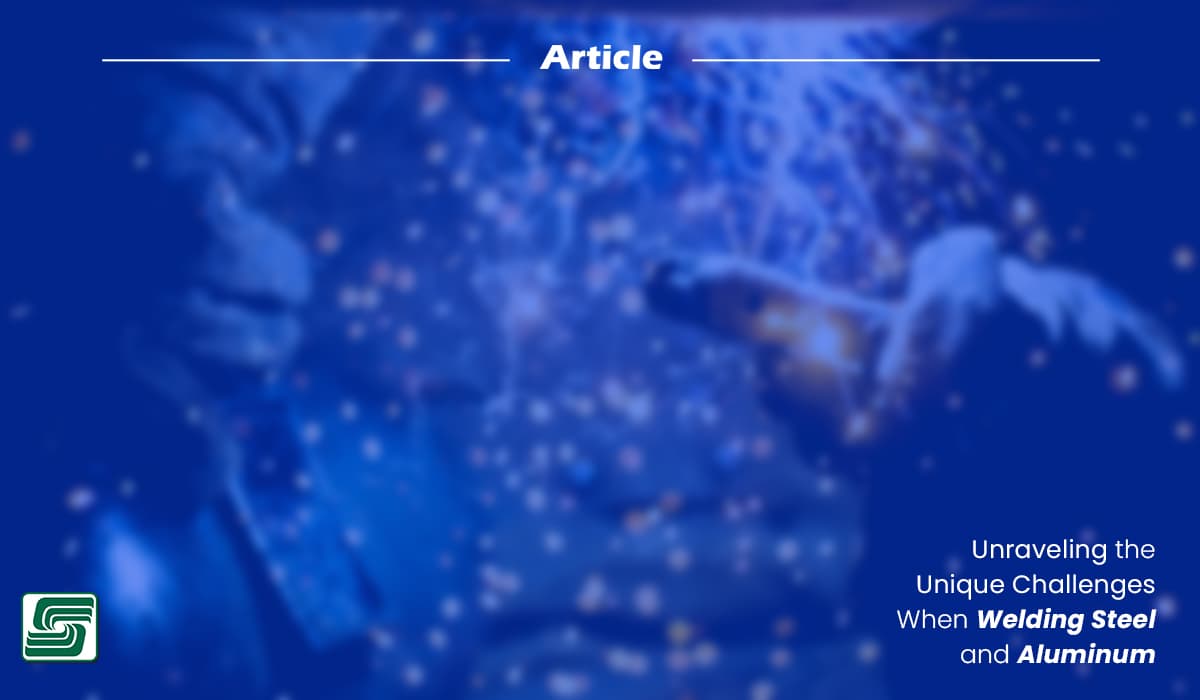
Welding is a fundamental process in metal fabrication, crucial in joining various metals to create structures and components. Two commonly used metals for welding are aluminum and steel.
While both offer unique properties and advantages, they also present distinct challenges during welding.
Understanding the Basics of Welding Aluminum and Steel
Understanding the unique properties and characteristics of different metals is essential for achieving successful outcomes in welding.
Welding aluminum and steel presents distinct challenges and requires specific techniques to ensure high-quality welds.
Welding Aluminum: A Quick Overview
Welding aluminum demands a thorough understanding of its key properties to overcome the challenges associated with this versatile metal. Aluminum is known for its lightweight nature, excellent corrosion resistance, and high thermal conductivity. These properties make welding aluminum a complex process that requires precise heat management and specialized equipment.
Key Properties of Aluminum in Welding
- Lightweight: Aluminum possesses a low density, making it ideal for applications where weight is a critical factor.
- Corrosion Resistance: The natural oxide layer on aluminum provides inherent protection against corrosion, making it suitable for various outdoor and marine applications.
- High Thermal Conductivity: Aluminum's high thermal conductivity requires careful heat control during welding to prevent distortion and burn-through.
Welding Steel: A Quick Overview
Working with steel presents challenges compared to welding aluminum because of the material's distinct properties. Steel is prized for its strength, durability, and versatility, making it a popular choice across several industries.
Key Properties of Steel in Welding
- Strength: The exceptional strength of steel makes it an indispensable material in structural applications where strength is critical.
- Durability: With proper treatment and maintenance, steel exhibits remarkable durability against wear, impact, and harsh environmental conditions.
- Versatility: Steel's versatility allows for a wide range of fabrication processes, including welding, cutting, forming, and shaping.
Understanding these fundamental properties is crucial for welders seeking to master the art of working with aluminum and steel, enabling them to adapt their techniques accordingly.
The Challenges of Welding Aluminum vs. Steel
When welding aluminum, welders encounter specific challenges that require careful consideration and specialized techniques. Heat management, material sensitivity, and critical cleaning and preparation are primary hurdles.
Heat Management and Material Sensitivity
One of the foremost challenges in welding aluminum is the intricate balance of heat control. Because of its high thermal conductivity, aluminum dissipates heat rapidly, requiring precise adjustments in welding parameters to prevent overheating and distortion.
Welders must use advanced techniques, such as pulse welding or modified waveforms, to manage heat effectively while ensuring proper fusion.
Aluminum is a Sensitive Metal
Aluminum's material sensitivity poses a significant challenge during welding. The metal's vulnerability to hot cracking demands careful preheating and interpass temperature control to mitigate the risk of weld defects. Selecting suitable filler metals with compatible alloy compositions is crucial for achieving strong, crack-free welds in aluminum components.
