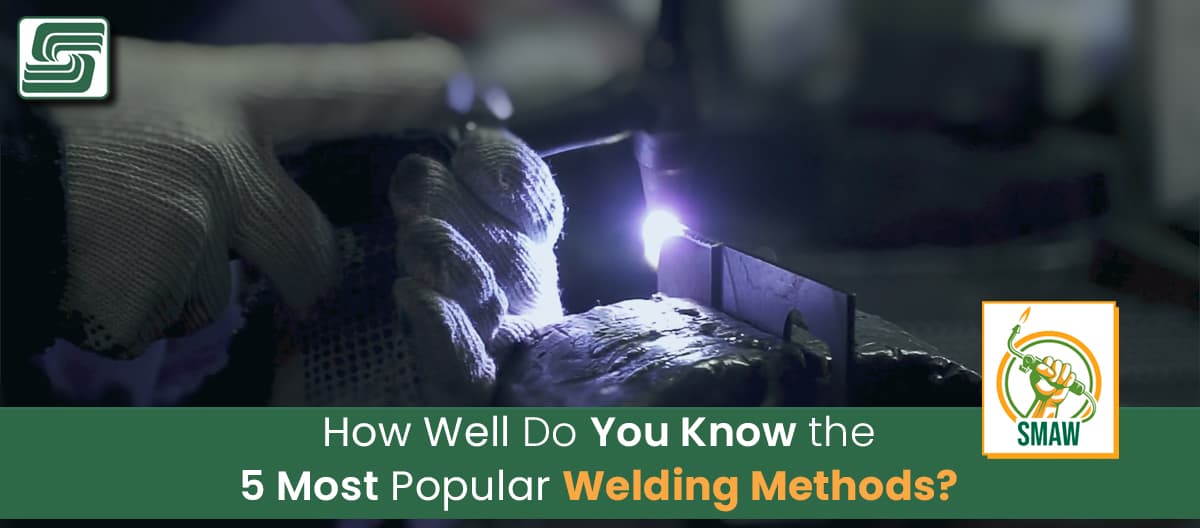
This week, we compare SMAW with four other popular welding methods head-to-head comparisons. Let's take a 10,000-foot look at each method to kick things off.
FAB Times SMAW Series
In our recent series on FAB Times, we delved deep into the world of Shielded Metal Arc Welding (SMAW). We focused on SMAW's nuances, starting with an overview of popular welding methods. The series also pits SMAW against other welding techniques, such as FCAW, GMAW, GTAW, and SAW, to help you understand which method best suits your needs.
Articles in the Series:
- How Well do You Know the 5 Most Popular Welding Methods?
Get a broad view of the top welding methods, including SMAW. Read More
- What Does it Take to Master the Art of Shielded Metal Arc Welding?
Learn what makes SMAW unique and how to master it. Read More
- SMAW vs. FCAW: Sparking a Debate About These Popular Welding Methods
Compare SMAW and FCAW to find out their pros and cons. Read More
- SMAW vs. GMAW: Unveiling the Key Differences to Decide Which is Better
Explore the differences between SMAW and GMAW. Read More
- Anyone Ever Teach you the Differences Between Stick and TIG Welding?
Understand how SMAW differs from GTAW, also known as TIG welding. Read More
- Speed Matters: How SAW Outpaces SMAW in Welding Efficiency
Learn why SAW is faster than SMAW and when to use each method. Read More
Comparing Popular Welding Methods
FCAW
FCAW, or Flux-Cored Arc Welding, is a highly versatile and widely used welding process in metal fabrication. This method uses a continuously fed electrode wire filled with flux, which melts and provides a shielding gas to protect the weld pool from atmospheric contamination.
FCAW offers several advantages over other welding methods, making it a popular choice in various industrial applications. One of the key benefits of FCAW is its high deposition rate, meaning it achieves fast and efficient welds, making it ideal for projects requiring quick turnaround times. FCAW provides excellent penetration into thick materials, allowing for strong and durable welds even in demanding applications.
The process is easily automated, increasing productivity for large-scale projects. FCAW is highly adaptable to different base metals.
Specific flux-cored wires suit each material's requirements, whether you are working with carbon steel, stainless steel, or even non-ferrous metals like aluminum and copper alloys. This versatility makes FCAW suitable for various welding tasks in construction, shipbuilding, automotive manufacturing, and pipelines.
Compared to other welding methods like SMAW (Shielded Metal Arc Welding) or GMAW (Gas Metal Arc Welding), FCAW exhibits superior performance in welding thicker sections or working in outdoor environments where wind or drafts may interfere with the shielding gas flow. This process produces less spatter than GMAW while providing good arc stability and control.
