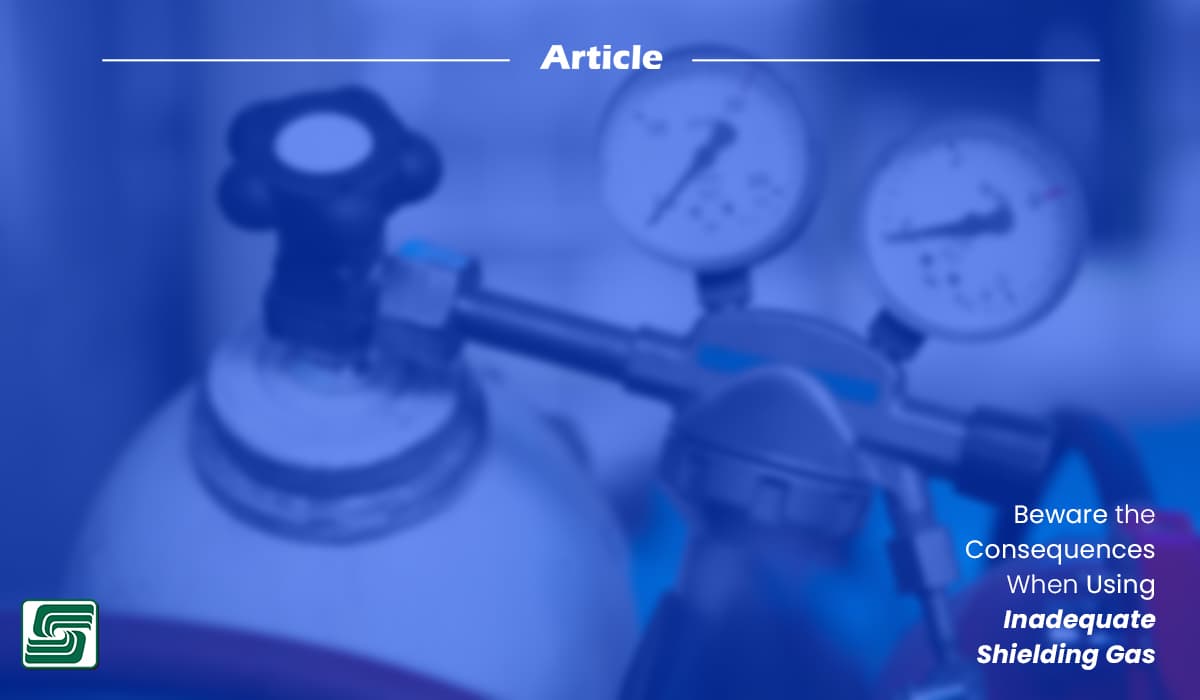
In the welding world, shielding gas's significance cannot be overstated. MIG welding, or Gas Metal Arc Welding (GMAW), relies on shielding gas to protect the weld pool and molten metal from atmospheric contamination.
The primary role of shielding gas is to create a stable arc and prevent oxidation and other detrimental reactions during welding.
The Role of Shielding Gas
The fundamental purpose of shielding gas in MIG welding is to safeguard the weld from atmospheric gases that could compromise its integrity. By enveloping the weld area, the shielding gas effectively displaces oxygen, nitrogen, and other impurities that might lead to defects in the welded joint.
Eliminating oxygen ensures that the molten metal solidifies with no undesirable interactions, contributing to superior weld quality.
Common Types of Shielding Gas
Several types of gases are used for MIG welding, each tailored to specific applications and materials.
Argon is one of the most commonly employed inert gases in MIG welding for various metals. It is particularly favored for non-ferrous metals such as aluminum, copper, and magnesium because it prevents reactions with atmospheric gases.
A mixture of argon and CO2 is traditionally used for MIG welding, offering a versatile option for different welding scenarios.
Using a combination of argon and helium is not limited to TIG welding; it is also applied in MIG welding processes. These mixtures influence:
- Weld Geometry
- Seam Appearance
- Metallurgical Properties
- Overall Efficiency
Poor Weld Quality in Steel MIG Welding
Shielding gas is paramount in MIG welding, especially when working with steel. The choice of shielding gas directly influences the welds' quality and integrity.
When inadequate gas is used in steel MIG welding, it harms the welds' mechanical properties and visual appearance.
How Inadequate Gas Affects Weld Strength
The shielding gas's composition significantly impacts steel welds' strength and durability. Incomplete protection because of inadequate gas increases corrosion susceptibility and reduces tensile strength.
Studies have shown that optimizing the shielding gas blend enhances weld joint properties, microstructure, and mechanical properties, ultimately improving overall welding efficiency.
Visual Defects in Steel Welds
Inadequate shielding gas during steel MIG welding often manifests visually through defects such as spatter, undercutting, or surface irregularities.
These imperfections compromise the aesthetic appeal of the welded joint and show potential structural weaknesses.
Properly selecting and applying shielding gases ensures a smooth and visually appealing surface finish on steel welds.
Increased Porosity in Aluminum MIG Welding
Unique challenges arise when MIG welding aluminum because of the material's properties and behavior during welding. Using shielding gas is crucial in aluminum MIG welding to mitigate the risk of porosity, a common defect that compromises weld integrity.