Cleaning and Preparation
Thorough cleaning and preparation before welding are critical for successful aluminum welds. The metal's natural oxide layer requires removal through mechanical abrasion or chemical etching to ensure optimal weld quality. Specialized cleaning solvents and wire brushes are commonly used to eliminate surface contaminants and promote metallurgical bonding during welding.
Common Hurdles When Welding Steel
Similarly, welding steel presents its own set of challenges that demand attention from skilled welders. Key hurdles include avoiding contamination and addressing the diverse range of steel alloys in fabrication processes.
Avoiding Contamination
Contamination control is critical when working with steel, particularly in environments prone to airborne impurities or surface pollutants. Proper shielding gas selection, effective ventilation systems, and meticulous workshop cleanliness are essential to prevent contamination compromising weld integrity.
Dealing with Different Steel Alloys
The vast array of steel alloys available introduces the welding process's complexity. Each alloy exhibits unique hardenability, tensile strength, and corrosion resistance characteristics, requiring welders to adapt their techniques accordingly. A thorough understanding of steel classifications and alloy specifications is essential for selecting appropriate filler materials and establishing optimal welding parameters based on the specific steel composition.
Metal Fabrication: Adapting Techniques for Aluminum and Steel
Metal fabrication encompasses a diverse set of techniques and processes tailored to the unique properties of aluminum and steel. Adapting welding techniques for each metal is essential to ensure the integrity and quality of the fabricated components.
Metal Fabrication with Aluminum
Property |
Aluminum |
Steel |
Welding Techniques |
Specialized equipment required: pulse settings, helium gas shielding |
Standard welding techniques are often sufficient |
Challenges |
Heat control to minimize distortion, precise filler metal deposition |
Less demanding; may require specific techniques for high-strength steels |
Cutting Methods |
High-speed saws or routers for low-density composition |
Standard cutting techniques applicable: torches, saws |
Forming & Shaping |
Tailored tooling designs for accurate dimensional control |
Standard tooling often sufficient |
Metal Fabrication with Steel
Versatility and Strength Considerations
In contrast to aluminum, steel's versatility in metal fabrication allows for a wide range of techniques catering to diverse applications. Steel's exceptional strength and durability enable fabricators to employ various cutting methods, including plasma cutting, oxy-fuel cutting, or abrasive water jet cutting, depending on the specific steel alloy being processed.
Steel's adaptability extends to forming operations, where roll forming, press braking, and stamping techniques create intricate shapes and profiles. These versatile forming processes enable fabricators to achieve precise geometries while harnessing the inherent strength of steel components.
When welding steel components, fabricators leverage an array of filler metals tailored to the compositions of different steel alloys. Shielded metal arc welding (SMAW), gas metal arc welding (GMAW), or flux-cored arc welding (FCAW) are commonly employed based on the specific requirements of each steel fabrication project.
Custom Fixturing for Welding Projects: Aluminum vs. Steel
Custom fixturing ensures precise and efficient welding processes for aluminum and steel projects. Tailoring fixturing techniques to the unique characteristics of each metal is essential for achieving optimal heat distribution, strength, and support.
Property |
Aluminum Welding |
Steel Welding |
Focus |
Heat management and distortion control |
Strength, support, and dimensional accuracy |
Fixture Design |
Heat dissipation: clamping systems, heat sinks, backing bars/chill blocks |
Robustness and adaptability: jigs, fixtures, clamping mechanisms, adjustable supports |
Material Considerations |
High thermal conductivity: facilitates heat transfer |
Varying material properties: adaptability for different steel alloys |
Benefits |
Minimized distortion, consistent weld quality, precise heat control |
Secure component positioning, minimized distortion, consistent weld accuracy |
Additional Features |
Adjustable configurations for varying geometries |
Modular designs for diverse applications, water-cooled supports (thick steel) |
In Sum
The welding processes for aluminum and steel present distinct challenges because of each metal's unique properties. Welding aluminum demands meticulous heat management and material sensitivity because of its lightweight nature, corrosion resistance, and high thermal conductivity. Welding steel requires careful consideration of contamination control and adaptation to diverse steel alloys with varying strength and durability.
The key differences lie in the intricate balance of heat control for aluminum welding, while steel welding requires measures to prevent contamination and adapt techniques based on specific alloy compositions. Understanding these variations is essential for welders seeking to master working with both metals effectively.
Making the Right Choice for Your Project
Several factors must be considered when selecting the right metal for a welding project to ensure optimal outcomes.
- Application Requirements: Assessing the specific application's demands regarding structural integrity, weight considerations, environmental exposure, and mechanical properties is crucial in determining whether aluminum or steel is better suited for the project.
- Material Characteristics: Understanding the distinctive properties of each metal, including weight, corrosion resistance, thermal conductivity, strength, and versatility, enables informed decision-making regarding which material aligns best with the project's requirements.
- Fabrication Techniques: Evaluating the fabrication techniques tailored to each metal's characteristics allows for a comprehensive comparison of welding processes, cutting methods, forming operations, and fixturing requirements unique to aluminum and steel.
By carefully weighing these factors against the project's objectives and performance expectations, welders can decide whether aluminum or steel is optimal for their specific welding endeavors. This thoughtful consideration ensures that the selected metal aligns seamlessly with the project's functional needs while facilitating efficient fabrication processes.
Navigating the complexities of welding aluminum versus steel involves deeply understanding their inherent challenges and adaptation techniques.
Welders achieve exceptional results by combining the unique advantages of both metals.