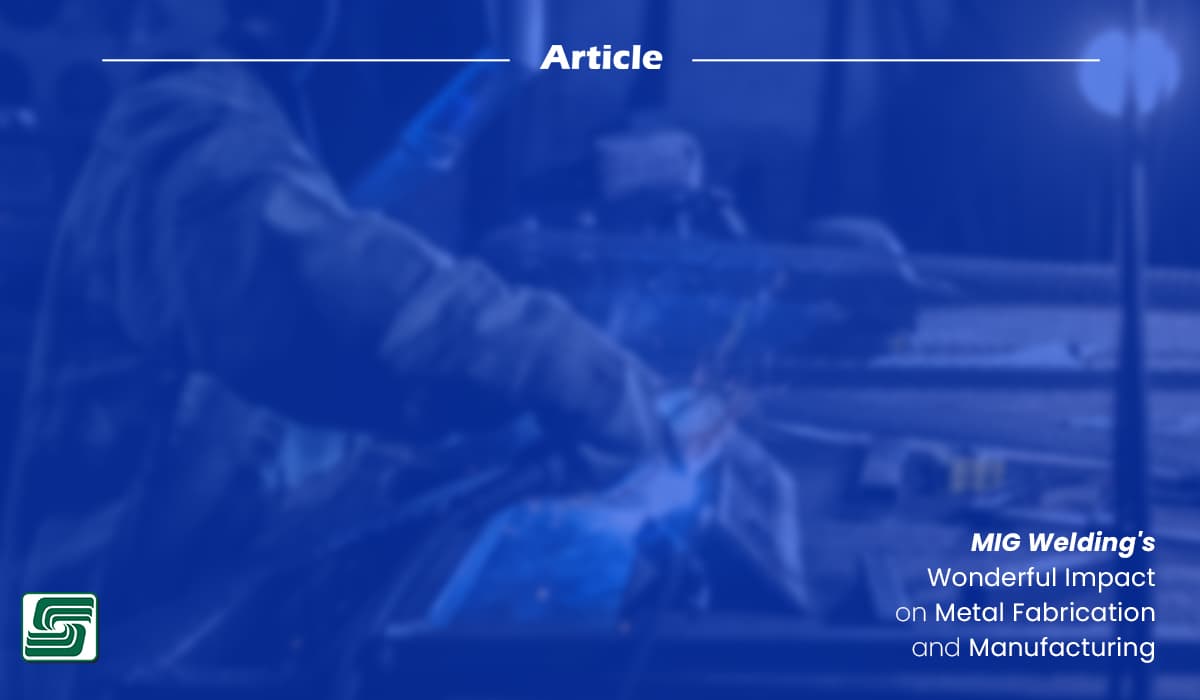
MIG Welding, called Gas Metal Arc Welding (GMAW), is pivotal in contemporary metal fabrication and manufacturing processes. This metal joining technique uses a solid wire electrode, offering heightened efficiency, superior weld quality, versatility, and cost-effectiveness.
Welding in various industries underscores the importance of MIG welding in the broader context of the welding industry. As a fundamental aspect of metalworking and metal forming, MIG welding has become an indispensable component of modern manufacturing processes.
The Impact of MIG Welding
Significance in Modern Manufacturing
- MIG welding significantly enhances production efficiency by enabling faster and more precise welds, contributing to streamlined manufacturing processes.
- The impact of MIG welding extends across various industries, including automotive, aerospace, and construction. MIG welding helps to assemble vehicle components with high precision and structural integrity in the automotive sector. Similarly, in aerospace and construction, MIG welding ensures the fabrication of durable and reliable structures essential for safety and performance.
Advancements in MIG Welding Technology
Advancements in MIG welding technology have not only improved the quality of welds but also opened up new possibilities for its application across diverse manufacturing sectors.
Innovations in MIG welding technology have revolutionized metal fabrication processes by introducing advanced features such as pulse welding, which allow for greater control over heat input and weld penetration.
The evolution of MIG welding equipment has led to improved ergonomics, user-friendly interfaces, and enhanced automation capabilities.
These advancements have significantly impacted manufacturing by increasing productivity and expanding the range of applications for MIG welding.
By embracing these technological advancements, modern manufacturers achieve higher precision, efficiency, and cost-effectiveness in their metal fabrication operations.
Understanding MIG Welding
Process and Technique
MIG welding involves using a consumable wire electrode and a shielding gas to join metal pieces. The process begins with generating an electrical arc between the wire electrode and the workpiece, creating the heat necessary to melt the metal and form a strong bond. Key MIG welding components include:
- The power source
- Wire feed system
- Welding gun
- Shielding gas supply
- Ground clamp
Several best practices and techniques are essential to achieve optimal results in MIG welding. Maintaining proper voltage and wire feed speed settings is crucial for controlling the weld pool size and ensuring adequate penetration.
Maintaining a consistent travel speed and proper torch angles helps achieve uniform and high-quality welds. It's also important to ensure that the work area is clean and free from contaminants to prevent defects in the weld.