Flux-Cored Arc Welding is an efficient and flexible method that offers high productivity levels and quality welds across various materials and conditions. Its adaptability to different base metals makes it a go-to choice for metal fabricators seeking optimal strength, durability, and efficiency results.
GMAW
GMAW, also known as Gas Metal Arc Welding or MIG (Metal Inert Gas) welding, is a widely used welding process in metal fabrication. This method uses a continuous solid wire electrode fed through a welding gun and melted with a shielding gas to protect the weld pool from atmospheric contamination.
GMAW offers several advantages over other welding methods, making it popular among professionals. One of the key benefits of GMAW is its versatility in handling a wide range of materials, including carbon steel, stainless steel, aluminum, and various alloys.
This flexibility makes it suitable for diverse automotive manufacturing, construction, and aerospace applications. Additionally, GMAW provides excellent control over the weld bead formation because of its controllable heat input and wire feed speed.
The ability to fine-tune these parameters allows welders to achieve high-quality welds with minimal distortion. Another advantage of GMAW is its efficiency and productivity.
The continuous wire feeding mechanism enables longer uninterrupted welding sessions than other processes requiring frequent electrode changes. Moreover, shielding gas provides better protection against atmospheric contamination than other methods that rely on flux coatings on electrodes or consumable wires, which results in cleaner welds with fewer defects and reduces the need for post-weld cleaning or rework. GMAW is an essential welding process in metal fabrication because of its versatility, control over bead formation, efficiency, and productivity.
Its ability to handle various materials and its reliable shielded environment make it an attractive choice for professionals across different industries. Whether it's joining thin sheets or thick plates together with precision and strength, GMAW consistently delivers high-quality welds that meet stringent industry standards.
GTAW
GTAW, also known as Gas Tungsten Arc Welding or TIG (Tungsten Inert Gas) welding, is a highly versatile and precise welding method commonly used in metal fabrication. This welding process utilizes a non-consumable tungsten electrode to create an electric arc with the base metal.
The weld area is shielded by an inert gas, such as argon or helium, to protect it from atmospheric contamination. One of the key advantages of GTAW is its exceptional control over the heat input.
A foot pedal allows welders to finely adjust the amperage, thereby regulating the heat generated during the process. This level of precise control makes GTAW ideal for welding thin materials where precision and minimal distortion are crucial.
This method offers excellent control over the weld pool size and shape, allowing for intricate welds on complex geometries. Another significant benefit of GTAW is its versatility across various metals and alloys.
It can be used on ferrous metals like stainless and carbon steel and non-ferrous metals like aluminum, copper, and titanium. By adjusting factors like current type (AC or DC), gas composition, electrode material, and polarity (for DC), GTAW can be customized to suit different materials' specific requirements.
This flexibility makes it highly sought after in industries where various materials must be joined accurately. GTAW offers unparalleled precision and control in the metal fabrication process.
Its ability to handle various metals while maintaining low distortion levels even on thin materials proves a reliable option for detailed work. Whether fabricating stainless steel components or joining intricate aluminum structures, GTAW remains an invaluable tool in welding.
SMAW
SMAW, also known as Shielded Metal Arc Welding or Stick Welding, is a widely used welding process using an electric arc to create a high-temperature heat source for metal fusion. This method uses a consumable electrode coated with a flux material that protects against atmospheric contaminants during welding.
SMAW's major advantages are its versatility and portability. Unlike other welding methods requiring complex equipment and gas shielding, SMAW can be carried out in various positions with minimal setup requirements—making it suitable for fieldwork or situations where mobility is essential. SMAW welds different metals, including carbon steel, stainless steel, cast iron, and even non-ferrous metals like aluminum.
However, it's important to note that SMAW may have certain limitations compared to other welding processes. For instance, it typically produces slower deposition rates than automated methods like GMAW or SAW.
Additionally, because of the manual nature of the process and the need for constant electrode replacements, as they are consumed during welding, SMAW may result in more frequent interruptions during larger-scale projects. Nonetheless, these limitations can be overcome through skilled craftsmanship and proper planning.
SMAW remains a significant welding method in metal fabrication because of its versatility and portability. The ability to perform this process in various positions makes it an excellent choice for on-site repairs or projects where mobility is crucial.
While it may not offer the same speed as automated methods or possess high deposition rates compared to other processes, SMAW compensates for its adaptability across different types of metals. Ultimately, selecting the appropriate welding method should consider project scale and environmental conditions to ensure optimal results in metal fabrication endeavors.
