific applications and materials.
Understanding these distinctions empowers professionals to choose the most appropriate technique for a project. Familiarity with diverse welding methods enables efficient troubleshooting during fabrication processes.
Professionals promptly implement suitable remedies by recognizing common issues associated with each technique—such as distortion, porosity formation, or cracking. Understanding different weld types helps evaluate joint strength requirements based on intended service conditions.
Meet this Articles Characters: SMAW and SAW
Shielded Metal Arc Welding (SMAW) and Submerged Arc Welding (SAW) are prominent among the various welding techniques. SMAW, also known as manual metal arc welding or stick welding, has been used extensively throughout history.
It involves using a consumable electrode coated in a flux that provides shielding gases to protect the weld pool from atmospheric contamination. SAW is an automated process that uses a continuous wire electrode and a granular flux blanket.
The weld joint is submerged under this flux layer during the welding operation to shield it from harmful atmospheric elements. SMAW and SAW possess distinct advantages and disadvantages, making them suitable for different applications.
In the subsequent sections, we will delve deeper into each technique’s intricacies, discussing their equipment requirements, step-by-step processes, and pros and cons associated with their usage. Understanding various welding techniques is vital for professionals engaged in fabrication processes across diverse industries.
SMAW and SAW are two important methods with unique characteristics that make them suitable for specific applications.
Shielded Metal Arc Welding
Shielded Metal Arc Welding (SMAW), also known as “stick welding,” is a welding process that uses an electric arc between a coated electrode and the workpiece to join metals. Its origins can be traced back to the late 19th century when C.L. Coffin invented the first practical coated metal electrodes. This revolutionary development allowed for a more controlled and efficient welding process, leading to the widespread adoption of SMAW across various industries.
For a complete look at the SMAW process, read the first article in this series: What Does it Take to Master the Art of Shielded Metal Arc Welding?
Submerged Arc Welding (SAW)
Submerged Arc Welding (SAW) is a welding technique that involves the formation of an arc between a continuously fed filler wire and the workpiece. The process is carried out under a granular flux blanket, shielding the molten metal and preventing atmospheric contamination.
SAW was first developed in the 1930s to improve manual arc welding methods. Its invention revolutionized industrial welding practices by enabling high-quality, high-speed welds for thick steel sections.
Equipment and Materials for SAW
Several essential pieces of equipment are needed to effectively perform Submerged Arc Welding. The key components include a power source, wire feeder, flux hopper, and various consumables. The power source provides the electrical current to create and sustain the welding arc. A wire feeder precisely controls and feeds the filler wire into the arc zone at a predetermined rate.
The flux hopper holds the granular flux material that blankets the weld area during operation. Besides these major equipment items, consumables play a vital role in SAW.
Depending on specific requirements, the filler wire used in this process can be solid or tubular. Fluxes are also crucial as they shield the arc and molten metal from airborne contaminants while facilitating efficient heat transfer.
The SAW Process: Step-by-Step
The successful execution of Submerged Arc Welding relies on careful preparation and meticulous execution. Before starting, cleansing the base metal is essential to remove any surface contaminants that could compromise weld quality. Once cleaned, setting up the equipment involves establishing proper electrical connections between power sources, wire feeders, and flux hoppers.
With all preparations, welding starts by positioning the electrode holder and nozzle assembly over the joint to be welded. As the arc ignites, the filler wire is continuously fed into the weld pool beneath a continuous flux layer, ensuring complete protection.
The automatic nature of SAW allows for consistent, high-speed weld metal deposition. After welding, slag removal becomes necessary.
The flux coating on the filler wire forms a protective slag layer during welding, which must be removed to reveal the finished weld. Proper post-weld cleaning ensures no residual slag or other contaminants remain on the surface.
Advantages and Disadvantages of SAW
Submerged Arc Welding offers many advantages in industrial applications. Its high deposition rates provide exceptional efficiency, making it suitable for thick sections and long weld runs. The continuous blanket of flux shields both molten metal and arc from environmental contamination, providing consistent, high-quality welds with minimal defects.
SAW is highly automated, reducing operator fatigue and allowing for improved productivity. However, SAW has some limitations that must be considered.
This process is primarily suitable for flat or horizontal position welding because of the reliance on gravity to hold the molten metal in place. Its application is largely limited to thick sections as thinner materials may experience excessive heat input, leading to distortion or burn-through.
In Sum
Submerged arc welding has emerged as an invaluable technique in heavy fabrication industries where productivity and quality are paramount. The historical development of SAW has significantly advanced welding practices by enabling the rapid and reliable joining of thick steel sections with superior mechanical properties. SAW differs from traditional welding methods by employing specialized equipment such as power sources, wire feeders, flux hoppers, and consumables like filler wires and fluxes.
With meticulous preparation, including base metal cleaning and equipment setup, followed by careful execution involving automatic filler wire feeding under a protective flux blanket, SAW ensures consistent and high-quality welds. While SAW excels in efficiency, productivity, and weld quality for thick sections, it has limitations regarding positional versatility.
With proper understanding and application of this technique’s strengths and weaknesses, Submerged Arc Welding remains an immensely valuable tool in the welding industry. Its continued advancement will undoubtedly contribute to the ever-evolving landscape of industrial welding, further enhancing fabrication processes worldwide.