These techniques are vital for producing structurally sound welds with excellent mechanical properties. As such, acquiring proficiency in MIG welding processes through training and hands-on experience is fundamental for welders aiming to deliver high-quality workmanship.
Safety Considerations in MIG Welding
Safety is paramount in MIG welding operations from potential hazards such as electric shock, arc radiation, fumes, and molten metal splatter.
To mitigate these risks, welders must adhere to stringent safety measures and precautions. These measures include wearing appropriate personal protective equipment (PPE) such as:
- Welding helmets with auto-darkening filters
- Flame-resistant clothing
- Gloves
- Closed steel toe shoes
Proper training in handling equipment safely and understanding the characteristics of different metals is crucial to minimizing workplace accidents.
Adequate ventilation or exhaust systems should be in place to remove fumes generated during welding processes. Regular maintenance of equipment ensures that it operates safely and efficiently.
By prioritizing safety considerations in MIG welding operations, workers safeguard themselves against potential hazards while delivering high-quality welds effectively.
Advantages of GMAW
Efficiency and Quality
The efficiency and quality advantages of solid wire welding in GMAW not only streamline manufacturing processes but also contribute to substantial cost savings.
In Gas Metal Arc Welding (GMAW), solid wire welding offers notable efficiency and weld quality advantages.
The solid wire electrode used in GMAW provides a stable arc, resulting in consistent and precise welds. A stable welding arc contributes to the overall efficiency of the welding process by reducing the need for extensive rework or corrections.
Solid wire welding enhances welds' quality, ensuring strong and durable metal joints that meet industry standards.
Solid wire welding in GMAW contributes to cost savings and improved productivity. The efficient deposition of metal through this method reduces material waste, leading to more economical use of resources.
The high-quality welds produced through solid wire welding minimize the likelihood of defects or failures, reducing the need for repairs and enhancing overall productivity in metal fabrication processes.
Versatility and Ease of Use
Solid wire welding is highly versatile and finds applications across diverse metal fabrication tasks.
Whether it's joining thin sheet metals or thicker structural components, GMAW with solid wire electrodes accommodates various material thicknesses and types. This versatility makes it ideal for various industrial applications, from automotive manufacturing to structural steel fabrication.
One significant advantage is its ease of use, making it suitable for beginners and those with limited experience in welding processes. The straightforward setup and operation of GMAW with solid wire electrodes enable individuals to quickly grasp the technique and produce high-quality welds with minimal training.
This accessibility makes GMAW a preferred choice for manufacturers seeking efficient yet reliable metal joining solutions.
Metal Fabrication Applications
Industrial Applications
MIG welding is pivotal in various industrial metal fabrication processes, offering efficient and reliable solutions for joining metal components. In the automotive industry,
MIG welding is extensively used for assembling vehicle frames, body panels, and other structural elements. The precise and high-strength welds achieved through MIG welding contribute to automobiles' overall safety and durability.
MIG welding helps fabricate steel structures in the construction sector, including beams, columns, and trusses.
The versatility of MIG welding allows for the joining of diverse metal profiles with precision, ensuring the structural integrity of buildings and infrastructure projects.
Shipbuilding also benefits significantly from MIG welding technology, which fabricates ship components such as hulls, bulkheads, and pipelines.
The ability of MIG welding to produce robust and corrosion-resistant welds makes it an indispensable process in marine metal fabrication.
Artistic and Custom Fabrication
Beyond industrial applications, MIG welding finds extensive use in artistic and custom metal fabrication projects. Artists and craftsmen leverage the versatility of MIG welding to create intricate metal sculptures, decorative pieces, and custom furniture.
The precision and control offered by MIG welding techniques enable artisans to bring their creative visions to life with durable and visually appealing metalwork.
An example of specialized applications includes creating customized architectural elements such as ornamental railings, gates, and signage. These unique pieces showcase the aesthetic potential of MIG welding in producing bespoke metal designs tailored to specific architectural or artistic requirements.
Comparing Welding Processes
Solid Wire Welding vs. Other Arc Welding Methods
Consider each technique's distinct characteristics and applications when comparing solid wire welding with other arc welding methods.
As used in Gas Metal Arc Welding (GMAW), solid wire welding stands out for its efficiency, precision, and versatility in various metal fabrication tasks. In contrast, other arc welding methods, such as Shielded Metal Arc Welding (SMAW) and Flux-Cored Arc Welding (FCAW), offer unique features that cater to specific welding requirements.
Solid wire welding distinguishes itself by delivering consistent and high-quality welds, making it ideal for applications demanding precision and structural integrity. Its stable arc and precise control over heat input contribute to superior weld outcomes.
On the other hand, SMAW is known for its portability and ability to perform effectively even in adverse conditions, making it suitable for outdoor or on-site welding projects. FCAW, with its flux-cored wire electrode, excels in providing deep penetration and is often preferred for welding thick materials.
Each method has advantages and limitations based on portability, ease of use, weld quality, and suitability for specific material thicknesses. Understanding these distinctions enables manufacturers to select the most appropriate welding process based on their unique project requirements.