SAW
In metal fabrication and welding processes, Submerged Arc Welding (SAW) stands tall as a reliable and efficient method. SMAW involves creating an arc between a continuously fed bare electrode and the workpiece to generate heat for melting the base metal. What distinguishes SAW from other welding methods is that it uses a flux layer, which shields the arc and helps control the weld pool's shape and size.
One notable advantage of SAW is its exceptional deposition rates. Because of its high current density and long electrode extension, SAW quickly deposits large filler material. It is well-suited for applications where productivity is crucial, such as in heavy-duty industries like shipbuilding or pipeline construction. SAW offers deep penetration capabilities, making it ideal for easily welding thick materials.
Another key attribute of SAW is its ability to consistently produce high-quality welds. The use of a flux layer helps protect the molten metal from atmospheric contamination during the welding process.
This results in clean welds with minimal defects such as porosity or cracks. Furthermore, since SAW operates with automatic feeding systems and requires limited operator intervention during welding, it reduces human error potential and improves overall weld quality control.
Submerged Arc Welding (SAW) shines brightly among welding methods regarding deposition rates and weld quality consistency. Its ability to deposit large amounts of filler material at an impressive rate makes it highly suitable for heavy-duty applications where productivity is paramount.
Its controlled shielding system also contributes to clean welds with minimal defects, ensuring excellent weld integrity. For industries seeking high productivity combined with superior weld quality control, SAW remains an excellent choice within metal fabrication and welding processes.
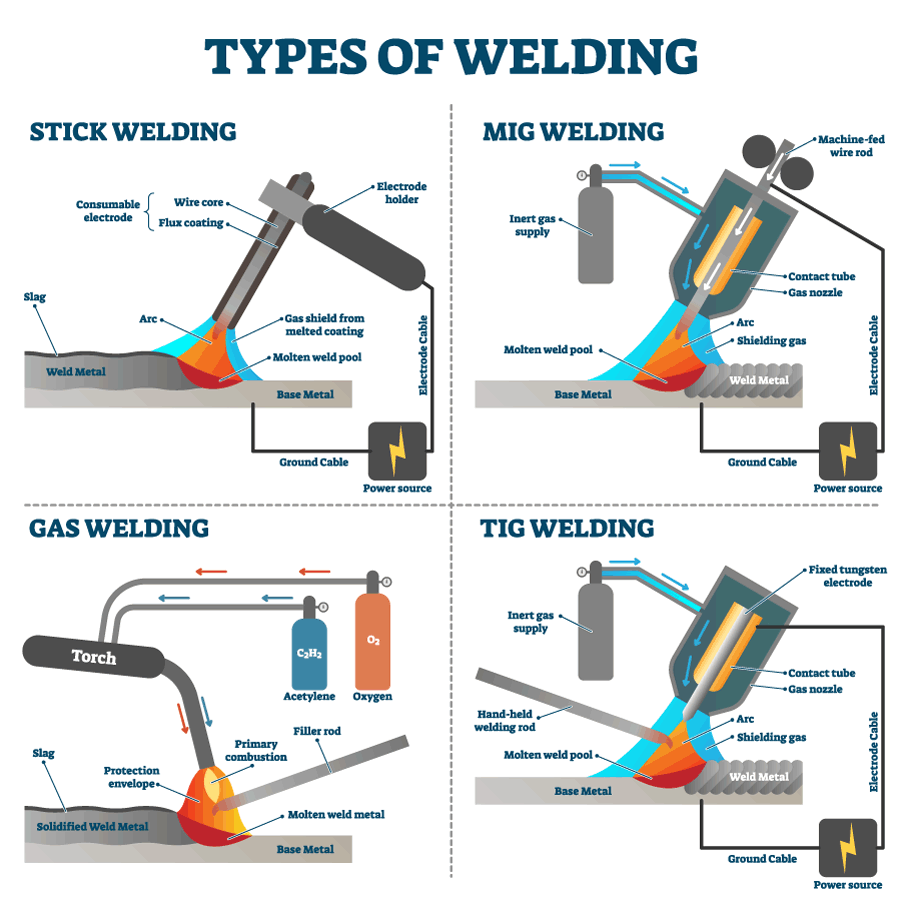
Denique
After looking at these welding methods, each process has unique advantages and applications in the metal fabrication field.
Whether it is the efficiency offered by FCAW for outdoor projects or the precision provided by GTAW for critical components, whether the simplicity yet adaptability offered by SMAW suits your needs or SAW's productivity proves valuable in large-scale welding tasks, there is a welding method suited for every project. The expanding realms of technology and continuous advancement in welding techniques ensure that the metal fabrication field will prosper with precise and efficient welding processes at its disposal.
Much of this may be repetitious for many, others may appreciate this introduction.