Challenges of MIG Welding Aluminum
Aluminum presents distinct challenges in welding, primarily because of its high thermal conductivity and susceptibility to atmospheric contamination.
The role of shielding gas in preventing porosity in aluminum welds cannot be overstated.
As emphasized by Welding Experts,
MIG welding is primarily used to weld steel, but you can also weld aluminum using a spool gun or a special liner for the regular MIG gun. It requires 100% pure argon shielding gas for aluminum welding.
The Role of Shielding Gas in Preventing Porosity
The primary function of shielding gases, such as 100% pure argon, in aluminum MIG welding, is to protect the weld pool from harmful contamination that could lead to porosity. This is echoed by Welding Experts, who highlight that shielding gases significantly affect the:
- Weld Shape
- Weld Geometry
- Seam Appearance
- Metallurgical and Mechanical Properties.
Inadequate Shielding Leads to Poor Aluminum Welds
Where inadequate shielding gas is employed during aluminum MIG welding, porosity becomes clear through visible voids within the weld bead. These voids weaken the weld's structural integrity and lead to premature failure under load conditions.
Properly selecting and applying shielding gases is essential for achieving sound and defect-free aluminum welds.
Aluminum Welding Techniques
When working with aluminum, carefully select appropriate shielding gases and fine-tuning welding parameters.
Achieving optimal results in aluminum MIG welding requires a comprehensive understanding of how different shielding gases influence welded joints' overall quality and integrity.
The significance of proper welding shielding in aluminum MIG welding cannot be overlooked; it plays a pivotal role in preventing defects, such as porosity, and ensuring robust welded joints.
Comparison with TIG Welding Shielding Needs
When comparing the shielding gas requirements for MIG welding and TIG welding, each process has distinct gas needs tailored to their specific applications and materials.
TIG Welding vs. MIG Welding Shielding Gas Requirements
In MIG welding, a mixture of argon and CO2 is commonly used for ferrous metals like steel and stainless steel, offering versatility in addressing their unique characteristics.
TIG welding relies on pure argon and the potential use of helium and hydrogen, depending on the specific requirements of the welding task at hand.
Similarities in Shielding Needs
MIG and TIG welding processes commonly use argon as a primary shielding gas. This gas ensures a stable arc and provides adequate protection against atmospheric contamination during the welding process.
This similarity underscores the fundamental role of argon in preserving weld integrity across different welding techniques.
Key Differences and Their Effects on Weld Quality
The key divergence lies in the additional gases used for each process.
MIG welding incorporates a mixture of argon, CO2, oxygen, and helium to address diverse material compositions, while TIG welding predominantly uses pure argon, with potential variations involving helium and hydrogen.
This distinction directly impacts the weld quality by influencing arc stability, heat input control, and overall penetration depth.
Why TIG Welding May Be More Forgiving
TIG welding's reliance on pure argon as a primary shielding gas contributes to its reputation for being more forgiving when working with various materials.
The absence of reactive gases like CO2 or oxygen allows for greater control over the weld pool dynamics, resulting in improved bead appearance and reduced spatter formation.
The ability to fine-tune shielding gas compositions in TIG welding enables welders to achieve precise control over heat input and minimize distortion in thin materials like aluminum.
The comparison between MIG and TIG welding reveals nuanced differences in their respective shielding gas requirements, underscoring the need for tailored approaches based on material composition and desired weld characteristics.
Best Practices for Welding Shielding
Selecting the Right Shielding Gas
Selecting the appropriate shielding gas is a critical factor in welding shielding, significantly influencing the quality and efficiency of the welding process.
Experienced welders emphasize that the choice of shielding gas depends on various factors, including the following:
- Type of Welding Process
- Welded Materials,
- Desired Outcome
For instance, when working with steel in MIG welding, a suitable shielding gas blend must be chosen to ensure optimal weld strength and visual appearance.
Similarly, selecting a shielding gas such as 100% pure argon in aluminum MIG welding is essential to prevent porosity and achieve robust welded joints.
The insights from experienced welders further highlight that shielding gases are pivotal in influencing several aspects of the welding process, including:
- Weld Geometry
- Seam Appearance
- Metallurgical and Mechanical Properties
- Welding Speed
- Metal Transfer
- Arc Stability
- Emissions Control
Meticulous consideration should be given to selecting the right shielding gas tailored to specific welding requirements and material compositions.
Tips for Maintaining Optimal Gas Flow
Maintaining an optimal gas flow is crucial for ensuring consistent and high-quality welds. The study on the effects of shielding gas mixtures on welding efficiency underscores the importance of using an optimum flow rate to achieve:
- Better Productivity
- Reduced Gas Consumption
- Improved Weld Properties
These results emphasize the significance of closely monitoring and adjusting the gas flow during welding to optimize its impact on weld quality and overall efficiency.
Experienced welders stress that maintaining optimal gas flow involves meticulous attention to detail throughout welding. Proper maintenance includes:
- Regular Calibration of Gas Flow Meters
- Periodic Checks for Leaks or Obstructions in the Gas Delivery System
- Stick to Recommended Flow Rates
In Sum
Selecting the right shielding gas tailored to each welding application and maintaining optimal gas flow are fundamental best practices that significantly contribute to achieving superior weld quality while enhancing overall process efficiency.