Cost-Effectiveness and Productivity
The cost-effectiveness and productivity factors differentiate solid wire welding from other welding techniques within the metal joining industry. Solid wire welding offers notable advantages in efficient metal deposition, reduced rework needs, and minimized material waste.
These aspects contribute to cost savings while enhancing overall productivity in metal fabrication processes.
In comparison, while SMAW may excel in portability and versatility across different work environments, it may involve higher labor costs from slower weld speeds and increased post-weld cleanup requirements.
FCAW's deep penetration capabilities make it suitable for heavy-duty applications but may cause higher consumable costs than solid wire electrodes used in GMAW.
When evaluating cost-effectiveness and productivity across different arc welding methods, it's important to consider the initial equipment investment and long-term operational costs associated with consumables usage, labor efficiency, and overall project timelines.
MIG Welding's Future
Technological Advancements and Innovations
The future of MIG welding is poised for significant technological advancements and innovations that will reshape the landscape of metal fabrication. The continuous quest for enhanced efficiency, precision, and adaptability in welding processes drives these developments.
One notable area of innovation is the integration of advanced automation and robotics into MIG welding systems. This trend toward automation aims to optimize production workflows, reduce manual intervention, and achieve consistent weld quality across diverse manufacturing environments.
Research and development efforts are focused on refining welding equipment and consumables to meet evolving industry demands, such as:
- The exploration of new materials for solid wire electrodes
- Improved shielding gases
- Enhanced power sources with advanced control features
These innovations aim to address specific challenges in metal joining applications while expanding the capabilities of MIG welding technology.
Besides hardware advancements, there is a growing emphasis on software integration for monitoring and controlling welding parameters in real-time.
Integrating data analytics and machine learning algorithms into MIG welding systems enables predictive maintenance, quality assurance, and performance optimization.
These technological innovations are expected to elevate the precision, reliability, and overall effectiveness of MIG welding in metal fabrication processes.
Industry Trends and Adoption
The adoption of MIG welding technology continues to follow prominent industry trends that emphasize the following:
- Sustainability
- Digitalization
- Operational Agility
In response to increasing environmental consciousness, there is a growing focus on developing eco-friendly welding solutions within the metal joining industry.
Eco-friendly solutions include exploring alternative shielding gases with reduced carbon emissions and sustainable consumables that minimize environmental impact.
As industries embrace digital transformation initiatives, MIG welding systems are expected to integrate seamlessly into smart manufacturing frameworks.
The convergence of MIG welding technology with Industrial Internet of Things (IIoT) platforms enables real-time monitoring, remote diagnostics, and connectivity with other manufacturing systems.
This interconnected approach enhances operational visibility, process control, and adaptability to dynamic production requirements.
The evolution of MIG welding in response to these industry trends reflects a broader shift towards more sustainable practices, data-driven decision-making, and agile manufacturing processes.
As manufacturers increasingly recognize the value of these trends in enhancing competitiveness and meeting regulatory standards, the adoption of advanced MIG welding technologies is expected to grow significantly across diverse industrial sectors.
MIG Welding's Role in Industry
Industry Impact and Significance
MIG welding impacts the manufacturing and metal fabrication sectors, playing a pivotal role in meeting industry-specific requirements and standards. The precision, efficiency, and versatility of MIG welding techniques contribute significantly to producing high-quality metal components across various industrial domains.
Whether it's automotive manufacturing, aerospace engineering, or structural construction, MIG welding ensures the fabrication of durable and reliable metal structures that adhere to stringent industry standards.
The seamless integration of MIG welding into manufacturing processes underscores its significance as a fundamental metal joining method. Its impact extends beyond conventional production practices, influencing product quality, safety, and performance across industries.
Skills and Training in MIG Welding
Learning the skills and training for MIG welding is essential for welders aiming to excel in this specialized field. Training programs and certifications tailored to MIG welding practices play a crucial role in developing proficiency among welders.
These programs encompass comprehensive instruction on welding techniques, equipment operation, safety protocols, and best practices for achieving optimal weld outcomes.
By undergoing structured training programs, welders gain hands-on experience handling MIG welding equipment effectively while mastering the nuances of different metal joining processes. Certifications validate their expertise and competence in executing MIG welding operations with precision and adherence to industry standards.
Continuous skill development through advanced training modules enables welders to stay updated with evolving technologies and best-in-class practices within MIG welding.
This commitment to ongoing learning enhances their capabilities to address complex manufacturing challenges while upholding superior quality standards.
In Sum
MIG welding, particularly solid wire welding, profoundly impacts metal fabrication processes and several industries. Its role in enhancing production efficiency, ensuring high-quality welds, and contributing to cost-effectiveness underscores its significance in modern manufacturing.
The future of MIG welding is characterized by ongoing technological advancements and integrating industry trends, shaping its continued role in manufacturing. Understanding the advantages and applications of MIG welding is crucial for meeting the evolving demands of the welding industry.
As innovations continue to drive progress in metal joining techniques, staying abreast of these developments is essential for manufacturers and welders.
By embracing the potential of MIG welding technology and its applications, stakeholders position themselves at the forefront of efficient and reliable metal fabrication practices while contributing to advancing diverse industrial sectors.